Производство клееного щита. Часть 3
Рубрика Деревообработка
Производство клееного щита
Часть 3
Что такое «забирка на шмыгу». Производство клееного щита. Часть 1
Производство клееного щита. Часть 2. Качество - сумма многих слагаемых
Производство клееного щита. Часть 4. Строгание (плоское фрезерование)
Производство клееного щита. Часть 5
Технология изготовления клееного щита, состав используемого оборудования и степень автоматизации производственного процесса во многом зависят от требуемой производительности.
Первоначальный раскрой досок
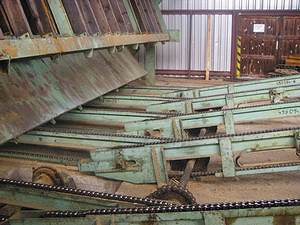
Рис. 1. Внешний вид разборщика сушильного пакета – зона приема ряда досок
Процесс производства клееного щита начинается с разборки сушильных пакетов.
Из-за слабой механизации эта операция чаще всего выполняется вручную, и стаскивать доски с верха высокого сушильного пакета обычно приходится крючьями, от чего в досках остаются глубокие вмятины, которые невозможно удалить при строгании и приходится выторцовывать, что приводит к дополнительным и неоправданным потерям материала (до 2%).
Поэтому при большом объеме переработки пиломатериалов в начале технологического процесса устанавливается агрегат для разборки штабелей с наклонным подъемником (рис. 1). Высушенный штабель из досок с прокладками по приводному рольгангу закатывается в разборщик, вилы которого поднимаются и отрывают штабель от рольганга. Затем рама разборщика вместе с этими вилами наклоняется и штабель сдвигается по вилам до контакта с этой рамой. Далее включается подъем вил и верхний ряд досок сдвигается на приемные шины и по ним вниз - до приемного рольганга, по которому по одной транспортируются к торцовочному станку для чернового раскроя. Когда очередной ряд досок на шинах заканчивается, снова включается подъем штабеля, сдвигающий на них следующий ряд. Сушильные прокладки проходят между шинами и падают вниз, где захватываются транспортером и передаются в специальную емкость для накопления и повторного использования.
В последние десятилетия для разборки сушильных штабелей на деревообрабатывающих предприятиях стали применять роботизированные системы с вакуумным захватом ряда досок.
Подобное оборудование поставляют, например, немецкие компании Mohringer, Braun-Canali, Vorvig GmbH, EWD, итальянские Bongioanni, Pezzolato, Primultini, а также ряд шведских и финских, производящих лесосушильное и лесопильное оборудование, и предприятия Тайваня.
На торцовочном станке выравнивают косо отпиленные торцы, удаляют явные крупные дефекты, выполняют раскрой длинных досок на меньшие, распиливают кривые доски на короткие отрезки с меньшей кривизной и т. п. Поскольку на этой операции требования к точности раскроя не предъявляются, здесь могут использоваться станки любого типа: балансирные (маятниковые), станки с прямолинейным движением пилы или с нижним расположением шпинделя.
Если принятой на предприятии технологией предусматривается использование необрезных досок, то после их чернового раскроя по длине выполняется раскрой по ширине на обрезные доски или сразу же раскрой по ширине на бруски.
Для этого применяются традиционные однопильные или двухпильные обрезные станки, или многопильные станки. При использовании однопильных станков после обрезки одной стороны доски надо обрезать ее с другой, поэтому приходится возвращать доску на станок - переворачивать и так далее, что диктует необходимость большой производственной площади. Поэтому однопильные (прирезные) станки на этой операции широкого распространения не получили и используются только при работе с короткими досками.
На двухпильных станках можно обрезать сразу две стороны необрезных досок, но если они не подвергались предварительной сортировке по ширине, то при постоянном расстоянии между пилами образуется слишком много отходов. Поэтому на современных производствах эксплуатируются двухпильные обрезные станки, в которых одна из пил (левая по подаче) может быстро перемещаться вдоль шпинделя. Оператор, оценив ширину обрезаемой доски, задает на программирующем устройстве станка расстояние между пилами. Левая пила перемещается настроечным механизмом вдоль шпинделя и фиксируется в рабочем положении. После обрезки доски определенной ширины пила может быть сразу же перенастроена в другое положение - для обработки более узкой или более широкой доски.
