Фабрика «Е1». Шкафы-купе наступают
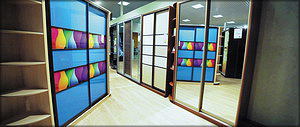
Год назад компания «КАМИ» организовала выезд делегации из РФ в Китай, на современный станкостроительный завод Nanxing, где тогда готовили к приемке и отгрузке в Россию первую автоматизированную линию Filato, произведенную специально для молодой и перспективной мебельной фабрики «Е1», выпускающей шкафы-купе в Краснодарском крае.
Еще тогда собственники предприятия - братья Михаил и Александр Линевичи - предложили нашему журналу посетить их фабрику год спустя, чтобы увидеть новое оборудование в работе. Предложение не могло не заинтересовать: хотелось не только убедиться в том, что линия Filato успешно работает, но и увидеть, как развивается молодая перспективная компания.
Производственная площадка «Е1» находится в окрестностях города Белореченска, в полутора часах езды от Краснодара. На участке 2,5 га построены цеха по раскрою и подготовке ДСП для поточного производства, сборке и упаковке шкафов-купе, выпуску шкафов на заказ, а также склад готовой продукции.
Новому оборудованию - новый цех
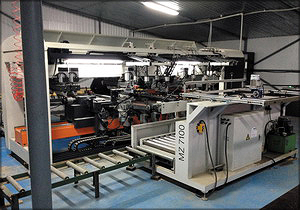
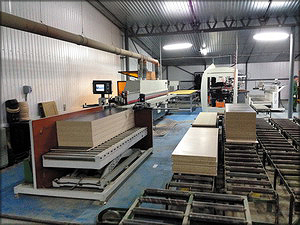
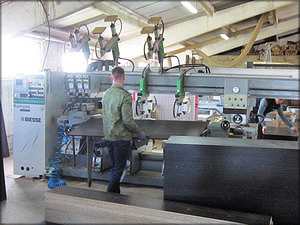
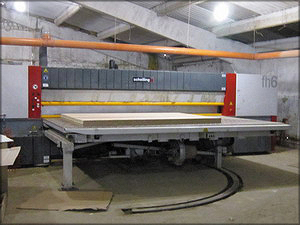
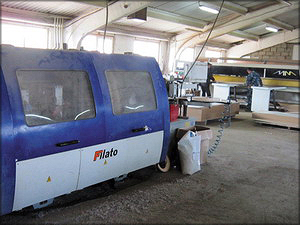
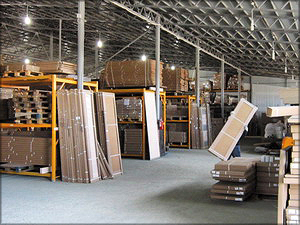
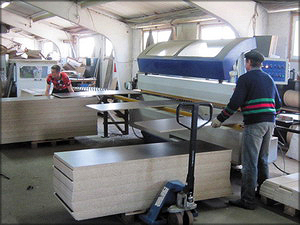
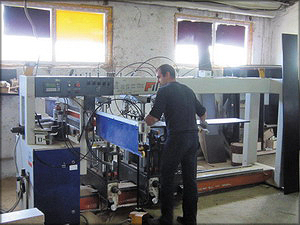
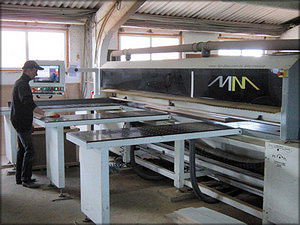
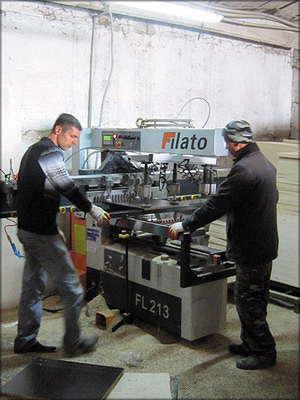
Линия Filato установлена в самом новом цеху площадью 650 кв. м, на ней выполняется раскрой, кромкооблицовка и присадка деталей из плитного материала - ДСП и HDF производства компании Kronospan. «Раньше мы заказывали сырье у Pfleiderer, но для наших растущих объемов их условия поставки оказались менее выгодными, чем у Kronospan», - поясняет Михаил Линевич, проводя экскурсию по предприятию. Здесь же, в цеху, находится склад материала, по вместимости примерно равный объему пяти-шести фур.
