Измельченная древесина
Разновидности, области применения, способы получения
Каждое деревообрабатывающее предприятие неизбежно сталкивается с проблемой образования и рационального использования внушительных объемов древесных отходов.
В качестве вторичного сырья или специального полуфабриката используется несколько видов измельченной древесины (табл. 1).
Технологическая щепа
Требования к качеству технологической щепы установлены ГОСТ 15815-83, которым предусмотрены следующие марки щепы в зависимости от ее назначения:
- Ц-1, Ц-2, Ц-3 - для производства сульфитной и сульфатной целлюлозы, древесной массы, бумаги, картона;
- ГП-1, ГП-2, ГП-3 - для производства спирта, дрожжей, глюкозы и фурфурола, пищевого кристаллического ксилита;
- ПВ - для производства древесноволокнистых плит;
- ПС - для производства древесностружечных плит.
Качественные характеристики щепы зависят от ее марки (табл. 2).
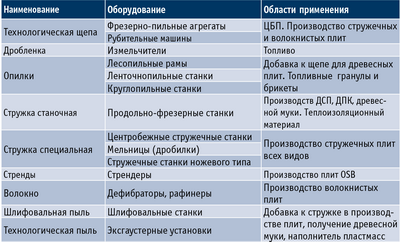
Таблица 2. Характеристики качества технологической щепы
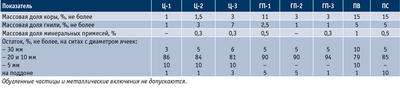

Рис. 1. Большой измельчитель MGB-Vario (Maier)
Как следует из приведенных данных, наиболее высокие требования предъявляются к щепе для целлюлозно-бумажного производства. Она должна быть получена из окоренной древесины и почти не содержать минеральных включений. Щепа для плитных производств может быть получена из неокоренного сырья, так как в ней допускается содержание коры до 15%. Размеры щепы: длина - 20-60 мм, толщина - до 30 мм.
Технологическая щепа из тонкомерных деревьев и сучьев приготовляется с соблюдением ТУ 13-735-83. В связи с тем, что ее качественные характеристики ниже, чем у щепы, приготовленной в соответствии с ГОСТ 15815-83, она используется только как добавка к стандартной щепе при изготовлении плитных материалов: до 20% от общего объема для наружных слоев стружечных плит и без ограничения - для внутренних.
Основным оборудованием для получения щепы являются рубительные машины (см. публикацию, посвященную этой технике, в «ЛПИ» № 3 (69), 2010 год). Крупные частицы могут дополнительно измельчаться до требуемых размеров в специальных малых рубительных машинах, называемых дезинтеграторами.
В лесопильном производстве щепа может получаться как попутный продукт при обработке бревен и двухкантных брусьев на фрезерно-пильных агрегатах. В этих станках первым по ходу движения бревна (бруса) режущим инструментом являются конические фрезы, которые превращают цилиндрическую часть бревна в щепу.
Рубительные машины могут использоваться также для измельчения древесных отходов и технологического сырья на так называемую дробленку - куски случайной формы и размеров (но не более определенного заданного размера) для использования в качестве топлива. К дробленке предъявляются лишь два требования: сыпучесть и сравнительно невысокая влажность (20-30%). В связи с этим нужно упомянуть о специальных станках - измельчителях древесного утиля (crashers). Образец такого оборудования представлен на рис. 1.
Они созданы для подготовки крупных изделий из древесины (отслуживших свое дверей, окон, мебели, шпал и пр.) к измельчению путем разбивания на крупные куски (длиной 100-500 мм) специальными зубьями, приваренными к жесткому валу. Из такого материала невозможно получить качественную щепу, поэтому он идет исключительно на дробленку, которая используется затем как топливо.
Подготовка щепы, особенно привозной, к дальнейшему измельчению требует ее обязательной сортировки, а иногда и мойки. Сортирование выполняют на ситовых сортировках, которые позволяют отделить от кондиционной щепы крупные куски и мелочь. Щепу моют при производстве волокнистых плит и плит MDF - это позволяет увеличить и стабилизировать влажность щепы и избавиться от возможных минеральных загрязнений.
Стружка
Стружку на деревообрабатывающих производствах изготавливают специально, в основном для производства стружечных плит, а также получают в качестве попутной продукции на продольно-фрезерных станках (фуговальных, рейсмусовых, четырехсторонних). Различают два вида стружки специального изготовления - полученную прямым резанием крупных древесных отходов или технологического сырья и полученную дополнительным измельчением технологической щепы.
Резаную стружку изготавливают на специальных стружечных станках с ножевым валом (среди отечественного оборудования можно привести в качестве примера станки ДС-6 и ДС-8 Новозыбковского завода). У резаной стружки стабильная толщина фрагментов. Для наружных слоев стружечных плит требуется дополнительно измельчать стружку в мельницах или рафинерах. Это оборудование отличается от стружечных станков тем, что дополнительное измельчение в нем достигается при помощи не только резания, но и истирания крупных частиц стружки, в результате чего отдельные стружки делятся продольно и достигают ширины, которая необходима по технологии.