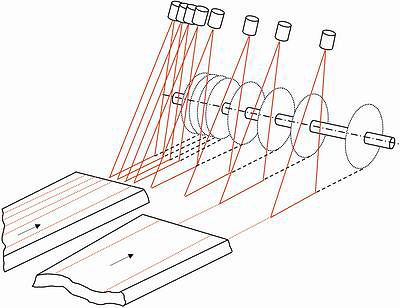
Рис. 2. Станок многопильный с лазерным указанием расстояния между пилами
Для односторонней и двухсторонней обрезки досок и их продольного раскроя на бруски сегодня также используется многопильный станок с большой рабочей шириной (от 1300 мм). Шпиндель такого станка (рис. 2) оснащается набором пил, установленных на разном расстоянии друг от друга. Перед станком устанавливается широкий загрузочный стол, на который перед обработкой укладываются доски. Над ним находится лазерное устройство, проецирующее на столе линию реза каждой из установленных на шпинделе станка пил. Оператор оценивает форму и ширину доски, сравнивает их с положением лазерных отметок и направляет доску между теми пилами, положение которых обеспечивает наиболее экономный раскрой. При обработке коротких досок (приблизительно до трех метров) такие станки могут оснащаться транспортером, возвращающим остаток доски к оператору после сортировки и оценки раскроенных частей на приемном столе за станком. Это позволяет за несколько проходов выполнять - в соответствии с заказом - наиболее точный продольный раскрой по ширине на узкие доски или бруски неравной ширины, используя наилучшим образом материал и не изменяя постав пил.
Станки для поперечного раскроя досок производят немецкие компании Anthon, GreCon Dimter, Fill, итальянские Bongioanni, Bottene, Cemil Italia, Cursal, Magh, MZ Project, Cosmec, Omga, Stromab и другие, а также некоторые тайваньские фирмы.

б
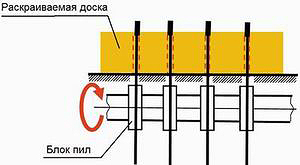
а
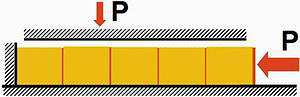
г
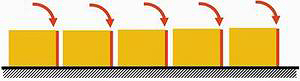
в
Рис. 3. Склеивание щита из одной доски или бруса, строганых по двум пластям:
а – продольный раскрой на бруски;
б – нанесение клея на бруски;
в – поворот брусков вокруг осей на 90°;
г – склеивание
Рядом технологических процессов перед раскроем обрезной доски на бруски предусматривается ее строгание (плоское фрезерование) по обеим пластям. При этом вскрываются дефекты и облегчается их обнаружение. Иногда, чаще всего при производстве клееного щита из заведомо высококачественного сырья - досок большой толщины (около 60 мм) и фиксированной длины (2,5-3 м), это строгание может быть финишным (рис. 3). Брус фрезеруется по обеим пластям и распиливается на бруски шириной (толщиной), равной толщине готового щита с припуском на последующее калибрование. В дальнейшем, после поворота на 90° вдоль своей оси, бруски склеиваются по этим простроганным пластям без дополнительной обработки, а пиленые кромки брусков, вышедшие на пласть щита, в дальнейшем калибруются. Такая технология из-за меньшего количества проходов при обработке и, соответственно, меньших припусков позволяет существенно сократить расход материала. Но склеивание таким способом брусков после их сращивания на зубчатый шип уже невозможно. Между операциями строгания и склеивания всегда должен быть короткий перерыв, чтобы изменение влажности простроганных брусков не привело к их короблению, что неминуемо сказывается на качестве склеивания.
Операция предварительного двухстороннего строгания проводится на двухсторонних строгальных станках, снабженных нижним и верхним фрезерными шпинделями. Рабочая ширина таких станков составляет от 300 до 1200 мм, что позволяет обрабатывать на них детали в несколько потоков. Но, как правило, у строгального участка на базе таких станков всегда есть значительный запас производительности, и обработка в несколько потоков не ведется.
