Эти удивительно полезные ДВП
Мы продолжаем знакомить читателей с разновидностями плитных материалов. Сегодня мы расскажем о мягких древесно-волокнистых плитах (ДВП) и их весьма полезных качествах.
Древесные плиты подразделяются на стружечные и волокнистые. Стружечные плиты изготавливают из стружки, волокнистые − из древесного волокна. Стружку получают резанием древесины, волокно − истиранием древесного сырья. Естественно, истирание более энергоемкий процесс, чем резание. Волокнистые плиты, в свою очередь, четко различаются по плотности: пористые (изоляционные, мягкие) плиты, плиты средней плотности (MDF) и твердые плиты (HDF).
В соответствии с европейским стандартом EN 622−4, устанавливающим требования к мягким ДВП, различают пять марок этого плитного материала: SB − общего назначения, SB.H − общего назначения влагостойкие, SB.E − общего назначения атмосферостойкие, SB.LS − конструкционные, SB.HLS − конструкционные влагостойкие. Сведения о требованиях к физико-механическим свойствам мягких ДВП представлены в табл. 1.
ДВП
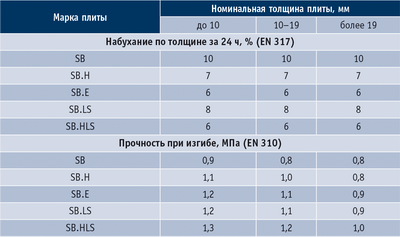
Таблица 2. Характеристики мягких ДВП марки «Изопанель»
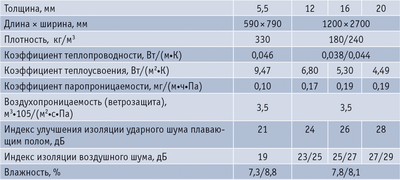
Автору публикации известно только одно предприятие в России, выпускающее мягкие ДВП − Княжпогостский завод ДВП. На российском рынке представлены импортные изоляционные ДВП с открытой диффузией − THD, DWD, UDP, TEP системы Agepan, которые производит компания Glunz (Германия), мягкие древесно-волокнистые плиты «Софтборд» от компании Woodway Group, а также изоляционные экологические плиты Vital из древесных волокон с использованием вискозы, которые изготавливает финская компания Vital Finland Oy.
В частности, ООО «Платан» предлагает мягкие ДВП, характеристики которых представлены в табл. 2.
Мягкие и твердые ДВП изготавливают «мокрым» способом. Исходное сырье − крупные кусковые отходы деревообработки, неделовые лесоматериалы − в рубительных машинах превращается в технологическую щепу, т. е. куски длиной 20−60 мм. Предприятия могут работать и на привозной щепе с лесопильных предприятий. Далее щепа моется и сортируется для удаления посторонних включений, затем поступает в установку горячего размола (УГР). Там сырье прогревается паром с температурой до 180 °С, при которой наступает плавление лигнина, и прочность древесины, особенно поперек волокон, значительно снижается. Затем прогретая щепа подается в дефибратор, где древесина размалывается на волокна и пучки волокон. Для получения качественных плит часто требуется и вторая стадия измельчения в рафинаторах, где происходит дополнительное истирание древесины и разрушение пучков на отдельные волокна. В результате получается волокнистая масса с частицами, длина которых примерно в 100 раз больше толщины. Такое соотношение размеров порождает основное свойство волокнистой массы − способность к переплетению волокон, «свойлачиванию», что позволяет в производстве волокнистых плит обходиться без использования связующих.
Далее волокнистая масса поступает в массный бассейн, в котором смешивается с водой (в пропорции примерно 1:100) и различными добавками.
Из бассейна смесь поступает на отливную машину, где волокнистая масса обезвоживается за счет свободной фильтрации через сетку. При фильтрации взвешенные частицы сближаются и переплетаются, возникают силы сцепления волокон друг с другом. После фильтрации концентрация массы увеличивается до 8−10%. Воду из массы продолжают удалять с помощью вакуумных отсосов и механического отжима, что приводит к повышению концентрации до 30−35% (то есть до влажности 65−70%).
После формирования волокнистого «ковра» и его резки на плиты нужного размера заготовки отправляются по разным адресам, ведь технологии изготовления твердых и мягких плит существенно различаются. Твердые плиты (толщиной 3,2 мм) получают в горячем многоэтажном прессе, где проводится отжим влаги из «ковра», сушка древесных волокон и собственно прессование на сетчатых поддонах.
