Ленточнопильные комплексы. Технология качественного распила
Приход ленточнопильных станков в индустрию деревообработки ознаменовался качественным прорывом. Технология на базе ленточного пиления позволила сократить долю отходов, получить пиломатериал с повышенными прочностными свойствами, оптимизировать процесс раскроя заготовки. Пройдя путь от модельной мастерской, «ленточные пилорамы» теперь все чаще занимают головное место в современных лесопильных производствах.
Прототипом ленточнопильного узла в машинах первичного раскроя бревна действительно послужил небольшой станок, используемый для распиловки мебельных криволинейных заготовок. Оператор вручную подавал брусок вдоль стола к «бегущей» узкой ленте в виде кольца, одетого на два шкива (рис. 1). На ленте были высечены зубья так, что они легко распиливали древесину по задаваемой траектории. Возможно, это изобретение так и осталось только на службе изящных дел мастеров, если бы не тенденции, ставшие приоритетными в области первичной лесопереработки.
Развитие принципиально нового подхода к данной задаче, получившего известность как метод радиального распила, и привело разработчиков к созданию ленточнопильных комплексов (рис. 4). Вырезка из периферийных областей сечения бревна (рис. 6б) требовала, чтобы заготовка несколько раз переворачивалась в процессе продольной распиловки. Все размеры — толщина, расположение пиломатериала рассчитывались в процессе оптимизации раскроя исходя из принципа максимальной выборки качественной доски. Только такая заготовка, с одинаковыми, высокими механическими свойствами по всей площади торца пригодна для дальнейшего сращивания и получения высокопрочного бруса для несущих строительных конструкций. Еще одним существенным моментом является применение особого вида инструмента — ленточной пилы, сводившей к минимуму долю стружки. Достаточно сказать, что переход на такой вид обработки поднимает процент выхода готовой продукции до 65−72%!
Ленточнопильные станки часто называют ленточными пилорамами по аналогии с названием традиционного оборудования для первичной распиловки древесины. Ленточная пила устанавливается на два стальных шкива, имеющих специальный выпуклый профиль (рис. 1). Механизм натяжения создает усилие, необходимое для устойчивой работы пильного узла, которое препятствует соскальзыванию или пробуксовке ленты. В мощных станках с шириной инструмента 100−200 мм эта величина достигает нескольких тонн! Выступ зубьев за край шкива регулируется с помощью устройства наклона на угол α (рис. 1), не превышающий 1−3 градуса.
Еще одно преимущество ленты по сравнению с рамной пилой — высокая и стабильная скорость резания. Она сообщается от вращающегося приводного шкива. Чтобы исключить колебание инструмента, помимо его натяжения применяется специальный успокоитель поз. 6 (рис. 4), подводимый оператором к зоне резания максимально близко. Таким образом, получаемый пиломатериал имеет весьма хорошие показатели шероховатости поверхностей, соответствующие экспортному ГОСТу.
Существующий модельный ряд условно можно поделить на две обширные группы — с вертикальным (рис. 2) и горизонтальным (рис. 3) расположением инструмента. Горизонтальная компоновка чаще всего встречается в малогабаритных комплексах, состоящих из стапеля, на котором закрепляется неподвижная в процессе резания заготовка и перемещающийся вдоль нее пильный блок. Характеристика таких систем предлагается в таб. 1.
Сочетание таких показателей, как относительно невысокая стоимость от 150000 руб. и мобильность, сделало эти модели легкой серии весьма популярными там, где остальные требования не высоки. Следует добавить, что для большей маневренности станки такого класса выпускаются на шасси в виде прицепа и могут иметь автономные приводы типа двигателей внутреннего сгорания, работающих на жидком топливе.
Но для массового производства пиломатериала, с объемами переработки от 50 м3 за смену предпочтительной является мощные агрегаты с вертикальной ориентацией ленточной пилы. Блок-схема одного из них изображена на рис. 4. Пильный блок стационарный и монтируется на специальном фундаменте.
Бревно устанавливается на каретку поз. 1, двигающуюся по рельсам. Фиксация происходит парными зажимами поз. 4 так, что силовое замыкание не затрагивает поверхности каретки. Впоследствии это минимизирует износ направляющих планок. В таком положении заготовка может перемещаться в поперечном направлении вместе со стойками поз. 2 и в продольном — с кареткой поз. 1. Требование технологии — поворот бревна происходит путем выдвижения специальных цепных вращателей поз. 5 до тех пор, пока не будет достигнуто требуемое положение.
