«СВЕЗА Верхняя Синячиха»: уральскую фанеру знают во всем мире
Фанерный комбинат «СВЕЗА Верхняя Синячиха» входит в группу «СВЕЗА». Доля группы на мировом рынке березовой фанеры почти 25%. Совокупный объем производства этого вида плитной продукции, выпускаемой на шести комбинатах группы, составляет 1,3 млн м3 в год, компания предлагает потребителям более 200 видов продукции разных сортов и формата.
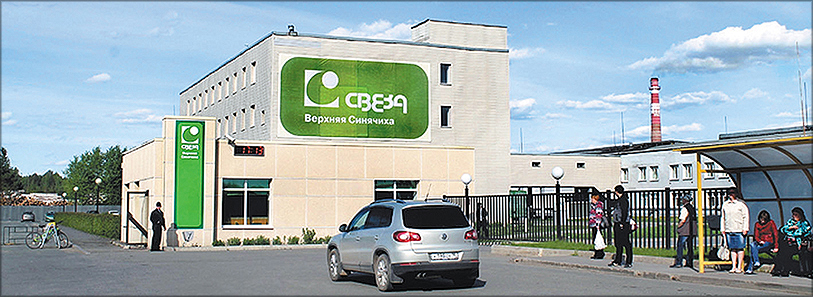
Фанерный комбинат в рабочем пос. Верхняя Синячиха Алапаевского района Свердловской области создан в 70-е годы прошлого века. В 1990 годы предприятие было преобразовано в ЗАО «Фанком». Переориентировавшись в основном на выпуск экспортной фанеры, «Фанком» обновлял технику, закупал современное импортное оборудование, в 2006 году была пущена вторая линия по производству большеформатной фанеры, а в 2007 - создан цех по производству широкоформатной хвойной фанеры. В 2012 году «Фанком» вошел в состав группы «СВЕЗА» и началась новейшая история комбината.
Сегодня «СВЕЗА Верхняя Синячиха» выпускает только стопроцентную березовую фанеру марок ФК и ФСФ, ламинированную фанеру, фанеру для производства паркетной доски SVEZA Parquet и специальную ламинированную фанеру SVEZA Deck 350 с разметочной сеткой для опалубки перекрытий, которая упрощает разметку и раскрой фанеры (к слову, технология изготовления этого вида продукции защищена патентом). На комбинате производят фанеру трех основных форматов: 5х5, 8х4, 8х5 м. Вся продукция предприятия сертифицирована по ГОСТу, а также обеспечена международными сертификатами СЕ, Е1, BFU 100, CARB. За два квартала 2017 года объем производства комбината составил 139,8 тыс. м3 (к 2020 году планируется увеличить этот показатель до 234,2 тыс. м3), 80% фанеры реализуется на экспортных рынках, 20% - на внутреннем.
Лесообеспечение и лесозаготовка
При производстве фанеры на комбинате используется только стопроцентный березовый шпон, продукция изготавливается исключительно из российской березы, которой по физико-механическим и качественно-эстетическим характеристикам нет аналогов в мире.
«Обеспечение производства сырьем - это, наверное, один из самых важных вопросов не только для нашего комбината, - говорит руководитель комбината "СВЕЗА Верхняя Синячиха" Илья Радченко. - Казалось бы, на Урале и вообще в России леса много, но сколько проблем надо решить, чтобы заготовить и доставить этот лес на деревообрабатывающее предприятие! И вызваны эти проблемы в первую очередь неудовлетворительным лесоустройством. Имеет место колоссальное несоответствие зафиксированных в давно устаревших документах данных по лесфонду и фактических данных о характеристиках растущего на делянках леса. А ведь экономика конкретного производства и лесозаготовки строится на основе именно официальных документов! В европейской части официальные данные о лесоустройстве более или менее соответствуют фактическим. В нашей же области по документам на делянке одно, а по факту - совершенно другое. А в целом по Сибири коэффициент несоответствия 1:5. Получается так: леса растет много, но мы даже не знаем, какой он, чтобы принять решение, брать ли его в работу. Эту проблему надо решать на уровне государства. Еще одна большая проблема в нашем регионе - это необходимость комплексной переработки древесного сырья. Чтобы отрасль развивалась, нужно потреблять не только «корешки», но и «вершки», то есть максимально использовать всю массу заготавливаемого леса: стволы, сучья, ветки, кору. К сожалению, на Урале нет ни плитных производств, ни ЦБК, есть незначительное в масштабе отрасли число пилорам, а мы же - как переработчики - потребляем только 20% всей массы заготавливаемой древесины: фанкряж. Появление в нашем регионе производств с глубокой переработкой древесины могло бы существенно поспособствовать развитию всей отрасли.
