Производство древесного угля
Получение продуктов из древесины путем воздействия на нее высокой температуры относится к числу древнейших технологий в истории человечества. Археологические раскопки свидетельствуют о том, что еще пещерные люди знали древесный уголь.
Рис. 1. Систематизация углевыжигательного оборудования
Рис. 2. Изменение температуры в процессе пиролиза
Рис. 3. Конвективные потоки в вертикальном аппарате, обогреваемом снаружи
Рис. 4. Изменение скорости сушки во времени
Рисунки смотрите в PDF-версии журнала
Его собирали на пожарищах или делали специально, засыпая золой тлеющие головни, и, укрываясь в пещерах от непогоды, использовали затем как топливо, не вызывающее угара. Наверное, первый металл был выплавлен случайно, когда камни, которыми обложили очаг с горящими углями, оказались рудой. С начала бронзового века древесный уголь стал одной из основ развивающейся цивилизации. Кузнецы умели получать уголь для своих нужд уже в XV–XVI веках. До середины XIX века металлургия развивалась в значительной степени на основе древесного угля.
Фактически европейские страны, прежде всего Англия и Франция, лишились своих лесов, изведя их ради углежжения. На древесном угле поднялась и металлургия нашего «каменного пояса» − Урала.
Сегодня Бразилия первенствует в производстве высококачественного чугуна, используя древесный уголь в качестве восстановителя. Он применяется в десятках технологий и в разных областях жизни. Уникальная особенность древесного угля − отсутствие угарного газа в продуктах сгорания − сделала его предпочтительным во многих случаях видом бытового топлива. В своей предыдущей публикации автор уже указывал на тот факт, что в развитых странах в последние годы интенсивно растет использование древесного угля в сельском хозяйстве. С его применением специалисты связывают новую «зеленую революцию» − очередной прорыв в интенсификации производства сельскохозяйственной продукции.
Как делают древесный уголь?
Выбор технологии производства древесного угля должен основываться на прогнозировании конъюнктуры рынка и учете сырьевых факторов. Аппаратурное оформление разрабатывается на основе знания сущности протекающих процессов и экономического сравнения вариантов оборудования. В разных экономических условиях востребованы разные технологические решения. Здесь кроется ответ на вопрос: «почему при таком обилии конструкций углевыжигательного оборудования надо создавать новые?» Важный момент − требования, предъявляемые потребителями к продукту. Прежде единственным критерием качества угля в нашей стране был ГОСТ 7657−84, который определял требования к различным сортам угля. Этот ГОСТ составлен во времена, когда главными и почти единственными потребителями древесного угля были металлургия и производство активных углей. Сегодня более половины этого продукта используется в быту (например, для жарки шашлыков на природе).
Высокое содержание нелетучего углерода и низкая зольность древесного угля были необходимы потребляющей его промышленности. Основных потребителей устраивало высокое содержание мелкой фракции. Сейчас структура спроса и технологии изменились.
Для бытовых целей нужен уголь более крупный и содержащий достаточное количество летучих − он лучше разгорается.
Последним словом техники в углежжении на протяжении второй половины XX века была вертикальная реторта. Это действительно один из наиболее совершенных аппаратов для углежжения. Но вертикальные реторты создавались под промышленное потребление угля, и качество выпускаемой ими продукции не вполне соответствует бытовым требованиям. Можно привести и другие примеры, объясняющие необходимость разрабатывать новые конструктивные решения в меняющихся условиях.
Предлагаем вниманию читателей разработанную автором схему (рис. 1), которая уже завоевала популярность в СМИ и Интернете. Задача этой схемы − показать, что накопленный поколениями углежогов опыт позволяет выбрать вариант технического решения осознанно. Выбор перестает быть результатом озарения. Сегодня накоплено достаточно информации, чтобы иметь возможность грамотно рассчитать гидравлику и теплопередачу, массообменные процессы и разработать оборудование.
