Производство шпона и фанеры. Часть 5
Технологии склеивания фанеры
Производство шпона и фанеры. Часть 1. Подготовка сырья к лущению
Производство шпона и фанеры. Часть 2. Лущение шпона
Производство шпона и фанеры. Часть 3. Сушка шпона
Производство шпона и фанеры. Часть 4. Сортирование и обработка сухого шпона
Производство шпона и фанеры. Часть 6. Прессование и послепрессовая обработка фанеры
Рассмотрим основные этапы технологического процесса склеивания фанеры. Первый этап один из наиболее ответственных: приготовление и нанесение клея на шпон, - от точности соблюдения параметров технологического режима во многом зависит качество фанеры.
Приготовление и нанесение клея на шпон
Для производства фанеры используются многокомпонентные клеи. Наряду с синтетической смолой в них могут присутствовать такие добавки, как отвердитель, наполнитель, пластификатор и пр. Рецептуры клеев на разных заводах разные и часто являются ноу-хау предприятия.
Фанера марки ФК на многих заводах изготавливается с использованием карбамидоформальдегидной смолы КФМТ, к которой добавляются хлористый аммоний (в качестве отвердителя), мука пшеничная (в качестве наполнителя) и другие компоненты. Фанера марки ФСФ склеивается на фенолоформальдегидной смоле типа СФЖ 3014, которая не требует добавки отвердителя.
Клеи приготовляют в механических клеемешалках с бачками разной формы и емкости. У бачков должны быть двойные стенки (как в термосе), между которыми циркулирует вода («водяная рубашка») для регулирования температуры клеевой смеси. Основным рабочим органом клеемешалок является вал с лопастями, вращаемый электромотором через редуктор. Конструкция лопастей может быть разной: в виде плоских пластин, приваренных к валу с одинаковым или разным наклоном плоскостей относительно оси вала; в виде пропеллерных пластин, направленных в противоположные стороны или винтообразно приваренных к валу. Движение лопастей может быть планетарным или встречным, создающим вихревое движение клеевой смеси. Лопасти изготовляют из высокопрочной легированной стали.
Обычно скорость вращения лопастей - 60 об./мин., но в зависимости от вида клея она может меняться (от 25 до 75 об./мин.). Нередко скорость вращения лопастей ограничивают для предотвращения вспенивания клея. Если же нужно получить вспененный клей, например карбамидный, скорость вращения повышают. Длительность перемешивания составляет 15-30 мин. Последним из компонентов в клеевую смесь вводят отвердитель.
Смеситель может быть отдельным оборудованием, у которого вал с мешалкой опускается, например, в бочку со смолой, куда уже загружены необходимые компоненты. Размеры стойки мешалки, длина вала, диаметр перемешивающего органа выбираются с учетом геометрических размеров емкости заказчика.
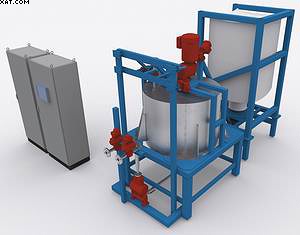
Рис. 1. Установка для приготовления клеевой смеси
Smart Mix 1200 (производитель – компания Raute,
Финляндия)
Компания Raute предлагает установку для взвешивания, дозирования и смешивания компонентов клея Smart Mix 1200 (рис. 1) с емкостью главного танка 1200 л. Здесь все работы выполняются автоматически с помощью плунжерных дозаторов и смесителя соленоидного типа. Все настройки и параметры процесса задают с пульта управления.
Для экономии клея прибегают к его вспениванию. Для этого добавляют в смолу поверхностно активные вещества (альбумин, ОП-10, сапонал и др.) в количестве 0,2-1%. Вспенивающий аппарат представляет собой многолопастную мешалку с частотой вращения рабочего органа 250-300 мин-1. За 5-10 мин. объем смолы увеличивается в 3-5 раз по сравнению с исходным. После этого в нее добавляют отвердитель и снова перемешивают 5-10 мин. Устойчивость пены поддерживается не менее восьми часов. Наибольшее распространение получил вспениватель конструкции Усть-Ижорского фанерного завода (УИФЗ) вместимостью 600 л.
