Снижение токсичности древесных плитных материалов
Решение проблемы экономного использования древесных ресурсов невозможно без развития производства древесных плитных материалов, включая фанеру и древесно-стружечные плиты, широко используемые для выпуска товаров потребительского спроса, в первую очередь мебели и деревянных домов заводского изготовления.
Для получения качественной конкурентоспособной продукции особое внимание необходимо уделять снижению токсичности древесных материалов, уменьшению расхода основных компонентов клея, разработке технологических процессов, обеспечивающих минимальную продолжительность склеивания при требуемой степени отверждения связующего. Учитывая потребность промышленности в использовании низкотоксичных клеев, эффективным способом создания таких клеев является наполнение и модификация синтетических смол.
Как в процессе прессования плитных материалов, так и при эксплуатации изделий, происходит выделение формальдегида, оказывающего вредное воздействие на человека. На интенсивность его выделения оказывают влияние следующие факторы: свойства применяемой смолы, и в первую очередь содержание в ней свободного формальдегида, количество добавляемого связующего, условия прессования плит (влажность осмоленной стружки или шпона, температура и продолжительность прессования), условия эксплуатации изделий из них. В настоящее время к санитарной характеристике плит предъявляются все более жесткие требования. В соответствии с ГОСТ 10632 содержание вредных химических веществ, выделяемых плитами в производственных помещениях, не должно превышать ПДК для воздуха рабочей зоны производственных помещений равной 0,3 мг/м3, а содержание вредных химических веществ, выделяемых плитами в условиях эксплуатации, не должно превышать 0,003 мг/м3.
При хранении компонентов смол и в процессе их производства объем токсичных газовых выбросов составляет 700−1000 м3/ч. Содержание вредных веществ в газовых выбросах, особенно фенола, во много раз превышает предельно-допустимые концентрации (ПДК).
Содержание свободного формальдегида в готовой продукции определяют в производственных условиях по ГОСТ 27678−88 перфораторным методом (более точным) и методом газового анализа ЕN 717 (более оперативным). Свободный формальдегид, выделяющийся из фанеры, изготовленной с применением клеев на основе фенолоформальдегидных смол и определяемый перфораторным методом, составляет 3−6 мг в 100 г продукции при норме до 8 мг в 100 г. Для плитных материалов класса «Е0» этот норматив в странах Евросоюза снижен до 4 мг/100 г продукции.
Последнее обстоятельство ограничивает экспорт российской фанеры на Запад.
Зачастую отечественные химические предприятия выпускают смолы, которые не позволяет деревообрабатывающим предприятиям выпускать низкотоксичную продукцию, способную конкурировать на мировом рынке.
В нашей стране разработано большое количество низкомольных карбамидоформальдегидных смол различных марок: КФ-НП, КФ-60П, КФ-А, КФ-МТ, КФ-МТ-15, КФ-МТ-15КП, КФ-МТ-ПП, КФ-МТУ, КФС-1, КФ-НФП, КФ-015,КФ-015 М, КФ-02, КФ-02Э, КФ-МНП, КФ-53Д и других [1], но мольное отношение карбамида к формальдегиду (К: Ф) в перечисленных смолах колеблется в пределах от 1:1,3 до 1:1,12. Их использование позволяет получать продукцию (фанеру, ДСП и др.) класса «Е2» и для отдельных марок фанеры − «Е1». Среди перечисленных смол есть вакуумированные КФ-НФП, КФ-МТ и другие (сухой остаток 63% и более), полувакуумированные и невакуумированные смолы КФ-60П, КФ-02Э, КФ-53Д, КФ-НВ, СКФ-НМ и другие (содержание сухого остатка от 50 до 60%). Содержание свободного формальдегида в этих смолах составляет в зависимости от марки 0,3% (КФ-МТ, КФ-А), в отдельных марках 0,1% (КФ-НП).
