Производство шпона и фанеры. Часть 2
Лущение шпона
Производство шпона и фанеры. Часть 1. Подготовка сырья к лущению
Производство шпона и фанеры. Часть 3. Сушка шпона
Производство шпона и фанеры. Часть 4. Сортирование и обработка сухого шпона
Производство шпона и фанеры. Часть 5. Технологии склеивания фанеры
Производство шпона и фанеры. Часть 6. Прессование и послепрессовая обработка фанеры
В предыдущей публикации (см. ЛПИ № 3, 2014 год) мы рассмотрели технологию и оборудование для подготовки сырья к лущению. На очереди современное оборудование для лущения и обработки сырого шпона.
Головным оборудованием лущильных цехов фанерных предприятий являются линии лущения - рубки - укладки шпона. На рис. 1 представлена схема линии лущения Raute.
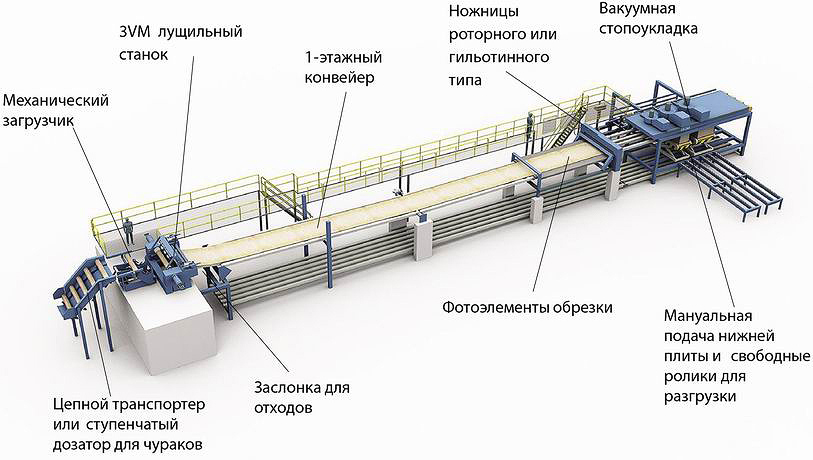
Рис. 1. Линия лущения шпона Raute для производства фанеры
Прогретые чураки, подаваемые по конвейеру, сталкиваются сбрасывателями на накопитель. Отсюда они поштучно подаются в центровочно-загрузочное устройство для ориентированной подачи в лущильный станок. Шпон-рванина, получаемый на стадии оцилиндровки чурака, падает на ленточный конвейер и удаляется на измельчение в рубительную машину (на схеме не показана). Деловой шпон направляется на конвейер, где он притормаживается и укладывается петлями. Это позволяет уменьшить длину конвейера и экономно использовать производственную площадь. На последнем участке конвейера смонтирована ускоряющая ветвь, с помощью которой лента шпона выпрямляется и подается на пневматические ножницы для получения форматных листов шпона, которые накапливаются на подъемном столе стопоукладчика. После полного формирования стопы она вилочным погрузчиком доставляется к сушилкам или на участок промежуточного хранения. Время хранения плотной стопы сырого шпона не должно превышать четыре часа.
Кусковой и неформатный шпон, неизбежно образующиеся при рубке ленты шпона, нижней ветвью конвейера возвращаются к конвейеру удаления отходов и вручную раскладываются на подстопные места. Карандаш (остаток от лущения) падает на продольный конвейер и направляется на измельчение или на переработку с получением попутной продукции.
Такова типичная организация труда в лущильном цехе фанерного предприятия. Изменения могут касаться в основном переработки кускового шпона, для чего могут быть предусмотрены ножницы. Не исключена также последующая сушка шпона в ленте; в этом случае оборудование для рубки шпона переносится на участок за ленточной сушилкой.
