Группа «Илим». Завод в Коряжме: чище, больше, дешевле
В сентябре этого года в г. Коряжма Архангельской области группа «Илим» открыла завод по выпуску нейтрально-сульфитной полуцеллюлозы (НСПЦ). По данным группы, это самое крупное в мире производство, выпускающее такую продукцию.
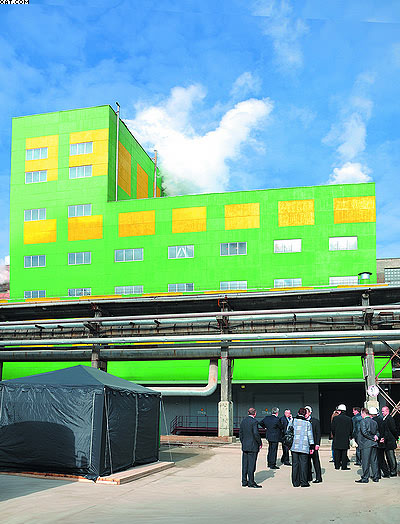
Ввод завода в эксплуатацию позволит решить имеющуюся проблему дефицита качественной полуцеллюлозы и увеличить выпуск тарного картона из низкосортной лиственной древесины, одновременно снизив расход леса и повысив производительность труда.
На другой уровень
Строительство нового завода по выпуску нейтрально-сульфитной полуцеллюлозы осуществлено в рамках разработанного в 2005 году инвестиционного проекта группы «Илим» стоимостью 10 млрд руб. Его целью была модернизация бывшего Котласского целлюлознобумажного комбината, входящего в бизнес единицу «Илим Запад», с тем чтобы повысить качество выпускаемой продукции, увеличить эффективность производства, добиться более глубокой переработки сырья и снизить экологическую нагрузку на окружающую среду. В ноябре 2008 года приказом Минпромторга России проект получил статус приоритетного инвестиционного проекта в области освоения лесов.
Компания ставила задачу в результате пятилетней модернизации нарастить выпуск наиболее перспективных и востребованных видов продукции. В частности, тарного картона, спрос на который до кризиса неуклонно рос на внутреннем и внешнем рынках. Одним из факторов, тормозивших увеличение выпуска картона в филиале группы «Илим», было состояние производства полуцеллюлозы в Коряжме. При изготовлении бумаги – основы для гофрирования, картона для наружных слоев гофроупаковки и флютинга в качестве полуфабриката используется композиция из сульфатной целлюлозы и нейтрально-сульфитной полуцеллюлозы (НСПЦ). Добавление последней позволяет снизить затраты на выпуск готовой продукции, сохраняя её потребительские качества. Для сравнения: при варке сульфатной целлюлозы на одну тонну продукции расходуется 4−5 м³ древесины, а на выработку одной тонны полуцеллюлозы в соответствии с современными технологиями – 2,6−2,8 м³.
До последнего времени этот полуфабрикат вырабатывался на производстве, функционирующем с 1964 года. Установленное на нем оборудование (два варочных аппарата «Пандия») по техническим характеристикам, а также вследствие морального и физического износа не удовлетворяло нужды филиала в полуцеллюлозе как по качественным, так и по количественным показателям. Две установки вырабатывали 430 т полуцеллюлозы в сутки, что не соответствовало растущим потребностям группы «Илим».
Руководство компании приняло решение о строительстве нового завода проектной мощностью 900 т полуцеллюлозы в сутки (или 310 тыс. т в год). Объем инвестиций в строительство нового завода НСПЦ составил 1,7 млрд руб.
Три плюса
Группа «Илим» провела тендер на право осуществления проекта строительства завода НСПЦ. Победителем конкурса, в котором участвовал ряд европейских компаний, стало шведское подразделение компании Metso – Metso Paper Sundsvall AB.
«Предложенное и осуществленное нашими партнерами технологическое решение имеет три ключевых достоинства. Первое – ориентация на использование низкосортной древесины лиственных пород. Удельный вес сырья этой категории при традиционной переработке был гораздо ниже, чем сейчас. Второе преимущество – экологичность. На новом производстве вообще нет выбросов и существенно снижены сбросы. Третье – это высокая производительность труда: управляет технологическим процессом, результат которого – выпуск 900 т полуфабриката в сутки, рабочая смена из трех человек», – говорит директор по GR группы «Илим» Дмитрий Чуйко.