Отдельно следует рассмотреть проблему экологичности аппаратов углежжения. В журналах и газетах иногда утверждается, что процесс углежжения вообще не может быть экологически чистым. Не владеющие вопросом журналисты получают такую информацию от малокомпетентных производителей угля и распространяют через прессу. Владельцы и изготовители всевозможных «экологически грязных» аппаратов иногда приводят следующий довод: мол, испокон веку уголь делали в кучах, ямах, и ничего. Известно, однако, что мужики, обслуживавшие те кучи во времена Демидовых, умирали рано. Просто никто не выяснял, отчего умер тот или иной крепостной. Населенность территорий, где производился уголь, была в те времена несравнимо ниже нынешней. И вред, наносимый природе, был менее заметен. К тому же еще не была осознана связь между работой углежогов и гибелью окружающих лесов.
Процесс образования угля

Таблица 2. Баланс при содержании в угле 94% нелетучего углерода

Образование древесного угля − это отщепление от веществ, составляющих древесину, более низкомолекулярных соединений. В твердом остатке увеличивается концентрация углерода. С летучими компонентами удаляются кислород и водород, содержащиеся в веществах древесины. Но и углерод тоже. В составе летучей части содержание углерода ниже, чем в исходной древесине. В итоге твердый остаток пиролиза составляет около трети массы исходных дров, но содержит около половины углерода дров. Пример распределения элементов в исходной древесине и продуктах распада приведен в табл. 1. Данные приведены в пересчете на абсолютно сухую древесину. Такой в природе не бывает, но для расчетов удобно пользоваться этим понятием. Для расчета по фактической влажности достаточно добавить известную долю воды.
Пример из табл. 1 относится к глубине прокалки, в результате которой содержание нелетучего углерода в угле составляет 84% (27,2 х 100/32,4). Выход угля при этом − 32,4%. Уголь может содержать и 76, и 96% нелетучего углерода − это зависит от того, как долго и при какой температуре его прокаливают.
В табл. 2 приведен выход и состав угля и парогазов при прокалке, которая довела содержание нелетучего углерода в угле до 94%. Выход угля составляет при этом 24,7%.
При сопоставлении данных табл. 1 и 2 видно, как существенно (примерно на четверть) уменьшается выход угля при увеличении содержания нелетучего углерода. Из этого можно сделать вывод, что прокаливать уголь нужно только до степени, требующейся заказчику. Прокалка, приводящая к получению угля с более высоким содержанием нелетучего углерода, убыточна и из-за большей продолжительности процесса, и из-за снижения выхода угля. Выход угля немного повышается, если процесс протекает медленно. Однако встречающиеся иногда данные о выходе на уровне 60% − явное недоразумение. Продолжительность процесса разложения древесины с отщеплением летучих соединений и образованием углеродного остатка составляет обычно от нескольких секунд до нескольких минут. Длительность технологического процесса, исчисляющаяся часами, зависит исключительно от условий передачи тепла.
Образование угля под воздействием тепла − сложный процесс. Его стадии схематически показаны на рис. 2. Абсолютно сухой древесины практически не бывает. Влажная древесина должна высохнуть, прежде чем начнется ее разложение. Пока в ее поверхностных слоях имеется влага, температура древесины не может превышать 100 °С, то есть температуры кипения воды. Только когда наружные слои высохнут полностью, температура древесины начинает повышаться. Древесина состоит из нескольких компонентов, имеющих различный химический состав. Сначала, при температуре на поверхности куска примерно 180−200 °С, начинают разлагаться гемицеллюлозы, затем целлюлоза и потом лигнин. При температуре на поверхности до 280−290 °С идет только отщепление небольших звеньев, образующих газы и легкие жидкие продукты. Ближе к 300 °С начинается более бурный процесс распада, сопровождаемый выделением тепла (экзотерма). При этом температура древесины растет самопроизвольно, пока не выделится все тепло экзотермы. Следующий этап требует снова подвода внешнего тепла. Это прокалка угля. Рассмотрим главные этапы подробнее.
