Производство шпона и фанеры. Часть 4
Сортирование и обработка сухого шпона
Каждый лист лущеного шпона можно характеризовать по породе древесины, толщине, длине и ширине листа, назначению и качеству. Задача разделения шпона по назначению и по сортам (качеству) решается на участке сортирования сухого шпона. Это очень важная операция, имеющая большое значение для дальнейшей судьбы материала, который используется для производства фанеры.
Производство шпона и фанеры. Часть 1. Подготовка сырья к лущению
Производство шпона и фанеры. Часть 2. Лущение шпона
Производство шпона и фанеры. Часть 3. Сушка шпона
Производство шпона и фанеры. Часть 5. Технологии склеивания фанеры
Производство шпона и фанеры. Часть 6. Прессование и послепрессовая обработка фанеры
Порода древесины, из которой лущат шпон, определяется уже на первой технологической операции фанерного производства, т. е. при приемке и сортировании сырья. На фанерных заводах могут выпускать комбинированную фанеру с внутренними слоями из довольно толстого соснового шпона и наружными слоями из тонкого березового шпона. Технологические параметры подготовки сырья к лущению для сосны и березы различны, поэтому разделение поступающего сырья по породам обязательно.
Толщина шпона задается на лущильном станке при настройке и в дальнейшем в одну стопу складывается шпон только одной породы и одной толщины.
Длина шпона, т. е. размер вдоль волокон, определяется длиной ножа лущильного станка. По заданной технологом ширине лист шпона обрезается пневматическими ножницами на линии лущения-рубки. После обрезки форматных листов (обычно в форме квадрата со стороной 1,6 или 1,9 м) на участке образуется неформатный и кусковой шпон, ширина которого меньше заданного формата продукции.
После сушки листы шпона могут быть использованы по разному назначению. Форматные листы шпона предназначены для получения фанеры, при этом часть их может подвергаться починке с целью повышения качества. Неформатный и кусковой шпон могут быть квалифицированы как отдельная товарная продукция или отправлены на линии ребросклеивания с целью увеличения их ширины до требуемого формата.
Каждому листу шпона должен быть присвоен сорт, который определяется наличием на нем пороков древесины или дефектов обработки. Всего ГОСТ 3916.1-96 устанавливает пять сортов лущеного шпона: Е, I, II, III, IV. Предприятия, выпускающие экспортную продукцию, разделяют шпон на четыре сорта: В, ВВ, СР, С.
На участке сортирования сухого шпона решается задача разделения шпона по назначению и по сортам (качеству). Качественный выход шпона зависит главным образом от сорта сырья. Для каждого сорта четко оговариваются допустимость того или иного вида пороков древесины или дефектов обработки: указываются предельные размеры сучков и их количество на 1 м2 площади листа, процент площади листа, занятой ненормально окрашенными участками и т.д.
На предприятиях, не прошедших модернизацию, сохраняется ручная сортировка шпона. Выполнять ее сразу на выходе шпона из сушилки довольно трудно, так как рабочие должны в этом случае приспосабливаться к ритму работы сушильного оборудования. Поэтому часто у сушилок накапливаются стопы несортированного сухого шпона, которые затем вилочным погрузчиком перемещаются на участок сортирования, где работники могут трудиться в привычном ритме.
При отсутствии механизации одна сортировщица обрабатывает 500-600 листов в час, перенося 1-1,5 т груза и проходя за это время расстояние до 3 км. Запаса сухого рассортированного шпона должно хватать на бесперебойную работу цеха склеивания в течение полутора-двух суток, поэтому требуется трехсменная работа большого числа рабочих низкой квалификации.
Естественно, что такая организация труда не способствует высокой производительности труда и снижению себестоимости продукции. По-этому на современных заводах сегодня используются автоматические линии сортирования сухого шпона, работа которых синхронизирована с работой сушильного оборудования.
В автоматических сортировках финской фирмы Raute сухой шпон сразу из сушилки попадает на поперечный конвейер. Оператор визуально оценивает сорт каждого листа и нажимает на пульте кнопку с номером кармана, в котором накапливается шпон того или иного сорта. Листы шпона с помощью вакуумных присосок поджимаются к верхней перфорированной ленте конвейера и транспортируются к своему карману. Установленные на этих линиях сканирующие устройства фиксируют пороки древесины, автоматически определяют сорт каждого листа и передают команду устройству, направляющему этот лист в нужный карман.
Значительная часть шпона проходит дополнительную обработку, а именно - починку форматных листов, ребросклеивание кускового шпона и стягивание трещин клеевой лентой.
