Дорога в тупик
Рубрика Техника и технологии
Опыт создания и опытно-промышленной эксплуатации газогенераторной установки на древесном топливе и газодизельной электростанции на ее основе.
Проблема производства тепловой и электрической энергии с использованием древесного топлива становится все более актуальной. Побудительными причинами являются опережающий рост цен на покупные энергоносители и экологические проблемы, связанные с загрязнением атмосферы и глобальным потеплением климата. Одним из вариантов решения задачи производства энергии с использованием древесного топлива является производство генераторного газа с последующим использованием его для выработки тепловой и электрической энергии. Этот вариант энергетического использования древесины привлекает внимание как ученых, так и лесопромышленников − потенциальных потребителей оборудования для производства энергии. Интерес к данному направлению вполне понятен: газ, несомненно, является одним из самых удобных в использовании видов топлива. Часто вспоминают период Второй мировой войны, когда в России газогенераторы широко применялись для выработки топлива для автомобилей и тракторов. Поэтому решение проблемы производства тепловой и электрической энергии посредством газогенерирования на современном этапе развития многим представляется наиболее простым и эффективным. Легковесному подходу в дискуссиях о преимуществах газогенераторов способствует и терминологическая путаница, когда газогенераторами называют шахтные топки с двухстадийным сжиганием топлива, часто используемые в отечественных и зарубежных водогрейных котлах малой мощности. Энтузиастам кажется, что создание эффективной газогенераторной дизельэлектростанции не представляет значительной трудности.
В настоящей публикации рассматриваются проблемы, связанные с созданием газогенератора как аппарата для выработки газа, пригодного для использования в качестве топлива для двигателя внутреннего сгорания или газовой турбины.
В СССР в середине 1960-х годов выполнен комплекс работ, завершившихся сооружением и опытно-промышленной эксплуатацией газогенераторной (энергохимической) установки. Настоящая работа посвящена анализу проектных показателей и результатов опытно-промышленной эксплуатации этой установки по материалам, представленным в отчете Центрального научно-исследовательского института механизации и энергетики лесной промышленности (ЦНИИМЭ).
Опытно-промышленный образец установки был смонтирован в Крестецком леспромхозе ЦНИИМЭ Новгородской области и некоторое время являлся его хозрасчетным цехом. Установка предназначалась для выработки смолы, а также электрической энергии для нужд ЛПХ. Смола использовалась на Чеховском регенератном заводе в качестве смягчителя для резины. Топливом служила щепа (дробленка) из ветвей и сучьев кроны деревьев. Схема установки представлена на рисунке.
газогенераторной энергохимической установки Крестецкого ЛПХ
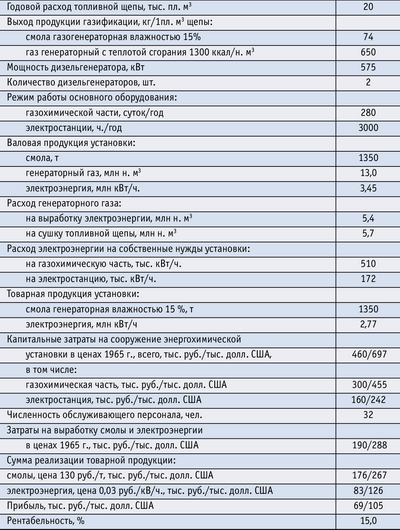
Энергохимическая установка и газодизельная электростанция включали: бункер-дозатор 1 топливной щепы со скиповым подъемником 2, циклоном 3 и шнековым конвейером 4; барабанную сушилку 5 с циклонной топкой 6, воздуходувкой 7, шнековым питателем 8, дымососом 9 и циклоном 10, шнековым выгружателем 11; ковшовый элеватор 12; газогенератор 13 со шнековым питателем 14, гидрошуровкой-уровнемером 15 и воздуходувкой 16; гидрозатвор 17; воздушный охладитель 18 с воздуходувками 19; центробежный смолоотделитель 20; сепаратор смолы 21; сборник жижки 22; сборники смолы 23 с насосом для перекачки смолы 24; дополнительный улавливатель смолы 25; пенный охладитель 26; сборник оборотной воды 27 с насосом 28; градирня 29 с насосом 30 и воздуходувкой 31; фильтр тонкой очистки газа 32; абсорбер 33; промежуточный сборник загрязненной воды 34 с насосом 35; ресиверы 36 с газодувкой 37; гидрозатвор 38; газодизельную электростанцию с газодизелем 39, электрогенератором 40 и электрощитом 41.
Энергохимическая установка и газодизельная электростанция работали следующим образом.
