«UPM Чудово»: 20 лет непрерывного развития
Высококачественная шлифованная и ламинированная фанера, которую изготавливают в компании «UPM Чудово» (Новгородская обл.), находит широкое применение в строительстве, оформлении помещений, производстве мебели, судостроении, машиностроении.
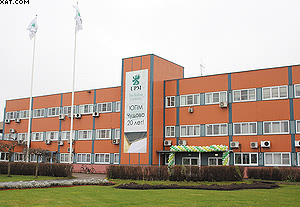
Здание администрации ООО «ЮПМ-Кюммене Чудово»
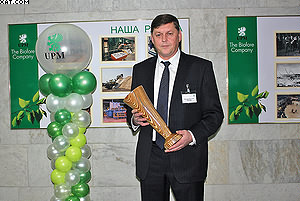
Генеральный директор ООО «ЮПМ-Кюммене Чудово» Анатолий Жуковец
История завода «UPM Чудово» началась 5 июля 1988 года, когда в Министерстве лесной промышленности СССР (Москва) были подписаны документы о создании первого совместного советско-финского промышленного предприятия по производству большеформатной березовой фанеры проектной мощностью 50 тыс. м3 − ЗАО «Чудово-RWS». Учредителями совместного предприятия стали: с финской стороны − Raute и Wilh, Schauman Ab, а с российской − «Новгородлеспром».
Выбор площадки для строительства нового завода в городе Чудово Новгородской области определили близость к источнику сырья, международному аэропорту Пулково и морским портам России и Финляндии, а также наличие автомобильной и железнодорожной магистралей. Для финансирования строительства 1 сентября 1988 года было подписано соглашение с лондонским Московским народным банком и финским банком Postipankki о предоставлении кредита на сумму 62,6 млн немецких марок. Работы начались в июле 1988 года на правом берегу реки Кересть, по соседству со спичечной фабрикой «Пролетарское знамя». Здесь уже были энергетические подстанции, которые вполне можно было использовать для нового предприятия. На стройке были заняты до 500 строителей, работали семь дней в неделю. Быстрые темпы строительства позволили запустить одно из крупных фанерных предприятий нашей страны на два месяца раньше намеченного срока − 1 ноября 1990 года.
В 2002 году финский лесопромышленный концерн UPM-Kymmene выкупил долю Raute Oy, а в 2005-м стал единоличным владельцем завода. В феврале 2006 года предприятие переименовали в ООО «ЮПМ-Кюммене Чудово».
Со дня запуска годовая производительность предприятия постоянно росла и сегодня составляет 100 тыс. м3. Летом 2008 года предприятие достигло рекордного рубежа, выпустив миллионный кубометр фанеры. Этот факт стал законной причиной для гордости коллектива завода, который насчитывает более 600 человек: на фанерном производстве занято около 570, а в цехе по производству шпона − 70.
«Финская» политика развития
На предприятии с самого основания не прекращается работа по совершенствованию технологии производства, модернизации оборудования, повышению качества продукции и обслуживания клиентов. Интенсивная модернизация технологий и оборудования на заводе началась семь лет назад.
В январе 2003 года на заводе введен в эксплуатацию цех по изготовлению березового шпона толщиной от 0,6 мм. Это лущильный станок, паровая сушильная камера и участок рубки-сортировки сухого шпона. Оборудование поставила компания Raute.
В 2006 году завершен монтаж третьей линии лущения, сушки-сортировки и ребросклеивания. На ней также установлено оборудование компании Raute.
Проведены модернизация и автоматизация всего участка набора пакетов шпона. Пять старых ручных станций заменены четырьмя новыми автоматическими станциями Plytec SGF4×8, каждая из которых обслуживается одним оператором-наборщиком. На станции все операции подачи шпона и алгоритм набора, переход пакетов на операцию подпрессовки и прессования выполняются автоматически. Это снижает потери сырья и рабочего времени и повышает производительность и эффективность работы всего участка.