По его словам, снижение затрат на сырье повышает конкурентоспособность конечной продукции. При этом качество полуцеллюлозы настолько высокое, что она резко улучшает качества флютинга, что очень важно в соревновании с другими участниками рынка.
Завод построен на основе наилучших существующих технологий, что позволяет снизить сбросы загрязняющих веществ по сравнению со старым производством на 15−20%. Атмосферные выбросы данного завода, кроме естественных выпаров, отсутствуют.
По данным группы «Илим», новое производство полуцеллюлозы по мощности не имеет аналогов не только в России, но и в мире. Сосед коряжемского предприятия, Архангельский ЦБК, запланировал в рамках программы модернизации производства строительство завода НСПЦ суточной производительностью 1000 т, но из-за мирового экономического кризиса отсрочил начало строительства, намеченное на 2009 год, как минимум на 12 месяцев.
Пошаговые решения
Апгрейд технологической цепочки в соответствии с бизнес-планом начался со строительства выпарной станции (объем инвестиций – около $40 млн), ввод которой в 2007 году позволил снять ограничения по упариванию и регенерации щелоков, создал условия для наращивания объемов производства, улучшил экологическую ситуацию в регионе. Это, в свою очередь, позволило включить в процесс новый завод НСПЦ, по мощности более чем в два раза превосходящий старое производство полуцеллюлозы. Но, в отличие от Архангельского ЦБК, при модернизации стартовавшего со строительства современного древесно-подготовительного цеха, «Илим» начал с модернизации транспортных систем подачи щепы и участка сортирования на древесноподготовительном производстве. Был переоснащен и участок приготовления и подачи моносульфита с увеличением его выработки.
План модернизации филиала группы «Илим» в Коряжме предусматривает строительство нового древесноподготовительного цеха, но точные сроки его ввода пока не называются. Группа не отказалась ни от одного проекта из плана модернизации коряжемского производства, но в связи с кризисом вынуждена увеличить сроки их осуществления.
Сюрпризы стройки
Генеральным проектировщиком завода было выбрано ЗАО «АРХГИПРО-БУМ» (г. Архангельск). Предварительный инжиниринг, проектирование, согласование и экспертиза проекта заняли более года. Строительные работы по возведению каркаса здания были начаты в июне 2008 года. Завод разместился на небольшой площадке, бок о бок со старым производством полуцеллюлозы, на тот момент ещё работавшем. Строители должны были действовать максимально осторожно, чтобы не повредить стоящие рядом производственные корпуса при забивке свай и возведении здания. Другой, более удобной площадки для застройки, кроме этого ограниченного пространства, на территории предприятия просто нет. «Если бы мы строили завод соответствующей производительности по традиционной технологии, то площадь понадобилась бы вдвое больше, – поясняет начальник отдела технического развития филиала группы „Илим“ в Коряжме Павел Кушмылев. – Но исходили из того, что есть, – Metso Paper адаптировала свой проект к заданным условиям, „вытянув“ завод по вертикали. Предстояло построить здание высотой 43,5 м, то есть почти с пятнадцатиэтажный дом. Давление, создаваемое массой оборудования на единицу площади, естественно, было значительным. Для обеспечения прочности фундамента были вбиты 474 десяти- и двенадцатиметровые сваи, тогда как при обычном строительстве на наших грунтах достаточно девятиметровых свай».
Генеральному проектировщику пришлось решать ещё одну нестандартную задачу. В Архангельской области не выпускаются готовые железобетонные конструкции заданных характеристик. Решение было принято необычное: возводить промышленное здание из монолитного железобетона. Подобного опыта в регионе ещё не было. Генерального подрядчика нашли в Северодвинске. Конкурс на выполнение работ выиграла компания «СпецФундаментСтрой», которая уже имела опыт строительства зданий из монолитного железобетона, правда жилых. Специальную опалубку пришлось заказывать в Германии.
Армирование конструкций, установка опалубки, бетонирование колонн и перекрытий выполнялись непосредственно на стройплощадке.