Экструдер представляет собой трубу с отверстиями, через которые вытекает клей, полосками ложащийся на проходящую под ним заготовку. Оптимальный расход клея - 10-12 г/м (55-60 г/м2), потери клея - не более 5%, скорость подачи под экструдером - до 70 м/мин.
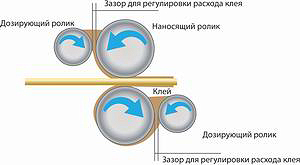
Рис. 2. Принципиальная схема и общий вид
клеенаносящего станка КВ-18М (производитель –
компания «МИИОР плюс», г. Рыбинск, РФ)
Доля стоимости клея в себестоимости фанеры примерно 20%, поэтому экономному расходованию клея уделяется большое внимание. Наиболее распространенным способом нанесения клея является контактный, реализуемый обычно с помощью клеенаносящих вальцов (рис. 2).
У рабочей поверхности клеенаносящих валов резиновое покрытие, которое может быть как гладким, так и с винтовыми канавками, обеспечивающими заданный удельный расход клея. Форма и шаг канавки выбираются в зависимости от применяемого клея и удельного расхода, необходимого по технологическому процессу. Резиновое покрытие валов подбирается по твердости, химической стойкости, термостойкости исходя из условий работы. Резиновое покрытие хорошо отдает клей (по сравнению с применяемым на некоторых станках полиуретановым или капроновым покрытием) и позволяет наносить клей на заготовки с разнотолщинностью до 0,2 мм (металлическая или полиуретановая поверхности из-за жесткости оставляют участки, не промазанные клеем).
У рабочей поверхности дозирующих валов может быть эбонитовое или хромовое покрытие, которое защищает ее от коррозии.
Все валы станка проходят балансировку, что снижает вибрации, износ рабочих поверхностей валов, нагрузку на опоры.
В приводе валов используются обгонные муфты, при помощи которых выравниваются окружные скорости поверхностей валов, что устраняет трение между валами, так как происходит обкатывание валов без скольжения. Устранение проскальзывания между валами позволяет уменьшить износ поверхностного слоя валов и избежать нагрева клеевой смеси.
Валы изготавливаются с жесткими допусками по длине, что позволяет полностью устранить подтекание клея по торцам валов через торцевые уплотнения. В механизмах торцевых уплотнений используются съемные бронзовые вкладыши с минимальным коэффициентом трения. По окончании рабочей смены при промывке станка вкладыши торцевых уплотнений легко вынимаются для очистки и устанавливаются обратно.
Для настройки валов на параллельность и параллельного разведения и сведения валов применяются червячные редукторы, соединенные попарно через шлицевые муфты. Эти редукторы не позволяют настройкам самопроизвольно сбиться. Строгая параллельность валов особенно необходима при работе с пониженным удельным расходом клея.
Через этот станок можно пропускать заготовки толщиной от 1 до 60 мм, но по желанию заказчика может быть изготовлен станок и для работы с заготовками большей толщины.
Привод станка укомплектовывается инвертором (частотным преобразователем), позволяющим менять обороты электродвигателя без потери мощности. Поэтому скорость прохождения заготовок может плавно меняться от 1-2 до 60 м/мин. При помощи инвертора осуществляется и плавный запуск станка, что позволяет избежать пусковых ударов и продлить срок службы станка. Инвертор дает возможность подключать станки с мощностью привода до 1,5 кВт к сети однофазного тока (220 В).

Важным моментом эксплуатации клеенаносящего станка является обеспечение безопасности работы оборудования. Защитные ограждения предназначены для исключения риска попадания рук операторов в опасные зоны станка во время работы. При открытии защитных ограждений станок останавливается, и включить его можно только после установки защитных ограждений в рабочее положение.
Промывка станка выполняется при выключенном приводе, а для вращения валов используется специальная съемная рукоятка.