Пачки ДСП специальным вилочным погрузчиком подаются в зону загрузки раскроечного центра с ЧПУ Filato NPL 330 HG, который установлен в самом начале линии. Затем, уже в автоматическом режиме, пачки ДСП поступают в рабочую зону станка, где согласно заданным картам раскроя происходит пакетный раскрой на заготовки нужного размера. Далее, после раскроя, заготовки попадают на принимающие рольганги и потом с помощью транспортной системы перемещаются и перегружаются на автоматический стол подачи кромкооблицовочного станка Filato FL-4000U, который связан автоматическими рольгангами со сверлильно-присадочным станком Filato FL-13.
«13 марта прошлого года мы приняли это оборудование в Китае, в начале июня оно приехало к нам, - рассказывает Михаил Линевич. - Почти месяц ушел на монтаж, пусконаладку и обучение сотрудников - ведь оборудование было новым не только для нас, но и для наладчиков "КАМИ". На форматно-раскроечном центре с ЧПУ Filato NPL-330HG работают всего два человека: оператор и помощник, принимающий и убирающий готовые детали. Программное обеспечение, установленное на станке, - англоязычное, но очень простое и доступное. Сейчас "КАМИ" уже поставляет подобные станки с русскоязычным интерфейсом и предлагает нам бесплатно русифицировать программу, но в этом нет необходимости. Специфика нашего производства в том, что никаких сложных настроек мы не производим, у нас большими объемами идет серийная мебель, в этом цеху мы не делаем шкафы на заказ и, соответственно, каждый раз карты не перебиваем. В программу вводится одна карта раскроя - четко под определенные детали, и материал пилится по ней изо дня в день».
Смена карты раскроя происходит только в том случае, если в производство запускаются шкафы новых размеров, но такое бывает редко. Раскроечный станок, как и вся линия, «заточены» именно под серийный выпуск.
Фактическая производительность линии - 300-350 листов в рабочую смену (8 ч), то есть обрабатывается примерно одна фура материала.
«Сначала были некоторые накладки, связанные с незнанием оборудования, - продолжает рассказывать руководитель предприятия. - Наших сотрудников серьезно обучали во время шеф-монтажных работ, но ведь всех нюансов и тонкостей заранее не обговоришь.
И вызывать специалистов из Москвы по любому поводу не будешь, проще постепенно научиться самим. Мы довольно быстро разобрались, теперь наш техник знает эти станки от и до. Уже полгода они постоянно работают в две смены. Конечно, мы внимательно следим за соблюдением инструкции по обслуживанию станков. Гарантия на них - год, и этим летом она заканчивается. Нас это не пугает, пока все работает отлично, да и опыт покупки станков Filato у нас давний - ранее мы уже приобрели четыре кромочника Filato, они сейчас стоят в другом цеху. Среди них есть такие, которым три года и больше, и все работают. Думаем, что и с этой линией в дальнейшем все будет хорошо».
Данная линия станков Filato специально рассчитывалась под специфику работы предприятия «Е1», то есть на одностороннее кромление, когда торцы деталей облицовываются кромкой только с одной стороны (например, у шкафа-купе это вертикальные стойки и полки). Поэтому раскроенный материал загружается длинной стороной в односторонний кромочник, и тот облицовывает на нужной стороне кромку, а дальше деталь автоматически поступает в сверлильно-присадочный станок, в котором за один цикл совершается сверление всех технологических отверстий. После присадки детали выгружаются из станка тоже автоматически, с помощью приемного устройства.
Кромооблицовочный станок Filato FL-4000U снабжен функцией «обкатка углов» (автоматическое скругление углов заготовок в местах стыковки кромочного материала), но ее на «Е1» не используют. Для этого производства важнее другая особенность станка: на кромочнике установлен узел циклевки и полировки, который ножом сначала удаляет остатки клея с кромки и поверхности детали, а потом дополнительно полирует для блеска и затирки клеевого шва. К слову, клей компания закупает фирмы Kleiberit.
Особенность сверлильно-присадочного станка Filato FL-13 - большое количество сверлильных голов: 13 сверлильных групп по 21 шпинделю. Таким образом, всего получается больше 270 видов различного инструмента, который одновременно можно использовать при присадке. Этого хватает с избытком. Как правило, для изготовления одной детали требуется 15-20 сверл, зато большое их количество позволяет делать универсальную присадку на любой детали.