Нагрев
Нагрев − это подвод тепла к материалу. Существует много способов нагреть материал (индукция, тепловая радиация и т. д.), но при углежжении обычно применяется либо прямой нагрев горячим газовым потоком, протекающим через слой и омывающим поверхность отдельных кусков, либо косвенный нагрев через стенку аппарата. В последнем случае теплопередача менее эффективна.
Прямой нагрев. Сам по себе этот способ подвода тепла более эффективен, чем другие, однако сопряжен с некоторыми технологическими проблемами, о которых поговорим позже. Движение газа через слой не бывает равномерным по сечению. При вертикальном движении вверх поток у стенок всегда больше, чем через слой. У стенок всегда больше пустот, и поэтому меньше сопротивление потоку. Тепло от горячего газа − теплоносителя − холодным дровам передается через поверхность кусков. Чем мельче загруженный материал, тем больше удельная поверхность. Но тем меньше и размеры каналов − пустот между отдельными кусками. Если мы загрузим в аппарат опилки слоем, то фильтрация потока через них будет ничтожна. Поток пойдет вдоль стенок и проделает каналы в слое. Основная масса частиц омываться не будет. Наличие замкнутых пустот между частицами делает опилки плохим проводником тепла (неслучайно в сельской местности опилки часто подсыпают на зиму к нижним венцам домов для утепления). Теплопередача через слой из-за этого затруднена. Поэтому сушка и пиролиз опилок и других мелких материалов в слое неэффективны.
Есть особенности в распределении потока через слой в зависимости от ориентации аппарата, мест подвода и вывода теплоносителя, отношения высоты аппарата к длине. Следует учесть, что при невысокой скорости потока в пространстве аппарата образуются застойные зоны, обогреваемые хуже других участков.
Технологические проблемы, связанные с прямым нагревом. Сложно приготовить теплоноситель, не содержащий кислорода. Даже при сжигании природного газа для обеспечения полного сгорания необходим избыток воздуха. Остальные виды топлива требуют для нормального горения избыток воздуха больший, чем для природного газа. Поэтому в теплоносителе всегда есть кислород. Можно поставить дополнительную систему для улавливания кислорода из теплоносителя, но она усложняет технологию и создает дополнительный объект, подлежащий контролю и обслуживанию.
Когда теплоноситель, содержащий кислород, поступает в сушилку, возникает необходимость более серьезного контроля, так как подсохшая древесина в сушилке может загореться. Если теплоноситель с кислородом поступает внутрь аппаратов, где протекает пиролиз, то окисление части угля неизбежно. Поэтому выход угля в этом случае уменьшается. Жидкие и газообразные продукты распада древесины смешиваются с негорючими дымовыми газами; образующиеся газы имеют низкую теплотворную способность, и их сложно сжечь. Если и удастся сжечь их с подсветкой из более калорийного топлива, то тепловой КПД будет низким, так как газы разбавлены. Для обратной подачи продуктов горения в пиролизную камеру нужно использовать горячий дымосос, он должен быть сделан из кислостойкого металла, так как возможно попадание в него кислот из продуктов распада. Еще одна сложность: в газе-теплоносителе остаются дурнопахнущие вещества, и уголь имеет неприятный запах. Чтобы избавиться от него, нужно зону охлаждения угля выделить в самостоятельный цикл и охлаждение осуществлять отдельным газовым потоком, не содержащим пахучих компонентов.
Нагрев через стенку. В углежжении распространен наружный обогрев встроенных в нагревательные устройства (печи, топки) сосудов, где протекают сушка и пиролиз. Тепло подводится к стенкам этих сосудов чаще всего газовым потоком теплоносителя, иногда прямой радиацией от горящего топлива и раскаленных стенок топки.
При этом в первую очередь нагреваются стенки сосуда. Нагретые газы начинают подниматься вверх вдоль стенок и, остывая за счет передачи тепла материалу, по внутренней зоне опускаются вниз. Образуются циклические потоки, как показано на рис. 3. В горизонтально расположенном аппарате такие потоки играют меньшую роль.