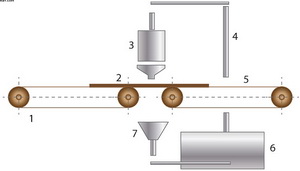
Рис. 3. Схема нанесения клея методом налива:
1 – подающий конвейер, 2 – лист шпона,
3 – клееналивная головка, 4 – трубопроводы,
5 – приемный конвейер, 6 – бак с клеем,
7 – приемная воронка
Способ налива (рис. 3) отличается от других тем, что заготовка (шпон) проходит через клеевую завесу. При этом способе применяется простое оборудование с малым числом трущихся деталей, не требуется настройка на толщину и легко регулируется расход клея, скорость подачи материала может доходить до 200 м/мин., а потери клея составляют не более 10%. Однако ввиду интенсивной циркуляции жидкий клей быстро теряет растворитель, и требуется постоянно добавлять свежий клей в бак, а вязкость клеевой смеси не должна превышать 100 с (по вискозиметру ВЗ-4). Кроме того, клей наносится только на одну сторону листа шпона, поэтому при использовании способа налива (так же как при методе экструзии) требуется менять всю схему сборки пакетов. Оптимальный расход клея - 90 г/м2, ширина донной щели - 0,75 мм, расстояние между щелью и шпоном - 60-100 мм. Скорость подачи не должна превышать четырехкратную скорость падения струи. Оптимальный расход клея в фанерном производстве (по данным специалистов фирмы Raute) приведен в таблице.
Сборка пакетов фанеры
Перед клеенаносящим станком устанавливается стопа шпона для среднего слоя. После станка - стопы шпона лицевого и оборотного слоев. Сборка выполняется вручную на столе с упорными линейками, образующими базирующий угол.
Основная идея механизации и автоматизации участка сборки пакетов с использованием классических клеенаносящих вальцов - обеспечение автоматической, без участия наборщика, подачи листов шпона из необходимого количества стоп непосредственно к месту наборки (рис. 4).
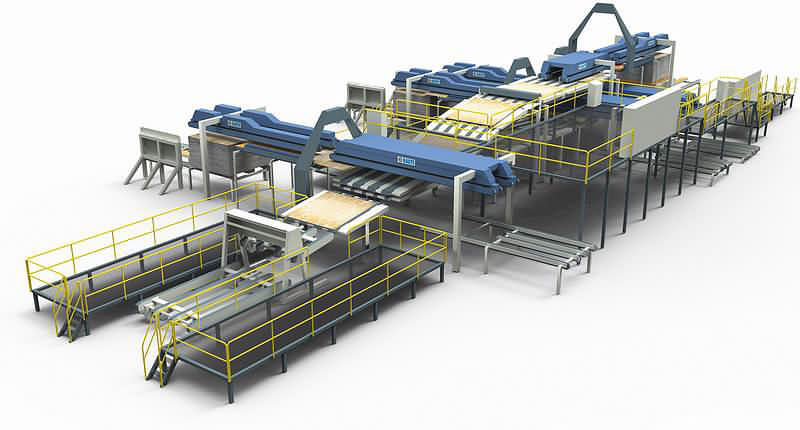
Рис. 4. Участок сборки пакетов фанеры (производитель – фирма Raute)
При этой концепции линию автоматической наборки можно условно разделить на два основных участка: подачи шпона в вальцы и подачи рубашек и сухих серединок. Необходимое количество подстопных мест определяется сортностью выпускаемой фанеры и применяющейся технологией. Таким образом, сборка пакетов осуществляется только одним оператором, который автоматически попеременно получает необходимые листы шпона и укладывает их в пакет.
При сборке особое внимание обращают на симметричность листа фанеры и соблюдение параметров заданной конструкции. Нижний и верхний листы должны быть обращены лучшей стороной наружу. При использовании шпона из хвойной древесины для изготовления фанеры листы заболонного шпона должны быть в пакете снаружи, а листы ядрового - внутри. Если используются листы шпона разных пород, то хвойный шпон помещается внутрь пакета.