Мягкие плиты не требуют прессования. Сырые заготовки сразу подаются в проходную сушилку. Используются трехзонные многоэтажные роликовые сушилки непрерывного действия, работающие по принципу противотока с рециркуляцией теплоносителя. Длина роликовых сушилок может колебаться от 30 до 90 м. Продолжительность сушки при температуре теплоносителя 130…160 °С составляет 3 ч. В конце процесса сушки предусмотрена операция охлаждения. Конечная влажность продукции составляет 8−12%. В результате получаются легкие плиты, обладающие прочностью, достаточной для выполнения всех послепрессовых операций с этим материалом.
Следует отметить, что производство ДВП энергоемко. В среднем на одну тонну плит затрачивается 550…650 кВт•ч электроэнергии, 4…4,5 т пара и около 110 кг условного топлива. Высокая энергоемкость процессов объясняется большими затратами электроэнергии на размол древесины. В процессе производства затрачивается значительное количество топлива на тепловую обработку сырья и сушку волокнистого «ковра».
Изготовленные из натуральной древесины изоляционные ДВП сочетают эффективные тепло-, термо- и звукоизоляционные свойства с высокими параметрами экологической безопасности, удобны и просты в монтаже, практичны в эксплуатации и имеют широкую сферу применения. Они могут быть использованы:
- для наружной обшивки стен (плиты, которые между собой соединяются системой «паз+гребень», выступают в качестве основы для последующей отделки «дышащими» штукатурками или сайдингом, при этом плиты представляют собой прекрасную ветрозащиту);
- в качестве дополнительной теплоизоляции и инсталляционного уровня для обшивки внутренней стороны стен;
- для устройства кровли, где важны такие свойства изоляционных ДВП, как прочность, влагостойкость, высокая теплоустойчивость, способность аккумулировать тепло, малый вес.
Выпускаются и плиты для устройства пола «плавающим» способом, когда на уложенный плитный материал настилают финишное покрытие разного рода, вплоть до керамической плитки.
Аккумулирующие свойства материала избавят летом владельца жилья от затрат на охлаждение помещений в дневное время за счет сдвига фазы (более 10 ч) и вернут помещению накопленное в небольших количествах тепло (сдерживание амплитуды) в ночные часы.
Изоляционные плиты из ДВП изготавливаются без использования формальдегида и других синтетических добавок, поэтому они абсолютно безопасны для человека и не наносят вред окружающей среде.
Одно из важных достоинств мягких ДВП − умение впитывать и отдавать влагу. У необработанной древесины в зависимости от климатических условий устанавливается сбалансированный уровень влажности: при температуре 23 °С и относительной влажности воздуха 50% уровень влажности составляет 8−10%. Изоляционные плиты ДВП благодаря высоким показателям диффузии пара способны впитывать влагу до 20% от своего объема и потом отдавать ее, не теряя при этом изоляционных свойств. При низкой влажности в помещении накопленная плитой влага возвращается в помещение. Таким образом обеспечивается благоприятный климат в помещении, а на плитах не бывает конденсата.
Древесно-волоконная изоляция не нуждается во влагоизоляционном пластике и способствует естественному газообмену в жилых строениях. Компактность же структуры обеспечивается ее воздухонепроницаемостью.
Вследствие высокой пористости эти плиты по показателю теплопроводности относятся к классу «А» − классу высокоэффективных теплоизоляционных материалов с сообщающимися открытыми порами, теплопроводность которых менее 0,06 Вт/(м•К).
Изоляционная плита из ДВП сдерживает и минимизирует шум внутри помещения и не пропускает в него шум снаружи, эффективно решает вопросы воздушной и ударной звукоизоляции.
При использовании плит ДВП для изоляции внешней стороны здания стены не требуются специальные материалы для ветрозащиты.
Изоляционная система на основе натурального древесного волокна не выделяет токсичных веществ при воздействии высокой температуры. Плиты отличаются значительной инертностью горения и довольно долго не теряют несущей способности, за счет обугливания защищают несущие конструкции зданий, увеличивая время для экстренной эвакуации людей при пожаре.
Владимир ВОЛЫНСКИЙ