Рельефный погонаж
Рельефный погонаж
В классической греческой и римской архитектуре уже более двух тысячелетий используются протяженные архитектурно-пластические детали и сегодня называемые обломами или мулюрами, главные из которых имеют всего десяток сечений.
На их основе на фасадах зданий, в оформлении интерьеров или в изделиях мебели строятся профили различного рода поясков, выступов, карнизов, плинтусов, наличников, галтелей и т. д.
Мулюры и порезки
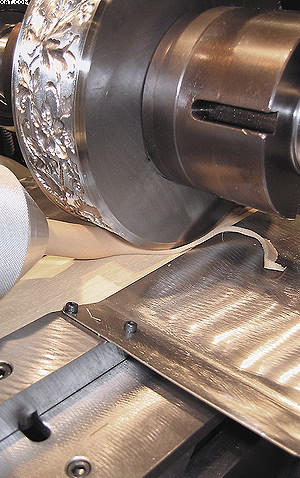
Рис. 1. Выдавливание пасты и накатывание роликом
рельефа на погонаже
По поперечному сечению классические обломы подразделяются на прямолинейные − полка или полочка, называемая также чембия или чимбия, − и криволинейные − валик, вал четвертной (прямой и обратный), выкружка прямая и обратная, гусек прямой и обратный, скоция и валик с полочкой (каблучок), которые могут комбинироваться друг с другом.
В строительстве они выполнялись из эластичной массы штукатурки путем протягивания шаблона вдоль закрепленной на стене линейки, изза чего стали называться у нас тягами. Позднее так же стали называть и поставлявшиеся строителям профильные прямолинейные заготовки из древесины довольно большой длины, которые раскраивали на детали по месту.
Мулюры могли и отливаться, например, из гипсовых или бетонных смесей. При этом на их поверхности иногда получали не искажавший профиля рельефный рисунок, в классическом зодчестве называемый порезкой.
Схожим способом порезки формировались и на тягах из древесины, которые в этом случае выполняли скорее роль наполнителя для массы из гипса или папьемаше, образовывавших рельеф. Но на деревянных тягах их долгое время можно было получить только вручную, поэтому в массовом производстве профили с ними практически никогда не изготавливались.
Промышленные способы создания рельефных узоров на погонажных заготовках разработаны и применяются уже давно, но, к сожалению, пока почти не известны подавляющему большинству наших деревообработчиков и мебельщиков.
Выпрессовывание рельефов
Древесина является термопластичным материалом, и при определенных условиях форму изготовленной из нее детали можно изменить под воздействием давления и зафиксировать. Это свойство древесины используется для получения рельефов на щитовых и брусковых деталях путем их обработки давлением − тиснением или горячим прессованием.
Тиснение − метод, при котором матрица, установленная на плите пресса и нагретая до температуры 200…300 °С, внедряется в поверхность помещенной в пресс заготовки из древесины, создавая на ее плоскости углубленный рельефный рисунок.
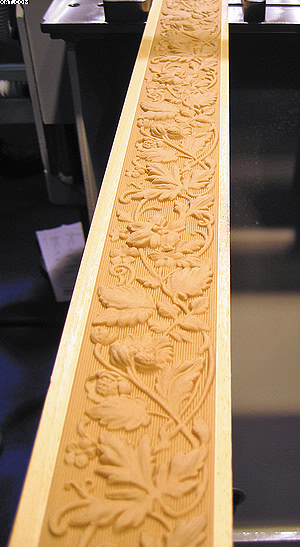
Рис. 2. Погонаж с тисненым рельефом на выходе
из станка
Существует три основных способа тиснения по древесине: обычное, при котором нагретая матрица может создавать на плоскости узор, заглубленный на величину приблизительно до 7 мм; вырубное тиснение, когда по периметру матрицы формируются заостренные выступы, продавливающие прессуемый материал почти на всю его глубину, после чего деталь шлифуется с обратной стороны до того момента, пока не будет отделена от основания; глубокое тиснение, когда штампованию подвергается заготовка, на поверхности которой в местах наиболее глубоких участков тиснения предварительно выфрезерован (удален) слой древесины определенной толщины. При обработке брусковых деталей наиболее распространен первый способ.
При высоких температурах нагрева матрицей прессуемой заготовки возможно изменение цвета ее поверхности. Однако потери прочности материала (обугливания) при этом еще не происходит. Наоборот, приобретение древесиной коричневатых или коричневых оттенков способствует выявлению структуры рельефа и повышению его выразительности. Кроме того, при окрашивании во время последующей отделки эти оттенки закрываются красителем и в готовом изделии вообще незаметны.