Топливная щепа при поставках ее к установке автомобилями-самосвалами посредством скипового подъемника 2 подавалась в бункер-дозатор 1, в котором создавался промежуточный запас измельченного древесного топлива. Предусматривалась также возможность подачи щепы в бункер-дозатор пневмотранспортом через циклон 3. Исходная влажность топливной щепы, подаваемой в бункер-дозатор, составляла 51−53% − влажность свежесрубленной древесины.
Из бункера-дозатора шнековым конвейером 4 топливная щепа через шнековый питатель 8 подавалась в барабанную сушилку 5. Сушка щепы в барабанной сушилке происходила за счет тепла, получаемого от сжигания в циклонной топке 6 генераторного газа, вырабатываемого установкой. Первичное и вторичное дутье в топке создавалось воздуходувкой 7.
Влажность щепы, выходящей из барабанной сушилки 8, составляла 21−22%. Отработанные продукты сгорания генераторного газа из барабанной сушилки дымососом 9 через циклон 10 выбрасывались в атмосферу. Подсушенная щепа шнековым выгружателем 11, ковшовым элеватором 12 и шнековым питателем 14 подавалась в газогенератор 13. Для разравнивания щепы по сечению шахты и автоматического слежения за ее уровнем в шахте газогенератора имелась шуровка-уровнемер 15. Первичное и вторичное дутье в газогенераторе создавалось воздуходувкой 16. Совместно с воздухом в шахту газогенератора подавался пар.
Парогазовая смесь из газогенератора через гидрозатвор 17 и воздушный охладитель 18 подавалась в центробежный смолоотделитель 20 и сепаратор смолы 21. Отделенная смола поступала в сборник жижки 22, а затем насосом 24 перекачивалась в сборники смолы 23. Далее парогазовая смесь поступала в дополнительный улавливатель смолы, затем в пенный охладитель 26, в фильтр тонкой очистки газа 32 и абсорбер 33. Температура парогазовой смеси на входе в пенный охладитель составляла около 700С.Генераторный газ в пенном аппарате удавалось охладить до температуры 30-370С при требуемой температуре 300С.
Загрязненная вода из фильтра тонкой очистки газа 32 и абсорбера 33 поступала в промежуточный сборник загрязненной воды 34, из которого насосом 35 перекачивалась на испарение воды и сжигание загрязняющих примесей в топку 6 барабанной сушилки 5.
Охлаждение парогазовой смеси в пенном охладителе 26 осуществлялось оборотной водой. Оборотная вода, прошедшая через пенный аппарат, имеющая температуру 39-430С, поступала в сборник оборотной воды 27, из которого насосом 28 подавалась для охлаждения в градирню 29. Охлажденная в градирне до 22-260С оборотная вода насосом 30 снова подавалась в пенный охладитель.
Часть очищенного и охлажденного генераторного газа из абсорбера подавалась в ресиверы 36, а затем газодувками 37 через гидрозатвор 38 в газодизель 39 для выработки электроэнергии. Другая часть газа подавалась на сжигание в топку 6 барабанной сушилки 5.
По проектным данным топливная щепа влажностью 53% на одну треть состояла из древесины хвойных пород и на две трети − из лиственных. Щепа содержала равные объемы частиц размером 35−10 мм и более мелких с небольшой (до 6%) примесью более крупных частиц.
Стоимость топливной щепы, потребляемой энергохимической установкой, составляла 3,7 руб./пл. м3 (5.6 долл. США). Основные расчетные технико-экономические параметры установки приведены ниже.
Отметим, что планировалось два дизельгенератора, но фактически был установлен один.
За три года, с 15 октября 1965 г. по 1 ноября 1968 г., энергохимическая установка отработала 4184 часа. За это время было переработано 9530 пл. м3 топливной щепы и выработано 682 т смолы влажностью 16,4%.
Однако в эксплуатации дизель-генератора возникли проблемы. В протоколе заседания Комиссии по межведомственным испытаниям установки от 16 октября 1968 г. отмечается, что дизель-генератор в процессе испытаний отработал на газе 76 часов вместо требуемых 200 часов по методике. В результате испытаний было установлено, что при нагрузке 540 кВт расход газа составлял 835 н.м3/ч., жидкого топлива − 40,5 кг/ч. Часовой расход газа составлял от 600 до 800 нм3/ч. в зависимости от нагрузки на двигатель. Удельный расход генераторного газа составлял около 1,8 н.м3/кВт/ч. Коэффициент полезного действия газодизеля составлял около 29,5%.
