Обслуживание и ремонт техники
Технологический ресурс, накопленный советскими мебельными предприятиями к концу 80‑х годов прошлого века, был полностью исчерпан уже к середине 1990‑х. Этому способствовали: неграмотно проведенная приватизация, крах экономики и полная дезорганизация управления предприятиями, в том числе связанная с ликвидацией министерств.
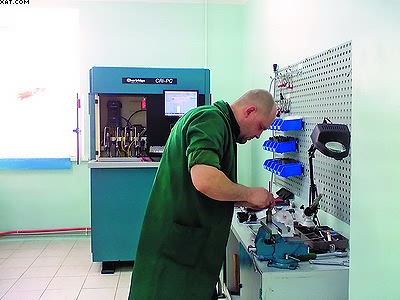
Но тогда же практически на пустом месте стали возникать новые мебельные производства, многие из которых начинали с круглопильного форматного станка, утюга для наклеивания кромочного пластика и дрели для сверления отверстий.
К концу 1990‑х многие из них встали на ноги и сумели обзавестись довольно сложным импортным технологическим оборудованием, включая обрабатывающие центры.
Отказы и запчасти
К сожалению, дороговизна кредитов и недостаток собственных средств не позволяли предприятиям оснащать производство комплектным оборудованием и заставляли почти всегда приобретать лишь самые простые и дешевые модели станков.
К концу 90‑х годов прошлого века у многих даже сформировалась своего рода философия: собственники старались интенсивно эксплуатировать дешевый станок, за пару лет довести его до износа, а потом просто выбросить и приобрести новый, такой же. Подобный подход позволял почти полностью отказаться от затрат на ремонт и постоянное обслуживание этих станков, ограничившись лишь приобретением дереворежущего инструмента и быстро изнашивающихся простейших запчастей, например приводных ремней.
Но с течением времени производительность предприятий стала увеличиваться, что потребовало использования все более сложного оборудования, частая замена которого слишком накладна. Одновременно оказалось, что кадровый ресурс, созданный еще в советские времена, исчерпан, а молодые кадры не обладают ни опытом, ни знаниями, необходимыми для работы на сложных станках и грамотного технического обслуживания оборудования.
В результате простои оборудования по причине внезапных отказов стали увеличиваться и приносить все более ощутимые убытки. Причем надо учитывать и то, что сроки поставок запчастей исчисляются месяцами, а их стоимость делает большие прорехи в экономике небольшого предприятия. В связи с этим многие руководители, наконец, пришли к мысли о необходимости заранее знать, какие запчасти могут потребоваться и какие суммы надо зарезервировать на их приобретение, и соответственно корректировать себестоимость производимой продукции.
Добрые советские времена
Еще в 1980-е, во времена жесткой плановой экономики, на любом достаточно крупном промышленном предприятии существовал отдел главного механика, в перечень обязанностей которого входила организация системы планово-предупредительного ремонта (ППР), регламентированная ГОСТом.
Система ППР предусматривала разработку годового графика проведения осмотров оборудования, его текущих, средних и капитальных ремонтов. Такой график с поквартальной и помесячной разбивкой, вычерченный на склеенных листах ватмана, был у каждого отвечающего за его выполнение механика. В соответствии с результатами предварительных периодических осмотров в качестве подготовки к проведению ремонтов заранее заказывались запчасти.
Достоинством системы ППР являлось то, что в рамках периодических осмотров оборудования производился и уход за ним, предусмотренный эксплуатационной документацией. При этом график ремонтов позволял руководителю предприятия заранее знать, когда и на какой срок будет остановлен тот или иной станок, что давало возможность соответствующим образом корректировать и план производства.
Но эта же плановость была и серьезным недостатком системы ППР: расчет сроков проведения ремонта осуществлялся в зависимости от некоей абстрактной группы технической сложности оборудования, не учитывавшей ни уровень его начального качества изготовления, ни сложность конструкции конкретной модели. Станок останавливался для ремонта принудительно, вне зависимости от его фактического технического состояния, что часто приводило к неоправданному увеличению затрат.
Соблюдение графика осмотров и профилактических ремонтов при наличии всех необходимых запчастей позволяло, однако, практически полностью исключить внезапные отказы большого числа оборудования.
Кто следит за станком?
На небольших отечественных деревообрабатывающих и мебельных предприятиях, где число единиц оборудования не превышает, к примеру, полутора десятков, содержать отдельную группу механиков для проведения профилактических осмотров и ремонтов просто невыгодно.
