Производство деревянных транспортных поддонов
Не правда ли, знакомая картина: к зданию подъехал грузовик, водитель открыл задний борт полуприцепа, из дверей дома высыпали какие-то люди, которые стали выгружать и, заметно натужась, переносить привезенные ящики и коробки? Упаковки постоянно рвутся, их содержимое оказывается на земле, а вскоре уставшие работники устраивают перекур…
Увидеть подобное в Европе теперь невозможно: там на мелких предприятиях просто нет такого количества сотрудников, чтобы обеспечить разгрузку и погрузку товаров вручную. И если каждый раз отрывать их от дела, то производство остановится. К тому же профсоюзами запрещена переноска тяжестей вручную.
Иллюстрации и таблицы см. в PDF-версии статьи
Деревянные поддоны на вилочном захвате
Так каким же образом там решается проблема загрузки-разгрузки? Все очень просто. Перед перемещением тяжелых предметов или большого количества изделий их укладывают на транспортные поддоны, на которых они хранятся на складе до отгрузки потребителю. Для манипулирования этими грузами на любом европейском предприятии, даже самом мелком, обязательно используется тележка или погрузчик с вилообразным подъемником.
Такой способ перемещения грузов определил распространение поддонов различной конструкции.
Под поддоном понимается транспортная тара, средство пакетирования, имеющее жесткую площадку и место, достаточное для создания укрупненной грузовой единицы, используемая в качестве основания для сбора, складирования, перегрузки и перевозки грузов. Поддон предназначен для хранения груза и его перемещения с помощью механических средств.
Поддоны подразделяются на так называемые одноразовые, используемые, как правило, только для доставки грузов в одном направлении и затем утилизируемые, и многооборотные, используемые многократно.
Габариты одноразовых поддонов (нем. Einwegpalette, в буквальном переводе одноходовой поддон) не регламентируются. Размеры многооборотных поддонов, требования к их прочности и нанесенным на них обозначениям определяются европейскими стандартами, отчего в России такие поддоны получили расхожее наименование «европоддоны» или «европалеты».
Различаются поддоны двухзаходные, конструкция которых обеспечивает возможность ввода вилочного захвата только с двух противоположных сторон, и четырехзаходные, позволяющие вводить вилы погрузчика с четырех сторон. Поддоны могут быть также одно- и двухнастильными, то есть имеющими площадку для размещения груза только с одной или с обеих сторон.
Поддоны изготавливаются из древесины, пластмасс, металлов. Для их производства все чаще делаются попытки использовать вторичное сырье.
Деревянный поддон
Деревянные поддоны до сих пор наиболее распространены. Одноразовые поддоны обычно проектируются самим поставщиком продукции так, чтобы их габариты в наибольшей степени соответствовали размерам стопы отгружаемых изделий (рис. 1).
Конструкция и размеры многоразовых поддонов определены несколькими европейскими стандартами (DIN) и несколькими российскими, в целом не противоречащими DIN, но разработанными ещё в 1980-х годах и нуждающихся в изменениях и дополнениях в соответствии с современными требованиями.
В конструкции поддонов должны быть предусмотрены образованные с четырех сторон с помощью шашек проемы, которые нужны для ввода в них вилочных захватов и скрепляющих средств пакетирования уложенного на них груза.
Настилы поддонов могут быть сплошными — из уложенных вплотную на основу из брусков и не соединенных между собой досок — или несплошными — из досок, уложенных с промежутками.
Наиболее распространены однонастильные четырехзаходные поддоны (рис. 2).
Пиломатериалы, применяемые для изготовления деталей поддонов, должны иметь влажность не более 25%, что практически соответствует транспортной влажности и позволяет использовать древесину атмосферной (естественной) сушки.
Деревянные детали поддонов изготавливаются из пиломатериалов низших сортов (не ниже 2-го) хвойных пород по ГОСТ 8486−86 и мягких лиственных пород и березы по ГОСТ 2695−83.
Древесина деревянных деталей должна быть без пороков: тупого обзола более чем на одном ребре любой детали, острого обзола, механических повреждений, прорости, рака и инородных включений, а также пластовых трещин, идущих от торцов досок более чем на 50 мм. Перечень допустимых пороков древесины приводится в соответствующих стандартах.
Каждая доска поддона должна быть цельной — сращивание и наращивание не разрешаются. Не допускается и наличие сучков на наружных ребрах крайних досок нижнего настила, а также в местах установки крепежных деталей.
