Современные строительные материалы из древесины
Современные строительные материалы из древесины различаются по способу, степени и характеру механической обработки, в зависимости от которых определяются и сферы их использования. Применение новых материалов позволяет сократить сроки строительства, облегчить конструкции, сэкономить энергию.
Ввиду теплотехнических свойств (теплопроводности, сопротивлению теплопередачи) материалы из древесины часто применяются в строительстве. В настоящее время объемы строительства из новых материалов в разных отраслях экономики, в том числе и в домостроении, стремительно растут. Одним из наиболее распространенных современных строительных материалов на Западе являются CLT-панели (Cross Laminated Timber), представляющие собой перекрестно склеенные ламели из хвойных и лиственных пород. По толщине эти панели могут варьировать от 6 до 40 см, в длину могут достигать 24 м, в ширину – 1,25–3,5 метра.
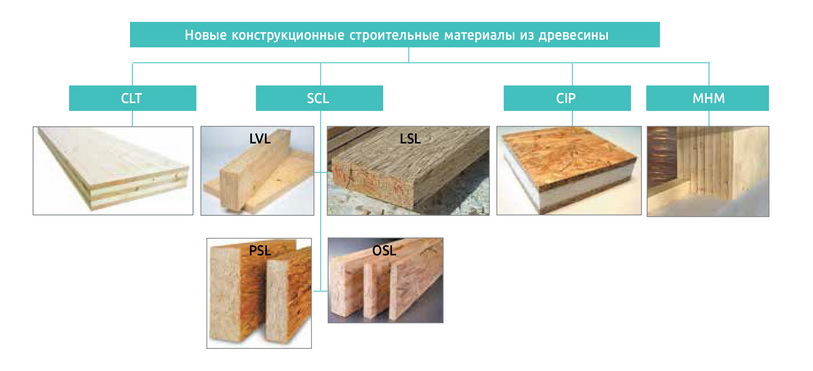
Первые образцы этого материала были разработаны в Австрии в 1996 году, хотя изначально идея строить дома из подобных панелей возникла в Швейцарии. Австрийцы заинтересовались новым материалом и усовершенствовали его, придав ему современный облик. Первый завод по выпуску CLT-панелей был открыт компанией KLH в Австрии. С начала 2000-х применение CLT-панелей в мировом строительстве постоянно увеличивалось, с 2000 по 2005 год ежегодный прирост составлял около 20%. В 2013 году потребление панелей составляло уже 540 тыс. м3.
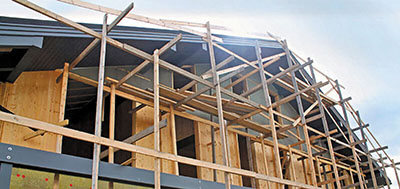
Пиломатериалы, высушенные в камерах до влажности 12±2%, строгают, затем они проходят контроль геометрических параметров и сращиваются по длине в ламели на клеевой шип. Склеивание ламелей в панель осуществляется под давлением с помощью полиуретановых клеев или меламиновых клеевых систем с классом эмиссии Е1.
Помимо склеивания, существуют методы соединения ламелей алюминиевыми гвоздями и металлическими скобками, но сделанные из них CLT-панели не получили широкого распространения из-за низкой сопротивляемости горению.
В течение короткого периода технология производства CLT-па- нелей быстро распространилась не только в странах Европы, но и Северной Америки. Сейчас предприятия, производящие CLT-панели, есть повсеместно. Наиболее известные: KLH (Австрия, Великобритания, Швеция); Stora Enso, Thoma Holz GmbH и Binderholz (все – Австрия); Martinsons (Швеция); Moelven (Норвегия); FinnForest Merk (Германия/Великобритания); HMS (Германия).
Деревянный дом, построенный из CLT-панелей, характеризуется повышенной сейсмостойкостью: в ходе одного из экспериментов, проводившихся за рубежом, семиэтажное здание выдержало 14 последовательных сейсмических толчков магнитудой семь баллов, повреждений почти не было.
Испытания зданий, возведенных из CLT-панелей, которые были проведены в Японии в 2007 году, доказали, что подобные строения могут выдержать землетрясения силой до девяти баллов. Сегодня Страна восходящего солнца опережает по объему строительства из CLT-панелей Канаду и некоторые европейские страны.
