Организация механической обработки и химической переработки древесины
Растущий уровень производства в российской лесоперерабатывающей промышленности обуславливает необходимость постоянного повышения квалификации работников, систематического совершенствования знаний по организации производственных процессов с учетом научно-технических достижений.
Производство любой продукции представляет собой воздействие живого труда на предметы труда с помощью орудий труда. Следовательно, производственный процесс включает следующие три необходимых элемента: труд – целесообразную деятельность людей, направленную на создание материальных благ; предметы труда – сырье и материалы, из которых изготовляется продукция; средства труда – агрегаты и машины, образующие материально-техническую базу производства.
Производственный процесс состоит из технологического процесса и организационных перерывов. Совокупность технологических операций и перерывов, связанных с обработкой и перемещением предметов труда между рабочими местами, составляет технологический процесс изготовления изделия (узлов, деталей) или выполняемых работ (сушки пиломатериалов, гнутья заготовок, технологической выдержки и т. п.).
В зависимости от роли в формировании готового продукта (полуфабриката) или выполняемых работах технологические операции подразделяются на основные и вспомогательные. Основные операции связаны непосредственно с обработкой предметов труда, вспомогательные – это транспортные, контрольно-учетно-сортировочные и операции хранения.
К технологическим перерывам относят межоперационные перерывы и технологические выдержки. Перерывы заранее предусматриваются в технологическом процессе, а окончательная их продолжительность регулируется в соответствии с условиями организации производства. Организационные перерывы полностью зависят от условий организации труда на предприятии (в цехе, на участке), то есть от сроков выполнения заданий, условий поставки сырья и материалов, режима работы и т. д.
Технологический процесс по отдельным видам производства разрабатывается на стадии проектирования или перевооружения предприятия, а затем отлаживается применительно к конкретным условиям и постоянно совершенствуется в ходе производства. Оформляется технологический процесс в виде технологических карт, альбомов, схем и других документов, в которых приводится перечень всех операций и их содержание, необходимого оборудования, приспособлений, требования к предметам труда до обработки и после нее (конструктивные, физические, химические), последовательность и продолжительность выполнения операций и другие сведения.
Основой производственного процесса служит технологический процесс, который для всех видов деревообрабатывающих производств можно разделить на три крупные стадии: раскройно-заготовительную, машинной обработки и сборочно-отделочную. В каждой из этих стадий, в свою очередь, можно выделить технологические процессы более дробных стадий в совокупности операций. Так, в лесопильном производстве раскройно-заготовительная стадия включает раскрой хлыстов, окорку, сортировку и подачу бревен в лесопильный цех, стадия машинной обработки – распиловку бревен, обрезку и торцовку досок, изготовление технологической щепы, сборочно-отделочная стадия – сушку досок, сортировку и формирование пакетов пиломатериалов.
Технология изготовления мебели может включать следующие технологические процессы: по первой стадии – сушку и раскрой древесных материалов, раскрой шпона и изготовление облицовок; по второй – обработку черновых и чистовых заготовок, склеивание и облицовывание заготовок; по третьей – сборку деталей в сборочные единицы и их отделку.
При организации производственного процесса технологические процессы квалифицируют по двум важнейшим признакам: способу формирования готовой продукции (полуфабрикатов) и движению предметов труда в пространстве (между рабочими местами, от одной операции к другой) и во времени. По первому признаку выделяют простые процессы, в которых готовую продукцию (полуфабрикат) получают путем последовательной обработки одного предмета, и сложные, при которых готовое изделие (узел) получают соединением отдельных узлов или деталей. Простые процессы характерны для лесопильного производства, изготовления сухого шпона, производства древесных плит, а сложные – для склеивания фанеры, операций в сборочных цехах столярно-механических производств и т. п. По второму признаку различают прерывные и непрерывные технологические процессы. При прерывном процессе накапливается и передается с одной операции на другую вся планируемая партия деталей (изделий), при непрерывном каждая деталь (изделие) или небольшая транспортная (передаточная) партия деталей (изделий) сразу поступает с одной операции на следующую.