Но в современных сложных экономических условиях, когда из-за девальвации рубля стоимость оборудования увеличилась, а рынок продаж изделий из древесины и древесных материалов существенно сузился, приобретение новых станков стало еще более трудным делом, и задача сохранения работоспособности уже имеющегося оборудования является для предприятий едва ли не одной из главных.
На многих европейских предприятиях проблема обслуживания и ремонта несложных станков решается своими силами. Так, непосредственно на станочника возложены обязанности настройки и наладки станка, его смазки, определения состояния и замены дереворежущего инструмента, уборки станка после окончания работы. Станочник же в присутствии бригадира или мастера и при их непосредственном участии может устранить мелкие неисправности оборудования.
Как правило, за рубежом станочниками являются лица, окончившие учебные заведения, аналогичные по уровню российским колледжам (бывшим ПТУ), но отличающиеся от них тем, что учащимся дается лишь необходимый минимум теоретических знаний, а основное внимание уделяется практике работы на станках, включая обрабатывающие центры и оснащенные современными электронными системами, а также основам их программирования.
Такого уровня подготовки от нынешних отечественных учебных заведений трудно ожидать еще многие годы, и нашим предприятиям приходится применять обучение рабочих на местах, так называемым бригадным методом, хотя сегодня найти хорошо обученного специалиста, обладающего необходимыми знаниями, почти невозможно. Поэтому доверять нашим станочникам настройку и наладку станка, а тем более его осмотр для определения технического состояния и степени износа нельзя, вне зависимости от стажа их работы на этом оборудовании.
В любом случае рабочий должен хотя бы изучить инструкцию по эксплуатации, обязательно прилагаемую к каждому станку, и только тогда начинать работу, обеспечив контроль постоянного выполнения изложенных в ней требований. К сожалению, к инструкциям на наших предприятиях относятся весьма небрежно и подчас найти паспорт станка оказывается просто невозможно. А как раз в нем содержится каталог запасных частей с их названиями на языке производителя и номерами, необходимыми для заказа, о чем у нас вспоминают лишь в самый последний момент!
Кто ремонтирует станки?
Так кто же проводит осмотры? На небольших предприятиях это делает, как правило, технический руководитель производства, называемый и главным инженером, и техническим директором, а по сути выполняющий функции мастера цеха, на которого возлагается еще множество других обязанностей: технолога, контролера ОТК, дизайнера и т. д. Понятно, что пока станки работают нормально, их осмотры будут проводиться этим специалистом бессистемно. И только при возникновении серьезного отказа оборудования, будут приняты соответствующие меры. К тому же нет никакой уверенности, что сам этот технический специалист настолько универсален, что знает и механическую часть оборудования, и электрику, и электронику.
То есть во главу угла на предприятиях ставится не профилактика, а решение проблем по мере их возникновения. А такая практика, как и раньше, приводит к длительным остановкам производства в ожидании запчастей, отсутствию на счету средств на их оплату и к использованию разного рода «эрзац-деталей», в еще большей степени вредящих станку.
Конечно, для проведения профилактических осмотров можно поискать грамотного механика на других предприятиях — с тем чтобы он осуществлял их в свободное время, но вся беда в том, что и у соседей не бывает специалистов, хорошо знакомых не просто с оборудованием, а с наладкой и ремонтом сложных импортных деревообрабатывающих станков. К тому же никто не даст гарантии, что такой привлеченный со стороны специалист не нанесет вашему предприятию вреда, отнесшись к своей работе как к халтуре и выполняя ее с соответствующим качеством.
Есть и другой путь. Несколькими деревообрабатывающими и мебельными предприятиями, расположенными относительно недалеко друг от друга или входящими в состав какой-то региональной ассоциации, может быть на долевых началах организовано самостоятельное предприятие, задачей которого будет проведение осмотров их действующего оборудования, приобретение запчастей и ремонт с их использованием. Фактически такое предприятие может стать их общим отделом главного механика. Со временем такая финансово самостоятельная фирма укомплектуется квалифицированными специалистами и сможет расширяться и выполнять сторонние заказы, но важно, что она будет всегда подконтрольна своим основателям.
Есть еще одно решение
Но пока такого предприятия нет и в проекте, для обслуживания действующего оборудования и его ремонта могут быть привлечены и его поставщики. Дело в том, что в условиях экономического кризиса продажи станков у всех российских станкоторговых фирм резко упали. В результате у каждой из них простаивают имеющие огромный опыт высококлассные инженеры-наладчики, которые еще не так давно были заняты шефмонтажом, запуском, наладкой, гарантийным и постгарантийным обслуживанием поставленного оборудования.