На довольно мощных производствах операции строгания досок по пластям и раскроя по ширине иногда выполняются на одном станке. У таких станков рабочая ширина 300-450 мм. Они отличаются высокой производительностью: рабочая скорость подачи может превышать 60 м/мин., мощная, тяжелая конструкция таких станков определяет и их высокую цену - от 150 до 200 тыс. евро (с учетом стоимости околостаночного оборудования). Изготовители такой техники - немецкая компания Paul Maschinenfabrik GmbH & Co. KG, итальянские A. Costa S.r.l., Paoletti S.r.l., а также несколько тайваньских.
Поперечный раскрой и удаление дефектов
Бруски, полученные после раскроя досок, должны быть хотя бы предварительно отсортированы по расположению (наклону) годичных слоев на три вида: со средним наклоном к пласти - от 90 до 60°, с наклоном от 30 до 60° и менее 30°.
Отсортированные бруски направляются на операции поперечного раскроя на заготовки заданной длины и удаления дефектов.
Раскрой длинных досок желательно начинать с комлевой части: в этой зоне наименьшее количество сучков и можно выкраивать качественные детали максимальной длины, что повышает полезный выход.
Оператор мелом размечает доску или брусок, уложенные на рольганг: поперечные отметки наносятся им в местах последующего реза. Далее материал продвигается по рольгангу к торцовочному станку, где второй оператор совершает резы, удаляя из заготовки дефектные участки. Для торцовки вручную обычно используются станки с нижним расположением шпинделя.
Пила такого станка монтируется под столом; после нажатия оператором на педаль она поднимается вверх, проходя через прорезь стола, и выполняет рез. В целях безопасности зона резания сверху закрыта кожухом и оператор не видит точного расположения линии пропила - это недостаток таких станков. Кроме того, метки, наносятся мелом произвольно, что не дает возможности раскраивать материал точно по длине. Поэтому в таких станках дополнительно используются откидные (убирающиеся) упоры, которые заранее настраивают по длине необходимых заготовок. Однако эти упоры находятся далеко от оператора, вне его рабочей зоны, что затрудняет их использование. Гораздо удобнее использовать пневмоупоры с автоматическим выдвижением, которые включаются оператором с пульта управления станка. С их помощью можно выполнять более точный раскрой.
При ручном раскрое оператор вручную сортирует заготовки, раскладывая их в отдельные стопы и отделяя отходы. При высокой производительности участка раскроя и одновременном использовании нескольких торцовочных станков последние могут быть объединены в линию ленточным транспортером, на который все операторы сбрасывают отпиленные заготовки. На выходе транспортера устанавливается медленно вращающийся круг диаметром 3-4 м, откуда эти заготовки снимаются, сортируются и укладываются в стопы исходя из длины, сечения и качества. Такое решение освобождает операторов торцовочных станков от сортировки и повышает производительность всего участка.
Однако оператор не может при раскрое досок или брусков запоминать число уже отрезанных им деталей заданной длины, определяемое спецификацией, и поэтому выполняет эти спецификации последовательно, выпиливая детали всего одной-двух длин. В результате из-за несоответствия расстояния между дефектами в доске и заданными длинами выкраиваемых деталей и образуются кусковые отходы чрезмерной длины, что приносит ощутимые убытки предприятию.
Уменьшение этих убытков путем увеличения полезного выхода материала проще всего достигается использованием «умного» оборудования, способного запоминать заданные спецификации раскроя деталей по длине и количеству полученных заготовок.