Линия Filato - высокотехнологичное, но в то же время простое и надежное оборудование, говорят на фабрике. Дополнительное удобство состоит в том, что станки соединены автоматической системой подачи. Не будь ее, большие и довольно тяжелые детали (каждая весит примерно 15-16 кг) пришлось бы переносить вручную, то есть за смену человеку нужно было бы поднимать тысячу раз по 16 кг (16 т в день!). В комплект поставки для «Е1» были включены две такие системы.
Выгрузка с форматно-раскроечного станка представляет собой стол с подъемным роликом, позволяющим регулировать его уровень и перекатывать на тележку стопку готовых деталей. Подъемный стол фабрика «Е1» заказала в «КАМИ», а ролики на него установили самостоятельно.
Все станки линии подключены к ЧПУ и системе датчиков. За счет этого обеспечивается высокий уровень безопасности. Если где-то производственный процесс нарушится, например, застрянет деталь, то остановится один станок, а за ним вся линия. Поэтому ситуация, когда, допустим, кромкооблицовка останавливается, а ролики продолжают крутиться и в итоге образуется затор, в данном случае невозможна.
«Хороший инструмент - важное условие производства качественной продукции, - подчеркивает Михаил Линевич. - Мы покупаем инструмент немецкой компании Leuco и очень довольны. У них отлично организован сервис в нашем регионе: инструмент доставляют прямо на фабрику, сами забирают на заточку и привозят обратно».
Сначала на фабрике «Е1» работали на пилах без алмазного напыления, но в последние 4-5 месяцев решили освоить алмазный инструмент, который реже обычного нуждается в заточке - в среднем раз в месяц. Увеличения производительности в компании не заметили, но экономить за счет заточки удается: алмазная пила стоит 45 тыс. руб., в 8 раз дороже обычной, но, поскольку точить ее нужно реже, меньше вероятность, что при замене она будет повреждена. Пока такие инструменты на фабрике используют не везде, но в дальнейшем планируют заменить алмазными все пилы.
В соседнем здании расположен склад. Здесь хранятся плитные материалы (всего вмещается объем, соразмерный с объемом десяти фур) и весь картон, который используется на предприятии. Картон рассортирован по размерам, идет с рилевками, прорезями - для того чтобы делать лоток. Картон фабрика закупает у компании «КартонТара» из Майкопа.
Сборка дверей-купе ведется в другом цеху. Ею заняты около 30 человек. Здесь же выполняется резка стекла и профиля. Размеры стандартные, режут только по прямой, все детали крупные. Из одного листа нарезают 5-6 зеркал почти без отходов. Работа преимущественно ручная - так и быстрее, и дешевле, убедились в компании.
В этом цеху собирают двери только с ЛДСП и зеркала, а фурнитуру сборщик добавляет на своем столе. Далее полностью готовую дверь упаковывают в картон. Цех работает здесь полгода, раньше двери собирали там, где сейчас организовано производство по индивидуальным заказам.
На любой вкус и цвет
Шкафы по индивидуальным заказам производят в отдельном цеху.
Для каждого изделия в соответствии с пожеланиями клиента подбирают материалы. Всего используется около 50 видов отделки разных цветов: десять вариантов цветного стекла, оклеенного пленкой; 15 видов экокожи (высококачественного кожзаменителя); натуральный бамбук пяти цветов; покрытие с фотопечатью и т. д. Шкаф, выполненный на заказ, в среднем в два раза дороже стандартного: например, шкаф с цветной печатью обойдется в 25-30 тыс. руб., тогда как цена стандартного колеблется от 15 до 18 тыс. Компания предлагает клиентам два каталога образцов фотопечати (для двух- и трехдверных шкафов) и около 500 вариантов образцов готовых дверей. Но если с отделкой можно «поиграть», то размеры шкафов остаются стандартными.
В цеху стоит итальянский форматно-раскроечный станок MacMazza с ручной фронтальной загрузкой (оператор загружает в него максимум три листа 16-миллиметровой ДСП). Стол снабжен функцией автоматического поворота, поэтому оператору не нужно вручную поворачивать стопку листов. «С одной стороны, это удобно, и оператор может работать в одиночку, с другой - времени затрачивается чуть больше, чем на поворот вручную, - поясняет Михаил Линевич, - к тому же второй человек все же нужен, чтобы успевать вынимать со станка готовые детали. Поэтому сэкономить, сократив число операторов, не получается. Когда создавался цех, этот станок нам предложила "КАМИ"" и он казался оптимальным вариантом по цене. Китайских аналогов тогда еще не существовало».