В 2014 году в нескольких странах Европы (Австрии, Германии, Швеции, Англии и Норвегии) насчитывалось восемь крупных компаний, которые занимались производством CLT-панелей. Несколько лет назад появились два крупных производителя перекрестно-клееных панелей в Канаде, планируется открытие новых заводов в США.
Увеличение числа предприятий свидетельствует о растущем спросе на эту продукцию. На 2019 год запланирован пуск производства CLT-панелей на российском предприятии в г. Соколе.
Основные характеристики CLT-панелей представлены в табл. 1.
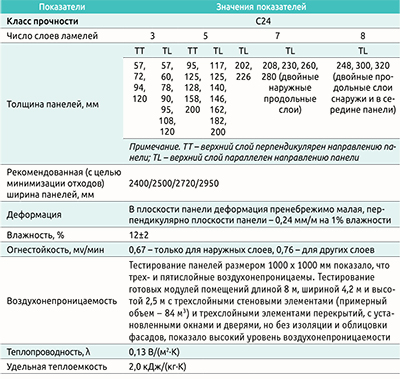
Основная сфера применения современных строительных материалов – возведение зданий и сооружений. Так, например CLT-панели, которые обладают высокой несущей способностью, используются при строительстве высотных зданий, большепролетных сооружений и конструкций, мостов, спортивных сооружений и т. д.
Основные достоинства этих панелей: пожаробезопасность, стабильность геометрических размеров, небольшая масса (по сравнению с кирпичом и брусом), высокая сопротивляемость статическим нагрузкам, возможность изготовления панелей с неограниченными габаритами (они зависят от характеристики используемого оборудования и условий транспортировки), высокая экологичность.
Но есть и недостатки. Производство этого материала требует использования дорогостоящего оборудования, что сказывается на цене панелей. При возведении зданий из CLT-панелей в тех регионах, где преобладает низкая температура окружающей среды, требуется утепление стен, что приводит к дополнительным затратам.
Говоря о перспективах материала, следует отметить, что в Европе объемы производства деревянных панелей высокой заводской готовности, а также спрос на них растут на 20% в год. Так, например, в 2011 году в Европе было произведено 425 тыс. м3 панелей CLT. В основном они используются в строительстве общественных зданий: стадионов, школ, больниц, торговых центров и т. д. Во многом высокий спрос на этот материал объясняется его экологичностью. Немаловажным фактором является и то, что квадратный метр готового дома из CLT-панелей дешевле квадратного метра дома, построенного из конкурентных материалов.
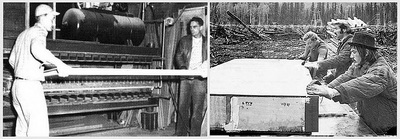
Панель CIP (Structural Insulated Panel), или структурно-изоляционная панель (СИП), согласно ГОСТ 32567-2013, состоит из двух листов плиты OSB, между которыми находится наполнитель. Этот продукт, который производят в промышленных условиях, полностью готов для строительства сооружений разного назначения. СИП могут быть разных размеров и толщины, допускается вариативность наполнителя. Плитные материалы склеивают под высоким давлением, что позволяет использовать их не только для создания стеновых конструкций, но и в качестве плит перекрытия и кровли.
Идею создания CIP-панелей в 1930-х годах выдвинул архитектор компании Usonian (США) Фрэнк Ллойд Райт. Первые CIP-панели состояли из двух слоев фанеры, между которыми был проложен пропитанный гудроном картон. Усовершенствовал CIP-панели ученик Райта и брат основателя корпорации Ольден Доу. Руководствуясь желанием создать экономный и практичный материал, он в 1950 году создал конструкционную панель с внутренним изоляционным слоем.
В 1951 году специалисты химического концерна BASF изобрели пенополистирол, на который сразу же обратили внимание производители домов из CIP-панелей.
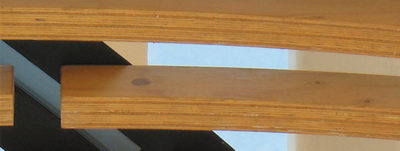
В 1952 году в США стали изготавливать панели, в которых между двумя слоями фанеры был проложен пенополистирол. Дома, построенные из новых панелей в этом же году в штате Мичиган, считаются первыми домами из CIP-панелей.