Поэтому большинство таких предприятий сегодня перенацелили этих инженеров на обслуживание проданных ранее станков и автоматических линий.
Сегодня они с удовольствием заключают договоры с любым предприятием на своего рода абонентское обслуживание. В рамках соглашения может выполняться периодический осмотр всего парка оборудования или отдельных станков, включая их обследование с определением фактического технического состояния, подготовку перечня необходимых запчастей, ремонт с последующей отладкой. Кроме того, эти специалисты могут производить и обучение сотрудников предприятия правильной работе на станках, наладке, настройке, и ежесменному обслуживанию оборудования. Причем работы производятся такими специалистами, выезжающими на предприятия в любой точке страны, по заранее согласованному графику.
Конечно, все это обходится недешево, но, как сказал один французский король, «Париж стоит мессы»: содержание оборудования в порядке, профилактика и исключение случаев его внезапных отказов, на что, собственно, и нацелено обслуживание профессионалами, обеспечивает предприятию огромную экономию средств.
И все же, хотя такой способ обслуживания и профилактического ремонта станков в некотором смысле заменяет на производстве отдел главного механика, на предприятии должен быть человек, непосредственно отвечающий за работу станочного парка.
Что мы не сможем сделать никогда
Представьте, что вы ездите на своем автомобиле, в котором никогда не регулировали сход-развал (углы установки) передних колес. Значит, будьте готовы к тому, что автомобиль плохо будет «держать» дорогу (рыскать), его будет уводить в сторону, руль изменит положение при движении по прямой, при торможении его потянет в сторону, повысится износ резины и т. д. Но если вы всегда ездили на таком автомобиле и уже привыкли к тому, что для других водителей недопустимо, то и не задумываетесь над подобными проблемами, считая их нормой жизни.
То же самое относится и к станкам. Многие их недостатки, «не предусмотренные» конструкцией, появившиеся как бы сами собой и незаметные глазу, могут серьезно повлиять на качество работы. В основном это относится к нарушениям норм точности и взаимного расположения деталей станка, что приводит к биению шпинделей и фланцев пил, нежесткости, неплоскостности и непараллельности столов, непрямолинейности и неперпендикулярности направляющих и т. д. Для того чтобы проверить точность любого станка, нужно знать, что именно надо проверять, какими методами и с использованием каких инструментов и приспособлений.
В советские времена технические условия (ТУ) и паспорт каждого станка обязательно содержали эти сведения или ссылку на соответствующий ГОСТ.
Сегодня российские предприятия приобретают преимущественно импортное оборудование, в паспорте которого сведений о порядке проведения проверок и необходимой точности деталей и узлов просто не бывает!
Но даже если бы они и были, где небольшому деревообрабатывающему предприятию взять, скажем, трехметровую чугунную поверочную линейку (между прочим, весом полцентнера), индикатор часового типа, набор плоскопараллельных мер длины, метровый угольник и набор щупов?! Специалисту-наладчику, которого предприятие могло бы пригласить, тоже не привезти все это оснащение с собой. Да и какой бы высокий профессионал не ремонтировал станок, все равно у него получилась бы халтура, ведь в его распоряжении не было бы сведений, без которых о полноценном ремонте не может быть и речи.
Поэтому качество выполненного ремонта можно проверить, только оценив качество обработки деталей, что, впрочем, также требует наличия методик и поверочного инструмента. То же, кстати, касается и совсем нового оборудования: наши продавцы, несмотря на их громогласные заявления об обязательном проведении предпродажной подготовки каждого станка, вряд ли могут проверить его на соответствие нормам точности, поскольку у них нет ни самих нормативов, ни инструментария для проверки оборудования на соответствие им. А ведь скрытые дефекты оборудования при его эксплуатации могут проявлять себя так, что причину образования брака при обработке деталей без проверки станка на точность найти невозможно.
Говорят, пик мирового экономического кризиса пройден и настает эра восстановления народного хозяйства. Но есть и такие скептики в правительстве, которые предрекают новую волну кризиса. Поэтому о приобретении нового оборудования сейчас можно только думать, а на практике — бережно сохранять то, которое есть. А это означает правильно обслуживать его и вовремя ремонтировать, используя все имеющиеся возможности и приобретая оригинальные запчасти.
Владимир КОЛОМИЙЦЕВ