Если же говорить о жизнедеятельности комбината "СВЕЗА Верхняя Синячиха", то надо отметить: из-за того что завод является потребителем лишь малой части заготавливаемой древесины, заниматься лесозаготовкой становится нерентабельно. Работа строится следующим образом: комбинат берет в аренду лесные участки, но заготовку осуществляют субарендаторы - частные лесозаготовители. Наши партнеры заготавливают для нас фанкряж, а остальное - низкосортную древесину, баланс, пиловочник и прочее - они перерабатывают и реализуют сами. Мы стараемся развивать наших поставщиков сырья. Ведь лесозаготовка - это не всегда крупный бизнес, оборотных и инвестиционных средств порой не хватает некрупным компаниям для развития. Мы кредитуем наших партнеров, покупаем для них лесозаготовительную технику: харвестеры, форвардеры, сортиментовозы».
Как ответственный лесопользователь комбинат уделяет большое внимание восстановлению зеленых массивов. На предприятии работает подразделение, которое занимается лесообеспечением. В его функции в том числе входит контроль работы подрядчиков с выездом на делянки и выполнения сроков и объемов лесовосстановительных работ. «СВЕЗА» поддерживает деловых партнеров и оказывает им помощь, если в этом есть потребность.
Производство
Технологические процессы на комбинате «СВЕЗА Верхняя Синячиха» ведутся на производственных площадках в двух зданиях. В первом корпусе, где изготавливается фанера форматов 5х5, 8х4, 8х5, расположены два цеха. В состав цеха по производству сухого шпона входят три участка: подачи сырья, лущения шпона и его сушки. В состав второго цеха, где изготавливается фанера, входят участки сортировки шпона, склейки и обработки фанеры. Во втором корпусе на трех участках: лущения и сушки шпона, комплектовки шпона и клейки фанеры, а также ламинирования фанеры - производят только фанеру формата 8х4.
Производство березовой фанеры на комбинате организовано следующим образом. Поступившее на предприятие сырье проходит гидротермическую обработку - в течение суток пропаривается в специальных бассейнах при 40-60°C для повышения пластичности древесины. После этого следует окорка сырья - она позволяет повысить срок службы лущильных ножей и прижимных линеек на этапе лущения шпона. Лесоматериалы поступают на комбинат в виде кряжей, которые после гидротермической обработки и окорки разделываются на чураки. Сырой шпон заданной толщины получают методом лущения чураков на линии Hashimoto Denki на базе станка Uroko (Япония). Размеры сырого шпона устанавливаются с учетом припуска на усушку и зависят от толщины шпона. Листы сырого шпона на автопогрузчике транспортируются на участок сушки, где установлены сушильные камеры Uroko. Сушка осуществляется в соответствии с режимами, установленными в зависимости от толщины шпона и давления пара или температуры воздуха в сушилке. Высушенный шпон проходит обязательный контроль влажности на установке Hashimoto Denki. В случае обнаружения на шпоне каких-либо визуальных дефектов, например сучков, лист направляется на починку - технологический процесс облагораживания поверхности шпона, имеющий целью повышение его сортности: на специальном оборудовании оператор вырезает сучки из листа и вставляет заплатку, так называемую бабочку, закрывающую дефект. Следующий этап производственной цепочки - сортировка, после которой выполняется предварительный набор рубашечных и внутренних слоев в соответствии с сортом фанеры и схемой сборки пачки. После этого отсортированный шпон отправляется на участок склейки фанеры. На клеенаносящем станке японского производителя Kitagawa путем пропуска листов шпона между вращающимися клеевыми барабанами на шпон наносится клеевой слой. Далее листы укладываются в определенной последовательности в пакет и отправляются в гидравлические прессы Kitagawa (Япония). Склеивание фанеры выполняется горячим способом в определенных температурных режимах. После выхода из прессов стопы фанеры автопогрузчиком перемещаются на линию форматной обрезки и раскроя Kitagawa (Япония). Листы фанеры одновременно шлифуются с обеих сторон до достижения требуемой толщины и качества поверхности. Для изготовления фанеры нестандартных размеров и для внутренних нужд производства листы раскраиваются на вспомогательном оборудовании - форматно-раскроечном станке Altendorf (производитель - Wilhelm Altendorf GmbH Co.KG, Германия).