Сушка
Перед пиролизом необходимо подсушить дрова. Процесс сушки любого кускового материала состоит из нескольких периодов (рис. 4). Пока влажность высока, скорость процесса определяется возможностью отвести влагу от поверхности и вывести из аппарата. Это период постоянной скорости сушки (I).
Скорость зависит от состояния газовой среды. Чем выше температура, а также чем быстрее выносится влага с поверхности материала, тем выше скорость сушки. По мере уменьшения влажности падает и скорость движения влаги внутри куска.
Наступает момент, когда влаги к поверхности поступает меньше, чем среда могла бы отвести − начинается период убывающей скорости сушки (II). Влаги к поверхности в каждое следующее мгновение поступает все меньше. Когда фронт влаги отступает внутрь куска, поверхность материала начинает нагреваться до температуры выше температуры кипения воды. Между тем внутри куска температура по-прежнему не превышает 100 °С. Поэтому нередко на поверхности куска идет пиролиз, а внутри − еще сушка. Когда большая часть свободной влаги удалена, скорость сушки начинает резко падать − это период удаления капиллярной влаги (III).
Влага в древесине распределяется в крупных и мелких порах, в полостях клеток. Часть мелких пор способна перекрываться при понижении влажности. Такой механизм защищает живое растение от полного пересыхания, но и затрудняет удаление остаточной влаги из древесины. Точка перегиба между периодами I и II называется первой критической точкой. И скорость сушки в периоде I, и время наступления периода II от начала сушки зависят от температуры и режима движения газового теплоносителя, окружающего древесину. Если сушка осуществляется теплоносителем, имеющим температуру не выше 100 °С (как это делается при сушке пиломатериалов), то имеет значение еще и влагосодержание теплоносителя.
Но при сушке дров обычно используются более высокие температуры. Второй критической точкой называют переход от периода II к периоду III. Практически сушка в периоде III протекает чрезвычайно медленно. Для практических целей можно считать, что она прекращается.
Нельзя указать точное положение критических точек. Их координаты зависят от внешних факторов и структурных особенностей древесины. Большинство исследователей находят в разных условиях положение первой критической точки соответствующим влажности от 25 до 35% отн., второй критической точки − от 8 до 12% отн.
Отсюда следует, что увеличение продолжительности сушки сверх времени, необходимого для приближения к первой критической точке, чаще всего экономически невыгодно, так как удаление каждого следующего процента влаги требует больше времени, чем удаление предыдущего.
Размер куска играет большую роль при сушке. Чем меньше кусок, тем больше открытых поверхностей приходится на единицу массы и тем быстрее идет сушка. Но это при условии, что слой материала равномерно продувается потоком.
Опилки создают потоку сопротивление, образуют закрытые пустоты между частицами и потому в слое сохнут хуже, чем крупные куски. Структурные особенности древесины обуславливают неодинаковые условия движения влаги изнутри к поверхности в направлениях вдоль и поперек ствола: круглый неокоренный ствол даже небольшого диаметра сохнет много хуже, чем более толстое колотое полено.
Прежде была принята технология, по которой колотые дрова, сложенные в поленницы, хранились на бирже в течение летних месяцев для естественной просушки. Штабелирование велось вручную, по определенным правилам, с прокладками, что обеспечивало хорошее проветривание. Сверху штабель накрывался корьем. В сухую погоду дрова достигали воздушно-сухого состояния (25−28% влаги) за первые недели. Такой способ в современных условиях убыточен, так как на долгий срок выводятся из оборота средства, потраченные на заготовку и хранение, требуются большие площади. От этой практики отказались повсеместно. Ручная укладка не окупается. Есть удачный опыт сушки в кучах на решетчатых подставках. В любом случае укладка дров на сушку, а затем отбор их для подачи на переработку − это дополнительное затратное звено. К тому же хранение дров в современных финансовых ситуациях означает снижение темпов использования оборотных средств. По-этому оптимальна искусственная сушка.
Как уже упоминалось, скорость сушки зависит от температуры теплоносителя. Но сушка − это не просто процесс удаления влаги. При сушке изменяется и структура древесины. Если сушка интенсивна (что бывает при высокой температуре теплоносителя), одновременно образуется много паров. В куске развивается давление тем большее, чем он крупнее и выше температура нагрева. Этим давлением рвет древесину.