Организация производственного процесса во времени характеризуется длительностью производственного цикла – временем от поступления исходных предметов труда до выхода полуфабриката (готового продукта) с участка, цеха или предприятия. Исходными материалами могут быть сырье, материалы, полуфабрикаты, заготовки, комплектующие узлы. На деревообрабатывающих предприятиях производственный цикл рассматривается применительно к партиям из десятков и сотен деталей и изделий. В зависимости от размера партии длительность производственного цикла учитывается в часах или календарных днях. От длительности производственного цикла немало зависят сроки и комплектность выпуска продукции, ритмичность производства, выполнение ассортиментного плана, производительность труда, размер незавершенного производства, производственные запасы и заделы. Длительность производственного цикла рассчитывают по столярно-механическим производствам: мебельному, музыкальных инструментов, оконных и дверных блоков, стандартного домостроения.
Длительность технологического (Ттех) и производственного (Тц) циклов рассчитывается по формулам:
Ттех = Тос + Твс + Тмо + Тв
и
Тц = Ттех + Трв + Тпр,
где ТОС – длительность основных технологических операций; Твс – длительность вспомогательных операций; Тмо – межоперационные перерывы; Т – технологические выдержки; Трв – перерывы, обусловленные режимом рабочего времени (нерабочие смены, дни, обеденные и другие регламентированные перерывы); Тпр – прочие перерывы, связанные с нарушениями организации производства: отключением электроэнергии, несвоевременным обеспечением материалами, инструментами и т. д. (в плановых расчетах не учитываются). Структура производственного цикла показана на рис. 1.
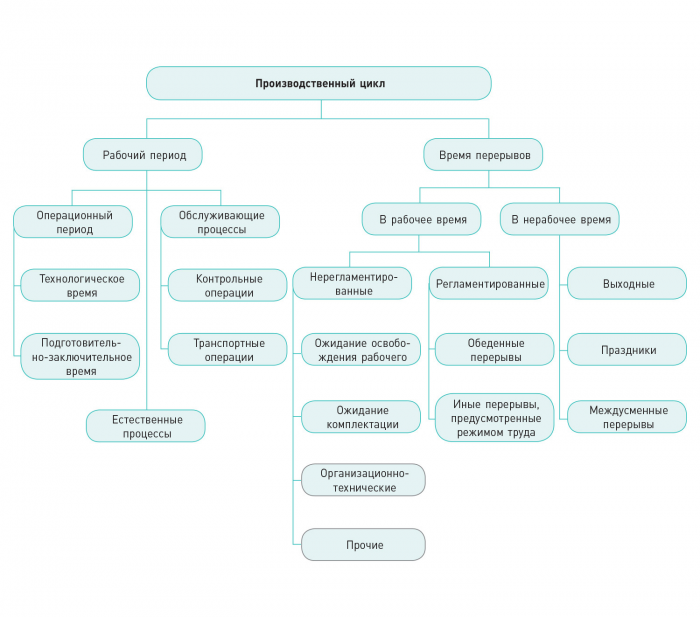
Длительность основных технологических операций Тос зависит от нормативной продолжительности каждой операции, размера партии деталей (изделий), процента выполнения норм выработки, числа рабочих мест на одноименных операциях, размера передаточных партий деталей (изделий) и последовательности выполнения операций. При расчете длительности цикла выделяют две формы движения деталей: прерывную (последовательную или параллельно-последовательную) и непрерывную (параллельную).
При прерывном движении детали направляются с одной операции на другую передаточными партиями, при непрерывном каждая деталь после одной операции сразу передается на следующую. Прерывная форма движения деталей используется при групповой расстановке станков, непрерывная – при цепной, особенно на поточных и автоматических линиях. Длительность выполнения основных технологических операций определяют по формуле:
где m – число операций; (m – 1) – число операций без последней; toп.i – длительность цикла i-й операции, мин; nд – число деталей в партии, шт.; pi – число деталей в передаточной партии по i-й операции, шт.; tмi – длительность меньшей операции из i-й и последующей, мин; t – длительность главной (наиболее продолжительной) операции, мин (табл. 1).
