На старом оборудовании далеко не уедешь, или что ожидает российское лесопиление?
Бравурные доклады российских чиновников о продолжающемся и ни на минуту не останавливающемся росте производства в российском лесопилении могут свидетельствовать о чем угодно, но только не о коренном переломе в отрасли. Рост, которого добиваются ЛДК и лесозаводы, является, скорее, не следствием грамотного руководства отраслью в целом, а следствием самоотверженности тружеников отрасли и грамотных управленческих решений на местах.
Положение России на мировом рынке пилопродукции
Ежегодно в мире производится около 400 млн м3 пиломатериалов различных сортов и сортировки. До середины 1980‑х годов СССР занимал лидирующие позиции в производстве этого вида продукции: в нашей стране производилось до 80 млн м3 пилопродукции ежегодно. Сегодня соотношение стран-лидеров лесопиления изменилось.
Наибольшая доля производства пиломатериалов приходится на США (в 2004 году там было произведено 87,5 млн м3), Канаду (60,6 млн м3), Россию (21,5 млн м3), Бразилию (21,5 млн м3) и Германию (19,5 млн м3). Таким образом, наша страна потеряла лидирующие позиции в лесопилении, и сегодня на ее долю приходятся лишь 5,5% мирового производства пиломатериалов. С большой долей уверенности можно предположить, что с каждым годом эта доля будет сокращаться, поскольку темпы роста производства пиломатериалов в России отстают от общемировых.
Так, за последние пять лет объем производства пиломатериалов в России вырос на 6,7%, в то время как в мире этот рост составил 7,8%. И такая тенденция сохраняется. Если же брать более длительный промежуток времени — с 1992 года,-то эти цифры и вовсе выглядят удручающе для России. С начала либеральных экономических реформ объем производства в лесопильной промышленности упал почти в 2,5 раза, а в мире увеличился на 1,5%.
Однако при этом в России наблюдается рост экспорта продукции лесопиления. Так, в 2004 году за рубеж отправлено 12,6 млн м3 пиломатериалов, тогда как в 1985 году — лишь 7,6 млн м3, а в 1992 году — 2,8 млн м3. Это свидетельствует не только об увеличении спроса на российские пиломатериалы, но и о все большей зависимости российских лесопильных предприятий от ситуации на внешних рынках и курсов основных валют.
Крупнейшими импортерами российских пиломатериалов являются: Япония — 750 000 м3, Великобритания и Египет — по 700 000 м3, Китай — 650 000 м3, Голландия и Германия — по 500 000 м3 в год.
Сегодня возвращению утраченных позиций препятствуют несколько факторов. В первую очередь отсутствие современного и значительный износ действующего оборудования, а также нехватка инвестиций в лесопиление. Как внутренних, так и внешних.
А что с технологиями?
В инвентаризационном отчете за 1995 год шведский Институт изучения лесоматериалов опубликовал рисунки трех лесозаводов Швеции, характеризующих состояние и развитие лесопильной отрасли в этой скандинавской стране в 1700‑х, 1950‑х и 1990‑х годах. Этот рисунок я приведу и в своей публикации. Понятно, что фотография 1990‑х годов соответствует сегодняшнему состоянию лесопильных предприятий в Швеции, а на фотографии 1950‑х годов каждый российский лесопильщик узнает любой крупный отечественный лесозавод или ЛДК, на которых до сих пор доминируют «лесорамы-восьмерки». Еще 30 лет назад руководитель крупнейшего лесоэкспортного объединения страны «Северолесоэкспорт» Валентин Парменович Самарин заявлял, что «в лесопилении мы отстаем на 25 лет», после этого такие же громкие заявления делал и министр лесной и деревообрабатывающей промышленности Николай Тимофеев. С тех пор никаких серьезных изменений в технологиях сделано не было. Ни в советское, ни тем более в постсоветское время. В результате сегодня можно смело говорить об отсталости лесопильной отрасли России от мировой минимум на 50 лет.