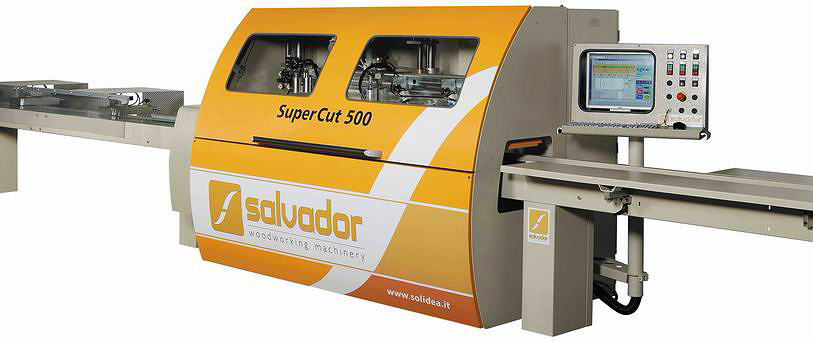
Рис. 4. Станок с системой оптимизации поперечного раскроя (Salvador)
Станки для оптимизации поперечного раскроя пиломатериалов (рис. 4) относятся к оборудованию, предназначенному для использования на предприятиях средней производительности. Процесс начинается с того, что заготовки укладываются на стол и оператор отмечает на них флуоресцентным мелом расположение дефектов (места резов пилой). Затем заготовки перемещаются подающим ленточным транспортером к пиле. Отмеченные мелом места реза распознаются фотоэлементом. Одновременно компьютер станка определяет расстояние между двумя соседними местами резов и сравнивает его с длиной заготовок, заложенных в спецификацию, которая заранее введена в память ПК. Компьютер вычисляет, сколько разных деталей наибольшей суммарной длины может быть размещено между этими соседними метками, отдавая предпочтение самым длинным деталям. После этого автоматически выполняются поперечные резы, а заложенное в спецификации количество деталей уменьшается на число полученных заготовок. Последовательность раскроя запоминается компьютером, и выходящие из станка заготовки автоматически сбрасываются с транспортера в определенные карманы-накопители (рис. 5).
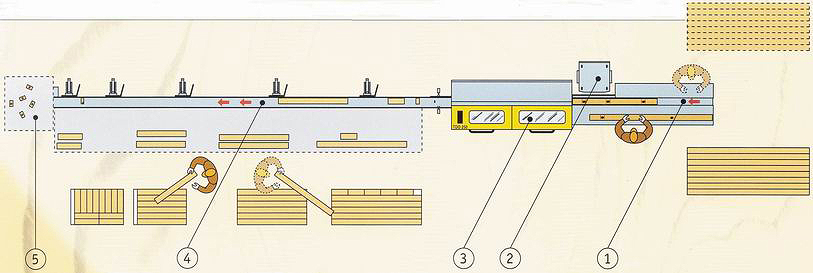
Рис. 5. Линия раскроя по длине с автоматическим станком с системой оптимизации: 1 – стол загрузочный; 2 – пульт управления;
3 – станок для поперечного раскроя; 4 – ленточный транспортер с автоматическими сбрасывателями; 5 – ящик для короткомерных отходов
По мере их наполнения рабочий вручную освобождает эти карманы, укладывая раскроенные заготовки в стопы. Обрезки остаются на транспортере и, двигаясь по нему, попадают в сборник или могут быть сразу же направлены в дробилку.
Применение такого оборудования обеспечивает снижение отходов древесины до 15%, позволяет существенно экономить рабочее время (до 50% в смену) и сократить число операторов, занятых на операции раскроя пиломатериалов, а также обеспечивает полную безопасность работы на станке, так как все рабочие органы оборудования полностью закрыты шумопоглощающим кожухом. Опыт показал, что при использовании таких станков, в отличие от обычных торцовочных станков, при раскрое досок больше чем вдвое уменьшается общая длина обрезков. Применяемое оборудование - позиционные станки или линии - выбирается исходя из требуемой производительности участка, причем однозначных решений быть не может.
Наиболее известные производители оборудования для раскроя досок и брусков на заготовки заданной длины - немецкие компания GreCon Dimter, Linck, итальянские Solidea (Salvador), OMGA, Stromab и др.
Сращивание по длине
Полученные после продольного и поперечного раскроя досок немерные (произвольной длины) и короткие заготовки поступают на сращивание по длине. В современном производстве оно обычно выполняется на клиновидные (зубчатые) шипы, иначе называемые мини-шипы, нарезаемые с шагом 2-4 мм и высотой зуба до 20 мм. Чем меньше сечение соединяемых заготовок, тем меньше размеры шипов.
Операция сращивания по длине включает: выравнивание (опиливание) торцов заготовок, фрезерование шипов на торцах, нанесение клея на поверхность шипов, соединение деталей (продольное прессование) и раскрой по длине на заготовки заданного размера.