Починка шпона выполняется с целью повышения сортности на один разряд за счет вырубки из листа сучков и постановки заплаток с натягом 0,1-0,2 мм. Починке подлежит шпон сортов II, III, IV. Вставки вырубаются из шпоновых полос с влажностью 3-5% и той же толщины, что и требующий починки лист. У вставок обычно форма эллипса, а размеры колеблются от 25 х 15 до 100 х 60 мм (всего четыре типоразмера). Из общего объема высушенных листов шпона починке подвергаются от 10 до 30%. Для этой цели используются шпонопочиночные станки марки ПШ или ПШ-2А. Станок работает так: лист вручную укладывается на рабочий стол станка, рабочий укладывает лист так, чтобы дефектное место находилось прямо под штампом станка, и нажимает педаль. После этого автоматически выполняется цикл нужных операций: верхняя просечка высекает в шпоне дефектное место, вырубленный участок шпона толкателем проталкивается вниз и удаляется сжатым воздухом при помощи подведенного воздуховода, из специальной ленты шпона нижней просечкой вырубается вставка (заплатка) и ставится на место дефекта. Заплатка удерживается за счет натяга, т. к. ее размеры немного превышают размеры образовавшегося отверстия.
В среднем производительность шпонопочиночных станков составляет 100-150 листов в час (0,4 м3/ч). Починки требуют примерно 30% сухого шпона 1-го сорта, 36% 2-го сорта и 57% 3-го сорта. Заплатки вырубаются из специальных полос шпона, для получения которых существуют специальные делительные станки, например, СД-800 от фирмы «МАГР» (г. Брянск).
В станке-полуавтомате Patchmaster PM100 (Raute) используются заплатки сложной формы, которые надежно фиксируются в листе шпона. Усовершенствованная конструкция этого станка позволяет добиться производительности до 60 листов в минуту. Представитель техники нового поколения - система RoboPatching - полностью автоматизированная система починки шпона, которая по производительности почти в два раза превосходит станок-полуавтомат. RoboPatching выполняет следующие операции: система поиска обнаруживает дефект шпона, определяет его координаты относительно заданной точки и передает эти координаты промышленному роботу, который подводит дефектное место шпона под штамп починочного станка, работающего в обычном режиме. Производительность - до 1000 заплаток в час.
Обработка кускового шпона включает в себя операции сортировки кусков по качеству, ширине и толщине, подготовки кромок и ребросклеивания, в результате чего из кускового шпона получают форматный.
Для подготовки кромок, то есть для создания идеально прямой кромки на листах кускового шпона, служат два типа станков - гидравлические ножницы и кромкофуговальные станки. В фанерном производстве наиболее распространены гидравлические ножницы.
Пачка кускового шпона обрабатывается на гидравлических ножницах марок НГ-30, НГ-18, СК-1, СК-2 и др. с целью формирования строго прямолинейных кромок для последующего ребросклеивания без фугования.
Цикл работы на ножницах таков. Из листов шпона примерно одной ширины формируется пачка, которая укладывается на рабочий стол станка так, чтобы одна из сторон пачки упиралась в направляющую линейку. После пуска станка пачку прижимает специальная прижимная балка, и нож, совершающий качательное движение в вертикальной плоскости («сабельный удар»), отрезает часть пачки. Станок может быть оснащен лазерным указателем линии резания, что облегчает позиционирование пачки шпона и уменьшает потери древесины. После подъема ножа прижимная балка поднимается, рабочий переворачивает пачку другой стороной, и цикл продолжается, то есть выполняется резка второй продольной кромки пачки шпона. Потери шпона на прирубке кусков составляют примерно 5-7%.
Фирма Kuper (Германия) выпускает ножницы для одновременного формирования кромок пачки шпона двумя ножами: один из них движется сверху вниз, а другой - снизу вверх. Станки оснащены лазерными разметчиками, на этом оборудовании можно обрабатывать пачки высотой до 80 мм. Линия прирубки шпона со сканером этой же фирмы позволяет выполнять автоматическую вырубку дефектов по критериям, задаваемым оператором.
Ребросклеивание шпона может выполняться по разным схемам.
Продольное ленточное ребросклеивание заключается в наклеивании гуммированной ленты (бумажной ленты с нанесенным на нее и подсушенным резиновым клеем) на стык двух подготовленных кусков шпона. Продольное безленточное склеивание заключается в предварительном смачивании кромок клеем и последующем склеивании этих кромок. Склеивание с помощью клеевой нити выполняется так: клеевая нить проходит через зону горячего воздуха, оплавляется и зигзагообразно укладывается на стык кусков шпона, где почти моментально отверждается и склеивает их таким образом.