В основу работы современного центровочно-загрузочного устройства положен принцип электронного сканирования формы чурака. Чурак в центровочном приспособлении Raute CPL при его проворачивании измеряется лазерными сканерами (от 3 до 7 шт.) со скоростью 16 тыс. точек в секунду (до 112 тыс. замеров на один чурак). После компьютерной обработки для окончательного расчета берутся 100-250 результатов замеров, на основании которых определяется ось цилиндра, вписанного в чурак. Компьютер посылает команду на гидравлические сервоцилиндры, которые корректируют положение торцов чурака в двух координатах (X, Y). Чурак захватывается в его оптимальном положении передаточными рычагами и подается на лущильный станок, где останавливается в позиции ожидания окончания лущения предыдущего чурака.
Такая система позволяет не только повышать полезный выход шпона из чурака, автоматически переходить от оцилиндровки к лущению чурака, но и до минимума сократить время, затрачиваемое на вспомогательные операции, за счет быстрой смены чурака и отвода суппорта на расстояние, соответствующее диаметру следующего чурака. Фирма выпускает ЦЗУ широкой гаммы типоразмеров для чураков диаметром до 1850 мм и длиной до 3300 мм.
Дальнейшим шагом в усовершенствовании системы центрирования чураков стала система Smart Scan, в которой используется лазерная завеса. Она позволяет делать с шагом 25 мм до 72 замеров в каждом сечении чурака и построить его трехмерное изображение. Помимо того, система позволяет выполнять центрирование по годовым кольцам путем их сканирования с торцов чурака. Все эти новшества обеспечивают увеличение полезного выхода шпона на 5-10% за счет увеличения примерно на 1 см диаметра чурака после оцилиндровки.
Лущильные станки в зависимости от размеров перерабатываемого сырья подразделяются на легкие (длина чурака - до 900 мм), средние (длина чурака - до 1900 мм) и тяжелые (длина чурака - больше 2000 мм).
На российских фанерных заводах есть лущильные станки ярославского завода «Пролетарская свобода» марок ЛУ-17 с длиной ножа 1700 мм и ЛУ-9 с длиной ножа 900 мм для получения спичечной соломки из коротких осиновых чураков, а также станки фирмы Raute с длиной ножа 2000 и 2650 мм.
Вращение чурака в этих станках обеспечивается за счет вращения кулачков, вонзающихся в торцы чурака. Внутри больших кулачков диаметром 110 мм находятся малые кулачки (диаметром 65 мм), выдвигаемые при уменьшении текущего диаметра чурака. Такие телескопические шпиндели позволяют уменьшить диаметр карандаша до 70-75 мм.
К основным параметрам режима лущения шпона относятся влажность и температура чурака, угловые показатели лущильного ножа и прижимной линейки, степень обжима шпона. Влажность древесины в период ее тепловой обработки почти не изменяется и в значительной мере зависит от породы древесины и способа доставки сырья. Наименьшей влажностью характеризуется ядровая зона сосны (минимальная 40% при железнодорожной поставке), наибольшей - береза с ложным ядром (до 160%). Оптимальная температура чураков на момент лущения зависит от породы древесины и заданной толщины шпона. Считается, что температура на поверхности карандаша должна быть не ниже 20°С.
Чтобы избежать нежелательной разнотолщинности шпона (допускается ±0,05 мм для шпона толщиной до 1,15 мм и ±0,10 мм - для более толстого шпона), следует тщательно соблюдать все угловые параметры, характеризующие установку ножа и прижимной линейки. Главными параметрами являются задний угол α и угол заточки β, которые в сумме образуют угол резания (δ = α + β).
Выбор начального значения угла α зависит от диаметра чурака: чем он больше, тем больше задний угол. В противном случае может возникнуть контактная площадка между ножом и чураком, что вызовет перегрев ножа. По мере лущения этот угол нужно уменьшать, чтобы усилие на чурак не было очень большим и не возникли вибрации в системе «чурак - нож - станок». Это особенно важно для чураков большого диаметра.