Игольчатую стружку получают в центробежных станках - в основном путем деления щепы в направлении вдоль волокон. Частицы толщиной 0,3-0,5 мм подходят для изготовления среднего слоя трехслойных плит или однослойных плит, а частицы толщиной менее 0,3 мм - для наружного слоя плит ДСП. И хотя у плит из игольчатой стружки рыхлые кромки, они обладают хорошей формостабильностью. Слишком крупную игольчатую стружку можно дополнительно измельчать в мельницах или рафинерах. Самые подходящие породы для изготовления стружечных плит - сосна и ель. При их использовании получаются плиты высшей прочности благодаря хорошей деформативности хвойной древесины, а также возможности получать из нее гладкую и ровную стружку.
Для изготовления плит OSB требуется плоская стружка, получаемая на специальных станках только из крупномерного сырья. Наилучшим сырьем считаются круглые лесоматериалы мягколиственных пород, особенно осина, однако используются также сосна, ель, пихта, лиственница.
Твердолиственные породы не рекомендуются, поскольку в процессе подготовки они дают слишком много мелкой фракции. По той же причине в производстве плит с крупномерной стружкой почти не используются отходы лесопиления.
В производстве волокнистых плит, как и в производстве стружечных, исходным материалом служит технологическая щепа, но получают ее из древесины, не подвергавшейся искусственной сушке. В технологическом процессе используется щепа без мятых кромок с длиной частиц 10-35 мм (оптимальной - 20 мм), толщиной не более 5 мм и углом среза 30-60°. Для ДВП, которые изготавливаются мокрым способом, рекомендуется хвойная древесина; для плит, которые производят сухим способом, предпочтительны лиственные породы. Если же в процессе производства одновременно используются (смешиваются) разные породы, то желательно вводить в волокнистую массу упрочняющие добавки.
Сырьем для заводов и цехов, выпускающих плиты MDF, служат в основном круглые лесоматериалы и отходы лесопиления лиственных и хвойных пород.
Из легкой древесины хвойных пород получают светлые плиты высокого качества. Также для изготовления плит MDF используется щепа, получаемая как попутный продукт на лесопильных заводах с современными фрезернопильными брусующими агрегатами, и станочная стружка и опилки.
Станочная стружка может образовываться при обработке массивной древесины в объеме до 20 % от объема сухих пиломатериалов (например, в производстве оконных и дверных блоков, покрытий пола, мебели из массивной древесины). Особенность этих отходов - невысокая влажность (6-10 %) и неплоская форма.
Последнее обстоятельство не позволяет использовать станочную стружку непосредственно в производстве стружечных плит, только после ее доизмельчения в мельницах для получения мелкой фракции наружных слоев ДСП. Станочная стружка является также отличным теплоизоляционным материалом, ее используют и как сырье для изготовления топливных брикетов, древеснополимерных композитов.
Опилки в лесопильном производстве составляют 10-12% от объема пиловочных бревен. Самые крупные опилки дают традиционные лесопильные рамы с толщиной пил до 2,5 мм, самые мелкие - ленточнопильные станки с толщиной пил до 1,2 мм. Как самостоятельный полуфабрикат опилки не используются в производстве древесных плит ввиду малого отношения длины фракций к их толщине.
Однако их можно добавлять к сырой стружке внутреннего слоя стружечных плит в объеме до 30 %. Другие области применения опилок - производство волокнистых плит, древеснополимерных композитов (ДПК), топливных гранул (пеллет). Используются они и в качестве теплоизоляционного материала в строительстве, добавки к глинистым почвам при рыхлении, а также как топливо.
В столярномебельном производстве большое количество опилок образуется на участке продольного раскроя пиломатериалов. Эти опилки отличаются от лесопильных низкой влажностью (обычно 10-12 % против 30-50 %), но применяются в тех же областях.
Сухие стружки и опилки - отличное сырье для получения древесной муки (размер частиц - не более 1 мм), которая находит широкое применение в качестве наполнителя пластмасс, добавки к краскам и клеям, основного компонента ДПК, а также используется для производства разных других материалов.
Технологическая пыль фракции 0,5/0 используется при изготовлении внутреннего слоя стружечных плит, фракции 0,25/0 - для получения наружных слоев ДСП. При объемной массе пыли 100-250 кг/м3 ее удельная поверхность составляет от 5 до 40 м2 на 100 г. Доля пыли в стружечной массе может доходить до 50 %.
Шлифовальная пыль состоит из частиц размером от 0,01-0,1 до 0,5-1,0 мм. Ее можно добавлять к стружке наружных слоев в количестве, составляющем 20-25 % от массы плиты. Но при этом расход связующего увеличивается на 10-20 % (по сравнению с технологией, в которой шлифовальная пыль не используется) и возникает опасность образования комков из пыли, пропитанной смолой, изза которых на плите могут возникать смоляные пятна.
Сухая древесная пыль - материал взрывоопасный, поэтому у бункеров для пыли должны быть установлены системы увлажнения.
Для получения щепы, стружки и древесного волокна используется несколько принципиальных схем основного оборудования (табл. 3).
Полную версию статьи (с таблицами и иллюстрациями) смотрите в PDF-версии журнала.
Владимир ВОЛЫНСКИЙ