Точечное ребросклеивание выполняется с использованием клеев-расплавов, которые наносятся в горячем состоянии на стык кусков в виде отдельных точек и очень быстро отверждаются.
Кроме продольного, существует поперечное ребросклеивание, которое предусматривает наиболее производительный - проходной способ склейки кусков шпона, уложенных на движущийся транспортер и фиксируемых между собой с помощью жидких клеев, клеев-расплавов или клеевой нити.
Наибольшее распространение на наших заводах получил станок с клеевой нитью РС-9. Парные полосы шпона вручную подаются в станок, где одно-временно с их продольным перемещением выполняется их стяжка, а нитеводителем, в котором нить проходит через сопла, смонтированные в гильзе, совершающей колебательное движение, на шов накладывается расплавленная термопластичная нить, которая нагревается воздухом, подаваемым через нагреватель.
Станки с продольной подачей малопроизводительны (0,3-0,4 м3/ч), поэтому используются в основном на мебельных фабриках для стяжки строганого шпона. На фанерных предприятиях все большее применение находят станки с поперечной подачей. У этого оборудования производительность выше.
Следующим шагом в совершенствовании техники для ребросклеивания явилось совмещение в одной линии ножниц и ребросклеивающего станка. Прирубка по одному листу позволяет использовать вместо тяжелых гидравлических легкие пневматические ножницы.
На линии ребросклеивания ОАО «Фантех» листы шпона разной ширины соединяются в бесконечную ленту шпона, которую можно прирубать на листы нужного формата. Стопы шпона, выгруженные на цепной конвейер, перегружаются на подъемный стол, который поднимает стопу на нужную высоту. Рабочий подает листы на конвейер, где винтовыми роликами выполняется боковое смещение, которое выравнивает шпон относительно поперечной кромки. Ножницы прирубают переднюю и заднюю кромку шпона перпендикулярно к направлению подачи с помощью оптического измерителя-фотоэлемента. Фотоэлемент также фиксирует дефекты в шпоне и, в соответствии с информацией, полученной от датчика, и встроенныйм ПК подается команда ножницам на вырубку дефекта. С помощью пневмосопла и управляющих эксцентриков отходы шпона сдуваются на нижний конвейер. Целые бесшовные листы переводятся на двухэтажный конвейер, служащий промежуточным складом и подающий куски шпона на ребросклейку.
На ребросклеивающем станке листы шпона склеиваются в бесконечную ленту с помощью расплавленной нити. На обе поверхности шпона наклеиваются расплавленные четыре пары нитей, причем крайние нити после каждого шва перекручиваются. Бесконечную ленту шпона ножницы раскраивают на листы заданного формата, которые укладываются на поддон в стопы на требуемую высоту стопоукладчиком. Когда стопоукладчик оказывается в нижнем положении, готовая стопа перемещается на рольганг выгрузки, а на стопоукладчик ставится новый поддон. Минимальная ширина кусков для ребросклеивания - 150 мм, производительность линии - 5-6 м3 в смену.
Наряду с немецкими и финскими станками в последние годы заметное место в поставках оборудования на российский рынок заняло японское и тайваньское оборудование. 10 лет назад в России появилась первая японская линия ребросклейки от компании «Хашимото Денки». На линии выполняется последовательно контроль толщины шпона, прирубка кромок, вырубка дефектов, соединение кусков каплями термопластичного клея и упрочнение нитями с одной стороны. Предусмотрена закрытая система клеенанесения. Расплав клея подается по горячим трубам к клеевым клапанам, расположенным на поверхности горизонтального аппликатора. Капли горячего клея попадают на кромку прирубленного куска шпона, который в ходе движения прижимается к предыдущему листу. Одновременно на верхнюю поверхность шпона прикатываются в направлении поперек волокон горячие термопластичные нити, которые быстро остывают и упрочняют готовый форматный лист шпона.