Также цех оборудован станками производства Biesse и Schelling. По словам главы компании, они достались фабрике б/у около 5 месяцев назад - были приобретены при закрытии завода «Волгоград-Мебель». «Если бы не срочность, купили бы еще Filato, - говорит глава компании, - но тогда ждать полгода заказ не могли: резко вырос спрос на серийные шкафы, и часть этого цеха нам пришлось также выделить под серийку». В цеху Filato делают только стоевые, то есть боковины шкафов, а здесь - крышу и дно. Полки - в соседнем здании.
В этом цеху также работают два новых кромкооблицовочных Filato - FL4000 и FL430, купленные три месяца назад.
Склад цеха при полной загрузке вмещает 6 тыс. шкафов, но обычно там хранится 2-3 тыс. Этот запас делается главным образом для стабильности поставок: если сломается и встанет на 2-3 недели какой-нибудь станок, заказчики все равно получат мебель в срок.
Начинали с нуля
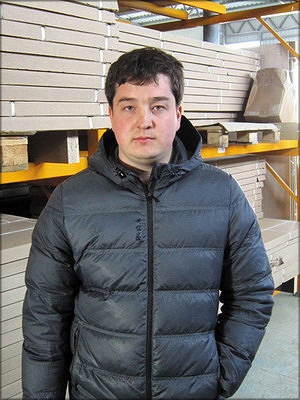
«Заниматься производством мебели на заказ мы решили в 2006 году, - рассказывает Михаил Линевич. - Что называется, с нуля. Друзья нашей семьи занялись производством и продажей кухонь, у них были арендованы небольшие, около 200-300 кв. м, производственные площади, где предложили делать кухни и нам. Попробовали, стало получаться».
Сначала в компании работали 10 человек. Не имея опыта в подобном производстве, начинающие мебельщики искали информацию в СМИ, на выставках, дотошно расспрашивали поставщиков оборудования. В итоге уже в 2007 году открыли свой салон мебели на заказ. Но объемы были невелики, и пришло понимание, что выпуск серийной стандартной мебели будет гораздо выгоднее.
Решено было перейти на поточное производство. Для этого в 2011 году выкупили площадку, где сейчас и находится производство. Тогда на ней стояли только полуразрушенные здания - остатки заброшенной лет десять или пятнадцать назад фермы, точнее перевалочной базы для зерна с ближайших полей.
«Мы привели территорию и здания в порядок, открыли цех по производству шкафов на заказ, а затем построили здание цеха под Filato, заказали линию в кредит на сумму 10 млн руб., получили ее и с прошлого лета запустили серийное производство», - рассказывает Михаил Линевич.
Сейчас общий объем производства - 2 тыс. шкафов в месяц, 90% приходится на стандартные (восьми размеров и трех цветов) шкафы-купе, а 10% - шкафы под индивидуальный заказ. Всего на производстве задействовано 150 человек: восемь посменно работают в цеху с линией Filato, 30 - в цеху сборки, 25 - в цеху индивидуальных заказов. Персонал в основном молодой, текучесть кадров минимальная, так как оплата вполне достойная: 15-25 тыс. руб., а у квалифицированных рабочих (операторов станков) - 30-40 тыс. При этом оплата сдельная и зависит от производительности труда. Кстати, практика показывает, что некоторые женщины способны работать даже эффективнее мужчин и зарабатывают не меньше, а то и больше многих из них.
Все стандартные шкафы реализуются через широкую сеть собственных магазинов компании. Александр Линевич отвечает за сбыт. Сейчас у «Е1» 60 магазинов в ЮФО, из них 15-20 (в Сочи, Адлере, Анапе, Новороссийске) работают по франчайзингу.
«В конце марта мы открыли собственные магазины в Москве - пока только два, но надеемся, что со временем их будет 30 или 40. Собственными магазинами проще управлять, - поясняет Михаил Линевич. - У каждого владельца магазина есть свое мнение об организации процесса, и с некоторыми из них бывает сложно что-то согласовать. Например, мы решили провести какую-то акцию или предложить покупателям определенные условия доставки в магазинах всех городов, а кто-то из собственников точек может не согласиться. Иногда они ориентируются на текущую ситуацию, меньше думая о перспективе».