Большинство российских лесозаводов оборудовано лесорамами, от производства которых за рубежом отказались еще 15−20 лет назад. Более того, ведущие лесопромышленные державы отказываются и от их использования. В доказательство этого приведу табличку, отображающую изменение числа крупных лесозаводов России и Швеции, оснащенных лесопильными рамами, с 1973 по 2002 годы. В России число таких лесозаводов стабильно (108), да и за три последних года изменилось незначительно. В Швеции количество «рамных» лесозаводов за 30 лет сократилось почти в 70 раз — с 279 до 4. По мнению специалистов, рамное лесопиление является наиболее затратным способом распиловки древесины как с энергетической (большой расход электрической и тепловой энергии), так и с сырьевой точек зрения (большое количество получающихся отходов, низкий выход пиломатериалов).
Безусловно, вопросы обновления и модернизации лесопильного оборудования регулярно поднимаются и находят понимание на всех уровнях — от курилок лесозаводов и кабинетов генеральных директоров до администрации президента. И все вроде бы знают, что нужно делать: предоставить льготы предприятиям, обновляющим технологии; поддерживать отечественную науку в ее разработках современных лесопильных станков и целых линий и т. п. Однако решение проблемы сдерживается не всегда грамотной политикой властей. В частности, в сфере таможенных отношений. Кроме того, свою негативную роль играет практически полное разрушение системы отраслевых НИИ. В стране нет, пожалуй, ни одного стабильно функционирующего НИИ. Более того, многие из них находятся в предбанкротном состоянии. Таким образом, отечественное лесопиление лишено российских разработок оборудования, а западные технологии, «благодаря» таможенной политике государства, становятся очень дорогими для российских предприятий.
оснащенных лесопильными
рамами в России и Швеции, шт.
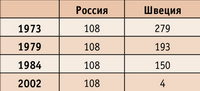
Впрочем, нельзя говорить, что в России не пытались создать собственные современные лесопильные станки. В конце 1970‑х — начале 1980‑х годов, когда и в Минлеспроме осознали бесперспективность рамного лесопиления, во многих отраслевых НИИ предпринимались попытки разработать отечественные ленточнопильные и фрезерные станки. Среди них ВНИИДМаш, ЦНИИМОД, ЦНИИМЭ, ЦНИИФ, ВНИИДрев, Гипродревпром, Гипродрев, СибНИИЛП, СвердНИИЛП, СевНИИП и многие другие. Проектировщиками предпринимались попытки скопировать существовавшие тогда зарубежные лесопильные станки, а также предложить оригинальные варианты лесопильных станков.
Так, директор Центрального научно-исследовательского института механической обработки древесины (ЦНИИМОД), конструктор Александр Грачев в начале 1980‑х годов предложил свой вариант ленточнопильной линии. Эта комплектная линия для распиловки бревен испытывалась на Архангельском ЛДК № 1 и на лесозаводе на Невской дубровке в Ленинграде в 1985−1987 годах, однако ее дальнейшая судьба неизвестна.
Внимание новым разработкам уделяли и серьезные научные издания. После публикации шведские ученые высоко оценили идеи, заложенные в оригинальном «грачевском» ленточнопильном станке. На его основе можно было создать свой конкурентоспособный станок, однако этого не произошло. Не произошло, прежде всего, потому, что в отечественной науке были сильны позиции сторонников традиционного варианта лесопиления — рамного. И в результате, когда Александр Грачев перешел на работу в Ленинградскую лесотехническую академию, направление ленточного лесопиления в ЦНИИМОДе «благополучно» свернули. ЦНИИМОД стал вновь заниматься изучением бесперспективного по большому счету рамного лесопиления. В результате к моменту либерализации экономики ЦНИИМОД подошел неподготовленным и, как следствие, долгое время с трудом сводил концы с концами. В 2003 году собственником ЦНИИМОДа стала фирма по торговле недвижимостью. С тех пор о ЦНИИМОДе практически ничего не слышно — здание института превратилось в офисный центр. Аналогичная картина произошла и с СевНИИПом (Северный научно-исследовательский институт промышленности), в котором научная составляющая деятельности отошла на десятый план, а главной целью института стало получение прибыли от сдачи помещений в аренду. Аналогичную картину можно наблюдать практически во всех отраслевых НИИ.