Массовое производство CIP-панелей на основе фанеры и полистирола началось в 1959 году американской корпорацией Koppers. В 1982 году в канадской провинции Альберта, на заводе Edison OSB изобрели OSB-плиты. Этот материал почти сразу стал пользоваться спросом у производителей CIP-панелей.
Согласно данным информационной службы «Века», сегодня более 80% малоэтажного жилья в США, Канаде, Японии составляют дома из CIP-панелей. По этой технологии в Японии и Канаде возводятся даже 9-этажные дома.
В нашей стране СИП появились в 1950-е годы, дома, построенные из них, назывались «финскими», но тогда технология не вызвала большого интереса у отечественных домостроителей, так как шла вразрез с технологиями традиционного домостроения. Возрождение интереса к этим панелям пришлось на 2000-е годы, когда на рынке появились усовершенствованные СИП, а российские производители стали в процессе изготовления придерживаться передовых технологий.
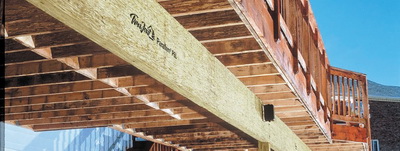
В 2003 году компания из г. Калгари EcoPan corporation, которая в Канаде является лидером отрасли, вышла на российский рынок с технологией строительства быстровозводимых домов из СИП (поэтому у ее называют «канадской технологией»).
Утеплители, то есть внутренний слой, могут быть разными: пенополистирол, пенополиуретан, стекловолокно, минеральная вата.
По типам материалов для наружных слоев СИП можно разделить на следующие виды панелей:
- с плитами OSB (и ППС – с пенополистиролом в качестве внутреннего слоя); СИП с наружными слоями из плиты OSB – наиболее распространенный тип CIP-панелей в Европе. У панели шириной 1,25 м и длиной 2,5–2,8 м толщина зависит от толщины плит OSB (6–25 мм) и листов ППС (100, 150, 200 мм). При соблюдении технологии изготовления подобная панель может выдержать вертикальную нагрузку до 10 т и поперечную нагрузку до 2 т. Вес панели габаритами 2500×1250×174 мм – 56 кг;
- с цементно-стружечными плитами (ЦСП), внутренний слой – ППС; размер панелей – 3,0×1,2 м, вес – 120 кг, у подобных панелей высокая огнестойкость. Применение панелей с ЦСП в строительстве позволяет возводить дома, которые по функциональности не уступают зданиям из газобетонных блоков, однако CIP-панели дешевле и практичнее, к тому же легче. Их недостаток – хрупкость;
- со стекломагниевыми листами (СМЛ), внутренний слой – ППС; размеры панели – 1,22×2,44 м, вес элемента – 68 кг. Использование ППС во внутренних слоях обеспечивает большую прочность панели при изгибе. Панель с СМЛ не горит (ей присвоен класс НГ), легко раскраивается и поддается отделке, у нее высокая адгезия ко всем строительным штукатуркам;
- панели с плитами OSB (и минеральной ватой в качестве утеплителя), изготавливаются преимущественно размером 1,22×2,44 м, но толщина утеплителя не может быть больше 150 мм, а значит готовое изделие должно быть не толще 174 мм. Минеральная вата – экологичный материал, но весит больше, чем другие утеплители. Плотность материала – 115–150 кг/м3, вес готовой панели – до 90 кг, поэтому для возведения частных домов этот материал используется довольно редко;
- панели с плитами OSB (и пенополиуретаном в качестве утеплителя и несущего материала). За счет высокой прочности пенополиуретана, превосходящего по своим физико-механическим характеристикам пенополистирол, толщина панелей для строительства может составлять всего 60 мм. В качестве примера приведем основные характеристики CIP-панелей толщиной 174 мм с плитами OSB-3 в качестве наружных слоев (толщина плит 12 мм) и пенополиуретаном ПСБ-С-25 в качестве среднего слоя (толщина 150 мм): теплопроводность – 0,039 Вт/м·ºС (норма для средней полосы России); паропроницаемость – 0,013 Мг/(м·ч·Па); огнестойкость – класс Г4.