Под воздействием температуры прессующей матрицы в материале древесины происходят изменения, приводящие к расплавлению лигнина и соединению отдельных древесных волокон. Поверхность обрабатываемой детали приобретает специфический глянец, шлифования полученного рельефа не требуется, а при дальнейшей отделке не происходит поднятия ворса, что существенно снижает затраты на последующую обработку изделия вручную.
Матрицы изготавливаются из алюминия, стали или бронзы. Алюминиевые прессформы изза их низкой твердости обычно используются для тиснения простых рельефов. Их достоинство в том, что они могут быть получены способом литья по готовой модели. Стальные применяются для более глубокого тиснения, в том числе вырубного, но их острые кромки изза довольно низкой вязкости материала подвержены сколам. Кроме того, стальные формы могут быть получены только методом фрезерования металла с последующим гравированием. Наилучшие результаты дают прессформы, изготовленные из бериллиевой бронзы. Твердость этого материала составляет 80…90 ед. по Роквеллу и может быть увеличена за счет термообработки. Прессформы из бериллиевой бронзы можно получать литьем с последующим гравированием мелких деталей рельефа. Срок их службы составляет несколько лет. Поврежденные места этих прессформ могут быть отремонтированы путем наплавления и последующего гравирования.
Для получения стандартного неглубокого тиснения обычно достаточно усилия пресса 100...150 т. Прессы, специально разработанные для тиснения древесины, предлагают итальянские компании Kolmag и Italpresse. У них же можно получить и рекомендации по поставщикам прессформ.
Тиснение роликами
Недостаток способа получения рельефов на брусковых деталях тиснением в прессах − их ограниченная длина, определяемая размерами плит пресса и прессующей матрицы, которой, однако, вполне достаточно для изготовления накладных декоров, используемых в изделиях мебели.
Но для столярностроительных изделий − элементов оконных блоков, дверных полотен, наличников, элементов оформления интерьера зданий и т. д., − как правило, требуются детали длиной более двух метров.
Поэтому некоторыми европейскими (в основном итальянскими) фирмами были созданы станки проходного типа для горячего тиснения рельефов по натуральной древесине, клееной фанере и ДВП (MDF), обеспечивающие получение деталей неограниченной длины. Это станки, рабочим органом которых служит нагреваемый вращающийся приводной ролик из закаленной стали с выгравированным на поверхности контррельефом, способный продавливать в материале неглубокие рельефы (до 3 мм).
В станках этого типа заготовка, уложенная на плоский стол станка, базируется между двумя направляющими линейками, захватывается этим роликом и проходит под ним, в результате чего на ее поверхности отпечатывается рисунок. Обогрев рабочей поверхности ролика производится открытым пламенем газовой горелки. Рабочая ширина такого станка может составлять до 900 мм, что позволяет осуществлять тиснение не только на брусках, но и на щитовых деталях, например на филенках дверей корпусной мебели.
Характерной особенностью способа также является потемнение древесины по контурам тисненого рельефа, что оттеняет и дополнительно подчеркивает полученный рисунок.
Тиснение по пасте
Модификации таких станков используются также в технологии получения рельефов на брусковых погонажных деталях путем нанесения на них специальных паст (левкасов), тиснение по поверхности которых производится такими же роликами, имеющими на поверхности заглубленный рисунок.
Особенность конструкции станка состоит в том, что он оснащается экструдером, выдавливающим на поверхность движущейся детали пасту в виде непрерывной полосы, которая раздавливается роликом, распределяется по ширине профиля и подвергается тиснению. Излишки пасты отрезаются заостренными боковыми краями ролика (рис. 1), свободно удаляются вручную и затем вновь помещаются в расходную емкость для левкаса.
Формирование рельефа может производиться на всей поверхности плоской детали или только в отдельной зоне сечения профильного погонажа. Большая рабочая ширина станка позволяет производить обработку деталей в несколько потоков или устанавливать на его рабочий вал одновременно несколько роликов с разными профилями, которые используются поочередно. Ролики выпускаются несколькими европейскими компаниями, специализирующимися на их производстве. Рисунки для тиснения могут выбираться из их каталогов или по эскизам заказчика.
Пасты для тиснения поставляются в пластмассовых бочках массой 30...50 кг, откуда вручную загружаются в приемную воронку экструдера. Туда же помещаются излишки пасты, выдавленные изпод ролика, для повторного использования, благодаря чему достигается стопроцентное ее использование.