На комбинате уделяют большое внимание качеству готовой продукции, толщину каждого листа фанеры проверяют на специальной установке, а качество склеивания - с помощью ультразвуковой установки (обе установки производства немецкой компании GreСon). В зависимости от технического задания фанеру ламинируют пленкой ПВХ на станке Kitagawa. Для ламинирования используются пленки финского и немецкого производства. Сейчас ведется тестирование пленок отечественного производителя Novel Group. К слову, некоторые технологии изготовления ламинированной фанеры запатентованы. Например, при производстве фанеры марки SVEZA Titan используется пленка, которая содержит корундовые частицы, это препятствует скольжению листа и широко применяется при производстве напольных покрытий для коммерческого транспорта. Клеевые составы на комбинате изготавливают из смол, основным поставщиком которых является российская «дочка» австрийской компании Metadynea. Готовая фанера сортируется и отправляется на упаковку. Пакеты фанеры обвязываются упаковочной лентой, маркируются. Под каждое место сгиба ленты на кромках пакета подкладываются защитные уголки. Упакованная таким образом фанера автопогрузчиком доставляется на склад готовой продукции, откуда в дальнейшем отгружается клиентам.
Помимо перечисленного выше, на разных участках производственных корпусов комбината эксплуатируется такое оборудование, как линия лущения и линия сушки шпона (производитель - фирма Raute, Финляндия), линия ребросклеивания шпона Ventek (США), ребросклеивающий станок фирмы Diehl (США), линия обрезки и шлифовки Holzma (производитель - Homag Group, Германия), линия горячего прессования фанеры формата 2440 х 1220 Felmann (Швеция) и другие.
Отходы производства (щепа) используются в качестве топлива для местной котельной, что позволяет не только отапливать производственные помещения, вырабатывать пар для технологических нужд, но и отапливать поселок. В настоящее время заканчивается монтаж утилизационной термомасляной котельной установки Polytechnik (Австрия), приобретенной комбинатом для реализации первого этапа модернизации энергетического хозяйства. Установка будет работать на древесных отходах, образующихся в процессе технологического цикла производства фанеры, в том числе на щепе, получаемой при дроблении обрезков фанеры, а также на шлифовальной пыли, коре и опилках. В этом проекте австрийская компания выступает не только как производитель оборудования, но и как генеральный подрядчик. На втором этапе модернизации котельного хозяйства предусматривается строительство еще одной термомасляной котельной. Начать реализацию этого проекта планируется до конца текущего года.