Простейший вид оборудования для фрезерования шипов - вертикальный фрезерный станок с нижним расположением шпинделя, оснащенный шипорезной кареткой и дополнительным горизонтальным пильным шпинделем.
Каретка универсального фрезерного станка дорабатывается таким образом, что одна ее половина поднимается на уровень, равный половине шага шипов. Станок оснащается продольной линейкой на входе и пильным суппортом для выравнивания торцов деталей. На каретке устанавливаются два поперечных упора.
При работе на станке каретка выводится в переднее исходное положение и на нее укладывается ряд брусковых деталей, торцы которых базируются по линейке. При движении каретки вперед торцы деталей опиливаются (выравниваются) и на них нарезаются шипы. Затем каретка возвращается в исходное положение, а бруски разворачиваются, укладываются на вторую часть каретки и снова базируются торцами по линейке. После второго прохода за счет разницы в высоте положения брусков на каретке, шипы на торцах оказываются смещенными на половину их шага, что исключает образование ступеньки между соседними брусками при последующем сращивании.
Нанесение клея на зубчатые соединения при небольшой производительности участка может выполняться вручную, а сращивание - с использованием простейшего пневматического пресса мод. ПС 250, выпускаемого костромским ООО «Простор». В нем вертикальные пневмоцилиндры прижимают сращиваемые заготовки к столу, состоящему из двух половин, после чего обе части стола с деталями продвигаются навстречу друг другу и осуществляется соединение деталей.
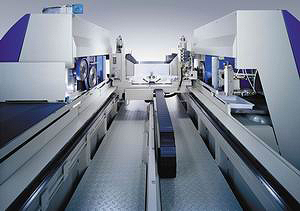
Рис. 6. Линия сращивания брусков по длине на зубчатый шип (GreCon)
Автоматизированное оборудование для сращивания брусковых деталей на зубчатый шип (рис. 6) можно подразделить на два основных типа: полуавтоматические (позиционно-проходные) - с поворотным столом, и автоматические (проходные) - с поперечной подачей заготовок для нарезания шипов.
Принцип работы линий с поворотным столом состоит в том, что брусковые заготовки, свободно уложенные оператором на поворотный стол, продвигаются рольгангом до упорной линейки фрезерного станка, выравнивающей по одной линии их торцы, которые оказываются на опорном столе этого станка. Затем бруски сверху прижимаются к этому столу и сбоку к продольной линейке. После этого упорная линейка поднимается, и суппорт, движущийся по горизонтальным направляющим, с помощью пилы выравнивает поверхность торцов заготовок, фрезерует шипы и наносит на них клей. Затем суппорт возвращается в исходное положение, а заготовки возвращаются по рольгангу на поворотный стол, который вместе с деталями разворачивается на 180°. Далее детали снова подаются своими необработанными торцами к уже опущенной упорной линейке и процесс обработки повторяется. После поворота стола базирующий (опорный) стол фрезерного станка поднимается (или опускается) на высоту, равную 1/2 шага зубчатых шипов, чтобы избежать образования ступенчатой формы детали после сращивания.
Детали с нарезанными шипами и клеем, нанесенным на шипы в станке, вручную передаются к прессу для продольного сращивания и загружаются в него поочередно, всегда одинаковыми торцами вперед. В прессе образуется непрерывный продольный ряд соединенных между собой заготовок, который по достижении определенной длины автоматически разрезается - в соответствии с заданными размерами - пильным суппортом, движущимся синхронно с соединяемыми заготовками. Готовые детали укладываются в стопу для выдержки.
Производительность таких линий определяется тем, в каком направлении нарезаются мини-шипы: если требуемое направление вершин их зубьев - вдоль пласти, то на столе станка всегда располагается меньшее количество деталей, чем при расположении деталей вертикально, на кромке, и при нарезании шипов перпендикулярно пласти брусков.
Существуют и другие конструктивные решения подобных линий, например, оснащенных двумя суппортами. При прямолинейном движении ковра заготовок по транспортеру они останавливаются упорной линейкой, их передние торцы обрабатываются, после чего выполняется реверс транспортера, заготовки возвращаются в исходное положение, упираясь в заднюю упорную линейку, и после обработки вторым суппортом задних торцов снова продвигаются вперед, к прессу, для сращивания по длине.