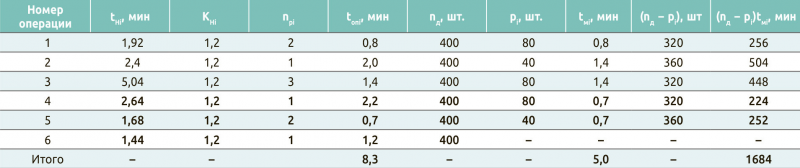
Длительность i-й операции (операционного цикла) рассчитывается по формуле
где tНi – нормативная длительность i-й операции (принимается по технологическим картам), мин; КНi – коэффициент выполнения норм выработки на i-й операции; npi – число рабочих мест, на которых одновременно выполняется i-я операция.
Рассчитаем длительность основных технологических операций при заданном числе операций, их нормативном времени, числе рабочих мест и передаточных партий по каждой операции (табл. 1). Партия запуска деталей – 400 шт., среднее выполнение норм выработки по всем операциям – 120%. Ниже приведены промежуточные результаты (табл. 2).
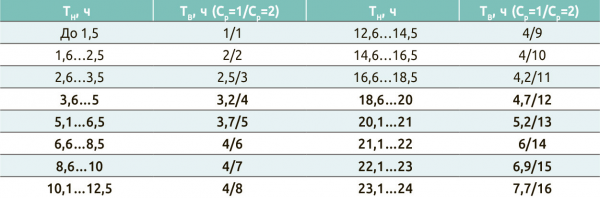
При прерывной форме движения деталей Т = 400·8,3 – 1684 = 1636 мин = 27,3 ч; при непрерывной Тос.н = 8,3 + (400 – 1) 2,2 = 8886 мин = 148 ч.
Длительность вспомогательных операций Твс, выполняемых на деревообрабатывающих предприятиях в большинстве случаев одновременно с обработкой деталей, так же перекрывается перерывами – межоперационными и связанными с режимом работы цеха, и это время при расчете длительности производственного цикла не учитывается. Если этого времени недостаточно, необходимо определить Твс путем замеров и специальных расчетов. Технологические перерывы Тв включают технологические выдержки, которые зависят от нормативной выдержки Тн и сменности работы цеха Ср. Тв можно также определить по формуле Тв = Тн – Тпер, где Тпер – величина перекрытия Тн нерабочим временем, ч. В более точных расчетах Тпер определяется применительно к конкретным условиям производства. При трехсменном режиме работы цеха Тв = Тн.
Межоперационные перерывы Тмо – это перерывы в процессе производства партии деталей, вызванные ожиданием освобождения рабочего места, занятого обработкой других партий деталей. На одном рабочем месте могут выполняться несколько разных операций и обрабатываться детали разных наименований (от одного до 30 наименований предмето-операций). Из-за чередования обработки партий деталей разных наименований и разных операций на одном рабочем месте возникают перерывы, которые могут занимать значительную часть производственного цикла. Тмо зависят от уровня специализации технологических процессов, на деревообрабатывающих предприятиях Тмо = (0…1,2) Тос. Чем выше уровень специализации, тем меньше Тмо. В реальных условиях производства продолжительность межоперационных перерывов следует тщательно обосновывать. При укрупненных расчетах ее определяют по формуле
Тмо = 1,2 Тос (1 – Кпар),
где Кпар – коэффициент параллельности технологического процесса,
i=1 В приведенном выше примере для прерывного процесса Кпар = 1684/400 (8,3 – 1,2) = 1684/2840 = 0,59, а Тмо = 1,2 × 27,3 (1 – 0,59) = 13,4 ч; для непрерывного Кпар = (400 – 1)·5/2840 = 0,7, а Тмо = 1,2 × 14,8 (1 – 0,7) = 5,3 ч.
Перерывы, связанные с режимом рабочего времени Тр.в, вызваны пролеживанием деталей (изделий) без обработки между сменами, в выходные и праздничные дни и учитываются с помощью коэффициента режима рабочего времени Креж. Креж = Ткал/Тпл, где Ткал и Тпл – календарный и планируемый фонд времени работы цеха за определенный период соответственно. Креж зависит от сменности работы цеха Ср и длительности Тос + Тмо (табл. 3). При ее величине до одной смены (I), свыше одной смены и до недели (II), свыше недели (III) значительно увеличивается длительность производственного цикла. (Для удобства пользования эти варианты в таблице приведены в часах.)