Логистика
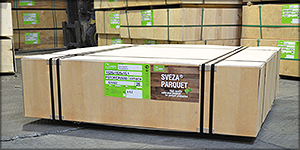
Фанера комбината «СВЕЗА Верхняя Синячиха» пользуется спросом у компаний из США, Египта, Италии, Голландии, Турции, Великобритании, Саудовской Аравии, Германии и Чехии. Из уральского региона в Европу продукция доставляется траками (грузовыми фурами), некоторым заказчикам - контейнерами на судах из морских портов Санкт-Петербурга и Новороссийска, а также по железной дороге. Так, например, если еще до недавнего времени доставка фанеры в Китай осуществлялась в основном по морю, то сейчас активно прорабатывается вопрос транспортировки по железной дороге. Не менее активно идет работа и с заказчиками из Казахстана - в этот регион в основном отгружаются ламинированная фанера и фанера для строительства.
Кадры
Сейчас на комбинате трудится 1200 человек. Это высококлассные специалисты из разных регионов Сибири и Урала и других регионов (на предприятии идет постоянный обмен опытом). Большое число сотрудников - жители поселка и соседних деревень. Таким образом, комбинат «СВЕЗА Верхняя Синячиха» является градообразующим предприятием. Руководитель комбината Илья Радченко с гордостью отмечает, что проблем с кадрами на предприятии нет: «Люди в поселке у нас хорошие. И мы стараемся поддерживать комфортные условия работы и организовывать досуг. Благодаря поддержке местной администрации район развивается, людям есть где работать и отдыхать (например, построен огромный спортивный комплекс с тренажерным залом, плавательным бассейном на 25 метров, открытой площадкой, которому позавидуют даже в крупных городах. - Прим. автора). Большинство местных жителей работают на комбинате и получают достойную заработную плату. У нас нет вакансий, наоборот, есть очередь желающих прийти к нам трудиться. На еженедельном приеме посетителей по личным вопросам мне часто приходится отвечать на просьбы о приеме на работу».
Комбинат работает круглосуточно, в четыре смены, по 12 часов каждая. Большое внимание здесь уделяется вовлеченности персонала в рабочий процесс. На предприятии считают, что сотрудники, вовлеченные в дела компании, это люди, которые хотят эффективно работать, а не просто отбывать 12 часов на рабочем месте.
Об автоматизации производственного процесса
Рассказывая об автоматизации производственного процесса и довольно большой доли ручного труда на комбинате, Илья Радченко отмечает: «Мы принимаем меры для автоматизации производства, благодаря чему произошло увеличение объемов производства почти на 40%, а доля ручного труда на комбинате сократилась. Например, на сегодня полностью автоматизированы процессы сортировки и упаковки, что позволило за последние годы повысить производительность в полтора раза».
Планы на будущее
Планы развития комбината амбициозные и большие. К 2020 году на предприятии намерены довести объем выпуска фанеры до 234,2 тыс. м3 в год. Безусловно, продолжатся модернизация оборудования, совершенствование технологий, поиск новых каналов сбыта и точек роста. Рассматриваются и возможности организации производства новых продуктов.
Постоянное развитие и оптимизация бизнес-процессов - неотъемлемая часть деятельности комбината «СВЕЗА Верхняя Синячиха». Поэтому проект «Сакура» очень важен для предприятия: в 2015 году с консалтинговой компанией Toyota Engineering Corporation был заключен договор «Об оказании консультационных услуг по внедрению системы производственных и сопутствующих процессов на основе всеобщей производственной системы Toyota T-TPS». Цели этого проекта: повышение производительности, сокращение межоперационных запасов, в частности сырого и сухого шпона, на протяжении всего жизненного цикла продукта, оптимизация материальных потоков по всей производственной цепочке, повышение качества продукции и обучение персонала новым методам работы на основе T-TPS. Результатом сотрудничества должно стать достижение общей оценки предприятия по мировому сравнительному анализу (GBM) три балла, а в дальнейшем и более высокой оценки ТЕС (текущая оценка 2,75 балла, а на старте проекта она была 1,1 балла). Получение оценки три балла, которое ожидается в результате оптимизации производственных и организационных процессов, позволит российской компании встать в один ряд с поставщиками концерна Toyota.
Подготовила Ольга РЯБИНИНА