Износ концевых деревообрабатывающих фрез
Критерии и причины
При фрезеровании, когда с поверхности заготовки срезается лишний материал (припуски на обработку), возникает трение на поверхностях зубьев фрезы. На передней поверхности зубьев трение проявляется как следствие скольжения снимаемого материала (стружки). По задней поверхности зуба трение возникает в результате взаимодействия с обрабатываемым материалом и его упругого восстановления.
В производственных условиях не всегда можно проследить степень износа зубьев фрезы, поэтому на переточку или замену режущих пластин фрезы часто отправляют, ориентируясь на их стойкость – период работы инструмента до достижения критического износа. На крупных производствах это, как правило, регулируется регламентами замены режущего инструмента, на мелких предприятиях – резким снижением качества обработанной поверхности, значительно сокращающим ресурс режущего инструмента. Поскольку стоимость современного высокопроизводительного инструмента довольно высокая и приобретали его раньше в основном за рубежом, актуальной задачей современной деревообработки стал переход к эксплуатации инструмента по фактическому состоянию и параметрам износа (контролируемых одним из методов нормоконтроля) и своевременной его замене.
Сейчас из-за экономических санкций ситуация на российском рынке дереворежущего инструмента меняется, появляется все больше отечественных инструментальных фирм, однако актуально и бережное и рациональное отношение к режущему инструменту, так как его доля в себестоимости выпускаемой продукции немалая.
Виды износа
Различают несколько видов износа фрез: абразивный, аварийный, окислительный и механический.
Абразивный износ – это повреждение режущей части в результате контакта с абразивными частицами, такими как металлические включения, песок, фрагменты лакокрасочных материалов. Увеличение скорости износа возможно в следующих случаях:
- фрагменты материала, находящиеся в рабочей зоне, имеют явные абразивные свойства (плитные и клееные материалы, ДПК);
- в заготовке содержатся твердые включения, устойчивые к режущему и температурному воздействию;
- обработка заготовок происходит на малой скорости подачи.
Аварийный износ – снижение остроты режущей части, сколы на лезвии и дальнейшее разрушение корпуса фрезы при чрезмерно высоких нагрузках на фрезу во время работе или из-за низкого качества ее изготовления. Самый травмоопасный вариант износа (рис. 1).
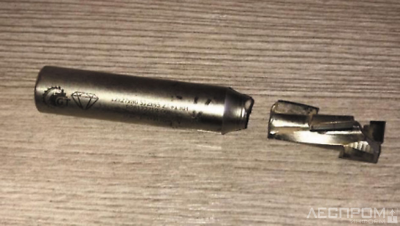
Окислительный износ. Преждевременный износ фрезы под действием внешних факторов, вызванный контактом разогретого режущего инструмента с кислородом, содержащимся в воздухе. В результате интенсивного окислительного износа меняется цвет инструмента (рис. 2).
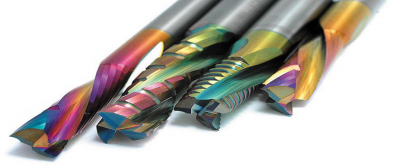
Механический износ вызван непосредственным воздействием на инструмент заготовок, приспособлений или иных элементов. Следствием становится затупление или скол режущей части зуба (лезвия) фрезы и в дальнейшем потеря функциональности инструмента.
Параметры износа
В зависимости от назначения инструмента используются разные критерии (параметры) износа фрез:
- достижение предельного износа, при котором повышается вероятность хрупкого разрушения (аварийного износа) инструмента и становится невозможна его переточка;
- достижение степени износа, при которой недопустимо повышается шероховатость обработанной поверхности или нарушается точность обработки.
Первый критерий определяет рациональную эксплуатацию инструмента и применяется при предварительной обработке или согласно заводским регламентам замены режущего инструмента. Второй, технологический, критерий используется при чистовой обработке (фрезеровании) и обеспечивает заданное качество (шероховатость поверхности) заготовки.
Интенсивному износу и последующему аварийному износу (поломке) фрез способствуют следующие факторы:
- неполное извлечение стружки из зоны резания;
- биение шпинделя и зажимного патрона при работе на скоростных режимах;
- длительное воздействие высокой температуры на режущий инструмент в зоне резания;
- некорректные параметры режущего инструмента и режимы обработки;
- контакт режущих кромок инструмента с абразивными включениями в материале;
- низкое качество режущего инструмента и расходных материалов при его изготовлении.