Отверстия от сучков, выпавших при обработке досок, должны заделываться пробками из древесины той же породы, из которой изготовлены доски, с применением водостойкого клея. Шашки должны быть цельными или состоять из двух частей, соединенных водостойким клеем.
Шашки должны быть расположены так, чтобы волокна древесины, из которой они сделаны, были параллельны длинной стороне поддона. В шашках и брусках не допускаются сердцевина и двойная сердцевина.
Показатель шероховатости поверхности Rz деталей поддонов из пиломатериалов лиственных пород не должен превышать 1000 мкм, хвойных пород — 1600 мкм по ГОСТ 7016−82. Это означает, что все детали могут изготавливаться путем пиления, без последующего фрезерования поверхности. Кроме того, шероховатая рабочая поверхность настила поддона обеспечивает лучшее сцепление с ним поверхности перевозимого груза.
Детали деревянных поддонов скрепляются друг с другом гвоздями или скобами. Но при изменении эксплуатационной влажности древесины обычные гвозди выталкиваются из нее. Поэтому такие гвозди или скобы следует загибать с оборотной стороны поддона или использовать для скрепления деталей винтовые или заершенные гвозди (рис. 3).
Поддоны должны иметь маркировку предприятия-изготовителя с указанием товарного знака предприятия, даты изготовления поддона, условного обозначения поддона, его массы в килограммах, грузоподъемности брутто в тоннах, знаков подтверждения произведенного обеззараживания. Маркировка должна быть нанесена на двух продольных сторонах. Способы нанесения маркировки, размеры маркировочных ярлыков должны соответствовать ГОСТу, который допускает использование для этого краски и пиротипии (выжигания).
На рынке также широко используются деревянные поддоны, бывшие в употреблении. В зависимости от износа и внешнего вида они подразделяются по сортам: 1-й сорт — поддоны, имеющие вид новых (светлые); 2-й сорт — поддоны, использовавшиеся несколько раз, не имеющие загрязнений технического характера, из древесины желтого или светло-серого цвета; 3-й сорт — поддоны, бывшие в употреблении неопределенное число раз, но не имеющие нарушений конструкции, на досках которых допустимы небольшие сколы, цвет — от темно-серого до темного, с небольшими загрязнениями технического характера.
Cтандарт ISPM 15
В связи с тем, что существует большая вероятность переноса вредных организмов, личинок и микробов с древесины поддонов на перевозимые товары, секретариатом Международной конвенции по защите (карантину) растений Продовольственной и сельскохозяйственной организации ООН (Food and Agriculture Organization, FAO) в марте 2002 года был принят стандарт ISPM 15 «Руководство по регулированию древесных упаковочных материалов в международной торговле». Он содержит перечень мер санитарной и фитосанитарной защиты, которые необходимо принять для снижения риска «интродукции и/или распространения карантинных вредных организмов, переносимых с древесными упаковочными материалами (включая крепежную древесину), изготовленными из необработанной хвойной и лиственной древесины и использующимися в международной торговле».
Эти меры применяются в отношении деревянных поддонов, которые нередко изготавливаются из свежей древесины, не прошедшей обработку, достаточную для того, чтобы удалить или уничтожить вредные организмы, содержащиеся в древесине.
Согласно требованиям стандарта ISPM 15 древесные упаковочные и крепежные материалы должны быть свободны от коры, вредителей древесины и их ходов.
Эти материалы также должны подвергаться обеззараживанию посредством камерной сушки, тепловой обработки или фумигации (окуривания) бромистым метилом. В большинстве стран используются технологии тепловой обработки древесины и камерной сушки. Метод фумигации бромистым метилом менее распространен, а в ряде стран запрещен.
После появления международного стандарта ISPM 15 во многих странах мира были приняты меры по введению в действие его положений через национальное законодательство, а Евросоюз одним из первых заявил о введении положений стандарта в Директиву ЕС.
В России, несмотря на отсутствие прямого действия стандарта ISPM 15, фитосанитарный контроль не менее строгий. Так, ещё в феврале 2005 года Росветнадзор распространил «Информацию о фитосанитарных мерах, вводимых странами мира к ввозимым на их территории древесным упаковочным и крепежным материалам». За пределы Российской Федерации, в страны — участники Международной конвенции по защите растений (страны Евросоюза, Китай, Индия, Иран, Канада, Мексика, США, Украина, Грузия), могут быть отправлены только маркированные пиломатериалы и изделия из древесины, включая деревянные поддоны. Основной фитосанитарной мерой является обработка заготовок и готовых поддонов по стандарту ISPM 15 методом камерной сушки при температуре свыше 60°С, которая должна приводить к полному уничтожению вредителей древесины всех видов.