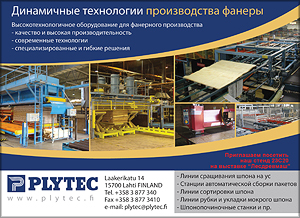
Plytec. Оборудование для производства фанеры
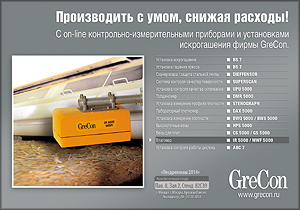
GreCon. Системы искрогашения и измерительные
системы
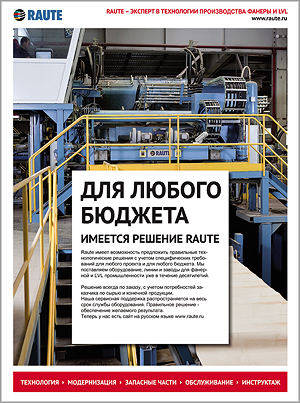
Raute. Оборудование для производства фанеры и LVL
В ребросклейке японской кампании «Минами» используется механическая система клеенанесения. Здесь предусмотрена ванна с горячим клеем, в который погружены специальные «пальцы». При подходе кромки шпона они поворачиваются на 180° и наносят клей на эту кромку. Скрепляющие нити наносятся на нижнюю поверхность листов, что предохраняет систему от попадания мусора под нити. У оборудования «Минами» производительность меньше, чем у ребросклейки компании «Хашимото» (скорость подачи 30 м/мин. против 45 м/мин.), но зато оно проще в обслуживании и, главное, обеспечивает высокое качество точечного ребросклеивания.
Технология «Минами» освоена тайваньскими машиностроителями. Сегодня в России работают по этой технологии около 30 тайваньских линий ребросклеивания шпона.
Помимо склеивания по ширине с целью получения форматного шпона из кусков на фанерном предприятии часто возникает необходимость сращивания листов шпона по длине с целью получения длинных листов из коротких. Это особенно актуально при производстве строительной фанеры с размерами 1220 х 2440 мм из чураков длиной 1,3 м. Уменьшение длины чурака снижает его кривизну и повышает выход шпона. Последующее сращивание коротких кусков шпона по длине открывает возможность для производства большеформатных плит при одновременном повышении полезного выхода шпона из сырья.
Для получения необходимой прочности склеивания используют усовое соединение с длиной уса 25-40 мм. Для этой цели ОАО «Фантех» выпускает линию сращивания шпона.
Стопа шпона подается с роликового конвейера, который служит накопителем, на подъемный стол. Оператор поднимает стол на удобную для себя высоту и затем подает шпон на загрузочный конвейер, где листы выравниваются по одной кромке. На усовочном станке листы шпона усуются таким образом, что на правой стороне листа скос получается сверху, а на левой - снизу. Длина уса регулируется в зависимости от толщины шпона. После усовки клеенаносящее приспособление наносит точно дозированный объем клея на поверхность шпона только с левой стороны. Затем листы укладываются в стопу высотой примерно 200-300 мм и выдерживаются перед запрессовкой (открытая выдержка), для того чтобы из клея испарилась излишняя влага. После набора стопы шпон по роликовому конвейеру передается к пресс-балкам. На каждой пресс-балке операторы подают подготовленный шпон к кареткам загрузочного устройства, которые автоматически перемещают шпон к пресс-балкам и устанавливают намазанную кромку одного листа и сухую другого точно одну над другой. В процессе смыкания плит положение листов не меняется, что обеспечивает хорошее соединение. Пресс-балка смыкается, при этом каретка возвращается в исходное положение для приемки следующего листа. Время прессования, в зависимости от свойств шпона и клея, заранее установлено на пульте управления, и по его истечении пресс-балка автоматически размыкается. При этом каретка подает очередной лист шпона. После прессования получается бесконечная полоса шпона, которую можно рубить на полотна необходимой длины. Нож выполняет рубку автоматически - в соответствии с заданной длиной сращенного шпона. Автоматический стопоукладчик укладывает форматные листы шпона на подъемный стол. После достижения нужной высоты стопы стол опускается и стопа шпона перемещается на выгрузочный конвейер. Стол возвращается в исходное положение.
Известные японские линии сращивания отличаются от выпускаемой ОАО «Фантех» тем, что усование шпона на них выполняется позиционным способом, т. е. при движении пильного узла относительно неподвижного листа шпона. На усованную поверхность шпона наносится горячий клей-расплав, а прессование выполняется в холодном прессе всего за несколько секунд.
Еще одним способом сращивания шпона является наклеивание бумажной ленты на стык листов шпона. Для того чтобы стык был плотным, сначала делают небольшую нахлестку и прирубку сразу двух листов. Затем отходы удаляют сжатым воздухом, торцы листов прижимают друг к другу и наклеивают на стык бумажную полоску со смоченным клеем, который моментально фиксирует соединение.
Владимир ВОЛЫНСКИЙ
Автор выражает благодарность
Александру Исаеву (ЗАО «Кронекс»)
за помощь в подготовке статьи