Монтаж оборудования также осуществлялся не по привычному сценарию. Вопреки обыкновению он шел параллельно со стройкой. Ограниченное пространство требовало виртуозного исполнения и слаженности. Подрядчикам на каждом этапе монтажа и строительства приходилось находить уникальные решения для установки оборудования и конструкций, поддерживающих опалубку выше расположенных отметок.
К лету 2009 года здание завода было уже полностью возведено, смонтировано оборудование, проложены внешние коммуникации, началась прокрутка оборудования вхолостую, на воде, со щепой.
Первую полуцеллюлозу на заводе получили день в день согласно утвержденному графику. Отставание от первоначальных планов реализации проекта, которые были отражены в бизнес-плане и составлялись ещё в 2005 году, на стадии согласования идеи строительства (на тот момент не было ни контракта на поставку основного оборудования, ни проекта, да и о кризисе не было речи), составило немногим более трех месяцев.
Сырьевой вопрос
Новое производство НСПЦ требует практически в два раза больше сырья, чем старое. Две «Пандии» выпускали 430 т полуцеллюлозы в сутки при норме расхода 2,7 м³ древесины на одну тонну продукции. Норма расхода сырья на новом заводе не намного ниже – 2,6 м³ на тонну, а объем производства вдвое выше. Уже сейчас завод вырабатывает до 900 т полуцеллюлозы в сутки.
При этом, как сказал директор по GR группы «Илим» Дмитрий Чуйко, затраты на закупку сырья снизились, так как новые технологии позволяют работать на самой низкосортной (и потому дешевой) осине и березе. Для лесоперерабатывающих предприятий Архангельской области подобный подход весьма актуален – в лесных запасах региона быстро растет доля лиственной древесины, качество которой при этом снижается.
Группа «Илим», вложившая в последние годы немало средств в развитие лесозаготовки, 43 % сырьевой потребности филиала в Коряжме обеспечивает собственными силами.
Технологическая цепочка
Схема технологического процесса коряжемского завода НСПЦ разработана Metso Paper Sundsvall AB. Для управления технологическим процессом используется оборудование австрийской фирмы Honeywell. Полная автоматизация позволяет управлять заводом с одного пульта.
Производство оснащено самой современной техникой. Основные узлы оборудования для коряжемского производства – рафинеры, промывное оборудование, варочный котел – изготовлены на заводах Metso в Германии, Швеции, Финляндии. Технологическая схема, безусловно, не уникальна – аналогичная используется на всех заводах по выпуску полуцеллюлозы, построенных Metso Paper. Но она полностью адаптирована к конкретным условиям, заданным группой «Илим» для своего производства: малой площади завода, породному составу сырья и т.д.
Смесь березы и осины в равном соотношении поставляется из цеха ДПЦ по системе транспортеров к приемным бункерам завода НСПЦ. Из двух бункеров она подается на ленточные транспортеры, где взвешивается с помощью автоматических весов. Результат суммируется и фиксируется на приборах пульта управления.
Взвешенная щепа размораживается и нагревается. Затем следует промывка, в ходе которой необходимо избавиться от посторонних примесей – частиц металла, камней, песка, которые могут повредить оборудование. В сепараторе загрязнений щепу медленно перемешивают в горячей воде, и камни и инородные частицы оказываются на дне. Одновременно щепа нагревается, что немаловажно для дальнейшего процесса.
Далее обезвоживание и пропарка щепы – промежуточный этап перед пропиткой. Пар подается в нижнюю и среднюю части бункера для прогрева щепы и устранения воздуха. Объем щепы определяется системой гаммадатчиков. Другой источник сведений для автоматической коррекции процесса – сигнал о скорости работы разгрузочного шнека бункера пропаривания. Так, если объем щепы в бункере зашкаливает, её подача прекращается.
Пропаренная щепа поступает в пропиточную камеру, которая примерно наполовину заполнена варочным щелоком. В качестве варочного щелока используется моносульфитный раствор (Na2CO3 + Na2SO3), который приготавливается из кальцинированной соды марки Б и технической газовой серы.
Пропитанная щелоком щепа поднимается вертикально по трубе, при этом избыточная жидкость сливается. В варочном котле она выдерживается в течение 20−30 мин при температуре 165−175°C. После этого щепа попадает в дефибратор в нижней части котла, где перерабатывается в волоконную массу. Оборудование позволяет, изменяя потребление энергии, регулировать размер производимого волокна.