Холодная подпрессовка пакетов
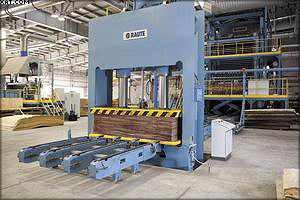
Рис. 5. Холодный пресс для подпрессовки пакетов шпона
(производитель – фирма Raute)
Холодная подпрессовка пакетов собранного шпона выполняется непосредственно перед горячим прессованием для получения цельных пакетов, удобных для транспортировки и загрузки в горячий пресс. Холодное прессование позволяет исключить взаимное смещение листов, сократить число повреждений наружных слоев, увеличить скорость транспортирования и загрузки в пресс, отказаться от использования прокладок, увеличить производительность пресса за счет повышения его этажности, сделать работу пресса независимой от участка сборки пакетов.
На рис. 5 представлен одноэтажный пресс с верхним рабочим давлением для подпрессовки пакетов шпона.
Цикл запрессовки обычно определяется периодом сборки одного пакета, в течение которого в прессуемом пакете происходит увлажнение шпона и повышение вязкости клея в клеевых прослойках, что обеспечивает условия для прилипания слоев друг к другу, но без отверждения клея. При разборке подпрессованного пакета целостность листов не нарушается. Время хранения подпрессованого пакета зависит от вида клея и температуры помещения. Для фенольных клеев (без отвердителя) оно может составлять около суток.
Обычно один холодный пресс может обслуживать не менее двух горячих прессов.
Технологические параметры горячего склеивания фанеры
При склеивании фанеры сухим горячим способом в многоэтажных прессах применяют три основные технологические схемы:
- склеивание нескольких листов в рабочем промежутке пресса при постоянном рабочем давлении. Этим способом склеивают фанеру толщиной от 6 до 8 мм. Максимальная толщина пакета (суммарная толщина листов шпона) в одном промежутке пресса не должна превышать 18 мм. В противном случае не гарантируется необходимый равномерный прогрев как по площади листов, так и по толщине пакета из-за низкой теплопроводности древесины;
- склеивание по одному листу в промежутке пресса при постоянном давлении в период термообработки. Таким образом склеивают фанеру толщиной более 8 мм, а в некоторых прессах и более тонкую фанеру;
- склеивание по одному листу с охлаждением плит пресса. Применяется при склеивании фанерных плит и другой продукции большой толщины (более 20 мм). У технологии склеивания по одному листу есть свои достоинства: обеспечиваются симметричный нагрев каждого листа, одинаковая влажность и упрессовка наружных листов, низкая упрессовка в целом всего листа фанеры.
К параметрам режима склеивания фанеры относятся:
- влажность пакета шпона, обычно она колеблется в пределах 12±3%;
- число листов в промежутке пресса. Оно определяется максимальной толщиной пакета (18 мм) и зависит от толщины фанеры. Обычно фанеру толщиной до 7 мм клеят по 2-4 листа в этаже пресса, более толстую - по одному листу;
- температура плит пресса. Зависит от марки используемого клея и числа слоев в фанере. Чем толще пакет, тем ниже должна быть температура склеивания. Для фенольных клеев требуется температура на 10-20 °С выше, чем для карбамидных.
В производстве древесно-слоистых пластиков повышенная температура требуется для дополнительной пластификации древесины и уплотнения материала. В результате получается материал значительно более прочный, чем рядовая фанера; - рабочее давление. Оно зависит от марки продукции и конструкции элементов пресса, передающих давление.
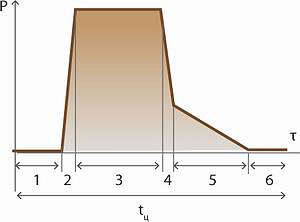
Рис. 6. Составляющие цикла склеивания и диаграмма
изменения давления при склеивании фанеры:
1 – время загрузки пакетов,
2 – время смыкания плит,
3 – время прессования,
4 – время снятия давления в первом периоде,
5 – время снятия давления во втором периоде,
6 – время размыкания плит и выгрузки пакетов
Цикл склеивания фанеры складывается из следующих периодов: загрузки пакетов в пресс, подъема и смыкания плит пресса, создания рабочего давления, выдержки под давлением, снижения давления, выгрузки фанеры.