Опыт использования отечественных низкомольных карбамидоформальдегидных смол с мольным соотношением карбамида и формальдегида 1:1,2…1,25 показал, что они пригодны для использования в качестве связующего при производстве ДСП и фанеры. Так, вакуумированная смола КФ-НФП и полувакуумированные смолы КФ-60П, КФ-Н-54, КФ-НВ, КФ-НП позволяют изготавливать плитные материалы, обеспечивая классы токсичности «Е1» и «Е2». Однако при использовании разработанной ООО «ЦНИИФ» смолы КФ-НФП отмечается целый ряд проблем: сложность синтеза смолы, невозможность ее транспортировки ввиду ограниченной жизнеспособности (срока хранения), практической непригодности для фанерных предприятий, использующих холодную подпрессовку пакетов шпона, снижение производственной мощности цехов, а самое главное − снижение прочности склеивания. Такими же недостатками обладают смолы марок КФ-МТ, КФ-МТ-У, КФ-МТ-15 в производстве фанеры, хотя они и обеспечивают снижение токсичности до 10 мг на 100 г абсолютно сухой фанеры.
Разработаны новые виды отечественных карбамидоформальдегидных смол КФ-А, КФ-115-53, КФ-115-55, синтезированные без сточных вод методом глубокой конденсации в кислой среде. Однако при производстве таких смол отмечается высокая загазованность воздуха метанолом (до 100 мг/м3 при ПДКр.з. = 0,5 мг/м3).
На предприятии «Акрон» (г. Великий Новгород) синтезирована карбамидоформальдегидная смола нового поколения серии КФ-ЕС с содержанием свободного формальдегида 0,1%, использование которой позволяет получать фанеру класса «Е1» при одновременном снижении расхода связующего в результате улучшения свойств пленочной структуры отвержденного полимера [1, 2]. При использовании смолы КФ-ЕС(Ф) для производства фанеры обеспечивается прочность склеивания не менее 1,5 МПа.
На химических предприятиях по производству карбамидоформальдегидных смол содержание в них свободного формальдегида снижают путем введения на последней стадии конденсации соединений, связывающих формальдегид и мочевину.
Работают над улучшением физико-химических свойств фенолоформальдегидных смол на Прилукском заводе пластмасс, в ОАО «Уралхимпласт», ООО «Тюменский завод пластмасс».
Рассмотрим характерные случаи модификации карбамидоформальдегидных и фенолоформальдегидных смол, которые широко используются для склеивания шпона.
Анализ результатов исследований истекшего десятилетия XXI века показывает, что наибольший интерес для разработчиков современных качественных смол представляют химически активные вещества, вступающие в реакцию с формальдегидом.
Одним из таких веществ является технический аэросил SiO2 − аморфный беспористый кремнезем, представляющий собой тонкодисперсный порошок серовато-белого цвета. В основе наполнителя диоксид кремния, содержащий примеси, в частности фтористый алюминий и кремнефтористоводородную кислоту. Эти вещества в составе наполнителя снижают рН смолы и количество метилольных групп при отверждении клея, что ведет к ускорению отверждения и углублению поликонденсации [3, 4]. К достоинствам метода добавления в смолу аэросила относятся повышение однородности клеевого слоя и уменьшение его усадки, что позволяет повысить прочность клеевого соединения. Аэросил технический является нетоксичным, пожаро- и взрывобезопасным веществом. Однако, несмотря на физиологическую безвредность аэросила, при работе с ним рабочие места должны быть снабжены мощной приточно-вытяжной вентиляцией; персонал должен работать в распираторах ввиду высокой дисперсности этого наполнителя. В качестве заменителя части карбамидоформальгидных смол [11] предлагается использовать кремнесодержащие соединения, в частности золь кремнезема полимерной формы − стабилизированного золя (Si02)n, в котором массовое содержание щелочных металлов не превышает 0,5%. Стабилизированный золь кремнезема представляет собой аморфное дисперсное вещество низкой вязкости и клейкости, обладающее высокой реакционной способностью. При горячем способе склеивания происходит гелеобразование. Частицы кремнезема образуют разветвленные цепочки ~Si-0-Si~, которые целиком пронизывают объем геля. Этот процесс сопровождается связыванием формальдегида в процессе структурирования и увеличением прочности склеивания древесных клееных материалов.