У зданий и сооружений, возводимых из СИП, множество достоинств:
- хорошие теплоизоляционные характеристики; «канадские» дома отличаются более высокой степенью теплоизоляции, чем здания из кирпича: чтобы достичь такого же низкого коэффициента потерь, как у панели толщиной всего 17 см, потребуется сложить из кирпича стену толщиной не менее 2,5 м;
- высокая огнестойкость;
- хорошая звукоизоляция – пенополистирол препятствует проникновению шума с улицы;
- невысокий вес общей конструкции – масса 1 м2 панели – 15–20 кг (в зависимости от толщины), для сравнения: 1 м2 кирпичной кладки может весить более 0,5 т. Вследствие этого дома из CIP-панелей не нуждаются в мощном и дорогостоящем фундаменте, для постройки зданий «канадского» типа достаточно мелкозаглубленного ленточного;
- сжатые сроки строительства: к примеру, двухэтажный загородный коттедж общей площадью 50 м2 возводится под ключ за три недели; • строительство возможно в любое время года;
- экономия: благодаря небольшому весу панелей их легко транспортировать и разгружать, что позволяет сэкономить на доставке и услугах грузчиков;
- устойчивость к действию агрессивной внешней среды, в том числе и биологической (например, плесени или грибка); • возможность поэлементной сборки конструкций дома;
- простота и высокая скорость возведения строений;
- отсутствие необходимости в дополнительной отделке;
- доступная цена: CIP-панели на 40% дешевле бетона, кирпича и массива древесины.
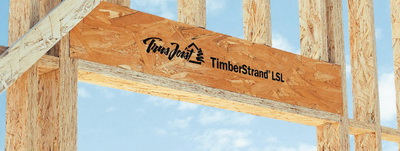
Основные минусы зданий и сооружений, возводимых из СИП: необходимость точной сборки и обеспечения герметичности, так как без устройства вентиляции со временем на стенах могут появиться плесень и грибковые поражения.
Сегодня строительство из СИП широко распространено, их используют не только в частном домостроении, но и для строительства коммерческих зданий, промышленных и муниципальных. Также эти панели применяются для устройства стеновых, кровельных перегородок, перекрытий и несущих конструкций, теплых веранд, мансард и крыш, гаражей и пристроек к дому, дополнительных этажей.
Помимо деревянных клееных конструкций, в которых в качестве армирующих элементов служат пиломатериалы (ламели), в современном строительстве используется немало перспективных древесно-композитных конструкционных (ДПК) материалов, объединенных под названием SCL (Structural Composite Lumber, конструкционная композитная древесина). Наиболее известные продукты этой группы: LVL-, PSL-, LSL- и OSL-брус.
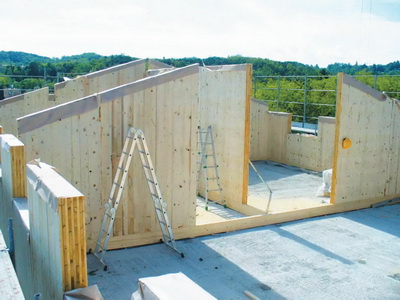
Эти материалы отличают следующие особенности: высокая прочность, однородность свойств и характеристик по всему объему, стабильность структуры и отсутствие усадки, долговечность, небольшой вес. Кроме того, они обеспечивают возможность архитектурного и творческого разнообразия в строительстве.
LVL-брус (Laminated Veneer Lumber) – брус, склеенный из листов однонаправленного лущеного шпона (с параллельным расположением волокон в смежных слоях). Это пока единственный материал из группы SCL, который производится в России: одно предприятие – «Талион Терра» – находится в Тверской области (в г. Торжке), другое – в Ханты-Мансийском АО (первая тысяча кубометров LVL-бруса была выпущена в феврале 2004 года на ОАО «ЛВЛ-Югра»). LVL изготавливается в виде плит, брусьев, брусков, досок.
По мнению аналитиков рынка, в 2018 году объем потребления LVL вырастет в мире до 5,2 млн м3 при среднегодовом росте 12%. Для примера, потребление LVL в Европе увеличилось за последние пять лет на 21%. Мощности заводов, расположенных в странах ЕС, почти полностью удовлетворяют потребности местного рынка. В Северной Америке, где каркасные дома в общем объеме строительства малоэтажного жилья составляют почти 90%, потребление и производство LVL неуклонно растет: в 2018 году спрос на изделия из LVL, по прогнозам, составит 3,2 млн м3.