К регламентируемым параметрам износа относятся линейный размер изношенной площадки на лезвии инструмента; сила и температура резания; шероховатость обработанной поверхности; уровень вибраций и шума.
Наиболее простым и доступным для измерения параметром считается линейный размер изношенной площадки на лезвии инструмента. Контроль его производится с каждым снятием режущего инструмента со шпинделя станка. Влияние последствий, которые возникают в виде износа по задней и передней стенке, усиливается с увеличением силы резания в единицу времени и затраченной при фрезеровании мощности.
Силовой и температурный критерии используются в основном в лабораторных условиях или при специальных измерениях, а также при наличии специального измерительного оборудования. По мере увеличения износа инструмента растут сила и температура в зоне резания, что негативно сказывается как на оборудовании и режущем инструменте, так и на обрабатываемом материале, поскольку снижается качество получаемой поверхности.
Для производства перспективны вибрационный и шумовой параметры износа, так как их можно измерить при работе станка без снятия режущего инструмента с оборудования. Износ режущего инструмента проявляется повышенным шумом, посторонними звуками, усиленной вибрацией шпинделей оборудования.
Характеристики износа инструмента
При фрезеровании режущие кромки инструмента поочередно врезаются в заготовку, создавая при этом импульсы силы. В зависимости от материала заготовки и инструмента, геометрических параметров инструмента и режимов обработки меняется скорость износа инструмента. Износ в зоне вершины лезвия зуба принято называть радиальным (ρ), он зависит от скорости резания и подачи, твердости материала зуба и обрабатываемого материала, состояния оборудования и т. п. Кроме этого, происходит износ по передней и задней поверхностям зубьев фрез. При радиусе ρ = 0,005 мм зубья фрезы считаются острыми, а при ρ = 0,0015 мм – тупыми, поэтому необходима их переточка или замена.
Для фрез с напайными и сменными твердосплавными режущими пластинами, а также изготовленных из быстрорежущей стали или стеллита характерны следующие виды износа:
- выкрашивание зубьев;
- износ по задней и передней поверхности;
- лункообразование на кромках зуба;
- пластическая деформация;
- термические трещины на корпусе фрезы.
При износе режущих кромок зубьев фрез изменяются параметры воздействующих силовых импульсов (мощности резания), которые могут увеличиться больше чем в два раза.
Износ по задней грани зуба можно характеризовать шириной фаски износа hз (рис. 3).
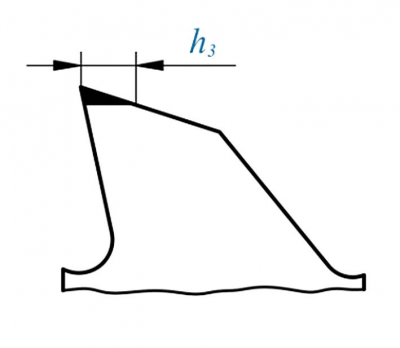
При обработке заготовок до точного размера, фреза не только изнашивается, на нее действует и упругая деформация в системе СПИД (станок–приспособление–инструмент–деталь). Деформация значительно усиливается с увеличением износа, который проявляется по задней и передней граням зуба. Показатель размерного износа, допускаемый при работе с материалом, можно установить только опытным путем для каждой ситуации и условий, в частности для определенных материала инструмента и обрабатываемого материала, так как нормативов не существует.
На передней поверхности зуба фрезы стружка выбирает лунку, а на задней образуется притертая к поверхности резания площадка без заднего угла, что приводит к увеличению трения задней поверхности, излишнему нагреву зуба и, как следствие, его повышенному износу и дальнейшему разрушению (аварийному износу). Особенно это опасно для фрез небольшого диаметра – 2–10 мм. Чтобы исключить аварийный износ подобных концевых фрез (прежде всего с корпусом из твердого сплава), следует соблюдать правило: длина максимальной рабочей режущей части корпуса не должна превышать 4–5 диаметров фрезы, а скорость подачи должна быть пропорциональна глубине обработки, особенно при обработке глухих пазов.
Как правило, величина износа h3 для концевых фрез не должна превышать 0,2–0,3 мм, иначе количество переточек инструмента значительно сократится, в том числе из-за потери твердости стали корпуса вследствие ее отпуска при нагреве и значительного съема материала зуба при переточке фрез, что отрицательно скажется на себестоимости готовой продукции из-за частой смены режущего инструмента.