За рубежом с целью снижения токсичности в смолы также вводят модифицирующие добавки, такие как карбамид, резорцин, смесь карбамида с резорцином, поливиниловый спирт, борогидриты щелочных и щелочноземельных металлов, а также соли аминов и иминов, образованные серной кислотой и фенолсульфокислотами с карбамидом, дициандиамином, меламином и другими аминами [1, 2].
Известен способ введения в состав связующего карбамида и карбоксиметилцеллюлозы в количестве 100 мас. ч. карбамида и 4 мас. ч. карбоксиметилцеллюлозы на 100 мас. ч. связующего (патент Японии № 5217048). Выделение формальдегида из связующего через два дня после его отверждения составляет всего 0,019%.
В Чехии для снижения токсичности в карбамидоформальдегидную смолу добавляют водный раствор тетрабората натрия в количестве, составляющем 0,05−2% (преимущественно 1−2%) от массы смолы При этом содержание формальдегида в связующем для ДСП снижается до 0,005%.
Уменьшение выделения формальдегида наблюдается при введении в смолу перед отверждением серосодержащих веществ в количестве 0,3−30% (преимущественно 2−10%) в пересчете на серу от массы абсолютно сухой смолы.
Известно, что для одновременного снижения токсичности клееных материалов и повышения водостойкости в некоторых странах (Германии, США, Японии) используют изоцианаты.
Во многих работах [5, 6, 7] описаны результаты исследований, в которых с целью снижения токсичности фанеры на основе карбамидоформальдегидной смолы в качестве модифицирующей добавки применялись алюмосиликаты с жесткой каркасной структурой природного происхождения. Алюмосиликаты вводят в смолу марки КФ-МТ-15 в количестве, составляющем 5−15% от массы смолы с содержанием формальдегида 0,15−0,25% непосредственно в процессе приготовления связующего перед прессованием. Опытным путем установлено, что при введении в связующее алюмосиликатов в количестве 10−15% степень очистки от формальдегида составляет 25−30% при однократном использовании добавки. Установлено, что наилучшие результаты получаются при обработке смолы алюмосиликатом природного происхождения − трижды по три часа. В этом случае токсичность исходной смолы снижается с 0,15−0,25% до 0,05−0,0%, степень очистки смолы КФ-МТ-15 от формальдегида составляет 60−80%. Алюмосиликаты не ухудшают физико-механические свойства фанеры. Таким образом, при введении алюмосиликатов в объеме 5−15% от массы смолы в карбамидоформальдегидное связующее для фанеры эмиссия формальдегида из них составляет не более 3 мг на 100 г сухой фанеры, что соответствует классу «Е1». В работе А. Д. Синегибской для снижения токсичности клеевых соединений на основе карбамидоформальдегидных смол предлагается использовать лигносульфонаты и пектолы в качестве модифицирующей добавки. Технические лигносульфонаты (ОСТ 13-183-83) являются побочным продуктом целлюлозно-бумажного производства по кислому сульфитному способу, совмещаются с карбамидоформальдегидными смолами и хорошо разводятся водой, обладают загущающей способностью, что позволяет использовать каолин в меньшем количестве или полностью от него отказаться. Лигносульфонаты реакционноспособны, характеризуются низкой вязкостью при высоком содержании сухих веществ. Добавление в карбамидоформальдегидные смолы 10−20% лигносульфонатов снижает образование парогазовой смеси в процессе поликонденсации, в том числе формальдегида в 2−2,5 раза. Введение лигносульфонатов в карбамидоформальдегидное связующее при изготовлении фанеры и древесно-стружечных плит позволяет получать продукцию класса токсичности «Е2», а при подборе отвердителей (персульфата аммония, сернокислого алюминия, гидросульфата натрия) и технологических режимов изготовления фанеры − продукцию класса «Е1».