Уголь потом получится мелкий и трещиноватый. Напротив, медленный нагрев, процесс, продолжающийся несколько суток с постепенным медленным повышением температуры, позволяет получить отлично выжженный уголь без трещин. Именно поэтому некоторые примитивные технологии от кучного углежжения до использования печей, принятых в Юго-Восточной Азии, дают уголь хорошего качества. Соблюсти эти условия можно в любых печах, а не только в традиционных азиатских. В литературе встречаются ссылки на некую особенность азиатских печей, являющихся единственно возможными для получения особо качественных углей, однако не следует доверять распространителям этих идей. Они либо ограничены в представлениях о процессе, либо сознательно дезинформируют читателей ради продвижения «своей» технологии.
Эти «экологически грязные» и расходные печи позволяют получить хороший уголь из-за сильной затянутости процесса. Но такие условия можно воспроизвести и в любых других аппаратах. Только экономические причины (низкая удельная производительность) не позволяют распространять подобный режим повсеместно.
Выбор технологии углежжения
параметрами, разрешенными законодательством ЕС)
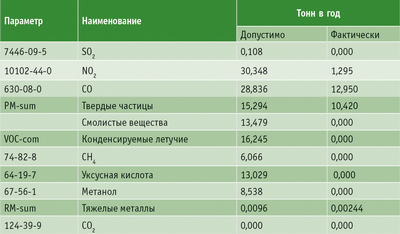
Стоячая куча − один из самых ранних, примитивных способов получения древесного угля. Ее продолжают использовать в слаборазвитых странах. И у нас некоторые российские предприниматели пытаются прибегать к этой технологии, невзирая на вред для работников и природы. Обслуживание такой кучи − еще и опасная работа, сопряженная с риском погибнуть в процессе так называемого кормления кучи − добавления дров в ходе углежжения.
Не только в России, но и в некоторых других странах, в том числе европейских, получили распространение «экологически грязные» аппараты в виде горизонтальных и вертикальных бочек с присоединенной топкой. Во всех этих установках горячие дымовые газы, содержащие много кислорода, поступают внутрь аппарата, заполненного дровами. Происходит разложение в токе газа. Кислород теплоносителя сжигает и часть парогазов, и уголь. Особенно много угля теряется на последних стадиях процесса. Помимо того что эти аппараты неэкологичны, они дают пониженный выход угля из-за сгорания его части. Отчасти уголь получается мелким и растрескавшимся, так как на стадии сушки создаются повышенные температуры и пар, выходящий из древесины, рвет кусок. В таких печах более 70% от исходной массы древесины выбрасывается в окружающую среду. Выбросы содержат фенолы, кислоты, спирты, смолы, альдегиды, кетоны и другие вещества, отравляющие людей и природу. Деревья вблизи этих установок засыхают, а люди наживают легочные заболевания.
Особо надо сказать о ситуации на Дальнем Востоке. Китайское правительство запретило кустарное производство угля в Китае, и тамошние кустари действуют теперь на российской территории. Они приходят нелегально и работают при попустительстве местных администраций, хищнически уничтожают реликтовые леса (железный дуб) и делают невыносимой жизнь в прилегающих населенных пунктах. Число постоянных жителей Приморья ежегодно уменьшается на 16−20 тыс. человек, зато на эти территории ежегодно въезжает более 320 тыс. иностранных граждан, 75% из которых − китайцы. Они получают уголь привычными для них способами. Надо ли говорить, что пришельцы не озабочены сохранением российской природы…
Для создания действительно экологически чистого углевыжигательного оборудования необходимо придерживаться следующих принципов:
- Сырьем для него должна служить древесина (остатки лесозаготовок, отходы деревообрабатывающих и мебельных производств), которая не годится для переработки или использования в других целях.
- Технология безоговорочно должна быть экологически чистой.