Полная длительность производственного цикла партии каждой детали (узла) в заготовительно-отделочных цехах и партии каждого изделия в сборочных цехах деревообрабатывающих предприятий укрупненно определяется по формуле
Тц = (Тосн + Тмо) Креж + Тв.
Полная длительность производственного цикла партии изделия равна
i=1 где n – число цехов от заготовительного до отделочного включительно; Тц.дет – длительность производственного цикла партии наиболее трудоемкой детали по совокупности цехов; Тц.сб – длительность производственного цикла партии изделия в сборочном цехе, ч.
Предположим, на мебельной фабрике планируется выпустить партию платяных шкафов из 200 шт. Рассчитана длительность производственного цикла по цехам и деталям (табл. 4).
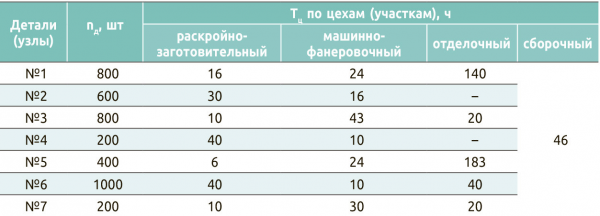
Общая продолжительность производственного цикла Тц.изд = (6 + 24 + 183) +46 = 213 + 46 = 259 ч = 10,8 дня. Таким образом, партия платяных шкафов в количестве 200 шт. будет изготовлена примерно за 11 календарных дней.
Организация поточного производства предполагает ритмичный выпуск продукции. Показателями ритмичности служат такт и ритм. Тактом называется промежуток времени между выпуском с линии двух очередных деталей (изделий) или партий деталей (изделий), а ритм – это число деталей (изделий), сходящих с линии за определенный промежуток времени. Такт и ритм связаны обратно пропорциональной зависимостью.
Такт измеряется в минутах, ритм – числом деталей (изделий), изготовленных в минуту, час, смену, сутки. Различают следующие такты: планируемый tпл, средний tср, рабочий tр и операционный tоп. Планируемый такт – это планируемый (необходимый) промежуток времени между выходом с линии двух очередных деталей (изделий),
где Тсм – продолжительность смены, мин; Тпер – продолжительность регламентированных перерывов (≈30 мин); Асм – сменное задание по выпуску деталей (изделий).
Средний такт – это физический (расчетный) промежуток времени между выходом двух очередных деталей (изделий) из потока. Он равен длительности наиболее продолжительной операции, то есть tср = tоп.макс.
Рабочий такт – это фактический (расчетный) промежуток времени между выходом с потока двух очередных передаточных (транспортных) партий деталей (изделий), tр = tср nпер, где nпер – число деталей (изделий) в передаточной партии.
Операционный такт – это фактическая (расчетная) длительность обработки одной детали (изделия) на определенной операции с учетом количества рабочих мест.
Для обеспечения ритмичности выпуска продукции необходимо соблюдение следующего условия:
tср = tпл, или tн = К, → tпл = (1 ± 0,15),
где tн – нормативная длительность операции, К – целое число (1; 2; 3 и т. д.). Различают ритмы планируемый rпл и средний rср. Планируемый ритм – это необходимый (планируемый), а средний ритм – фактически возможный (расчетный) выпуск деталей (изделий) из потока в минуту, час, смену, сутки:
rпл = 1/tпл ; → rср = 1/tср ,
где tпл и tср – планируемый и средний такты на одну деталь соответственно.
На деревообрабатывающих предприятиях, прежде всего мебельных, чаще всего устанавливаются следующие три вида линий.
- Поточные линии с переменным потоком, в которых станки (рабочие места), расположенные по ходу технологического процесса, соединены транспортными средствами – неприводными и приводными конвейерами (в исключительных случаях используют ручные тележки и электрокары). Каждую операцию выполняют на одном или нескольких станках (рабочих местах). На линии могут быть ручные, машинно-ручные и машинные операции. Используемое оборудование на разных операциях строго не увязано по производительности, поэтому нет регламентированного такта. Длительность операций на линии находится в диапазоне ±15% планируемого такта, то есть отношение максимальной и минимальной продолжительности операций может достигать 35%. Такие линии довольно мобильны, не требуют больших затрат времени на переналадку при изменении планируемых объемов и ассортимента выпускаемой продукции, но некоторые виды оборудования недостаточно загружены на ряде операций, поэтому необходимо иметь запас деталей.