Через 180 часов работы газодизеля произошло заклинивание ротора газодувки. Причиной заклинивания было названо наличие в генераторном газе растворимых смол, а также летучих кислот. Было также отмечено, что на привод газодувки затрачивается около 5% электрической мощности, развиваемой дизель-генератором.
Обнаружено повышенное содержание летучих органических кислот в оборотной воде и в парогазовой смеси. В пересчете на уксусную содержание кислот в парогазовой смеси до пенного аппарата колебалось от 16,7 до 25,4 г/н.м3 сухого газа; на выходе из пенного аппарата − от 0,43 до 2,44 г/н.м3. Эффективность улавливания кислоты в пенном аппарате колебалась от 91 до 97,5%. Содержание кислоты в генераторном газе после уловителя кислоты составляло в пределах 0,92−2,16 г/н.м3. Концентрация кислоты в оборотной воде колебалась в пределах 2,6−8,84%. Оборудование установки, изготовленное из углеродистой стали, подвергалось коррозии от воздействия паров, газов и смоляных конденсатов. В сточных водах обнаружено наличие фенольных соединений.
Сложной проблемой являлась сложность утилизации и обезвреживания загрязненных технологических вод. При производительности энергохимической установки не более 62−70% от расчетной за сутки выделялось 1700−1900 л конденсата, а при расчетной производительности (2500 н.м3 генераторного газа в час) должно выделяться до 3000 л конденсата в сутки. Из-за наличия в этих конденсатах фенольных соединений и кислот, направлять их в промышленные стоки нельзя. Поэтому в установке была предусмотрена возможность термической ликвидации загрязненных вод − испарением их и последующим сжиганием содержащихся в них органических веществ в топке барабанной сушилки топливной щепы. Опыт эксплуатации показал, что производительность установки по ликвидации загрязненных вод должна быть не менее 550−600 л/ч. что потребует существенного увеличения расхода газа на их огневую утилизацию.
Несмотря на очевидные негативные результаты проведенных в Крестецком ЛПХ испытаний энергохимической установки в середине октября 1968 г. Межведомственная комиссия пришла к следующему решению: энергетическая установка ЦНИИМЭ после доработки может быть рекомендована для внедрения в лесозаготовительную промышленность. В числе рекомендаций комиссии имели место предложения по тиражированию установок, для чего заинтересованным организациям поручалось откорректировать конструкторскую документацию, определить количество установок, подлежащих строительству в течение следующей пятилетки, и места их строительства. В Опаринском ЛПХ была даже построена установка, по мощности превышающая Крестецкую в два раза.
Жизнь, тем не менее, сильнее постановлений. Запустить в эксплуатацию газодизельную электростанцию так и не удалось. Расчетные экономические показатели работы установки не были достигнуты. Кроме того, установка ощутимо отрицательно влияла на экологическую обстановку. Чеховский регенератный завод отказался от поставок смолы, перейдя на более дешевые реагенты. Других постоянных потребителей на смолу найти не удалось, и это послужило еще одной причиной прекращения работ в данном направлении. В скором времени после завершения испытаний установка была остановлена, а затем демонтирована. Та же участь постигла и Опаринскую установку.
Для оценки эффективности энергетического использования древесины посредством производства генераторного газа необходимо прежде всего определить коэффициенты полезного действия установки. Нами выполнены эти расчеты с использованием проектных данных и результатов испытаний установки.
Оказалось, что коэффициент полезного действия (КПД) газогенератора, определенный как отношение суммы теплоты сгорания выработанного газа и смолы к теплоте сгорания использованного топлива, составил всего 54%, что в 1,5 раза ниже, чем у самого несовершенного парового или водогрейного котла. Проектный КПД по выработке электроэнергии, определенный как отношение отпущенной электроэнергии к теплоте сгорания использованного топлива, составил только 8,3%, а по результатам испытаний и того меньше − около 5%.
Опыт эксплуатации газогенераторной (энергохимической) установки в Крестецком ЛПХ, несмотря на то, что над этим проектом работало несколько квалифицированных научных, проектных и производственных коллективов, оказался отрицательным. По эффективности использования теплоты древесины установка газогенератор − дизельгенератор уступает установкам с прямым сжиганием древесного топлива − паровым и водогрейным котлам и электростанциям с паровыми турбинами.
Капитальные затраты на сооружение энергохимической установки составили бы в современных ценах более 20 млн руб. Можно оценить удельные затраты на 1 МВт установленной мощности с учетом инфляции доллара США за прошедшие годы величиной около 35 млн руб. При современных, гораздо более строгих экологических требованиях, эта величина окажется еще выше.