Основные характеристики LVL-бруса, согласно ГОСТ 33124-2014, приведены в табл. 2.
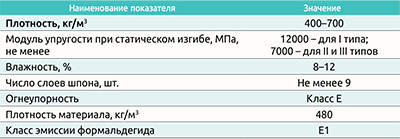
Сферы применения LVL-бруса весьма разнообразны: строительство спортивных сооружений, ангаров, загородных домов, производство окон, мебели, дверей и т. д. Этот материал может выступать в качестве элемента несущих конструкций и часто заменяет цельные и клееные из пиломатериалов балки, особенно при изготовлении элементов сложной формы и большой длины.
По прочностным характеристикам LVL-брус подразделяют на три группы: I, II и III.
PSL-брус (Parallel Strand Lumber, Parallam) – брус, склеенный из длинных (не менее 1000 мм) листов шпона. Основной сферой его применения является изготовление большепролетных конструкций, испытывающих высокие нагрузки, а также производство двутавровых балок. В России Parallam пока не производится.
PSL под маркой Parallam выпускает на предприятиях Канады и США компания Weyerhaeuser. Сырьем для производства Parallam служит древесина дугласии, сосны желтой, лириодендрона, тсуги западной.
Начинается процесс переработки с лущения древесины на шпон; технология аналогична применяемой при производстве фанеры. Далее шпон транспортируется в сушильную камеру, затем нарезается на ленты и сортируется. На ленты наносится клей, и из них собирают непрерывную заготовку-пакет, которая поступает в ленточный пресс с подогревом. Полученный материал заготовки раскраивается на брус, балки необходимого сечения и длины (стандартное сечение PSL Parallam – 30,5×30,5 см или 30×45,7 см, длина – до 18 метров).
Еще два вида бруса из группы SCL, которые пока не производятся у нас в стране, это LSL (Laminated Strand Lumber) и OSL (Оriented Strand Lumber). Брус LSL получают путем раскроя плит, которые изготавливают из длинных плоских стружек, уложенных в ковре плиты параллельно друг другу; OSL-брус (Оriented Strand Lumber) получают подобным способом, но для изготовления плит используется стружка в два раза короче, чем для бруса LSL.
По прочности и жесткости оба материала уступают PSL и LVL, зато в процессе их производства достигается максимальная глубина переработки древесного сырья и возможно использование низкосортной древесины. В североамериканском строительстве LSL и OSL применяются для изготовления стоек и ригелей каркасных домов.
При изготовлении несущих элементов зданий и сооружений все шире применяются современные строительные композиционные материалы из древесины, которые вытесняют традиционные балки из бетона и металла, что обусловлено более высокими физико-механическими характеристиками древесных композитов и меньшей массой конструкций из них.
Панели МНМ (Massiv-Holz-Mauer) все еще остаются новинкой на российском рынке деревянного домостроения, тогда как во многих странах Европы дома из МНМ-панелей уже получили широкое распространение. Технология производства МНМ-панелей разработана в Германии, где уделяется большое внимание качеству жизни.
МНМ-панели производят из обрезных досок древесины хвойных пород толщиной 24 мм, высушенных до влажности 12,4%. У каждой доски стеновой панели по боковым кромкам есть выборка четверти (фальца) для стыковки со смежными досками. Смежные слои досок скрепляются алюминиевыми гвоздями, так как при дальнейшей механической обработке изделия алюминиевые гвозди не представляют угрозы для дереворежущего инструмента.
Для изготовления стен могут использоваться доски разной ширины. Особых требований к качеству пиломатериалов не предъявляется. Для панелей подбирается древесина, в основном 3–4 сорта, тангенциального распила, без сортировки. Размеры выпускаемых по технологии MHM-панелей: высота – 3,25 м, длина – до 6 м. В зависимости от климатической зоны, в которой ведется строительство домов из этих панелей, толщина наружных панелей стен может варьировать от 340 мм (15 слоев досок) до 160 мм (семь слоев), число слоев досок должно быть нечетным. Толщина панелей внутренних стен 160 или 115 мм.
Толщина панелей может быть от 115 до 345 мм. Стена из МНМ-панелей за счет их высоких изоляционных характеристик, обусловленных физическими свойствами древесины, представляет собой массивную конструкцию, а благодаря крестообразной конструкции досок, составляющих МНМ, не подвержена усадке и усушке, ее форма остается стабильной.