Чем выше плотность древесины, тем больше угол заточки β и толщина шпона. Угол заточки может меняться в пределах 18-22°. Большие углы заточки (24-25°) при обработке еловой древесины связаны с высокой твердостью ее сучков.
Чем меньше задний угол и угол резания, тем выше качество шпона, так как с увеличением этих параметров увеличивается давление ножа на шпон. В результате повышается шероховатость шпона и уменьшается его прочность из-за углубления трещин, неизбежно образующихся на внутренней стороне ленты шпона (внутренней называют сторону, обращенную к сердцевине чурака).
Слишком малый задний угол опасен тем, что при этом увеличивается площадь поверхности соприкосновения задней грани ножа с чураком. Давление на чурак возрастает, он прогибается, что вызывает неравномерность толщины ленты шпона. В современных лущильных станках предусмотрен механизм автоматического изменения заднего угла по мере уменьшения текущего диаметра чурака. В начальный период лущения он составляет 1-3°, в конце лущения 0-0,5°.
На изменение заднего угла влияет положение лезвия ножа по отношению к оси вращения чурака. У разных моделей станков величина h (см. рис. 2) может колебаться в пределах ± 1,0 мм. Если лезвие ножа установлено выше оси вращения шпинделей, то задний угол в процессе лущения будет уменьшаться, если лезвие будет ниже этой оси - увеличиваться.
Важнейший параметр лущения - величина обжима шпона. Обжим достигается за счет того, что устанавливаемый между ножом и прижимной линейкой зазор меньше толщины шпона (S0 < S). Это позволяет упрочнить древесину в зоне резания и резко уменьшить глубину трещин на внутренней стороне шпона. Оптимальная величина обжима зависит от толщины шпона и составляет 16-20%.
Угол заточки прижимных линеек - 48-63°, радиус закругленной нажимной кромки - 0,2-0,3 мм. При лущении шпона толщиной более 2 мм следует применять прижимную линейку с нажимной микрогранью шириной 3-8 мм и принимать h0 = 0.
Порядок операций на лущильном станке:
● чурак направляется в загрузочное устройство и устанавливается между шпинделями;
● чурак зажимается большими кулачками шпиндельных бабок, включается вращательное движение шпинделей;
● на ускоренной подаче подводится суппорт, захваты центрирующего устройства отводятся;
● ускоренная передача переключается на обдирочную подачу, при этом прижимная линейка отведена;
● после оцилиндровки включается рабочая подача, одновременно опускается прижимная линейка;
● при диаметре чурака 120-130 мм автоматически включается приспособление, предотвращающее изгиб чурака, а большие кулачки заменяются малыми;
● при подходе к кулачкам суппорт автоматически останавливается и на ускоренной подаче отводится назад, прекращается вращение шпинделей, они разводятся, и карандаш падает вниз.
В модернизированных лущильных станках фирмы Raute применен ряд новшеств, которые позволяют сократить время цикла лущения и повысить качество шпона. Это следующие новшества:
● цифровая регулировка зазора между ножом и прижимной линейкой;
● цифровое изменение заднего угла лущильного ножа;
● гидравлическое крепление ножа, облегчающее его замену;
● уменьшение диаметра малого кулачка с 65 до 60 мм, что позволяет уменьшить диаметр карандаша и увеличить выход шпона;
● цифровая подача ножевого суппорта вместо механической коробки передач, что облегчает плавную регулировку толщины шпона;
● автоматический возврат суппорта в исходное положение.
Наряду с традиционными лущильными станками, предназначенными для получения шпона для фанеры, в последние годы появились лущильные станки для изготовления другой продукции, в частности тарной дощечки (рис. 3).