В результате сегодня отечественные производители не могут предложить конкурентоспособных станков, и, как следствие, российские лесопильщики все больше внимания уделяют зарубежным производителям.
Модернизация идет. Без плана
Пересчитать по пальцам двух рук все крупные российские лесопильные предприятия, которые модернизировали не только оборудование, но и технологии лесопиления, несложно. Таких предприятий не более десятка. Однако о какой-то системности подобной модернизации и наличии целевой программы речи не идет.
Так, например, модернизация лесопильного цеха на Онежском ЛДК стала не следствием продуманной перспективной программы, а следствием пожара, уничтожившего весь лесопильный цех. И чтобы не закрывать предприятие (ведь наименование «Онежский ЛДК» является уже достаточно «раскрученным» и авторитетным брендом в Европе), петербургская промышленная группа «Орими» была вынуждена строить новый лесопильный цех, оборудованный современными станками и линиями сортировки. Четыре года назад, когда цех пускался в эксплуатацию, его по праву называли лучшим в России. Тогда он был единственным в своем роде.
Российские предприятия неохотно вкладывают средства в развитие производства. Причина — крайне неблагоприятный климат для отечественных инвесторов. Иностранцам предоставляются налоговые льготы, оказывается всемерная поддержка, а вот российские предприятия подобного отношения лишены. В частности, при начислении НДС зарубежные компании освобождены от уплаты налога, российские же платят его в полном объеме.
Кроме того, производственная база большинства деревообрабатывающих предприятий устарела. И многие западные инвесторы предпочитают не покупать существующее лесоперерабатывающее предприятие (пусть даже и крупнейшее в стране или Европе), а строить новое «с нуля». Тем более что по сравнению с ЦБК затраты на строительство лесопильного производства в десятки раз меньше. Инвесторы «убивают сразу двух зайцев»: им не надо платить за устаревшее оборудование, а потом тратиться на его модернизацию. Пока строительство «с нуля» дороже, чем приобретение существующих предприятий, но скоро наступит такой момент, когда это будет наиболее оптимальным путем вхождения в лесопильную промышленность.
Кроме того, изношенность основных фондов лесопромышленных предприятий России, которая составляет свыше 60%, заметно уменьшает возможную выручку от продажи российской пилопродукции. Западные партнеры не желают платить высокую цену за пиломатериалы, выпущенные на лесорамах образца середины прошлого века. Либо цена, за которую они готовы их приобретать, ниже уровня рентабельности предприятий отрасли.
В качестве наиболее яркого примера отношения бизнеса и государства при модернизации лесопильных технологий приведу опыт строительства нового лесопильного цеха на архангельском Лесозаводе 25. Пожалуй, впервые в отечественной истории российский лесозавод сумел самостоятельно поднять производство до европейского уровня: здесь в августе 2004 года была пущена в эксплуатацию лесопильная линия, укомплектованная новейшим оборудованием ведущих мировых производителей Linck, Valon Kone, Lekops, Vollmer и Hekotek. Мощность лесопильной линии по распиливаемому сырью составляет 400 000 м3, или 200 000 м3 пиломатериалов в год. Объем инвестиций в реконструкцию лесопильного производства составил более 15 млн евро. Сумма очень внушительная для российского леспрома.
Аналогичных архангельскому заводов в России не так много — менее десяти, причем большинство построены за счет иностранных инвесторов, в частности скандинавских концернов Stora Enso и UPM.