Износ по задней и передней граням зуба также вызывает изменение переднего и заднего углов зуба, что, в свою очередь, может привести к значительному повышению мощности, затрачиваемой на резание, и снижению качества получаемой поверхности.
Стойкость режущего инструмента
Время, в течение которого заточенный инструмент работает до переточки, считается его стойкостью.
Если известны стойкость и время, затрачиваемое на обработку одной детали, то можно рассчитать, сколько заготовок удастся обработать за период от одной переточки до другой. Потраченное на одну заготовку время называют машинным временем.
Предположим, установленная стойкость фрезы 400 минут, а одна заготовка обрабатывается 10 минут – это ее машинное время обработки, которое учитывается при расчете производительности оборудования. В этом случае перетачивать фрезу придется после обработки каждых 40 заготовок.
Стойкость инструмента и его износ зависят от многих факторов, в том числе следующих:
- режимов резания;
- материала режущих зубьев фрез;
- геометрии инструмента, особенно угловых параметров;
- скорости резания и подачи;
- глубины и ширины фрезерования;
- качества (твердости) обрабатываемого материала.
Для повышения производительности труда и увеличения скорости подачи необходимо подобрать соответствующий по стойкости материал зуба фрезы, например твердый сплав или алмаз (DP), при которых можно достичь максимальной экономической эффективности обработки заготовок.
В качестве примера, можно привести выдержку из ГОСТ P 52589-2006 «Фрезы концевые, оснащенные твердым сплавом, для высокоскоростной обработки древесных материалов и пластиков», касающуюся принципов выбора режимов резания и стойкости твердосплавных фрез:
5.9. Испытания фрез для обработки древесных материалов на работоспособность, средний и установленный Ту периоды стойкости проводят на вертикально-фрезерных станках, обрабатывающих центрах с ЧПУ с установленными для них нормами точности и жесткости на режимах обработки, указанных в таблице 3.
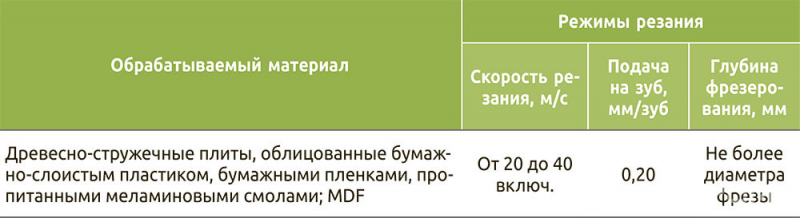
5.10. Приемочные значения среднего и установленного Ту периодов стойкости для выборки из трех фрез для обработки древесных материалов должны быть не менее указанных в таблице 4.
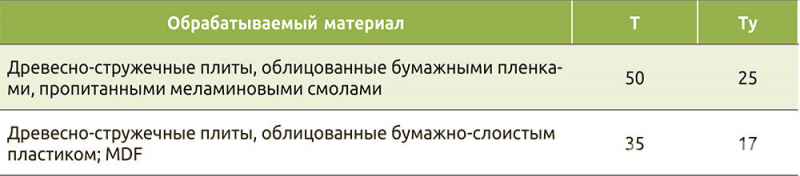
Для восстановления режущих свойств напайных фрез их затачивают на универсально-заточных станках. Режущие свойства фрез с многогранными и неперетачиваемыми твердосплавными пластинами восстанавливаются путем замены изношенных или сколотых пластин.
Качество заточки определяется соблюдением заданных геометрических параметров, радиальным биением режущих кромок, шероховатостью передней и задней заточенных поверхностей, заточкой режущего инструмента с СОЖ, отсутствием микротрещин на твердосплавных режущих элементах.
Для увеличения долговечности фрез нужно придерживаться следующих рекомендаций:
- выбирать режимы обработки заготовок в соответствии с возможностями оборудования и режущего инструмента;
- выполнять рекомендации производителей инструмента и оборудования;
- обеспечивать качественное охлаждение фрезы при заточке;
- использовать режущий инструмент правильной геометрии и в рекомендуемых режимах резания;
- обеспечивать качественный отвод стружки при фрезеровании.
На высокотехнологичных производствах могут также использоваться химические и термические способы повышения износостойкости инструмента: плазменное напыление различных карбидов, нанесение износостойких материалов, в том числе алмазоподобных, или качественная закалка режущих элементов фрез.
Текст Владимир Падерин