Была модернизирована и линия починки листов шпона (Raute). Замена центровочно-загрузочного устройства (ЦЗУ) всех трех лущильных станков (Raute) завершена осенью 2009 года. И в 2010 году на предприятии установлен второй пресс для ламинирования фанеры.
Итак, сегодня на заводе действуют три технологические линии, на которых автоматически осуществляются операции получения и переработки лущеного шпона, подпрессовки и склеивания набранных пакетов из шпона, а также обработка фанеры (обрезка в размер, шлифование, ламинирование).
Качество начинается с сырья
Требования к качеству готовой фанеры постоянно повышаются, поэтому недопустимо использование некачественной древесины, приводящее к росту производственных затрат и увеличению числа претензий потребителей. В 1996 году компанией UPM впервые в нашей стране была разработана и стала использоваться система отслеживания источников происхождения российской древесины. Изначально эта система была создана для обеспечения высоких кондиций отечественной древесины, отправляемой на экспорт в Финляндию. Сейчас она применяется для контроля качества всех партий древесного сырья, поступающих на российские предприятия компании UPM.
В год фанерный завод потребляет до 300 тыс. м3 березового кряжа. Одним из основных поставщиков сырья для завода является ЗАО «Тихвинский комплексный леспромхоз» (КЛПХ).
Это предприятие стало собственностью UPM в ноябре 2005 года. Тихвинский КЛПХ был основан в 1929 году и считается одним из наиболее стабильно развивающихся лесозаготовительных производств Ленинградской области. Общая площадь арендуемых им лесов составляет около 200 тыс. га, которые в основном представлены эксплуатационными лесами. Предприятие арендовало на 49 лет лесные участки в Тихвинском и Бокситогорском районах Ленобласти.
В основе работы Тихвинского КЛПХ лежит соблюдение международных принципов устойчивого развития, которые предусматривают ответственный и основанный на этических принципах подход к экономическим и социальным вопросам, а также проблемам окружающей среды.
С 2007 года Тихвинский КЛПХ владеет лесным сертификатом FSC по лесоуправлению.
Производство на современном уровне
Задачи снизить влияние человеческого фактора на производственный процесс и повысить объем выпуска продукции актуальны для многих фанерных предприятий. Один из путей решения этих задач − автоматизация производства с одновременным уменьшением затрат сырья и сокращением издержек. На «UPM Чудово» это хорошо понимают.
Гидротермическая обработка древесины необходима для обеспечения пластичности древесины с целью повышения качества окорки и уменьшения глубины трещин, которые образуются на внутренней стороне шпона при лущении. Сырье подается со склада в бассейны (вместимость каждого бассейна − 1000 м3) для гидротермической обработки, где выдерживается при температуре 40−50° С в течение 20−24 ч. Перед подачей на окорку в станок Valon Kone VK32SX каждое бревно измеряется сканером «ВЕКТОР 2010», при помощи которого одновременно с функцией учета сырья выполняется и оптимизация раскряжевки для получения сортимента нужного размера − чурака для лущения. Источники лазерных лучей установлены через каждые 1330 мм. По свету лазерных лучей оператор видит, как правильно раскроить бревно. Для получения лущеного шпона из чурака на заводе установлены линии лущения, рубки и укладки шпона. Процесс лущения шпона на станке Raute VS 600×1400 начинается с ЦЗУ, которое обеспечивает центровку и подачу чурака в зону лущения. От его четкой работы зависит процент выхода шпона из чурака.
Для перемещения ленты шпона от станка к участку рубки используют ленточные конвейеры. Подают ленту шпона в роторные ножницы Raute RC-1800 с помощью подающего стола. При движении ленты по столу в шпоне с помощью датчиков выявляются дефекты, которые вырубаются ножницами. Датчики определяют также границы ленты шпона и дают команду ножу на прирубку передней и задней кромок. Получаемые после лущения чурака кусковые отходы или шпон-рванина направляются в барабанную рубительную машину Raute TR 1020−1300.
