Перспективы развития производства древесных плит в России
Предлагаем вниманию читателей текст доклада генерального директора ЗАО «ВНИИДРЕВ» Александра Шалашова на конференции «Деревообработка в России: лесопиление, плитное и мебельное производство», проходившей в рамках XIII Петербургского Международного лесного форума.
Рисунок 1. Производство ДСП в 2011 году в сравнении с 2010 годом
Рисунок 2. Производство ДВП в 2011 году в сравнении с 2010 годом
Рисунок 3. Производство фанеры в 2011 году в сравнении с 2010 годом
Рисунок 4. Динамика изменения средних цен на древесностружечные плиты
Рисунок 5. Динамика изменения средних цен на древесноволокнистые плиты
Рисунки смотрите в PDF-версии журнала
В России общие мощности по производству древесных плит и фанеры составляют 13,2 млн м3 в год. Согласно статистическим данным, которые приведены в табл. 1 и содержатся в диаграммах (рис. 1-3), выпуск плит ДСП, ДВП и фанеры в 2011 году превышает показатели 2010 года.
Древесные плиты сегодня и завтра
Внутренний рынок древесных плит (за исключением рынка фанеры) не обеспечивается в должной мере отечественным производством. Поэтому его потребности удовлетворяются за счет импорта, составляющего до 1200 тыс. м3 в год. Спрос растет в среднем на 10% ежегодно. Экспорт относительно мал и осуществляется преимущественно в ближнее зарубежье. Такая ситуация стимулирует строительство заводов по производству древесных плит.
Производство фанеры превышает потребности внутреннего рынка, до 64% выпускаемого общего объема отправляется на экспорт. Рост спроса на этот материал в мире стимулирует развитие производства фанеры.
Спрос на плиты OSB полностью покрывается импортом и, по официальным данным, составляет до 400 тыс. м3 в год. Первый завод ООО «ДОК «Калевала» (Петрозаводск, Карелия) мощностью 500 тыс. м3/год начнет работать в 2012 году.Проекты строительства древесноплитных заводов инвестиционно привлекательны, но есть и сдерживающий фактор - довольно высокая стоимость таких проектов - 3-6 млрд руб. в зависимости от мощности и типа производства. Сроки окупаемости 5-6 лет при продолжительности строительства около полутора лет.
Предприятия по выпуску ДСП, MDF и ДВП используют низкосортную древесину и древесные отходы. Для изготовления фанеры необходима круглая древесина (специальный фанерный кряж), для плит OSB - балансы хвойные или осиновые. Необходимость в таком сырье предопределяет размещение древесноплитных производств в составе крупных лесопромышленных комплексов в лесоосвоенных регионах.
Неудовлетворенная потребность внутреннего рынка составляет: по ДСП - около 2,5 млн м3, по OSB - 1,2-1,5 млн м3, по MDF - 0,5 млн м3. Следует отметить, что отечественный рынок мал. Значительные ресурсы экономически доступного низкосортного древесного сырья потенциально позволяют интенсивно увеличивать производство древесноплитных материалов, но при условии выхода российских компаний на внешние рынки сбыта продукции.
Цены на древесные плиты в сравнении с ценами 2010 года продолжают расти (см. рис. 4-5).
В стадии строительства сейчас находятся 19 заводов с приростом мощностей на 2,75 млн м3/год (23%). Имеется 21 проект по новым заводам ДСП, MDF, OSB и фанеры мощностью 5,37 млн м3/год. Часть из них включены Минпромторгом России в перечень приоритетных в области освоения лесов.
Общий прирост мощностей по древесным плитам и фанере к 2015 году может составить 8,1 млн м3 (рост на 59%).
Прогнозируется насыщение внутреннего рынка с необходимостью выхода на внешние рынки сбыта. Подотрасль древесных плит в перспективе должна стать экспортно ориентированной - по аналогии с производством фанеры.
В лучшем положении находятся вновь созданные и создаваемые крупные заводы ДСП, MDF, OSB и ДВП, оснащенные современным оборудованием с прессами непрерывного действия.