Дома, построенные из панелей MHM, соответствуют европейским стандартам по тепло-, звукоизоляции, ветрозащите, однако огнестойкость подобных сооружений очень низкая. В настоящее время проведена сертификация в системе «Госстандарт России» на пригодность панелей для эксплуатации в регионах Сибири. Результаты испытаний стен из панелей МНМ показали, что по ряду параметров они превосходят аналогичные по параметрам стены из бруса, бревна и других материалов. Например, показатель теплоизоляции стены МНМ при толщине 345 мм соответствует теплопроводности стены из кирпича толщиной один метр.
Основными достоинствами домов из панелей MHM являются массивность стен, высокое качество, стабильность формы, повышенная сейсмоустойчивость. Не меньшее значение имеет и высокая скорость изготовления панелей за счет автоматизации производства, быстрота монтажа благодаря высокой степени заводской готовности панелей. При строительстве домов с наружными ограждающими стенами максимальной толщиной 345 мм не требуется дополнительного утепления. И конечно, не нужно забывать про экологичность дома, ведь при его строительстве используются только древесина и алюминий. Кроме того, стены из панелей МНМ защищают от воздействия вредных электромагнитных излучений: монолитная конструкция может элиминировать до 95% электромагнитных радиоволн. Кроме того, древесина является воздухопроницаемым материалом и регулирует влажность воздуха в помещении.
Технологическая линия немецкой компании Hundegger по производству стеновых панелей из массивной древесины работает на заводе «Электросигнал» с 2006 года. За это время по технологии MHM реализовано несколько проектов: в р. п. Колывань Новосибирской области по заказу районной администрации построен 14-квартирный жилой дом; изготовлено несколько домов для частных заказчиков. Технология доказала свою конкурентоспособность, и сейчас в р. п. Колывань ведется комплексная малоэтажная застройка земельного участка площадью 3,6 га. Уже утвержден генплан, согласно которому планируется построить 23 дома.
По технологии строительства из панелей МНМ можно возводить не только жилые дома, но и детские сады, гостиницы, медицинские учреждения и другие бытовые помещения. Итак, древесно-композитные конструкционные материалы в силу их многочисленных достоинств и высоких качественных характеристик, а также преимуществ перед традиционными строительными материалами выгодно производить и использовать для возведения домов самого разного назначения.
Древесно-полимерные композиты в строительстве
Применение новых материалов, изготовленных на основе древесины, позволяет сократить сроки строительства, облегчить конструкции, сэкономить энергию. К подобным материалам, приобретающим все большую популярность, относятся и древесно-полимерные композиты (ДПК) – композиционные материалы, содержащие полимер и древесный наполнитель, модифицированный химическими добавками.
Появление композиционных материалов на основе древесины связано прежде всего с истощением древесных ресурсов. Кроме того, эксплуатационные характеристики изделий из ДПК превосходят характеристики изделий из натуральной древесины или древесно-стружечных плит. Другие плюсы: низкая стоимость сырья, безотходность производства, эффективность технологического процесса.
В состав ДПК входят три основных компонента: частицы измельченной древесины или древесная мука фракцией 0,5–2 мм (некоторые производители для удешевления продукции добавляют в состав рисовую шелуху или жмых семечек) – 50–70% массы материала; термопластичный полимер (поливинилхлорид, полиэтилен, полипропилен) – 30–50%; модификаторы – химические добавки (до 5%).
Древесно-полимерный композит создан в Италии. В 1974 году концерн ICMA San Giorgio получил патент на изобретение этого материала, состоящего из древесины и полипропилена в соотношении 1:1 и выпускавшегося под маркой Wood-Stock.
Первое профильное предприятие по производству ДПК появилось в Швеции во второй половине 1970-х годов. К сожалению, спрос на новый материал оказался на тот момент незначительным, а износ технологического оборудования для изготовления ДПК – весьма высоким.
И только в 1990-е годы работы по созданию ДПК возобновились, причем сразу в нескольких странах: Финляндии, Швеции, Германии, Италии, Голландии, Японии, США и Китае.
Самый большой рынок ДПК был и остается в США. Владельцы частных домов (особенно в штатах с жарким климатом), расположенных на океанском побережье или близ речных артерий, устраивают из этого прочного и влагостойкого материала террасные настилы и веранды. Декинг (террасные настилы) из натуральной древесины недолговечен, поэтому в конце XX века американцы решили использовать для его изготовления пластик: на рынке появились террасные настилы из ПВХ и других видов пластмасс.