После лущения сырой шпон должен быть сразу высушен. На предприятии шпон требуемой влажности получают в двух газовых сушилках Raute YST-480 (производительность каждой − около 8 м3/ч сухого шпона) и одной паровой сушилке. Заданный режим сушки соблюдается и контролируется автоматической системой с помощью встроенных датчиков. В автоматических сортировках Raute сухой шпон из камеры попадает на поперечный конвейер. Оператор визуально оценивает сорт каждого листа и нажимает на пульте управления кнопку с номером соответствующего «кармана», куда эти листы поступают. Приборы камеры Mecano оценивают сорт каждого листа, а механизмы автоматически направляют его в нужный «карман».
После сушки и сортировки листы шпона с дефектами отправляют на линии сращивания, ребросклеивания − и починки, где установлены четыре линии сращивания Raute с усовочными станками VS-1600 и прессами JPL–1700, две линии ребросклеивания VS 1010 и одна линия ребросклеивания VT 2080.
В 2009 году впервые в России на заводе «UPM-Чудово» была установлена одна из последних разработок компании Raute − автоматизированная линия Raute P4 4×4-ft для удаления (вырубки) дефектов листов шпона; производительность этой линии − 3,5 м3/ч.
Достоинства линии: повышение качества и увеличение объема шпона, пригодного для склеивания; минимальная потребность в рабочей силе − для обслуживания линии достаточно одного оператора; высокая точность починки, выбор форм для вставки (5−6 видов). О производительности линии говорит такой факт: одна починочная головка заменяет два-три починочных станка.
Установленный на линии VDA-сканер оснащен интерфейсом, отображающим в режиме реального времени необходимую информацию для определения сорта и размеров листа шпона. Сканер распознает виды дефектов и их размеры, учитывает их количество. На линии также установлены датчики по определению шероховатости и волнистости шпона. Цветной VDA-сканер обнаруживает засмолки и «кармашки» с большей точностью, чем черно-белые сканеры. Магазин ленточек шпона, используемых для вставок, пополняется без остановки работы линии. По словам Александра Кирпичникова, главы московского представительства ООО «Рауте Ою», «плотное прилегание штампа к листу шпона при вырубке дефекта обеспечивает нулевую фаску и тем самым сохраняет прямолинейность листа после починки».
Наборка пакетов шпона для последующего склеивания фанеры осуществляется на автоматических станциях набоки пакетов Plytec SGF4×8. К месту наборки листы шпона поочередно подаются автоматически, где оператор укладывает их в пакеты и стопу. Алгоритм подачи шпона может быть выбран либо из 99-ти записанных в память рецептов наборки, либо задан оператором самостоятельно в зависимости от характеристик продукции, которую необходимо получить. Это не только ускоряет процесс наборки, но и позволяет повысить качество управления и контроля, а так же более гибко реагировать на требования конечного заказчика к продукции.
Сформированные стопы набранных пакетов по команде оператора автоматически направляются на операцию прессования. Автоматика и тут управляет процессом, отвечая за логическую очередность перемещений стоп, что позволяет максимально сократить временные издержки и увеличить эффективность использования оборудования при минимальной потребности в рабочей силе.
Затем оператор подает пакеты шпона для склеивания на транспортер, установленный перед горячим прессом Raute VPH 30 1400×2700. Режим склеивания устанавливается автоматически, в зависимости от заданной толщины конечной продукции.
Для обеспечения чистового раскроя по формату листы фанеры обрезают с четырех сторон круглыми пилами с твердосплавными напайками на линии форматного раскроя производства австрийской компании Schelling.
По словам Александра Космина, специалиста компании ООО «Шеллинг+Сервис», модель форматно-раскроечного центра марки FP, которая эксплуатируется на заводе в Чудово, не новая, но отдельные узлы в ней постоянно совершенствуются, что обеспечивает высокую производительность при почти полной автоматизации процесса раскроя.
В линии форматной обрезки, установленной в 2007 году на заводе «UPM-Чудово», загрузка пакета листов фанеры осуществляется податчиком с вакуумными присосками. Этот метод позволяет максимально исключить механические повреждения листов фанеры при подаче на загрузочный стол. Одним из плюсов вакуумной загрузки является скорость набора пакета для раскроя, которая в полтора-три раза выше, чем при механическом сдвиге листов с подающего стола на загрузочный стол.