Новые заводы создаются преимущественно на основе оборудования последних модификаций с ленточно-роликовыми прессами германских фирм Siempelkamp и Dieffenbacher.
Они составляют основу современных линий по выпуску плит ДСП, MDF, OSB, ДВП и LVL. При изготовлении плит на этом оборудовании уменьшаются объемы использования смолы, древесины, тепловой и электрической энергии. Продукция отличается стабильностью качества и при пониженной стоимости древесного сырья обладает конкурентными преимуществами на внешних рынках.
Перспективы отечественного производства древесных плит связаны со строительством подобных заводов мощностью от 200 до 700 тыс. м3/год. Постепенно отмирают производства, оснащенные оборудованием небольшой мощности 1960-1980-х годов.
и осваиваемые линии по производству MDF в России
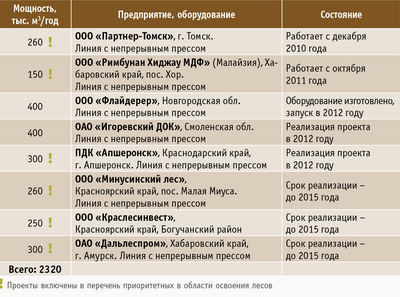
Таблица 3. Готовящиеся к строительству, строящиеся и
осваиваемые линии по производству ДСП в России
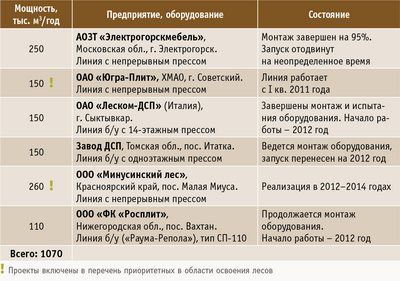
Сегодня плиты MDF выпускаются на семи линиях общей мощностью более 900 тыс. м3/год. Из них только три линии оснащены современным оборудованием с непрерывными прессами фирмы Siempelkamp.
Строятся или готовятся к строительству шесть линий по производству плит MDF (см. табл. 2).
Общее потребление плит MDF внутренним рынком в 2010 году составляло около 1,1 млн м3/год.
В период до 2015 года прогнозируется увеличение емкости внутреннего рынка в 1,5-2 раза - эта потребность будет полностью обеспечена новыми заводами.
Плиты ДСП в стране производят 47 линий общей мощностью 7370 тыс. м3/год. С непрерывными прессами работают пять производств общей мощностью 2160 тыс. м3/год - это около 40% общего объема производства.
Стране необходимы новые заводы по выпуску плит ДСП с современным оборудованием. По оценкам ЗАО «ВНИИДРЕВ», приемлемая экономическая эффективность предприятия обеспечивается при мощности завода ДСП с непрерывным прессом не менее 250 тыс. м3/год. Оптимальной является мощность от 350 до 500 тыс. м3/год. В ближайшие годы будут введены шесть линий ДСП (табл. 3).
Среди этих предприятий только три производства (общей мощностью 660 тыс. м3/год) оснащаются непрерывными прессами, что недостаточно для переоснащения подотрасли ДСП на новой технико-технологической основе и обеспечения спроса растущего внутреннего рынка. Поэтому до 2015 года на внутреннем рынке дефицит в плитах ДСП современного качества сохранится.
Экологическая безопасность при производстве древесных плит
Обостряется проблема обеспечения экологической безопасности древесных плит и мебели на их основе. В 2008 году изменением к ГОСТ 16371 для мебели введен норматив выделения формальдегида в воздух жилых помещений, равный 0,01 мг/м3 при испытании камерным методом по ГОСТ 30255. Такой же предельно допустимый уровень (0,01 мг/м3) выделения формальдегида в воздушную среду для мебели и плит утвержден решением № 299 Комиссии Таможенного союза стран ЕврАзЭС от 28 мая 2010 года.