- Непрерывно-поточные линии, в которых станки (рабочие места), как правило, соединены едиными транспортными средствами (конвейерами). Остановка одной операции вызывает остановку всей линии. Для таких линий характерны машинно-ручные, машинные операции, а на некоторых рабочих местах – автоматизированные. Длительность операций равна планируемому такту ±10%, то есть отношение максимальной и минимальной продолжительности операций может достигать 22%. Эти линии менее мобильны, чем поточные линии с переменным потоком, а их переналадка требует больших затрат времени. Преимущества – устойчивый ритм и высокая производительность.
- Автоматические поточные линии, на которых все операции обработки и движения предметов труда осуществляются автоматически, лишь загрузка и выгрузка деталей могут быть машинно-ручными. Отступление от средней величины планируемого такта в пределах ±5%. Планируемый суточный (сменный) выпуск продукции увязывается с производительностью линии, а не наоборот. Эти линии способствуют повышению эффективности производства.
Одно из основных условий организации работы на поточной линии – синхронизация потока, то есть расчленение процесса на такие операции, нормативная длительность которых равна или кратна планируемому такту. Синхронизация поточной линии проводится в два этапа. На первом осуществляется предварительная синхронизация, при которой отклонение операционных тактов от планируемого допускается в пределах ±10–15%, на втором этапе (в ходе работы поточной линии) уточняется и корректируется продолжительность операций, то есть проводится окончательная, точная синхронизация.
Окончательная синхронизация в зависимости от вида поточной линии достигается внедрением малой механизации и специального оборудования, форсированием технологических режимов, использованием высокопроизводительной оснастки, более рациональной планировкой и организацией рабочих мест. В исключительных случаях может возникнуть необходимость пересмотра конструкции деталей или изделий.
В настоящее время поточная организация производства наиболее распространена на деревообрабатывающих предприятиях. В производство внедряются автоматические поточные линии, которые должны обеспечить самую высокую производительность труда, полное и наиболее рациональное использование новый техники и применяемых материальных ресурсов, минимальные сроки изготовления продукции, эффективность инвестиций.
Производственный процесс как совокупность технологически взаимосвязанных работ различается в зависимости от вида производимых изделий. Отсюда возникает необходимость использования разных методов организации производства, определяемых технологическим процессом, характером производимой продукции, типом производства, уровнем техники, режимом работы предприятия и т. д. Например, на целлюлозно-бумажных и лесохимических предприятиях круглосуточное производство, режим их работы почти не влияет на длительность производственного цикла. На деревообрабатывающих предприятиях в большинстве случаев весьма длительные перерывы, обусловленные режимом работы. На целлюлозно-бумажных и лесохимических предприятиях чаще всего налажено массовое производство, а на деревообрабатывающих, помимо массового, широко практикуется серийное и единичное производство.
В целлюлозно-бумажной промышленности индивидуальное производство имеет место в ремонтно-механических мастерских, при изготовлении отдельных деталей и узлов для оборудования в цехах основного производства. Аналогично и на лесохимических предприятиях.
Серийное производство – это выпуск однотипной продукции сериями, то есть определенным количеством одноименных изделий за определенный отрезок времени. Различают мелкосерийное, среднесерийное и крупносерийное производства. Мелкосерийное производство ближе к индивидуальному, а крупносерийное – к массовому. При серийном производстве оборудование может быть как универсальным, так и специализированным. Технологический процесс разрабатывается более детально, чем при индивидуальном производстве, поэтому квалификация рабочих обычно ниже, а рабочие места узко специализированы.
В отличие от индивидуального производства, при серийном выше коэффициент использования оборудования, короче производственный цикл, выше производительность труда и ниже себестоимость продукции.
В целлюлозно-бумажной промышленности серийное производство используется при выработке особых марок бумаги специального назначения и при изготовлении изделий из бумаги и картона для определенного потребителя. Серийное производство применяется также на вспомогательных производствах, при изготовлении серии однотипных деталей для оборудования, специального режущего инструмента и т. д.