Существуют прессы для сращивания с разными механизмами подачи, создающими продольное усилие при сращивании: роликовые (вальцовые), гусеничные или с возвратно-поступательным движением каретки, зажимающей начало соединяемого ряда заготовок между двумя плитами и продвигающей их вперед, к выходу из пресса, где устанавливается механизм, противодействующий движению, за счет чего и создается необходимое усилие для соединения шипов. Гусеничные механизмы подачи обеспечивают наиболее равномерное продвижение ряда соединяемых заготовок и достижение наибольшей производительности.
На предприятиях с большим объемом сращиваемых пиломатериалов и заготовок, используются автоматические линии сращивания с поперечной подачей заготовок при нарезании клиновидных шипов.
Механизм подачи таких линий - конвейер из двух цепей, объединенных плоскими планками, перемещающимися по плоскому столу. В разрывах стола поперек него установлены два рольганга с косыми роликами, а справа и слева от стола - суппорты для нарезания шипов, каждый из которых включает в себя пильный, фрезерный суппорты и механизм нанесения клея на поверхность шипов.
Во время работы линии заготовки укладываются на стол станка и захватываются планками транспортера. Двигаясь по транспортеру и попадая в зону первого поперечного рольганга, заготовки перемещаются им к правой продольной упорной линейке, прижимаются к столу ремнем и обрабатываются пильным и фрезерным суппортами, после чего на шипы сразу же наносится клей. Далее детали, перемещаемые планками транспортера, попадают в зону второго косого рольганга и смещаются им к левой упорной линейке, где обрабатывается второй торец. Детали с нарезанными с двух сторон зубчатыми шипами передаются по транспортеру в проходной пресс для продольного сращивания по длине, на выходе которого установлен пильный суппорт, отрезающий от непрерывного ряда соединенных деталей заготовки нужной длины. Такие линии выпускались немецкой компанией Torwegge.
Производительность такого оборудования столь высока, что оно может обеспечивать беспрерывную работу установленного за ними в линию четырехстороннего строгального станка, работающего со скоростью подачи более 60 м/мин!
При сращивании большое значение имеет состояние и качество заточки фрезерного инструмента, формирующего мини-шипы. При его затуплении или плохой заточке форма шипов может отличаться от заданной. В результате у вершин соединенных шипов могут образовываться полости, которые относятся к недопустимым дефектам обработки. Причиной их появления может быть избыток клея в соединении, недостаточное продольное усилие пресса или проскальзывание рабочих органов механизма подачи относительно соединяемых деталей. Избыток клея в соединении или чрезмерное усилие прессования могут приводить и к появлению продольных трещин на соединяемых деталях. Весьма важно также, чтобы при сращивании в прессе сохранялось положение базы брусков, определенной при нарезании шипов, и направление подачи брусков в пресс, определяемое разным положением мини-шипов на их торцах относительно этой базы. Поэтому при ручной загрузке пресса для сращивания большое значение имеют внимательность и уровень подготовки оператора.
Производители оборудования для сращивания брусков на зубчатый шип по длине - немецкие компании GreCon Dimter, REX Maschinenfabrik, итальянские Solidea (Salvador), OMGA, Spanevello, Stromab и другие, а также несколько тайваньских, активно поставляющих свое оборудование в нашу страну.
Четырехстороннее фрезерование
Следующий этап технологии - четырехстороннее плоское фрезерование цельных и срощенных по длине брусков. У полученных после этой операции заготовок должно быть постоянное, строго прямоугольное сечение и не должно быть кривизны, а также дефектов обработки - заколов, мшистости, ворсистости и т. д. Поэтому к четырехсторонним станкам предъявляются довольно высокие требования.
Основные производители такого оборудования - немецкая компания Weinig, итальянские SCM, Casolin, Casadei, Sicar, Griggio, чешские Rojek и TOS Svitavy, Боровичский завод деревообрабатывающих станков, а также тайваньские Winner Machinery Co. Ltd и Chang Iron Works, корпорация Holytek, холдинг Leadermac и др. Подробно об этих станках мы расскажем в следующем номере журнала.
Андрей ПЕТРОВ,
компания «МедиаТехнологии»,
по заказу журнала «ЛесПромИнформ»