Следует отметить, что западноевропейские стандарты на мебель предусматривают другой норматив выделения формальдегида - 0,124 мг/м3, что в 12,4 раза превышает российский для мебельной продукции. Правомерно предположить, что импортная мебель может не соответствовать требованиям ГОСТ 16371 по выделению формальдегида при испытаниях ее камерным методом. Об этом следует информировать потребителей.
и деталях мебели по результатам испытаний центра
«Лессертика»
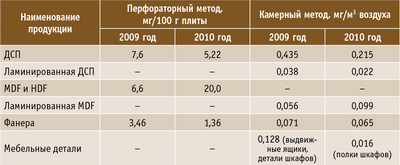
В г. Балабаново (Калужская обл.) по заказам отечественных предприятий проводятся испытания деталей мебели на предмет выяснения количества выделяющегося формальдегида с использование однокубовой климатической камеры. Среднестатистические результаты этих испытаний за 2009 и 2010 годы приведены в табл. 4.
Испытания показали, что количество формальдегида, выделившееся из выдвижных ящиков, а также полностью облицованных полок для шкафов, превышает норматив в несколько раз. Аналогичные испытания продолжаются в 2011 году, в том числе для полнокомплектных наборов мебели, в новой 30-кубовой камере, введенной в действие в конце 2010 года.
Выделение формальдегида из мебели определяется совокупностью трех факторов: содержанием формальдегида в древесноплитных материалах; изолирующими свойствами защитно-декоративных покрытий; полнотой покрытия поверхностей, кромок и технологических отверстий в деталях мебели.
Плиты Е-1 с содержанием формальдегида до 8 мг/100 г по перфоратору являются основным материалом для изготовления мебели, и потому класс Е-1 должен быть преобладающим в выпуске древесных плит. Перед производителями плит стоит задача: добиваться снижения содержания формальдегида до уровня не более 4,0 мг/100 г.
Облицовочные материалы должны обеспечивать сокращение выделений формальдегида в 12-15 раз по сравнению с существующими, для того чтобы уложиться в показатель 0,01 мг/м3 по формальдегиду. За последние 20 лет в составе декоративной пленки, используемой для ламинирования древесных плит, с целью экономии затрат массу бумаги сократили со 130 до 70-80 г/м2. В итоге ухудшилась изолирующая способность защитных покрытий. Соответственно, увеличилась эмиссия формальдегида через облицованные поверхности. Фактор влияния массы бумаги на эмиссию формальдегида требует специального изучения. Необходимо также продолжение НИР по модификации пропиточных смол для получения полимеров с более плотной трехмерной структурой, чем у применяемых сегодня. Методика определения изолирующих свойств пленочных материалов в этом году разрабатывается ВНИИДРЕВом, планируется применить ее для оценки качества покрытий.
Необходимо отметить, что ГОСТ 16371 на мебель допускает использование деталей из плит с необлицованными или не имеющими защитных покрытий невидимыми поверхностями и кромками щитов и без заделки технологических отверстий. В результате для свободного выхода формальдегида нет препятствий. Необходимо исключить эти допущения и внести изменения в мебельный ГОСТ.
Развитие производства древесных плит взаимосвязано с перспективой развития экспорта, и потому объективно необходимо ориентироваться на требования европейских и международных стандартов по эмиссии формальдегида. Внутренний рынок в ближайшие 3-5 лет будет заполнен плитной продукцией с учетом создаваемых мощностей по ДСП и MDF. Целесообразно будет экспортировать плиты в Западную Европу и Америку. И вот здесь на первый план выходит проблема эмиссии формальдегида.
Например, европейские стандарты EN-312 (ДСП), EN-622 (MDF) и EN-31986 (плиты для строительства) предусматривают для необлицованных древесных плит норматив эмиссии 0,124 мг/м3 воздуха по камерному методу. Этот показатель является основным критерием для экспорта-импорта древесноплитной продукции в странах Западной Европы. Аналогичное положение и в Северной Америке.