В соответствии с требованиями ISPM 15 и Федерального закона РФ от 15 июля 2000 года № 99-ФЗ «О карантине растений» каждая партия произведенных поддонов, обработанных методом камерной сушки, снабжается документами, подтверждающими, что все они прошли фитосанитарную обработку: сертификатом соответствия и актом Государственного карантинного фитосанитарного надзора.
Технология производства деревянных поддонов
Стоимость поддона невелика — от 250 до 350 руб. (за новый поддон), поэтому транспортировка готовых поддонов на дальние расстояния экономически нецелесообразна.
Из-за этого производство заготовок для них обычно размещается в местах получения наиболее дешевого древесного сырья, а сборка поддонов осуществляется в местах их наибольшего потребления, например в промышленных зонах или в портах.
Изготовителю для выпиливания заготовок выгодно располагать собственным источником древесного сырья, имеющего соответствующие цену и качество.
Поскольку к заготовкам поддонов не предъявляются специальные требования по наклону годичных слоев в древесине, для их производства рационально использовать тонкомерную древесину.
Для того чтобы при лесопилении можно было эффективно использовать дешевые искривленные сортименты, целесообразно сначала выполнить их поперечный раскрой на короткие бревна одинаковой длины, что также позволяет уменьшить рабочие площади цеха.
В общем случае технологический процесс изготовления деревянных поддонов включает операции поперечного раскроя бревен; выпиливание бруса квадратного сечения; поперечный раскрой бруса на шашки; продольный раскрой брусьев на доски; поперечный раскрой досок на заготовки нужной длины; сортировку шашек и досок; заделку дефектов заготовок; сколотку досок оснований поддона с шашками; сколотку настилов с основаниями; загибание выступающих концов гвоздей или скоб; обрезку (опиливание) углов поддона; нанесение маркировки; фитосанитарную обработку.
Изготовленные поддоны отгружаются потребителю в пакетированном виде — устойчивыми штабелями прямоугольной формы. Высота штабелей при их хранении не должна превышать 6 м; допускается их отклонение от вертикали не более чем на 50 мм.
Оборудование для производства деревянных поддонов
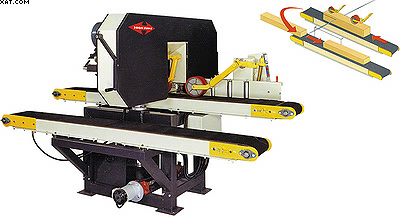
Рис. 4. Простейший горизонтальный ленточнопильный станок с
механизмом подачи и транспортером возврата заготовок
При производстве деревянных поддонов небольшими партиями, например для собственного применения, для их изготовления может использоваться универсальное оборудование.
Так, поперечный раскрой бревен может производиться ручными цепными пилами, выпиливание бруса и его раскрой на доски — на лесопильных рамах или с использованием горизонтальных ленточнопильных станков (рис. 4), а раскрой бруса на шашки и торцевание досок в размер — с помощью торцовочных станков с верхним или нижним расположением пилы.
Сложнее решать проблему заделки дефектов заготовок пробками. Отечественные специальные станки для выполнения этой операции уже давно не производятся, а импортные имеют довольно высокую цену. Поэтому для высверливания мучков могут применяться вертикальные одношпиндельные сверлильные станки, оснащение которых полыми сверлами позволяет изготавливать с их помощью и сами деревянные пробки.
Для сколотки оснований поддона с шашками и скрепления настилов с основаниями обязательно изготавливаются ложементы, соответствующие размерам поддонов. Забивание гвоздей или скоб вручную производится с помощью скобо- или гвоздезабивных пистолетов. При этом следует учесть, что стоимость винтовых или заершенных гвоздей, склеенных в блоки, в несколько раз больше, чем обычных. Обрезка углов одноразовых поддонов, как правило, не производится. Но если она необходима, операция может быть выполнена вручную, цепной пилой, с использованием ложемента, служащего шаблоном. Однако для предприятий по производству деревянных поддонов с высокой производительностью перечисленного выше оборудования недостаточно. Для обеспечения необходимой мощности требуется использование специального оборудования.
Но об этом мы расскажем в следующий раз.
Петр КАЗАНЕЦ, компания «МедиаТехнологии», по заказу журнала «ЛесПромИнформ»
Статьи из цикла «Производство деревянных транспортных поддонов»:
Производство деревянных транспортных поддонов. Часть 2