Средние затраты на открытие одного магазина - около 500 тыс. руб., включая расходы на выставочные образцы, арендную плату за первый и последний месяцы, персонал и рекламу. Как правило, через месяц-полтора магазин уже выходит на окупаемость.
По словам Михаила Линевича, конкуренты не дремлют, но в ЮФО никто не производит такую же продукцию в таком объеме и в такие сроки. Любой заказ «Е1» может выполнить в течение семи дней.
«Мы не экономим на качестве - не стремимся купить более дешевые кромку и клей, чтобы снизить цену, - говорит глава компании. - Зато стараемся оптимизировать раскрой, уменьшить количество брака, договориться с поставщиками о льготах на сырье и т. д. Уже сейчас процент брака на поточной линии не превышает 2%. За годы накопленного производственного опыта мы пришли к выводу, что зарабатывать нужно и на минимизации всех возможных затрат, учитывая тонкости производства. Мне самому для души надо, чтобы на производстве все было логично сделано».
В планах – пятикратный рост
Спрос на продукцию «Е1» растет, соответственно растет и сбыт, поэтому компания планирует увеличивать мощности. «Раскрою карты, - говорит Михаил Линевич. - Первый опыт сотрудничества с "КАМИ" по поставке автоматизированной линии Filato нас полностью устроил, и мы уже подписали с компанией договор на приобретение еще четырех точно таких же линий; в каждую входит форматно-раскроечный центр с ЧПУ, кромкооблицовочный и сверлильно-присадочный станки. С "КАМИ" мы начали работать, когда стали закупать первое оборудование для мебельного производства. Выбор в их пользу был сделан по объективным причинам: устроили и спектр услуг, и степень надежности сервиса. На наш взгляд, эта компания была и остается лидером по продаже станков в эконом- и среднем сегментах, но в то же время активно развивается в направлении поставки оборудования премиум-сегмента. Мы оценивали их по уровню сервиса и количеству филиалов. В Краснодаре был их офис, нам удобно было к ним обращаться. И с заказом линии Filato из Китая у нас сомнений не возникало: даже если бы оборудование нас подвело, "КАМИ", мы уверены, решили бы проблему в нашу пользу».
Помимо расширения производства компания намерена оптимизировать его организацию. «Из-за того что наш бизнес развивался постепенно, без заранее продуманного плана, на этой площадке накопилось много ошибок, - признается генеральный директор фабрики. - В поселке регулярно возникают перебои с электричеством, здания цехов находятся далеко друг от друга, что усложняет внутреннюю логистику, станки под одни задачи пока стоят в разных зданиях. Из-за этого страдает эффективность труда, мы теряем деньги. Есть разница: позволяет технологический процесс сразу упаковать произведенную деталь после раскроя или ее еще нужно повозить по цеху. Только в новом цеху с линией Filato установка оборудования соответствует логике технологического процесса.
Понимая, что логика производства с одной стороны и растущий спрос с другой требуют перемен, мы приняли решение о постепенном переезде на новую производственную площадку. На днях мы определились с местом, будем выкупать территорию площадью 7,5 га и строить одно большое здание, чтобы все цеха были под одной крышей. Кстати, новая площадка находится в городе Белореченске, и нам будет проще набирать персонал. После запуска нового производства нынешняя площадка еще будет работать, но, возможно, мы ее закроем».
Кроме четырех линий Filato, на новом производстве планируется установить современную аспирационную систему, а также котельную (скорее всего, марки «Гефест»), которая будет обеспечивать теплоснабжение производственных площадей только за счет использования отходов производства.
По планам руководства «Е1», источником для инвестиций и в строительство фабрики, и в приобретение новых линий Filato (которые обойдутся в полтора раза дороже, чем первая, «рекламная» поставка) станут оборотные средства компании. «Уже сейчас мы прирастаем примерно на 20% в месяц, - говорит Михаил Линевич, - а в ближайшие полгода рассчитываем вырасти и по объемам, и в денежном, и в штучном отношении примерно в два раза».
Хочется выразить надежду, что у братьев Линевичей все получится, все планы реализуются, и еще через год мы увидим уже новое, с чистого листа организованное производство.
Светлана Яровая
Фото автора и компании «Е1»
Благодарим компании «Е1» и «КАМИ» за помощь в подготовке статьи