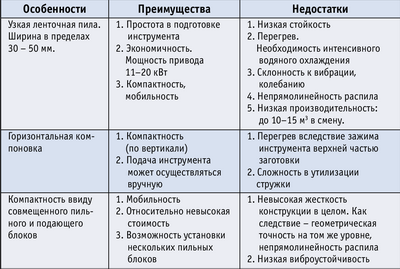
Управление всем комплексом осуществляет один оператор с помощью объединенного пульта. Его место в зависимости от модификации может располагаться как на каретке, так и рядом со станком. Поскольку станки такого класса имеют высокую производительность, большинство функций в них механизировано. В частности, перемещение успокоителя пилы происходит по команде, с включением электро- или гидропривода.
После того, как в ленточный узел установлена пила поз. 8, производится ее натяжение верхним шкивом поз. 7. Как и в предыдущем случае, в различных моделях встречаются как механические, так и гидравлические натяжные устройства. Узел запускается в работу приводным шкивом поз. 9. Необходимо отметить ряд особенностей таких узлов.
- Ширина пил варьируется от 100 до 250 мм.
- Диаметр шкивов 1000−1400 мм
- Мощность привода так же значительна — от 22 до 55 кВт
- Обязательно наличие защитного кожуха, очистителя шкива от поверхностного загрязнения, успокоителя пилы поз. 6 с управляемым положением по вертикали.
- Наличие устройства капельной смазки ленты, препятствующей налипанию древесной смолы и облегчающего процесс резания.
Важнейший показатель работы комплекса — прямой распил заготовки имеет помимо уже известных составляющих еще одну — прямолинейность движения каретки поз. 1. И здесь гарантом выступает точная установка направляющих рельс, а также массивность и жесткость конструкции, компенсирующей все ударные и грузовые нагрузки. Современные модели имеют массу подвижной части 3500−5000 кг. Для их разгона до штатных скоростей (а на обратном, «холостом» ходу они могут достигать более 100 м/мин.) требуются мощные, высокомоментные приводы, исключающие заклинивание в процессе рабочего хода каретки и, соответственно, заготовки. В этом качестве хорошо зарекомендовали себя гидродвигатели мощностью от 5 кВт с возможностью плавной регулировки скорости дросселем гидросистемы.
Количество стоек поз. 2 при выборе модели зависит от длины заготовки (таб. 2) и определяет геометрию распила.
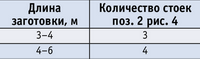
Технология качественного распила заготовки обязательно предполагает формирование и использование базовой грани. Делается это на первом переходе. Когда целое бревно только что было установлено на каретку. Поперечным перемещением стоек поз. 2 достигается необходимый выступ заготовки за плоскость пиления, и начинается рабочий ход. В конечной точке отпиленный горбыль отделяется от бревна и сбрасывается со станка.
Далее происходит поворот заготовки на 180°. Одновременно выдвигаются специальные упоры поз. 3, с которыми и соприкасается полученная базовая поверхность. Бревно вновь фиксируется зажимами поз. 4, циклы перемещения стоек и каретки повторяются.
Встраивается ленточнопильный комплекс в технологическую линию, как правило, по типовой схеме, представленной на рис. 5. Подача бревен по поперечному транспортеру происходит через бревноподатчик или устройство поштучной подачи бревна. Здесь в полной мере можно оценить способность каретки компенсировать нагрузки от скатывающихся даже с высоты 100−200 мм полутонных заготовок.
Далее производится цикличный раскрой бревна с поочередным сбросом на приемный транспортер либо горбыля, либо доски, либо бруса. Задача системы транспортировки — в оперативном распознавании и соответствующем направлении того или иного полуфабриката. В случае, если функция ленточнопильного станка — получение полубруса с последующей распиловкой на многопильном станке (максимальная производительность), то по необходимости, без дополнительных усилий головной станок может полностью взять на себя производство пиломатериала (максимальная доля готовой продукции).
Производительность ленточнопильного станка оценивается путем составления циклограмм. Для приблизительной оценки можно считать, что средняя скорость подачи составляет 20−30 м/мин., обратный ход в 2 раза быстрее. Скоростью поперечного перемещения можно пренебречь, так как она составляет 0,1−0,5 м/сек. Значительные потери времени происходят на этапе первого позиционирования бревна, оценки качества заготовки и планирования карты раскроя. Неизбежно сказываются на работе участка и сбои в системе сортировки цеха, если таковые имеют место. Если обратиться вновь к вопросу компоновки станка, то вертикальное расположение широкой пилы, во-первых, исключает ее зажим заготовкой, а во-вторых, за счет большей площади наблюдается интенсивная теплоотдача, препятствующая перегреву ленты. Все это способствует повышению стойкости, времени работы инструмента и, как результат, сокращению простоев оборудования.