После подачи листов с загрузочного стола на промежуточный (роликовый) происходит предварительное продольное выравнивание пакета, что актуально при работе с листами фанеры, имеющими большой свес.
При первоначальном раскрое пакета в продольном направлении предусмотрена возможность остановки при выполнении реза. Это необходимо для удаления узкой обрезки и предотвращения ее попадания при последующих резах между листами пакета и внутрь пильной каретки во избежание повреждения ремней вращения и подшипников подвески пильной каретки линии.
Г-н Космин отмечает, что торцовка любой ширины с фронтальной стороны пакета возможна почти на любом форматно-раскроечном станке или линии, а торцовка тыльной стороны пакета на линии Schelling выполняется с помощью прижимной балки и каретки подачи с захватами, удерживающими пакет фанеры.
Подача пакета для обработки в размер выполняется в два приема, что обуславливает максимальную точность позиционирования. Для получения перпендикулярного реза при раскрое по заданному формату используется система двухступенчатого выравнивания пакета листов фанеры. Сначала создают базу для последующего раскроя пакета с помощью выравнивателя, установленного внутри промежуточного стола. Расстояние для предварительного выравнивания определяет оператор линии. Затем пакет обрезают до требуемого размера. Для предотвращения заклинивания пильного диска во время раскроя пакета оператор выбирает режимы скоростей движения пильной каретки: отдельно указывает скорость входа пильного диска в пакет, скорость «чистового» раскроя и скорость выхода из пакета. Оператор выбирает скорость согласно диаграмме нагрузки на мотор основной пилы; диаграмма нагрузки постоянно отображается на мониторе пульта управления при выполнении раскроя.
Для управления работой автоматики линии используется стандартный программируемый логический контроллер производства Siemens Simatic серии Step 3.
Указанные выше технологические особенности линии обеспечивают производительность форматно-раскроечного центра с высотой раскраиваемого пакета до 80 мм в пределах 5−7 м3/ч.
После операции форматной обрезки фанеру шлифуют и отправляют на склад готовой продукции для упаковки и отгрузки потребителям.
В конце 2010 года в дополнение к имеющемуся прессу для ламинирования Raute VPP 16 1450×2700 на заводе установили еще один − производства компании INFOR.
Лущеный шпон является не только полуфабрикатом для изготовления фанеры. Это также самостоятельный вид товарной продукции, используемой обычно в мебельной промышленности для облицовывания щитов и получения клееных деталей, а также в ряде других производств, где в целях экономного расходования сырья рациональнее использовать именно шпон, а не пиломатериалы. Поэтому, помимо основного производства − выпуска фанеры, на предприятии с 2003 года действует линия производства шпона, предназначенного для нужд мебельной промышленности. Инвестиции в проект, который реализовали в короткие сроки, составили 13,8 млн евро. Это единственная в нашей стране линия получения тонкого (толщиной от 0,6 мм) лущеного березового шпона. Производительность линии − до 6 тыс. м3/год. Кроме того, сейчас на этом оборудовании в Чудово производят также конструкционный шпон толщиной от 1 до 1,5 мм − 4 тыс. м3/год.
На заводе установлена одна линия по производству лущеного шпона. Технологический процесс включает следующие операции. После гидротермической обработки бревна проходят обязательную окорку на станке Valon Kone и обмер системой «ВЕКТОР», которая одновременно с функцией учета сырья выполняет и оптимизацию раскряжевки для получения сортимента нужного размера − чурака для лущения. Чурак подается в лущильный станок Raute PCLT 3300 для получения ленты шпона с ее последующей рубкой в размер роторными ножницами. Затем листы сырого шпона сушат в паровой сеточной сушилке модели Raute VMS 3600. Сортировка сухих листов шпона по сортам и их упаковка производятся вручную.