В исследованиях, проведенных Санкт-Петербургской государственной лесотехнической академией [8, 9], использовались модифицированные лигносульфонаты на смешенном кальций-натриевом основании, ионы кальция в которых были заменены ионами алюминия. Положительные результаты были получены при использовании модифицированных лигносульфонатов в сочетании с ортофосфатами аммония и карбамидом. При этом эмиссия формальдегида снижалась с 4,5 до 2,7 мг на один грамм смолы. Применение этих составов для фанеры показало снижение эмиссии формальдегида в полтора-два раза при сохранении физико-механических свойств плит.
Минусом использования этих модификаторов является то, что они ухудшают физико-механические свойства плитных материалов на 5−10%.
В работах В. П. Кондратьева [1, 2] в качестве модификатора карбамидоформальдегидных смол для снижения токсичности фанеры был применен аминоэпоксид − продукт конденсации эпихлоргидрина с µ-фенилендиамином. При введении добавки происходит связывание свободного формальдегида и углубление отверждения − следствие связывания свободного формальдегида с вторичными аминогруппами аминоэпоксида. В результате эмиссия формальдегида уменьшается в 4,4−8,3 раза (в зависимости от марки смолы). Но сам аминоэпоксид является очень токсичным веществом, из-за чего эта добавка не получила распространения.
Проведены исследования по использованию подкисленной коры дуба в карбамидоформальдегидных смолах для уменьшения токсичности фанеры и сокращения продолжительности отверждения за счет окисления среды. Получены положительные результаты: снижение токсичности в полтора-два раза. Но этот метод не нашел широкого применения из-за уменьшения прочности клеевого соединения, дефицита коры, трудности ее сушки, обработки и размалывания.
В. П. Кондратьев и Ю. Г. Доронин в своих работах [3] рассматривают использование модификатора РМ-1 для карбамидоформальдегидных связующих при производстве фанеры. РМ-1 − резорциномеламиноформальдегидная смола с минимальным содержанием свободного фенола и формальдегида, разработанная в ОАО «ЦНИИФ», вводится в карбамидоформальдегидную смолу для повышения водостойкости фанеры, а также для снижения ее токсичности. Из результатов исследований этих ученых следует, что при использовании клея на основе смолы КФ-Ж и введении в смолу модификатора РМ-1 в количестве, составляющем до 16,5% от массы смолы получают фанеру, соответствующую классу «Е2», и содержание в ней свободного формальдегида снижается в 2−2,5 раза по сравнению с контрольными образцами. При введении РМ-1 в низкомольные смолы, такие как КФ-МТ, КФ-НФП и другие, и их дальнейшем использовании при производстве древесных материалов была получена фанера пониженной токсичности «Карбофан С», соответствующая классам «Е1» и «Е2» − в зависимости от марки смолы. Но использование дорогостоящей смолы РМ-1 снижает экономическую эффективность производства фанеры.
В СПбЛТА проведены исследования по модификации феноло- и карбамидоформальдегидных смол кремнеземными дисперсными порошками, цеолитсодержащими породами, монтмориллонитами, шунгитовыми сорбентами [6, 7, 8, 9, 10, 11]. Определению подлежали: продолжительность желатинизации клея, его условная вязкость и поверхностное натяжение, угол смачивания, содержание свободного формальдегида и прочность клеевого соединения при скалывании по клеевому слою и прочность при растяжении перпендикулярно пласти.