Удовлетворительным является показатель для промышленного класса станков на уровне 50−70 м3 переработанного сырья в смену (8 ч.). Только в этом случае стоимость комплекса, стартующая от 50 тыс. у. е. (в среднем), сопоставима с прибылью, получаемой в течение 9−12 месяцев работы.
За последние годы в России ленточнопильные станки, как никакое другое оборудование, стали предметом тиражирования десятками отечественных производителей. Ложное представление о простоте конструкции, помноженное на нулевой маркетинговый прогноз, привели к тому, что почти все выставки, связанные с деревообработкой, буквально пестрят «ленточками» «а ля сделай сам». Возникает закономерный вопрос: настолько ли непреодолимы трудности освоения других классов лесопильной техники?
А в то же время зарубежные заводы предлагают все новые решения. К их числу относятся итальянские системы с независимыми захватными стойками, гидростатические приводы позиционирования, вытесняющие традиционные винтовые пары. В результате скорость и точность установки заготовки увеличиваются на порядок. В том же русле разворачивается конкурентная борьба за сокращение времени на основные и вспомогательные операции за счет активного внедрения автоматики и телемеханики. Агрегатированные модули, включающие до 4‑х пильных блоков и поточную систему подачи бревна, уже успешно работают в составе лесопильных комплексов с объемами переработки до 200000 м3 сырья в год. Уникальность ситуации в том, что, несмотря на все эти достижения, всегда будут сторонники как ленточного, так и альтернативного способов пиления, а значит, соперничество новаторских идей не остановится никогда.
Справка: Классической технологией распиловки пиловочника — круглых бревен диаметром от 150 до 1000 мм и длиной от 4 до 6 м — считается так называемый двухрядный раскрой. В первом ряду бревно пропускается через пилораму, где рамные пилы отрезают два горбыля, оставляя двухкантный брус. Этот полуфабрикат попадает на пилораму второго ряда меньшего размера. Здесь полубрус («лафет») распиливается на доску тем же инструментом. Из-за особенностей работы скорость потока не превышает 5−7 м/мин., а доля отходов составляет 40−45%. Но главное ограничение такого метода — неоднородность доски в поперечном сечении, полученной путем так называемого тангенциального распила (рис. 6а). Это проявляется особенно отчетливо в пиломатериале, извлекаемом из сердцевины бревна, где в его центральной части прочность минимальна. Как следствие, деформация доски при последующей сушке. Использование такой продукции возможно только в строительстве и только в тех местах, где требования к прочности деталей минимальны. Вот почему этот вид пиломатериала еще называют сокращенно «стройдоска».
Справка: Ленточная пила изготавливается из заготовки — стальной ленты, имеющей высеченные с одной стороны зубья. Применяется специальная сталь, упругая и восприимчивая к знакопеременным изгибным нагрузкам, хорошо свариваемая и износостойкая. Ее толщина в подготовленном состоянии колеблется от 1 до 2 мм. Тогда как рамные или дисковые пилы делают пропил шириной от 4 мм. Такая разница и позволила ленточным пилам по праву считаться наиболее экономичным инструментом. Подготовка пилы заключается в ее отрезке, сварке стыка так, что образуется форма кольца. В дальнейшем зачищается сварной шов, инструмент вальцуется и затачивается. Есть два основных способа формирования режущих граней зубьев — формовка-разводка или наплавка твердосплавных наконечников. И в том, и в другом случаях финишной операцией будет заточка передней и задней рабочих поверхностей зуба (для напаянных зубьев также необходимо формирование боковых граней). Стойкость пилы относительно невысока — от 2 до 4 часов интенсивной работы до очередной заточки. Тем не менее, при правильной организации технологического цикла этот показатель вполне оправдывается общим экономическим эффектом от такого производства.
Важное замечание: система автоматического управления бревнораспиловочным комплексом настроена таким образом, что нулевая поперечная координата совпадает с базовой поверхностью выдвижных упоров поз. 3. Это существенно облегчает задачу позиционирования. Следует также отметить, что производители таких комплексов предлагают выбор систем управления — от простейшей механической до цифровой, с ЧПУ. Последние способны хранить в памяти типовые карты раскроя, определять оптимальные режимы и управлять комплексом в целом. Но независимо от избранного вида, каждая из них оснащена датчиком поперечного перемещения в абсолютных и относительных координатных сетках, что дает минимально необходимые исходные параметры оператору для настройки станка на очередном переходе.
Вячеслав ДОГМА