Разделенная на волокна щепа проходит под давлением в циклон, где под воздействием центробежных сил удаляется пар, поступающий вместе с массой из варочного котла. Этот вторичный пар используется для подогрева щепы в пропарочном бункере и паровом смесителе.
Перемешанная в бассейне низкой концентрации масса подается в пресс TwinRoll, который обезвоживает массу с изменением содержания полезного вещества с 5 до 30 %. Через шнек¬разрыватель масса проходит к двум рафинерам второй ступени. В них она измельчается до заданной степени.
Размельченная и вновь разбавленная до концентрации 10 % масса перекачивается в баки вместимостью 370 м³ каждый, где хранится готовая полуцеллюлоза. Вырабатываемая в Коряжме полуцеллюлоза высокого выхода должна соответствовать следующим физико механическим показателям: разрывная длина – не менее 6300 м; сопротивление продавливанию – не менее 390 кПа; сопротивление раздиранию – не менее 820 мН.
Планы и перспективы
Первые пробные пуски нового производства были проведены в июле 2009 года – к этому моменту в Коряжме уже был сформирован штат сотрудников будущего завода. Из тех, кто трудился на прежнем производстве, отобрали 12 наиболее квалифицированных и перспективных специалистов, которые прошли дополнительное теоретическое и практическое обучение под руководством сотрудников компании Metso. Уровень автоматизации производства настолько высок, что технологическим процессом непосредственно управляет один человек, остальные работники смены осуществляют обход линейки оборудования и визуальный контроль его состояния.
На заводе планируется провести трехсуточные гарантийные испытания оборудования с целью достижения заданных качественных и количественных показателей вырабатываемой полуцеллюлозы. По словам начальника отдела технического развития завода Павла Кушмылева, сомнений в том, что они будут достигнуты, практически нет, так уже в период пусконаладочных и функциональных испытаний оборудования завод вырабатывал до 930 т высококачественной полуцеллюлозы в сутки. Сегодня эти мощности остаются в резерве.
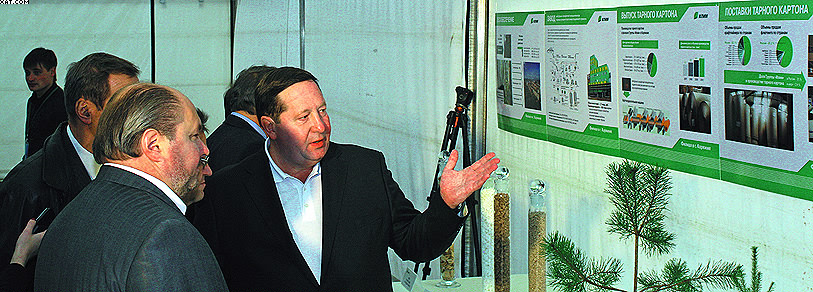
Последующая модернизация БДМ-1 (в 2010 году) с увеличением производительности по выработке флютинга, основным компонентом которого является полуцеллюлоза, модернизация БДМ-5 (в 2011 году) с целью перевода её с выпуска офсетных бумаг на производство флютинга позволят в полной мере использовать возможности нового завода. Кроме того, уже сегодня в композиции картона и флютинга, вырабатываемого на картонно-бумажном производстве, увеличена доля НСПЦ. В картоне «крафтлайнере» (плоском слое гофрокартона) долю полуцеллюлозы увеличили с 26 до 43 %, в композиции флютинга – с 74 до 80 %. При этом физико механические показатели продукции, её потребительские свойства значительно улучшились.
Благодаря предпринятым действиям в 2010 году планируется увеличить выпуск продукции картонной группы более чем на 56 тыс. т по сравнению с нынешним уровнем. Общий план производства этой продукции по филиалу в 2010 году должен составить 490 тыс. т. До 10 % производимого в Коряжме картона и флютинга группа «Илим» намерена перерабатывать в гофроупаковку на собственных предприятиях, а остальной объем поставлять на внутренний и внешний рынки.
Елена ДЕНИСЕНКО