Массовое производство отличается от серийного и индивидуального большим, неограниченным объемом однотипных изделий, выпускаемых непрерывно, лишь с периодическими внесениями изменений в технологический процесс для повышения качества изделия, его надежности и долговечности. На массовом производстве высокий уровень специализации рабочих мест, подробно разработанная технология, все оборудование специализированное, с широким применением автоматических и полуавтоматических установок, средняя квалификация рабочих ниже, чем на серийном и индивидуальном производствах, а высокий уровень специализации и большой объем продукции позволяют производить ее с минимальными затратами, достигать высоких производительности труда и коэффициента использования оборудования и минимальной продолжительности производственного цикла.
Основной процесс включает круг операций и естественных процессов, направленных на изменение формы, физических и химических свойств перерабатываемого сырья и материалов с целью создания основных видов продукции предприятия (бумаги, целлюлозы, древесной массы и т. д.). На лесохимических заводах основное производство, как правило, обеспечивает выпуск нескольких видов продукции: 1) древесного угля, уксусной кислоты, этилацетата (пиролизное производство); 2) канифоли, скипидара и продуктов на их основе (канифольно-экстракционное и канифольно-терпентинное производства); 3) растворителей ингибитора, пластификатора, крепителей и др. (переделочные производства); 4) хлорофиллина натрия, эфирных масел, хвойного воска и др. (переработка древесной зелени).
Основной производственный процесс состоит из более простых, частичных, процессов – стадий. Стадия состоит из операций и представляет собой законченный этап производственного процесса. Так, процесс производства уксусной кислоты включает следующие стадии: I – подготовка сырья к пиролизу; II – пиролиз сырья; III – переработка жижки; IV – розлив и упаковка кислоты. Стадия переработки жижки состоит из нескольких операций: отстаивание, обесспиртовывание, обессмоливание, экстракция кислоты-сырца, ректификация кислоты-сырца.
К побочным производствам относятся переработка отходов основного производства (например, получение таллового масла из сульфитного щелока; изготовление минеральной кормовой добавки из древесно-угольной мелочи и т. д.).
Вспомогательные процессы обеспечивают все необходимое для обслуживания основных процессов изготовления продукции. К ним относятся ремонт оборудования, зданий и сооружений, изготовление инструментов и запасных частей для ремонтируемых машин, оборудования и прочего, производство пара и т. д. В большинстве случаев эти процессы являются обособленными частями производства и выделяются в самостоятельные подразделения предприятия.
Обслуживающие процессы обеспечивают нормальную работу производственного процесса. Это снабжение производства сырьем, материалами, оснасткой, инструментом, работа внутрипроизводственного транспорта, складское хранение запасов продукции и сырья, материалов, инструментов и прочего, погрузо-разгрузочные операции и др.
На современных целлюлозно-бумажных и лесохимических предприятиях в производственных процессах используется много сложных аппаратов, разнообразные виды сырья и материалов, поэтому рациональная организация материального и технического обслуживания имеет большое значение для организации производственного процесса.
Из комплекса производственных процессов, осуществляемых на целлюлозно-бумажных и лесохимических предприятиях, следует выделить процессы производства основной (целевой) продукции, для выработки которой они и созданы. Выпуск каждого вида продукции представляет собой процесс основного производства. Изучение процессов целлюлозно-бумажного производства осуществляется по циклам (стадиям) и операциям. Например, производство целлюлозы может быть разделено на 13 циклов (рис. 2). Производство бумаги состоит из следующих процессов: подготовки бумажной массы для отлива бумаги, варки проклеивающих веществ, подготовки суспензии наполнителя, изготовления бумаги, отделки бумаги (каландрирование, разрезка на рулоны, бобины и листы), сортировки и упаковки.