Лущильный станок СЛ-800 от НПО «Группа компаний МАГР» одновременно с лущением выполняет раскрой ленты шпона подвижными ножами на полосы необходимой длины. Станки оснащены гидравлическим подъемником-центроискателем для подачи чураков и их центрирования в телескопических кулачках. Необходимая толщина шпона в диапазоне от 0,5 до 5 мм задается на пульте станка и поддерживается в течение всего цикла лущения при помощи электронной системы с точностью до 0,1 мм. За лущильным станком устанавливаются ножницы для рубки шпона на дощечки заданной ширины.
Заслуживает внимание бесшпиндельный лущильный станок, впервые представленный фирмой Raute еще в 1990-е годы.
Вращение чураков осуществляется за счет приводных рифленых роликов, расположенных под углом 120° друг к другу. Верхний валец служит прижимной линейкой, а нижние перемещаются прямолинейно по мере уменьшения текущего диаметра чурака. Каждый валец оснащен индивидуальным гидроприводом. В процессе лущения ножевой суппорт немного поворачивается относительно чурака, что обеспечивает оптимальные параметры лущения от исходного диаметра до диаметра карандаша 50 мм. Положение валов, толщина шпона и угол резания регулируются компьютером. Диаметр чурака измеряется до его подачи в станок для определения просвета между валами.
Идея бесшпиндельного лущения в Европе не получила развития, но эта технология широко распространилась в азиатских и южноамериканских странах. В качестве примеров производителей бесшпиндельных станков можно привести бразильскую компанию Omeco и тайваньскую «Чан Тай».
В Юго-Восточной Азии и Южной Америке на многих предприятиях применяют бесшпиндельное лущение тонкомерного сырья и долущивание карандашей. Обычно лущильная линия состоит из окорочно-оцилиндровочного станка, бесшпиндельного лущильного станка, роторных ножниц и стопоукладчика.
В окорочно-оцилиндровочном станке чурак получает вращение от трех приводных зубчатых роликов. Нож, аналогичный лущильному, удаляет кору и неровности, придает чураку цилиндрическую форму. Начальный диаметр чурака - до 500 мм, после оцилиндровки - не более 360 мм.
Передающий конвейер выравнивает чураки и подает их на бесшпиндельный лущильный станок, оснащенный тремя приводными роликами с мелкой насечкой и лущильным ножом. Максимальный диаметр чурака - 360 мм. Диаметр карандаша 30-40 мм в зависимости от модели станка. Толщина шпона - от 1,0 до 3,0 мм. Линейная скорость лущения - 40 м/мин. После лущения лента шпона поступает на роторные ножницы, которые в автоматическом режиме рубят ее на форматные листы.
Технология лущения тонкомерных чураков может быть интересна и российским производителям шпона. Минимальный диаметр чурака на загрузке определяется тем фактом, что диаметр карандаша может не превышать 30 мм. Китайские лущильные станки работают и в России, например на фанерном заводе «Инвестфорест» в пос. Суслонгер (Республика Марий Эл), на Уфимском фанерно-плитном комбинате, на заводе «Сатис-Мебель» под Нижним Новгородом.
Фирма Weihai Hanvy Plywood Machinery Manufacturing Co. выпускает станки серии SL для чураков длиной 1350, 2000 и 2600 мм. Толщина шпона - от 0,8 до 3 мм, диаметр карандаша - 40 мм, скорость движения шпона - 42 м/мин.
По мнению ряда специалистов, имеющих опыт эксплуатации оборудования для лущения, наиболее удачными следует считать тайваньские линии, которые комплектуются японскими подшипниками, сервоприводами, а также контроллерами и другой электроникой.
Рубка шпона выполняется на ножницах разной конструкции с целью получения форматных листов шпона и заготовок кускового шпона. До недавнего времени были широко распространены пневматические ножницы с возвратно-поступательным движением ножа в вертикальной плоскости. Схема работы этого оборудования была такова: передняя кромка ленты шпона касалась конечного выключателя, который включал электромагнит, приводящий в действие золотниковую коробку, которая открывала доступ воздуху в пневмоцилиндр, шток которого через систему рычагов приводил в движение ножевую траверсу. Продолжительность одного двойного хода составляла всего 0,15 с.