Пластиковые изделия долговечны, водостойки, гигиеничны, не требуют ухода, однако их стоимость высока, а экологичность сомнительна.
Технология, предусматривающая добавление к пластической массе древесной муки, опилок и стружки, пришлась весьма кстати. Уникальные свойства ДПК и оптимальное соотношение цены и качества обеспечили этому материалу большую популярность как в США, так и в других странах, позднее. Потребители сразу же оценили долговечность, внешний вид изделий из ДПК, простоту ухода, невысокую стоимость древесного композита.
С тех пор ассортимент строительных и отделочных материалов из ДПК постоянно расширяется, помимо декинга, на рынке представлены сайдинг (фасадные панели), ограждения, кровельные материалы и многое другое.
Объем мирового рынка ДПК постоянно растет. В 2012 году он составил около $4,2 млрд. Суммарный объем производства превысил 1,2 млн т в год. Более 60% мирового выпуска и потребления ДПК приходится на США, 20% – на Канаду, 10% – на страны Европы, 5% на страны Азии, 2% – на Россию. Около 50% предприятий в мире, изготавливающих изделия из ДПК, специализируются на выпуске декинга, 25% – на производстве оконных и дверных профилей.
Основные физические и механические характеристики ДПК представлены в таблице 3.
В России производство и потребление ДПК, по сути, находятся еще в начальной стадии. Однако, по мнению специалистов, у нашей страны есть потенциал для развития этого направления, так как отечественные цены на древесные отходы, полиэтилен или ПВХ, необходимые для изготовления полимерного композита, довольно низки. ДПК находит все больше сфер применения: сайдинг, изготовленный из него, – весьма неплохая альтернатива цементной, металлической или виниловой фасадной отделке зданий; его используют для производства мебели и ее элементов; сооружения садовых беседок, устройства цветников и клумб на приусадебных участках и в парках, при оборудовании детских и спортивных площадок, установке заборов и ограждений. Из ДПК делают тару и поддоны, балюстрады, дверные и оконные профили, перила лестниц, кровлю, штакетник, его используют при строительстве пирсов, в качестве опалубки для строительных работ, при устройстве противошумных барьеров. В автомобильной промышленности из композитных материалов изготавливают прокладки крыш и дверей, короба, внутренние панели, спинки сидений, полы грузовиков, подъемные полки. Характеристики композита зависят от доли древесной составляющей в материале, породы древесины и типа полимера.
Благодаря пластификаторам, модификаторам и прочим добавкам композиция ДПК приобретает необходимые химические и физические свойства. Правильно подобранные аддитивы повышают влагостойкость изделий, износостойкость, прочность, защищают от старения (воздействия низкой температуры и УФ-излучения), обеспечивают эффективность технического процесса при экструзии.
Достоинства древесно-полимерного композита:
- долговечность и надежность. Изделие из ДПК может прослужить более 20 лет, этот материал, в отличие от древесины, не подвержен короблению и растрескиванию в ходе эксплуатации;
- удобство применения. ДПК – материал довольно легкий, что существенно упрощает процесс монтажа изделий из него;
- в отличие от древесины, древесно-полимерный композит не требует дополнительной обработки специальными составами;
- экологичность. Несмотря на присутствие полимеров, композит можно назвать экологичным материалом;
- влагостойкость. ДПК, в отличие от древесины, хорошо переносит воздействие влаги и не подвержен гниению и образованию плесени – изделия из него можно использовать в помещениях с постоянной высокой влажностью;
- изделия из ДПК не изменяют характеристик при резких перепадах температуры;
- огнеупорность. В отличие от древесины, ДПК не поддерживает горения, что делает изделия из него безопасными для использования в помещениях с высокой температурой и вблизи открытого огня.
Основной недостаток материала – высокая стоимость. Сегодня древесно-полимерный композит гораздо дороже древесины и других стройматериалов. Покупка древесины обойдется дешевле, чем древесно-полимерного композита (цена 1 м3 древесины составляет 1000–1500 руб., 1 м3 ДПК – 2000–2900 руб.).
Олеся Юркова
СПбГЛТУ