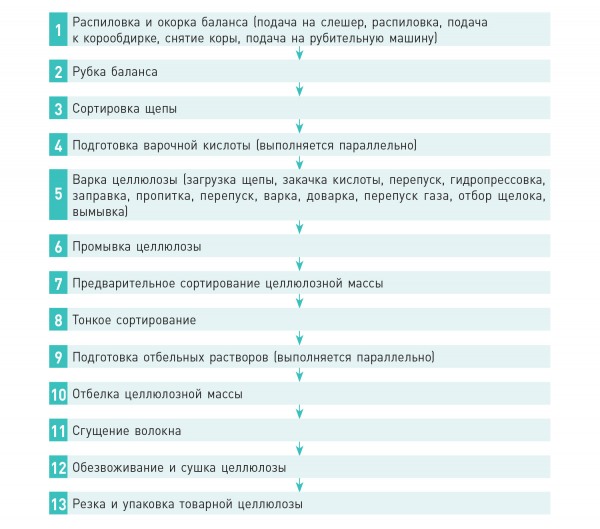
Разделение процесса на циклы может меняться в зависимости от уровня техники и технологии производства, условий на предприятии, но прежде всего от выбранной технологической схемы.
В зависимости от характера изготовления продукции технологические процессы подразделяются на простые и сложные. При простых в результате последовательной обработки исходного сырья получается конечный продукт. Примером простого процесса в целлюлозно-бумажном производстве может быть дефибрирование, в пиролизном – распиловка бревен на чураки и др. В сложных технологических процессах одновременно осуществляются простые процессы производства полуфабрикатов, которые в дальнейшем путем механического или химического соединения превращаются в готовый продукт (производство полуцеллюлозы, целлюлозы, древесной массы).
В целлюлозно-бумажном и лесохимическом производствах использутся как непрерывные, так и периодические процессы. При периодических (прерывных) процессах загружают сырье и материалы и выгружают полуфабрикаты или продукцию периодически, с прекращением на время работы механизмов и оборудования. Обрабатываемые предметы при этом задерживаются на определенных рабочих местах до продолжения обработки. На лесохимическом производстве периодически функционируют экстракторы, плавильники, некоторые марки реторт. При непрерывных производственных процессах сырье загружается и обрабатывается, а полуфабрикаты или продукция выгружаются непрерывно. В случае химической обработки реагенты, поступающие в аппарат, постоянно взаимодействуют с сырьем. Загрузка реагентов и отвод продуктов могут осуществляться непрерывно или периодически, но без прекращения работы аппарата. То есть по сравнению с периодическими процессами непрерывные более совершенные, они обеспечивают резкое повышение производительности труда. Дальнейшее развитие химической переработки древесины будет связано с внедрением на всех участках основного производства непрерывных технологических процессов, организацией поточного и автоматизированного производства, характеризующихся высокой экономической эффективностью. Примером может служить современная организация поточного производства бумаги.
Одним из важнейших критериев оценки уровня организации производства на целлюлозно-бумажных и лесохимических предприятиях выступает производственный цикл – время нахождения изделия (продукции) в процессе изготовления. Производственный цикл характеризуется длительностью и структурой и состоит из рабочего периода (в течение которого предмет труда находится в процессе изготовления) и перерывов.
Рабочий период цикла включает время выполнения основного и обслуживающих процессов, необходимых для изготовления заказа. Доля рабочего периода цикла в его общей длительности характеризует непрерывность движения предметов труда по операциям производственного процесса. Чем больше доля рабочего периода, тем совершеннее организация производственного процесса по времени на предприятии. В составе рабочего периода цикла выделяют операционный период и время выполнения естественных и обслуживающих процессов.
Операционный период является основной частью производственного цикла по структуре использования календарного времени и представляет собой время, затрачиваемое на выполнение рабочих операций или совокупность операций основного производственного процесса по изготовлению конкретного изделия. Операционный период состоит из времени выполнения технологических операций и подготовительного времени.
Время выполнения технологических операций (или технологическое время) является основной частью операционного цикла, затрачиваемой непосредственно на изготовление продукции, и может быть отнесено к учетной единице измерения продукции.
Подготовительно-заключительное (вспомогательное) время включает время, затрачиваемое на подготовку к работе и получение и сдачу наряда, инструмента, дневника дежурства и пр.
В рабочий период входит время протекания естественных процессов, а также время контрольных и транспортных операций.
Второй составной частью производственного цикла являются перерывы: обусловленные способом изготовления продукта (перерывы в рабочее время) либо режимом работы предприятия (перерывы в нерабочее время).