На Лесозаводе 25 (входит в группу компаний «Титан») не планировали экономить на качестве, подбирали наиболее оптимальные сочетания станков и вспомогательного оборудования. Подсчитав, получили, что общая стоимость лесопильного цеха (оборудование, здание цеха, монтажные работы) составляет около 12 млн евро. Однако затем в дело вступило государство и предприятие заплатило свыше 2 млн евро НДС и около 1,5 млн евро таможенных пошлин. Таким образом, 3,5 млн евро предприятие было вынуждено дополнительно изыскать помимо стоимости оборудования. Так, о каком желании модернизировать лесопильные технологии может идти речь, если инвестиции, вкладываемые в развитие производства нашими предприятиями, облагаются такими налогами и пошлинами?!
Однако сегодня и в руководстве страны, и в умах лесопромышленников созрела мысль о том, что только ввод в строй подобных линий — единственный шанс для россиян сохранить свои позиции на мировых рынках в конкурентной борьбе со скандинавскими и прибалтийскими производителями. Поэтому предприятия берут кредиты, ищут тех, кто может за них поручиться, затягивают потуже ремни и работают на перспективу, надеясь, что в будущем все вложения окупятся сторицей.
Да и государственные органы стали «шевелиться» чуточку активнее. Недавно правительством было принято решение об установлении 0%-й импортной таможенной пошлины на некоторое деревообрабатывающее и мебельное оборудование. Однако такой размер пошлины установлен лишь на 9 месяцев. Неужели в правительстве полагают, что за столь короткий промежуток времени предприятия успеют обновить свои технологии?
Где взять деньги на модернизацию?
экспорта пиломатериалов
с 1985 по 2004 годы, млн м
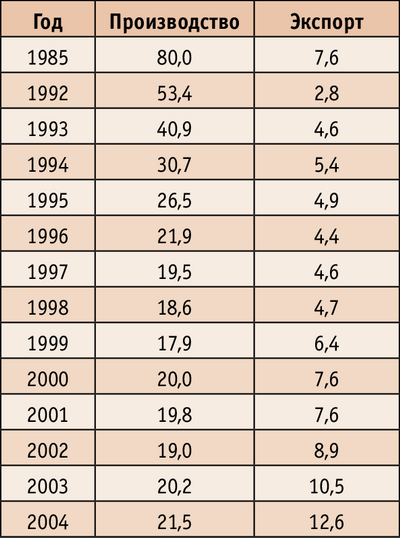
Вполне естественно, что на модернизацию лесопильного оборудования нужны деньги. И деньги немалые. Даже для крупного предприятия, каким является 25-й лесозавод, сумма в 15 млн евро — деньги более чем внушительные. Такими собственными средствами обладают лишь крупные вертикально интегрированные холдинги и компании нефтяной и газовой отрасли, которые, в свою очередь, не спешат вкладывать деньги в развитие лесной промышленности. Более того, они все активнее избавляются от «непрофильных активов» в других отраслях, в том числе и в деревообрабатывающей.
По мнению экспертов инвестиционных компаний, для стабильного развития отрасли ежегодно в российский ЛПК необходимо привлекать не менее $2−3 млрд. Фактически же в 2004 году, по данным Рослесхоза, в лесную отрасль поступило менее $1 млрд иностранных инвестиций при их общем объеме в экономику России на уровне $40,5 млрд. Для сравнения: годовые продажи продукции всех предприятий лесной отрасли России оцениваются в $10 млрд. Таким образом, сегодня внутри отрасли найти ресурсы для модернизации не представляется возможным. Необходимо искать другие варианты привлечения средств.
Столь высокий уровень необходимых иностранных инвестиций обусловлен, прежде всего, тем, что износ основных фондов весьма велик: в некоторых отраслях ЛПК он достигает в среднем 80% (в лесопилении — 60%). Привлечение внутренних кредитов ограничено их дороговизной: ставки по кредитам достигают 20%, и лишь в лучших случаях предприятиям (давним и надежным партнерам Сбербанка) удается договориться о процентных ставках в размере 10−12% на очень короткий срок. Однако эти деньги не «длинные»: максимальный срок возврата кредита — 5 лет, а срок окупаемости проектов в лесопромышленном комплексе (особенно дорогостоящих — в ЦБП) редко бывает меньше 7−10 лет. Таким образом, предприятие платит практически двойную стоимость оборудования.
