Как из кряжей шпон лущили...
Усилиями научно-технических работников отрасли производства фанеры как в России, так и за рубежом создана современная структура технологического процесса изготовления фанеры. Однако разнообразие видов фанеры, безусловно, определяет ряд особенностей технологических процессов их производства.
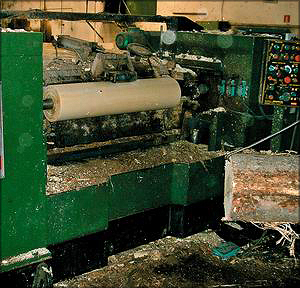
Станок по производству лущеного шпона
Общая схема процесса следующая. Древесное сырье (кряжи) распиливается на чураки, длина которых соответствует длине листа шпона. Эта операция выполняется на круглопильных агрегатах. В случае использования сырья большого диаметра (60 см и более) применяют станки с цепными пилами. Далее сырье подвергается гидротермической обработке: его нагревают и увлажняют в бассейнах с горячей водой. Это делается для повышения эластичности древесины перед лущением, так как при лущении холодной и недостаточно влажной древесины шпон получается шероховатым и трескается, вплоть до разрушения. Затем сырье окаривается на окорочных станках - наличие коры снижает производительность лущильного станка, а присутствие в ней минеральных загрязнений (песка и других) ведет к быстрому затуплению режущего инструмента. Последовательность перечисленных операций может меняться в зависимости от условий производства, например распиловку сырья производят и после тепловой обработки.
Подготовленное таким образом сырье поступает на лущильные станки, на которых производится лущение древесины. Шпон из станка выходит в виде ленты шириной, равной длине чурака, и рубится на листы требуемой ширины гильотинными или более современными роторными ножницами. В результате лущения образуются отходы: из поверхностной зоны чурака - рванина, из центральной - карандаш. Они используются для выработки щепы, применяемой для древесностружечных, древесноволокнистых плит и в качестве топлива.
Шпон должен иметь влажность 6±2%. В связи с этим его подвергают сушке в паровых или газовых сушилках проходного типа, а затем сортируют в соответствии с требованиями, предъявляемыми к шпону для наружных и внутренних слоев фанеры.
Возможна и другая схема изготовления шпона, когда его сушат в виде ленты, а затем рубят на листы. Каждая из схем имеет свои достоинства и недостатки.
Стремление повысить качество фанеры определяет необходимость нормализации размеров и качества шпона. Из листов шпона вырубают пороки и заделывают вырубки вставками из шпона. Это делается на шпоно¬починочных станках. Нередко пороки устраняют посредством вырубки из ленты шпона зоны порока по всей ее ширине. В этом случае получающиеся куски шпона склеивают с помощью стеклонити, покрытой полиамидной смолой. Для этого используются ребросклеивающие станки с продольной или поперечной подачей шпона. Таким же образом ребросклеивают и пусковой шпон, образующийся на этапе лущения или в процессе сушки, транспортировки шпона. Ребросклеивание повышает качество фанеры и дает возможность механизированного перемещения листов шпона в процессе сборки пакетов для изготовления фанеры.
Подготовленный таким образом шпон после его кондиционирования поступает на участок склеивания. Современные участки построены обычно на базе многоэтажных 20-40-этажных горячих прессов, оборудованных механизмами загрузки пакетов, выгрузки фанеры. В состав оборудования участка входят также станки для нанесения клея (вольцовые, наливные), механизмы укладки шпона в пакеты, пресс для подпрессовки пакетов в собранных стопах, переместительные устройства.
Пакеты для изготовления фанеры обычно состоят из нечетного количества листов шпона. Клей наносят на каждый четный лист шпона. При сборке пакетов в стопу последовательно чередуют листы шпона без клея и с клеем. Стопы перемещают к прессу для подпрессовки, которая необходима для улучшения качества склеивания и придания пакетам компактности. После этого пакеты загружают в промежутки горячего пресса.
Склеенную фанеру кондиционируют, а затем обрезают по периметру на механизированных линиях обрезки, оборудованных круглопильными станками.
Нередко фанеру шлифуют с двух или одной стороны. Это делается на широколенточных шлифовальных станках. При этом снижается шероховатость поверхности фанеры и повышается ее точность по толщине (калибрование). Далее фанеру сортируют, иногда заделывают мелкие дефекты, маркируют в соответствии с сортом и упаковывают для транспортировки.
Подготовленное таким образом сырье поступает на лущильные станки, на которых производится лущение древесины. Шпон из станка выходит в виде ленты шириной, равной длине чурака, и рубится на листы требуемой ширины гильотинными или более современными роторными ножницами. В результате лущения образуются отходы: из поверхностной зоны чурака - рванина, из центральной - карандаш. Они используются для выработки щепы, применяемой для древесностружечных, древесноволокнистых плит и в качестве топлива.
Шпон должен иметь влажность 6±2%. В связи с этим его подвергают сушке в паровых или газовых сушилках проходного типа, а затем сортируют в соответствии с требованиями, предъявляемыми к шпону для наружных и внутренних слоев фанеры.
Возможна и другая схема изготовления шпона, когда его сушат в виде ленты, а затем рубят на листы. Каждая из схем имеет свои достоинства и недостатки.
Стремление повысить качество фанеры определяет необходимость нормализации размеров и качества шпона. Из листов шпона вырубают пороки и заделывают вырубки вставками из шпона. Это делается на шпоно¬починочных станках. Нередко пороки устраняют посредством вырубки из ленты шпона зоны порока по всей ее ширине. В этом случае получающиеся куски шпона склеивают с помощью стеклонити, покрытой полиамидной смолой. Для этого используются ребросклеивающие станки с продольной или поперечной подачей шпона. Таким же образом ребросклеивают и пусковой шпон, образующийся на этапе лущения или в процессе сушки, транспортировки шпона. Ребросклеивание повышает качество фанеры и дает возможность механизированного перемещения листов шпона в процессе сборки пакетов для изготовления фанеры.
Подготовленный таким образом шпон после его кондиционирования поступает на участок склеивания. Современные участки построены обычно на базе многоэтажных 20-40-этажных горячих прессов, оборудованных механизмами загрузки пакетов, выгрузки фанеры. В состав оборудования участка входят также станки для нанесения клея (вольцовые, наливные), механизмы укладки шпона в пакеты, пресс для подпрессовки пакетов в собранных стопах, переместительные устройства.
Пакеты для изготовления фанеры обычно состоят из нечетного количества листов шпона. Клей наносят на каждый четный лист шпона. При сборке пакетов в стопу последовательно чередуют листы шпона без клея и с клеем. Стопы перемещают к прессу для подпрессовки, которая необходима для улучшения качества склеивания и придания пакетам компактности. После этого пакеты загружают в промежутки горячего пресса.
Склеенную фанеру кондиционируют, а затем обрезают по периметру на механизированных линиях обрезки, оборудованных круглопильными станками.
Нередко фанеру шлифуют с двух или одной стороны. Это делается на широколенточных шлифовальных станках. При этом снижается шероховатость поверхности фанеры и повышается ее точность по толщине (калибрование). Далее фанеру сортируют, иногда заделывают мелкие дефекты, маркируют в соответствии с сортом и упаковывают для транспортировки.