В процессе предварительных исследований установлено, что критическое поверхностное натяжение березового, осинового, соснового и лиственничного шпона составляет от 40 до 50 мН/м, то есть сопоставимо с поверхностным натяжениям фенолоформальдегидных смол без наполнителей и свидетельствует о способности древесины удовлетворительно смачиваться этими связующими. Кремнеземные дисперсные порошки, цеолитсодержащие породы являются эффективными реакционноспособными модификаторами, обладающими способностью ускорять процесс отверждения фенолоформальдегидных клеев, а шунгитовые сорбенты способны существенно снижать токсичность продукции.
Шунгитовые сорбенты представляют собой кварцеуглеродистый каркас из элементарных структурных звеньев, упакованных неплотно, поэтому архитектура шунгитовых сорбентов создает области свободных полостей, соединяющихся пересекающимися каналами [12, 13]. Эти каналы имеют молекулы, диаметры «входных» окон которых позволяют проникать в них молекулам, в данном случае формальдегида. То есть во внутренние полости по каналам в зависимости от размеров «входных» окон одни молекулы проходят, а другие отсеиваются. Положительные центры шунгита способствуют проникновению полярных молекул формальдегида во «входные» окна, и таким образом происходит снижение содержания токсичных продуктов в смоле.
свойства природных шунгитов
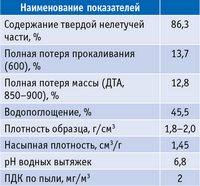
Кроме того, шунгитовые сорбенты являются термостойкими, они выдерживают без изменения свойств нагрев до 750 0С и устойчивы к действию концентрированных кислот. Природные шунгиты экологически безвредны, неканцерогенны и нерадиоактивны. Весь этот набор свойств дает широкие возможности использования их в процессах адсорбции, катализа и модификации. Основные физико-химические свойства природных шунгитов сведены в табл. 1. Для шунгитов Карельского месторождения минеральным субстратом послужила смесь глинистого, карбонатного, кремнистого материала с содержанием органики от долей процента? до 99%. В результате метаморфизма они превращаются в зеленовато-серые слюдисто-карбонатно-кварцевые сланцы тонкодисперсного сложения. Содержание главных минеральных составляющих: хлорит − 35−55%; плагиоклаз − 35−45%; кварц − 10−30%. Химический состав некоторых разновидностей шунгитов приведен в табл. 2.
К основным направлениям использования шунгитов относятся: производство фосфора, кремнистых ферросплавов, антикоррозионной техники, получение пигментов, противопригарных красок и адсорбентов. Есть основание полагать, что сорбционные возможности пород этого типа связаны с наличием в них первичных и вторичных слоистых силикатов в сочетании со специфической органикой. Этот минерал содержит 93−99% углерода как в аморфном состоянии, так и в виде сильно диспергированного графита [12, 13]. В нем могут присутствовать включения антроксолита. Кроме того, 3−4% в шунгите приходится на неидентифицированные соединения H (0,5−1,0%), N, O, S и H2O. Зольный остаток содержит V, Ni, Mo, W, Ce, As. Минерал образуется при метаморфизме (любой природы) битуминозных осадков. Шунгит блестящего черного цвета, с раковистым изломом, его твердость 3−4, плотность 1,8−2,0 т/м3; обладает высокой электропроводностью. При инфракрасной спектроскопии хлороформных экстрактов шунгитов обнаружены неуглеродистые структуры − сложноэфирные и спиртовые группировки, парафиновые и нафтеноароматические структуры [12, 13].

Таблица 3. Механические и санитарно-гигиенические свойства
фанеры
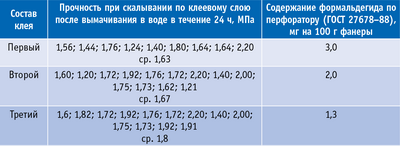
Поисковые исследования показали возможность применения шунгитовых наполнителей для снижения токсичности клееных древесных материалов в технологии склеивания плитных материалов клеями на основе феноло- и карбамидоформальдегидных смол. Шунгитовые сорбенты являются активными наполнителями и обладают способностью не только ускорять желатинизацию карбамидо- и фенолоформальдегидных смол, но и снижать содержание свободного формальдегида в готовой продукции.