в России
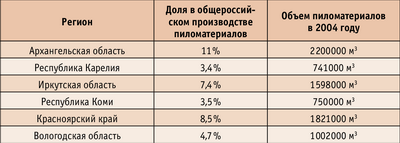
Зарубежные инвесторы не спешат вкладывать деньги в развитие ЛПК России. Почему? Ответов на этот вопрос может быть множество, но главным из них на сегодня является непонятная ситуация с принятием Лесного кодекса, который правительство и Госдума не могут довести до ума уже в течение четырех лет. Кто будет собственником лесных ресурсов? Когда наше государство ответит на этот непростой вопрос, ситуация с инвестициями чуточку прояснится. Кроме того, низкая инвестиционная активность западных инвесторов обусловлена следующими причинами.
1. Как правило, лесфонд предоставляется в аренду, максимум, на 3−5 лет, в лучших случаях — на 49 лет. Для вновь образованных лесозаготовительных предприятий и предпринимателей такие маленькие сроки аренды оптимальны, поскольку эти предприятия очень мобильны и могут организовать лесозаготовку практически в любом районе. Кроме того, они не обременены дополнительными социальными нагрузками. Крупные леспромхозы с богатой историей, образованные после акционирования госпредприятий в начале-середине 90‑х годов, на плечах которых лежит и социальная сфера построенных вокруг них лесных поселков, наоборот, заинтересованы в длительных сроках аренды лесфонда, поскольку это является залогом успешной работы в будущем. Собственниками именно таких предприятий, как правило, зачастую выступают крупные перерабатывающие компании — ЦБК, ЛДК, — наиболее нуждающиеся в инвестициях в обновление оборудования.
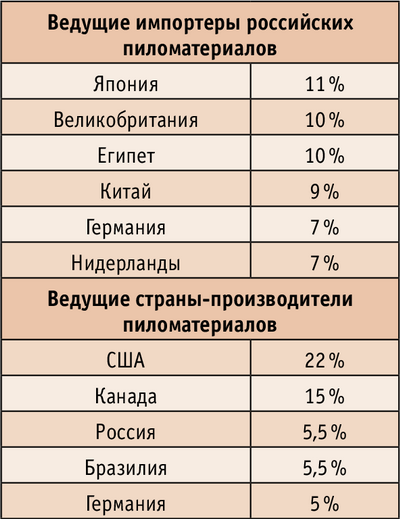
Логическая цепочка здесь состоит из трех звеньев: леспромхозу выделяют лесфонд на 5 лет; таким образом, лесозавод-владелец обеспечен сырьем лишь на 5 лет; инвестор не может вложить средства в развитие лесозавода, поскольку срок окупаемости инвестиций больше срока аренды лесфонда. А вдруг через пять лет предприятие не выиграет на аукционе лесфонд? То есть срок аренды лесных участков не должен быть меньше срока окупаемости инвестиционных проектов.
2. Нелегальные заготовки древесины. По официальным данным, в России нелегально заготавливается менее 11% древесины. Однако активисты природоохранных организаций на Западе упорно распространяют информацию о том, что каждое пятое бревно, заготовленное в России, добыто с нарушением законодательства. А какой инвестор согласится вкладывать свои деньги в такую криминализированную страну?