Паротурбинные тепловые электростанции на древесном топливе при аналогичных удельных капиталовложениях (20−30 млн руб./МВт в зависимости от мощности) имеют больший эффективный КПД при гарантированном сроке эксплуатации более 30 лет, минимальном загрязнении окружающей среды и возможности в широких пределах изменять соотношение электрической и тепловой мощности.
КПД газогенераторной установки мог бы повыситься за счет полезного использования тепла. Однако с технической точки зрения эта задача достаточно сложна, а с экономической − затратна, поскольку теплоту предстоит собирать на большом количестве объектов установки и при различных уровнях температур: на сушилке топлива, на шахте газогенератора, на воздушном охладителе, на пенном охладителе, от системы охлаждения и выхлопных газов дизеля. Отметим также жесткую связь между электрической мощностью и возможной тепловой мощностью установки.
Весьма затратным является решение проблемы очистки газа до степени, обеспечивающей нормальную и долговечную работу дизеля даже при условии использования запального топлива в количестве 20−30% от общей теплоты сгорания используемого топлива. Сложная и дорогая система охлаждения и очистки генераторного газа и воды значительно увеличивает стоимость установки, но не обеспечивает их эффективной очистки.
И, наконец, нельзя не сказать о том, что газогенераторная установка представляет собой небольшой химический завод, со всеми вытекающими последствиями: требованиями к материалам, из которых должно быть изготовлено оборудование, и требованиями к охране окружающей среды. С учетом изложенного, энергохимические установки могут иметь экономическую эффективность только при производстве химических продуктов с достаточно высокой рыночной ценой одновременно с выработкой силового генераторного газа. Цена таких продуктов должна составлять не менее 4000 руб./т. В обозримом будущем представляется маловероятным достижение относительно малотоннажными газо-генераторными энергохимическими установками конкурентоспособности с современными гигантскими газо- и нефтехимическими предприятиями оргсинтеза.
Всякая попытка переделать топливо с целью улучшения его качества приводит, как минимум, к снижению КПД. Как показывает опыт эксплуатации Крестецкой установки, почти половина вырабатываемого генераторного газа использовалась для предварительной сушки топливной щепы и испарения загрязненной воды. Люди, приводящие в качестве примера опыт использования газогенераторов во время Второй мировой войны, забывают о том, что в то время в газогенераторах использовали специально подготавливаемые высушенные колотые березовые чурочки, а какие бы то ни было требования к охране труда и окружающей среды отсутствовали, равно как и требования к долговечности оборудования.
Преобразование топлива может быть экономически оправдано, это видно по росту производства топливных гранул (энергопеллет), по существенному снижению затрат на перевозку топлива на значительные расстояния в случаях, когда затраты на преобразование топлива компенсируются исключением затрат на строительство новых энергообъектов (приспособление топлива к использованию на ранее построенных энергетических объектах) или в случаях, когда затраты на улучшение потребительских качеств топлива для богатого потребителя не имеют большого значения.
Не выдерживает критики и вариант использования газогенераторов для выработки тепловой энергии по схеме газогенератор − паровой котел. Для обеспечения газом, например, одного парового котла паропроизводительностью 10 т/ч. (~ 8 МВт) потребовалось бы построить 3 газогенератора по 3 мВт, подобных Крестецкому. Если принять стоимость собственно газогенератора с сушилкой щепы в размере 20% от общей стоимости установки, то стоимость трех газогенераторов составит ~ 420 тыс. долларов США при стоимости котлоагрегата не более 70 тыс. долларов США, в котором стоимость топки Померанцева едва ли превышает 9 тыс. долларов США.
Надеемся, представленный выше анализ позволит читателям сделать вывод о более эффективном использовании прямого сжигания древесины для выработки тепловой и электрической энергии по сравнению с производством и использованием генераторного газа. Этот вывод подтверждает и судьба другого энергетического объекта в том же Крестецком ЛПХ − котельной на древесном топливе, которая была построена практически одновременно с энергохимической установкой − в 1964 г. Эта котельная исправно снабжала тепловой энергией цех ДВП, административные и промышленные здания предприятия и жилой поселок с населением около 4000 жителей около 35 лет и может продолжить работу после ревизии котлов.
Приглашаем к сотрудничеству заинтересованные организации.
Контактный телефон/факс:
(095) 916-05-99.
E-mail: gnclpkte@rol.ru
В. С. СУХАНОВ, д. т. н., А. Б. ЛЕВИН, профессор,
Головной научный центр лесопромышленного комплекса по технологиям и энергетике, г. Москва