Для проведения экспериментов использовалась карбамидоформальдегидная смола КФ-МТ-15 (ТУ 6-06-12-88).
В качестве сорбента применялся шунгит типа 7631/25 (Сорг = 0,75%) в виде мелкодисперсной смеси.
На основе смолы КФ-МТ-15 и шунгитов разработано три состава клеев для склеивания фанеры марки ФК. Результаты испытаний приведены в табл. 3.
Из результатов, приведенных в таблице, видно, что клеи с использованием в качестве сорбента формальдегида шунгитов позволяют снизить содержание свободного формальдегида в опытных образцах фанеры до 1,3 мг на 100 г абсолютно сухой фанеры.
Галина ВАРАНКИНА,
канд. техн. наук, доцент СПбГЛТА,
Анатолий ЧУБИНСКИЙ,
д-р техн. наук, профессор СПбГЛТА
Список литературы
- Кондратьев В. П., Кондращенко В. И. Синтетические клеи для древесных материалов. − М.: Научный мир, 2004. − 520 с.
- Кондратьев, В. П. Новые виды экологически чистых синтетических смол для деревообработки // Деревообрабатывающая промышленность. − 2002. − № 4. -с. 10−12.
- Доронин Ю. Г., Кондратьев В. А. Малотоксичные фенолформальдегидные смолы в деревообрабатывающей промышленности. Плиты и фанера // ВНИИПИЭлеспром. Обзорн. инф. − М., 1978. − Вып. 5. − 44 с.
- Доронин Ю. Г., Кондратьев В. П. Основные направления модификации синтетических смол. Плиты и фанера // ВНИИПИЭлеспром. Обзорн. инф. − М., 1985. − Вып. 4. − 44 с.
- Варанкина Г. С. Склеивание древесных клееных материалов на основе малотоксичных клеевых композиций: Автореф. дис. … канд. техн. наук. − СПб.: СПбГЛТА, 2000. − 24 с.
- Высоцкий А. В., Варанкина Г. С., Каменев В. П. Низкотоксичная клеевая композиция на основе КФС с алюмосиликатным наполнителем / Роспатент. Авт. свид. № 2114144 от 27.06.1998 г.
- Чубинский А. Н., Денисов С. В., Варанкина Г. С. Применение цеолитов в производстве низкотоксичных клееных материалов: Сб. науч. тр. − Красноярск. − 1999. − 128 c.
- Брутян К. Г., Варанкина Г. С., Глебов М. П. Новые наполнители для синтетических смол, применяемых в деревообработке. // Деп. в ВИНИТИ. − М.: № 369-В2003. − 30 с.
- Глебов М. П., Брутян К. Г. Анализ природных минеральных модификаторов для клеящих смол // Материалы международной научно-практической конференции. − СПб.: СПбГЛТА, 2007. − С. 28−33.
- Исследование цеолитов методом электронного парамагнитного резонанса // Unijn Carbide Cjrp., Tarrytown Techical Center, Tarrytown, N.Y. 10591.
- Казакевич Т. Н. Разработка режимов склеивания хвойной фанеры с использованием наполненной смолы СФЖ-3013 // Тезисы докладов областной научно-технической конференции. − Екатеринбург: УГЛТА, 1997. − С. 33−34.
- Луговская И. Г. Минералого-технологические критерии оценки тонкодисперсного рудного и нерудного сырья: Автореф. дис. … д-ра г.-м. наук. − М.: ФГУП ВИМС, 2007. − 48 с.
- Чубинский А. Н., Варанкина Г. С., Брутян К. Г. Совершенствование технологии склеивания фанеры // Известия Санкт-Петербургской лесотехнической академии. − 2007. − Вып. 179. − С. 167−175.