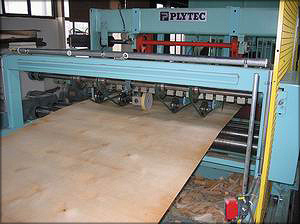
Рис. 4. Ножницы эллипсного хода
Компанией Plytec (Финляндия) были выпущены также ножницы эллипсного хода (рис. 4), в которых - в отличие от классических гильотинных - нож совершает не просто прямое возвратно-поступательное движение, но и двигается по ходу движения шпона, таким образом совершая при рубке эллипсоидное движение.
Сегодня почти повсеместно эксплуатируются роторные ножницы, например, марки НР 18-3. В них нож совершает вращательное движение, что позволяет уменьшить массу станка, упростить конструкцию и повысить точность рубки листов. Нож в этом станке установлен между двумя обрезиненными валами (толщина оболочки - 20 мм) и расположен горизонтально. По команде датчика длины, настроенного на заданный размер листа шпона, нож занимает вертикальное положение и синхронно с движением ленты шпона очень точно отделяет от нее лист нужной ширины.
Аналогичной конструкции ножницы представляют фирмы Raute и Plytec. В этом станке приводом вращающегося ножа управляет микропроцессор, связанный со сканирующим устройством. Система сканирования управляет также сбрасывателем кускового шпона и отходов после их отделения от ленты шпона.
Ножницы с автоматической вырезкой дефектных участков выпускают фирма Colombo Cremona (Италия) и Plytec. В качестве устройства, определяющего дефекты, применяется датчик - планка с инфракрасными фотосчетчиками. Ножницы работают по программам, в которые включены следующие операции: обрезка кускового шпона и вырезка дефектов, деление шпона на листы по заданному размеру, автоматическая рубка на форматные листы. Продолжительность реза составляет 0,05 с при скорости движения ленты шпона от 3,5 до 30 м/мин. Изменена по сравнению с прежней конструкцией и механика работы ножниц: движение ножа осуществляется через коленчатый валик от пневмоцилиндра, которым управляют быстродействующие магнитные вентили. Вместо обрезиненного ролика под ножом находится ролик из синтетического материала.
После рубки форматные листы укладываются в плотные стопы с помощью специального механизма - стопоукладчика. Сегодня на наших заводах распространены механические стопоукладчики. Лист шпона подается на гидравлический стол, который постепенно опускается и в крайнем нижнем положении вручную выкатывается для передачи стопы сырого шпона на промежуточное хранение.
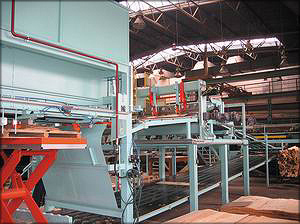
Рис. 5. Вакуумный стопоукладчик
На рис. 5 представлен вакуумный стопоукладчик. Здесь листы шпона за счет отсоса воздуха из верхней части станка поджимаются к подающим ремням, которые передают их на приемный стол. Может быть одно или два подстопных места, в зависимости от используемого сырья и производительности лущильного станка.
В результате совершенствования линии лущения - рубки шпона заводом «Пролетарская свобода» с учетом опыта эксплуатации лучших образцов аналогичного оборудования отечественных и зарубежных производителей разработан комплекс лущильный КЛ 13-17. В комплект поставки входят транспортер-накопитель чураков, центровочно-загрузочное устройство (с центровкой чурака при помощи ультразвуковых датчиков), лущильный станок, а также линия рубки и укладки шпона мод. ЛРУШ 13-17. Работа всех механизмов синхронизирована и автоматизирована. Лущильный станок оснащен трехкулачковыми шпинделями, что позволило добиться при лущении чураков уменьшения диаметра карандаша до 55 мм. Производительность комплекса (по сырью) - 10-11 м3/ч.
Владимир ВОЛЫНСКИЙ