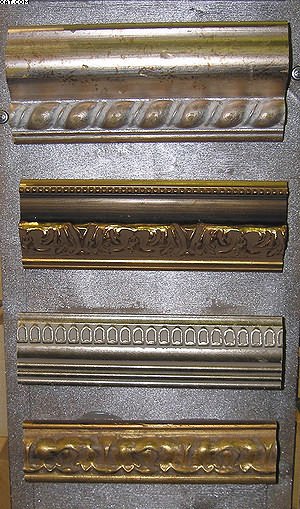
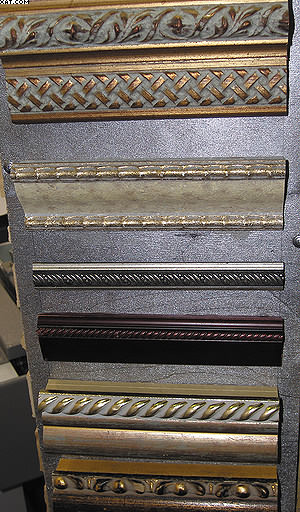
Рис. 4. Профили, отделанные методом термопечати
После формирования декора детали раскладываются на стеллажах, размещаемых в камерах или помещениях, снабженных необходимыми системами аспирации, так как из используемых паст выделяются пары растворителей, хотя и в весьма незначительном объеме. Время выдержки деталей до полного отверждения пасты при температуре воздуха около 20 °C составляет от 12 до 24 ч. Продолжительность сушки зависит от типа декора и относительной влажности воздуха. Поддержание правильного режима позволяет избежать образования трещин и повреждений на поверхности тисненого рельефа. После отверждения декоры, полученные таким способом, не требуют какойлибо доработки (рис. 2).
В дальнейшем пасты хорошо воспринимают красители и другие лакокрасочные материалы, что позволяет отделывать полученные рельефы в любой цвет, в том числе совпадающий с цветом основного материала изделия.
Термопечать
Рельефы, полученные из таких паст, можно также отделывать методом горячей печати, называемым еще «термопечать», «трансферная» или «термопереводная печать» и в последние десятилетия получившим в Европе довольно широкое распространение.
Метод позволяет отделывать брусковые и профильные погонажные изделия путем нанесения на их поверхность укрывистых красок, рисунков текстуры древесины и орнаментов. Он состоит в перенесении на поверхность изделия многокрасочного рисунка в обратном порядке слоев краски, нанесенного на поверхность термо и химически стойкой ленты, обычно из полиэтилентерефталата (нейлона, лавсана), под действием температуры и давления.
Ленты с рисунком производятся специализированными фирмами и могут иметь однотонные или фантазийные рисунки, имитировать цвета и структуру металлов (позолоты, серебра, бронзы и т. п.), а также текстуру древесины любых пород.
Для перенесения рисунка на плоскую или рельефную поверхность используются специальные станки, оснащаемые одним или несколькими агрегатами для термопечати (рис. 3).
Для того чтобы исключить повреждения рельефа, их накатывающие вальцы изготавливаются из эластичного термостойкого силикона. За счет высокой температуры (190…220 °С), создаваемой встроенным в эти вальцы нагревателем, происходит нагрев термопечатной пленки и расплавление красочного слоя, который сразу же припрессовывается к отделываемой поверхности, отделяется от пленкиосновы и переходит на подложку.
Термопечать может производиться не только по плоским, но и по профильным, а также по профильным рельефным поверхностям, для чего накатывающие силиконовые ролики предварительно профилируются. При обработке рельефов профильные ролики изнашиваются и требуют замены.
Их стойкость в зависимости от сложности и высоты профиля − до года непрерывной работы. Ширина деталей, отделываемых методом термопечати, может колебаться от 10 до 140 мм.
Станки для термопечати могут одновременно или последовательно наносить на одну и ту же деталь несколько рисунков (рис. 4).
При этом количество рабочих головок таких станков зависит от количества цветов и типа и размеров профилей. Средняя скорость подачи при термопечати составляет 6…7 м/мин.
Создание рельефных узоров на погонажных деталях, в особенности из паст, наносимых на заготовки из MDF и затем отделываемых термопечатью, − хорошая альтернатива простому облицовыванию гладких профилей бумажносмоляными пленками.
Ведь не секрет, что вкусы нашего потребителя часто склоняют его к приобретению изделий с довольно сложными декорами, украшенными резьбой и золотом.
А из таких профилей можно, к примеру, изготавливать не только карнизы, но и обвязы филенчатых дверей (межкомнатных и мебельных), наличники и даже плинтусы.
Причем стоимость необходимого оборудования относительно невелика, а при достаточно высокой загрузке оно может окупиться буквально за несколько месяцев.
Андрей ДАРОНИН,
компания «МедиаТехнологии»,
по заказу журнала «ЛесПромИнформ»