- В ХХ веке жидкие продукты распада древесины пользовались более высоким спросом, чем уголь. В последней четверти века появились продукты органического синтеза − более дешевые и более качественные. Спрос на жидкие продукты пиролиза древесины упал до нуля. Необходимо исключить и выброс продуктов распада в окружающую среду.
- Тепло, выделяющееся при сжигании летучих продуктов, должно быть использовано для покрытия потребностей процесса углежжения.
- В СССР большие лесохимические заводы потребляли сырье, доставляемое издалека. Тогда это было возможно, поскольку для них существовали специальные низкие транспортные тарифы.
Необходимо выбирать оборудование такой мощности, которая позволяла бы длительное время обеспечивать установки сырьем при радиусе доставки не более 50−80 км. - Установки будут обслуживаться персоналом невысокой квалификации. Это повышает требования к их устойчивости и работоспособности.
- В установках должна быть возможность нестабильной подачи энергии.
Такие задачи во главу угла поставили перед собой петербургские специалисты, приступая в 1992 году к созданию экологически чистого углевыжигательного оборудования. В 1997 году была создана и запущена первая установка нового типа «Поликор-1».
Опыт работы этой установки позволил сделать следующие шаги. Построены и работают «Поликор-2» и «Поликор-3». Сейчас заказчикам предлагаются установки серий «Эколон», «Корвет» и «Луч». В основе их технологического решения лежит использование помещаемых в обогреваемую камеру вертикально реторт, закрытых сверху и имеющих внизу отверстия для выхода паров и газов, которые отводятся прямо в топку, где сгорают все компоненты. Продукты горения омывают реторты в пиролизной камере. Затем горячие газы проходят через камеру сушки. Такое решение позволяет использовать топливо эффективно.
Площадь, на которой располагаются печь и вспомогательное оборудование, не превышает 0,5 га. Анализы подтвердили, что «Эколон» − экологически чистый аппарат. Производительность печи «Корвет», которая представляет собой уменьшенную копию «Эколона», − 1,5 т угля в сутки, печи «Луч» − 1−1,6 т в сутки. Одна из последних разработок − уголь из древесных опилок. Опилки предварительно брикетируются на экструдерном прессе, полученные брикеты подвергаются пиролизу.
В результате промышленного эксперимента на действующей углевыжигательной установке «Эколон», в ходе которого переработано 60 т брикетов из хвойных опилок, получено около 20 т угольных брикетов. Брикеты обладают большей прочностью, чем самый качественный древесный уголь, и высокой теплотворной способностью. Нами выявлены режимные особенности, вытекающие из свойств брикетов. Теперь технология известна и можно развивать это производство. Но покупатель пока незнаком с таким углем, а соотвественно, нет достаточного спроса.
Зато активный спрос на такие брикеты наблюдается в Японии, где их ценят выше, чем кусковой уголь из твердых пород. Охотно покупают это топливо в южной Европе. Основные производители брикетов − страны Юго-Восточной Азии, где их делают из опилок тропических твердых пород.
Исследования показали, что брикеты, изготовленные из опилок хвойных пород, ни в чем им не проигрывают, кроме того, был сделан важный вывод о пригодности углевыжигательных печей с выемными ретортами для такого производства.
Опровергнуто бытующее в ряде стран и распространенное среди потребителей и производителей такого угля мнение, будто только традиционная технология Юго-Восточной Азии пригодна для такого производства. Аппараты с выемными ретортами получили значительное распространение в последние годы.
Надо сказать, что применение таких аппаратов при всех их достоинствах ограниченно. Увеличить их производительность более чем до 2 тыс. т угля в год затруднительно по ряду технологических и организационных причин.
Оборудование этого типа плохо поддается автоматизации, его работа зависит от рациональной организации работы и добросовестности исполнителей. Поэтому мы начали разработку нового типа углевыжигательного аппарата, в большей мере соответствующего требованиям времени.
Юрий ЮДКЕВИЧ, канд. техн. наук,
гл. специалист отдела «Биоэнергия»
ЗАО «Лонас-Технология» (концерн AF)