Товар лицом
Продукция предприятия поставляется как на внутренний, так и на международный рынок. Около 75% выпускаемого товара завода идет на экспорт, преимущественно в Скандинавские страны и другие страны Европы, а также в США и Китай.
В 2001 году предприятие «Чудово-RWS» получило право маркировать свою продукцию с использованием торговой марки WISA.
На сегодняшний день завод выпускает три вида продукции: ламинированную березовую фанеру WISA Form Birch, фанеру WISA Wire с поверхностью «сетка», березовую фанеру ФСФ шлифованную WISA Birch с размерами листов 1220 х 2440 и 1250 х 2500 мм (толщина фанеры − от 5,2 до 30 мм). О том, насколько востребован этот материал, красноречиво говорит хотя бы такой факт: при строительстве зданий «Москва-Сити», храма Христа Спасителя, нескольких станций Московского метрополитена, а также атомной электростанции в Воронеже опалубку для бетонных работ делали из чудовской фанеры. При производстве фанеры на «UPM-Чудово» используют смолу производителя Momentive, которая при склеивании позволяет получить высококачественный прочный и малотоксичный клееный материал (класс эмиссии формальдегида Е1).
Фактическое количество выделяемого свободного формальдегида − менее 0,1 мг/м2•ч, что намного ниже норматива, определенного стандартом EN 717−2 (метод газового анализа): менее 3,5 мг/м2•ч. Треть выпускаемого объема фанеры облицовывается только финскими пленками (плотностью 145, 167 и 220 г/м2) от производителя Imprex, пропитанными фенолоформальдегидными смолами. С 2007 года на предприятии стали выпускать новый вид продукции − фанеру марки LNG, предназначенную для производства танкеров для перевозки сжиженного природного газа (Liquid Natural Gas). Эта фанера выпускается в соответствии со стандартом GT96 и характеризуется повышенной атмосферостойкостью.
Качество всей продукции, которое проверяют в лаборатории завода и независимых экспертных организациях, соответствует российским (Госстандарт) и международным (ISO 9001 и ISO 14001) стандартам. Кроме того, продукция прошла международное сертифицирование в центрах VTT (Финляндия), DIN Otto Graf (Германия) и GTT (фанера для газоналивных танкеров).
Вопросы экологии
Особое внимание на «UPM Чудово» уделяют вопросам экологии и защиты окружающей среды. На предприятии действует замкнутый цикл водо-оборота, произведена реконструкция очистных сооружений, работает котельная для сжигания древесных отходов, воздух из системы вентиляции проходит через воздухоочистные сооружения. Российское агентство «Эксперт РА» присвоило заводу рейтинг Eco, А за экологические показатели.
Часть отходов (отторцовка, забракованное сырье и отходы лущения), не востребованных заводской котельной установкой, перерабатываются в щепу и поставляются на расположенный неподалеку завод древесных плит ООО «Флайдерер» и на целлюлозно-бумажные заводы компании UPM в Финляндии.
В 2003 году введена в эксплуатацию установка по брикетированию пыли и мелкой фракции щепы. Отсев и кора вместе с готовыми древесными брикетами экспортируются в Финляндию и там перерабатываются для получения тепловой энергии. Кусковые отходы фанерного производства измельчают в щепу, которую используют в качестве сырья для изготовления целлюлозы на заводах концерна UPM-Kymmene в Финляндии.
Екатерина МАТЮШЕНКОВА
Автор благодарит руководство ООО «ЮПМ-Кюммене Чудово» за помощь в подготовке публикации. Отдельная благодарность начальнику производства ООО «ЮПМ-Кюммене Чудово» Андрею Петрову, директору по корпоративным коммуникациям компании UPM-Kymmene Russia Наталии Малашенко и директору по продажам компании UPM-Kymmene Russia Александру Тоцкому
Справка
Компания UPM владеет шестью фанерными заводами и двумя заводами по производству шпона в Финляндии, фанерными заводами в России и Эстонии. «UPM Чудово» входит в подразделение «UPM Фанера» компании UPM-Kymmene Oy. Объем продаж «UPM Фанера» в 2009 году составил 306 млн евро.