Продолжительность производственного цикла изготовления основных видов целлюлозно-бумажной продукции Tц определяется по формуле
Tц = tтех + tec + tку + tтр + tпер,
где tтех – время технологических операций; tec, tку, tтр – время естественных процессов, контрольно-учетных и транспортных операций соответственно; tпер – перерывы, предусмотренные технологическим процессом.
Из формулы видно, что производственный цикл не учитывает временную составляющую, на которую оказывает влияние режим работы предприятия, поскольку в большинстве случаев на целлюлозно-бумажных и лесохимических предприятиях организовано непрерывное, круглосуточное, производство. Это обстоятельство значительно сокращает производственный цикл, от которого зависит количество продукции, которое может быть отработано за определенный период времени, оборачиваемость оборотных средств, производительность труда. Чем продолжительнее производственный цикл за счет режимных перерывов, тем больше оборотных средств требуется предприятию. А режимные перерывы могут быть длительными. Достаточно сказать, что в прерывном производстве производственный цикл за счет сменности удлиняется примерно на 17 ч при односменной работе, на 10 ч при двухсменной работе и на 3,5 ч – при трехсменной.
Основу производственного процесса все же составляет рабочий период (технологический цикл), поэтому важнейшей задачей совершенствования организации производства является сокращение длительности технологического цикла за счет уменьшения затрат времени на выполнение технологических операций.
На предприятиях ЦБП и лесохимической промышленности в основном производстве совмещаются во времени производственные операции, поэтому длительность технологического цикла устанавливается по самой продолжительной операции. Расчет выполняется по формуле
Tц = tоб/Qi,
где tоб – продолжительность одного оборота; Q – количество сырья, загруженного в аппараты за один оборот; i – выход продукции из единицы сырья.
Предположим, на целлюлозном заводе длительность оборота варочного аппарата составляет 7,5 ч, емкость котла 280 м3, на 1 м3 емкости загружается 140 кг абсолютно сухой древесины, а выход целлюлозы 52%. При таких исходных данных за каждые 23 мин (7,5 × 60/280 × 0,140 × 0,50) вырабатывается 1 т целлюлозы.
При непрерывно действующем основном оборудовании длительность производственного цикла определяется по формуле
Tц = 1/Qi,
где Q – количество сырья, загружаемого в аппараты в течение 1 ч; i – выход продукции из единицы сырья.
Сейчас прорабатываются вопросы внедрения непрерывных процессов произво дства во всех технологических схемах получения лесопродукции. При этом большая роль отводится научно-технической подготовке производства (рис. 3).
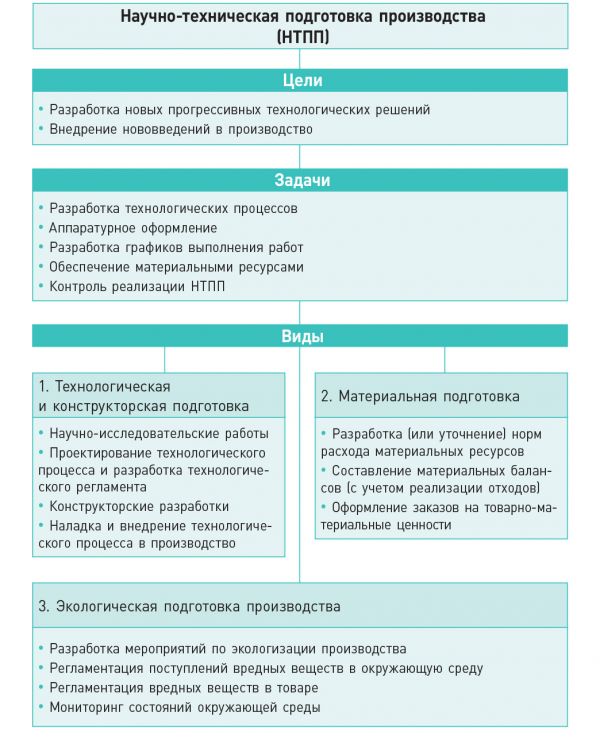
Текст
Владимир Мосягин, д-р экон. наук, член-корр. международной академии наук высшей школы, профессор СПбЛТУ