3. Отсутствие правовой защиты собственности. Корпоративные конфликты последних лет за право обладания целлюлозно-бумажными комбинатами (в первую очередь, Котласским, Архангельским и Сокольским ЦБК, Братским ЛПК) не прибавляют привлекательности российскому ЛПК. Лесозаводам в этом отношении пока повезло — все взоры «недружественных поглощателей» направлены на ЦБК (сегодня это единственные стабильно прибыльные предприятия в российском ЛПК), и пока они не замечают лесозаводы. Но, похоже, скоро очередь дойдет и до крупных ЛДК, поскольку сейчас все более‑менее стабильно работающие ЦБК поделены и, как правило, позиции действующих собственников весьма устойчивы как в региональных, так и в федеральных органах власти, а также среди работников предприятий.
В последнее время проявляются симптомы будущих недружественных заходов и на лесозаводы: скупка акций, распространение негативной информации о лесозаводах. Если попытки незаконного захода на лесопильные комбинаты будут предприняты, это не будет способствовать увеличению роста инвестиций в российскую лесопильную отрасль.
Чтобы избежать корпоративных конфликтов, зарубежные инвесторы предпочитают строить предприятия «с нуля», дабы максимально исключить возможность претензий со стороны бывших собственников. Более того, представители финско-шведской компании Stora Enso хотели даже расторгнуть договор о строительстве комбината в новгородском поселке Неболчи, когда обнаружили на месте строительства остатки предыдущей постройки.
Корпоративные конфликты, возникавшие в последнее время вокруг российских ЦБК, не придают привлекательности отечественному ЛПК. Вряд ли западный инвестор, находящийся в здравом уме, захочет вкладывать деньги в развитие комбината, который в течение нескольких лет лихорадит из-за судебных разборок. Да и владельцам предприятия, которым до последнего момента неясно, отберут у них комбинат или нет, вкладывать средства в его развитие не резон — а ну как наша неповоротливая судебная машина задавит законного владельца?
4. Низкая доходность лесного бизнеса. Как известно, лесопильные предприятия могут достигнуть наибольшей рентабельности лишь за счет максимально глубокой переработки древесины. Однако отечественное лесопиление ориентировано в большинстве своем на экспорт и выпускает то, что пользуется спросом за рубежом. Справедливости ради стоит сказать, что большим спросом за рубежом пользуются продукты с низкой добавленной стоимостью.
5. Отсутствие собственных научных разработок в лесопильной отрасли. Отечественное машиностроение не предлагает станки, на которых можно было бы выпускать продукцию с более высокой добавленной стоимостью, нежели обычные пиломатериалы. В результате оборудование приходится закупать за рубежом. Но несмотря на то, что государством провозглашается отмена ввозной таможенной пошлины и НДС на товары, не имеющие аналогов в РФ, предприятиям приходится буквально доказывать уникальность зарубежных станков с привлечением экспертов. А это удлиняет сроки поставки оборудования.
Кстати, когда на 25‑м лесозаводе обсуждался вопрос, где взять деньги на модернизацию, российские банки «отпали» сразу же. Свой взор предприятие обратило на запад. Надежного кредитора предприятие нашло в Австрии. Кредит (15 млн евро) на реализацию проекта модернизации производства предоставил «Райфайзенбанк Австрия». Но выделил он эти деньги не просто так. Для этого лесозаводу пришлось предоставить просто «железные» поручительства ведущего европейского ЦБК — Архангельского, председателем совета директоров которого является австриец, доктор Хайнц Циннер. Лишь после этого лесозавод получил необходимый кредит.
Таможня забирает добро
В своей публикации я уже отмечал, что в России, по большому счету, нет передовых конкурентоспособных разработок в лесопильной промышленности. И ожидать их появления в ближайшем будущем, наверное, не стоит. Так что использование зарубежных станков и линий на лесозаводах видится оправданным, поскольку промышленность необходимо развивать уже сейчас. Другой разговор, что параллельно с этим государство должно содействовать проведению внутри страны разработок и конструированию новых отечественных лесопильных линий, отвечающих мировым стандартам. И лишь потом, когда такие разработки и линии появятся, можно будет защищать отечественного производителя введением заградительных импортных таможенных пошлин на ввоз лесопильного оборудования. В России очень часто все ставится «с ног на голову».