Составляющие цикла склеивания и типичная диаграмма изменения давления представлены на рис. 6.
К вспомогательному времени относится время, необходимое для загрузки и выгрузки пакетов, для смыкания и размыкания плит пресса. Время выдержки под давлением (tпр) зависит от марки клея, породы древесины, слойности и толщины пакета и температуры плит пресса. Время снятия давления складывается из двух периодов. В первом периоде происходит снижение давления с максимального уровня до безопасного, равного уровню давления пара в плитах пресса. Обычно этот период составляет 0,25 мин. Второй период занимает 1-3 мин., так как быстрое снятие давления может вызвать интенсивное парообразование, которое приведет к разрушению листов фанеры. При склеивании по одному листу время снятия давления сокращается примерно вдвое по сравнению с приведенным выше.
Производительность горячего многоэтажного пресса, м3/ч, определяется по формуле
где Кр - коэффициент рабочего времени, Кр = 0,94; nэт - число этажей пресса (из характеристики пресса); nл - число листов фанеры в промежутке пресса; Sф - толщина фанеры, м; tц - время цикла прессования, мин.; l, b - длина и ширина обрезного листа фанеры, соответственно, м.
Согласно принятой методике, в расчет принимаются размеры обрезного листа фанеры, то есть размеры готовой продукции, хотя из пресса выгружают, конечно, необрезную фанеру. Это связано с тем, что горячий пресс является головным оборудованием, по которому рассчитывается вся годовая программа предприятия, выражаемая в кубических метрах обрезной фанеры.
Упрессовка фанеры
Упрессовка определяется как относительное уменьшение толщины пакета ΣSш до толщины фанеры Sф,%:
Упрессовка зависит от многих факторов: давления склеивания, времени склеивания, температуры плит пресса, начальной влажности пакета шпона, толщины пакета шпона.
Возрастание влажности шпона, как и увеличение времени прессования, ведет к повышению упрессовки. При большой толщине пакета упрессовка неравномерная - наружные слои упрессовываются сильнее, так как они находятся ближе к горячим плитам.
Причиной упрессовки являются пластические деформации древесины под действием высокой температуры и давления. Силы упругости целлюлозного каркаса древесины недостаточно для полного восстановления его первоначального размера. Упрессовке способствует и проникновение клея в полости клеток, и его отверждение в них.
Шпон хвойных пород уплотняется на 30-50% сильнее, чем березовый, из-за содержания в смоле летучих веществ, влияющих на коэффициент внутреннего трения в древесине.
Сокращение потерь при упрессовке может быть достигнуто за счет склеивания фанеры по одному листу в промежутке пресса, использования эластичных средств для передачи давления. При использовании очень жестких нагревательных плит необходимо обеспечить избыточное давление для ликвидации неплоскостности этих прессующих плит (нормативное значение - 0,1 мм на 1 м длины) и повышения качества клееной продукции.
Разработано несколько систем управления упрессовкой. Они основаны на том, что при снижении давления с 1,8-2,5 до 0,4-0,5 МПа развитие упрессовки во времени прекращается. Момент снижения давления устанавливается по общей деформации всех пакетов в горячем прессе, например, с помощью задатчика упрессовки, дающего команду гидросистеме пресса (система АСУП-1).
Почти не дает упрессовки холодный способ склеивания фанеры. При температуре плит пресса 18-20°С толщина пакета может быть любой. Время выдержки в прессе зависит от типа используемого клея. В настоящее время наилучших результатов можно добиться при использовании ПВА-клеев (период холодного отверждения - 15-30 мин.). Однако их применение сдерживается высокой ценой, низкой водостойкостью клеевых соединений. Особенно эффективно использование холодного способа склеивания при изготовлении фанеры из соснового шпона.
Владимир ВОЛЫНСКИЙ