В России нет своих станков. Это признают и в правительстве. При этом государство не вкладывает деньги в развитие науки, в современные разработки. Зато государство «успешно» замедляет модернизацию лесопильных производств ввозными пошлинами — сегодня для того, чтобы ввезти оборудование в страну, лесозаводы должны заплатить не только 18%-й НДС, но и 10%-ную таможенную пошлину, что делает стоимость оборудования выше практически на треть. Кроме того, существует и пошлина «на технологии», достигающая трети стоимости оборудования. Чтобы ее не платить, предприятие-импортер должно предоставить справку о том, что аналогичное оборудование не производится в России, ему нет российских аналогов.
По логике, задача государства заключается в стимулировании вывоза из России продукции самой глубокой переработки древесины — бумаги, картона, плит MDF, вагонки и т. п. Однако политика правительства такова, что сегодня российским предпринимателям выгоднее экспортировать круглый лес, нежели продукцию глубокой переработки. Так, продолжает взиматься таможенная пошлина при вывозе пиломатериалов — 3% (но не менее 2,5 евро/м3), целлюлозы — 5%. Это приводит к тому, что лесной бизнес сегодня не является источником повышенной доходности и не привлекает инвесторов. Когда вывозные пошлины на круглый лес будут повышены хотя бы до 25%, а на продукцию глубокой переработки отменены, инвестиционная привлекательность отрасли увеличится.
Безусловно, сегодня понимают это и в правительстве. Постепенно предпринимаются шаги по снижению вывозных таможенных пошлин на продукцию глубокой переработки (некоторые виды целлюлозы, бумаги, пиломатериалов), в будущем году запланировано увеличить вывозные пошлины на «кругляк» до 10%, на некоторые виды деревообрабатывающего оборудования временно введена 0%-ная ставка ввозной таможенной пошлины. Однако этих шагов пока недостаточно.
Более того, попытки более значительных изменений в сфере таможенного регулирования натыкаются на барьер в виде Минэкономразвития. Впрочем, постепенно и в правительство приходит понимание, что во многом от государства, его роли зависит развитие лесной отрасли страны. Уже много раз говорилось о том, что выручка российского леспрома может достигать $100 млрд. Однако пока рост товарной продукции находится в пределах инфляции и даже не достигает ее, а это говорит о том, что организм лесной промышленности работает крайне неудовлетворительно.
Резюме
На открытии лесопильного цеха Лесозавода 25 председатель подкомитета Государственной Думы по лесным ресурсам, бывший президент группы компаний «Титан» Владимир Крупчак отметил, что именно за такими современными заводами будущее лесопильной отрасли России. Новая техника значительно повысила производительность труда и уровень зарплаты на предприятии.
Однако вопрос модернизации оборудования необходимо увязывать с социальными вопросами. Как известно, увеличение производительности труда ведет и к сокращению штата предприятия. Если раньше существовавшие объемы производства обеспечивали работой сотни человек, то после модернизации необходимы единицы — на лесозаводах проводятся сокращения. Это, пожалуй, единственный минус модернизации оборудования. Однако прогресс не остановить, и рано или поздно модернизацию оборудования и технологий проведут все крупные лесопильные предприятия страны — без этого завтра не будет возможности развивать свой бизнес и удерживать завоеванные позиции.
В своей публикации я неоднократно употреблял словосочетание «модернизация технологий». Именно так. Сегодня мы отстали не просто по оборудованию, у нас не просто «износились» станки. Мы отстали принципиально. Мы могли бы пилить со скоростью до 90 м/с, а пилим на 18 м/с. Мы могли бы выпускать больше евровагонки, а выпускаем пиломатериал. Что делать?
Видимо, необходимо ждать, пока в правительство придут люди, способные думать несколько иными категориями, кроме как «сиюминутная прибыль». Практически на всех крупных лесопильных предприятиях такие люди появились.
Александр ГРЕВЦОВ