Этот норматив для необлицованных плит довольно жесткий. Чтобы уложиться в него, необходимо обеспечить среднее содержание формальдегида по перфоратору для ДСП не более 4,2 мг/100 г, для фанеры - не более 6,0 мг/100 г, для MDF - не более 3,8 мг/100 г. Это значительно меньше 8 мг/100 г, предусмотренных отечественными стандартами.
Несоответствие отечественной продукции европейским нормативам по эмиссии формальдегида будет препятствовать экспорту необлицованных плит ДСП, MDF, HDF и изделий из них. Следует отметить, что отечественная фанера в основном отвечает зарубежным стандартам по экологической безопасности и потому является экспортно ориентированным товаром.
Обеспечение современных требований по формальдегиду зависит от особенностей применяемых технологий и используемых связующих. Лучшие результаты достигнуты на современных линиях по изготовлению плит ДСП, MDF и ДВП, оснащенных ленточно-роликовыми прессами непрерывного действия, одноэтажными и сдвоенными прессами периодического действия. Для обеспечения гарантий экологической безопасности необходимо выдерживать стабильность всех параметров техпроцессов при налаженном производственном контроле, использовании статистических методов управления и эффективной системе менеджмента качества.
Известно, что для получения малотоксичных плит необходимы карбамидоформальдегидные смолы с мольным отношением формальдегида к карбамиду 1,1 и меньше. Из-за короткого срока хранения этих смол оптимальное расстояние для их доставки от производителя потребителю составляет не более 1000 км. Поэтому на крупных заводах древесных плит целесообразно создавать собственное производство низкомольных карбамидных смол с участками получения концентрированного формалина из метанола.
Для снижения токсичности ДСП в зарубежной практике при их изготовлении применяется система из двух смол с разными периодами отверждения для внутреннего и наружных слоев ковра: для наружных слоев - низкомольная, для внутреннего слоя - высокореакционная смола. Такой вариант с двумя смолами предлагается и фирмой «Метадинеа» из г. Губаха (Пермская обл.). Требуются относительно небольшие затраты на дооснащение производства ДСП емкостями для одновременной работы с двумя смолами.
В качестве варианта решения, способствующего снижению содержания и выделения формальдегида, а также расширению ассортимента плит, целесообразно применение меламиносодержащих связующих, обеспечивающих изготовление малотоксичных ДСП, а также плит влагостойких и повышенной прочности классов РЗ, Р5 и Р7 по европейскому стандарту EN 312.
Промышленность в настоящее время использует импортный меламин, что ведет к значительному удорожанию меламиносодержащих смол, предназначенных для изготовления древесноплитной продукции и импрегнирования декоративной бумаги. Сейчас проблема решается, началось создание мощностей по производству меламина. В ОАО «Невинномысский азот» (Ставропольский край) компания «Еврохим» монтирует установку мощностью 50 тыс. т/год, в ОАО «Тольяттиазот» готовится установка мощностью 20 тыс. т/год с последующим увеличением производительности до 40 тыс. т/год. Оба производства начнут работать к концу 2011 года.
Необходимо внести изменения в отечественные стандарты на древесные плиты, в том числе:
- в ГОСТ 10632 для необлицованных ДСП следует ввести показатель выделения формальдегида 0,124 мг/м3,
определяемый камерным методом, предусмотреть показатели для влагостойких, конструкционных и особо прочных плит; - в ГОСТ 53208 на плиты древесные моноструктурные необходимо изменить название и включить в этот стандарт ДВП высокой плотности, а также показатель выделения формальдегида.
Для ламинированных плит и фанеры надо ужесточить нормативы по выделению формальдегида. Нужны также национальные стандарты на влагостойкие огнестойкие плиты, ламинированные и окрашенные плиты MDF и ДВП и др. Требуется пересмотреть стандарты на методы определения экологической безопасности древесных плит, фанеры и мебели.
Сегодня сложилась парадоксальная ситуация: отечественные заводы, выпускающие древесные плиты и фанеру, работают на импортном европейском оборудовании по западноевропейским технологиям, используют идентичные зарубежным связующие, однако российские стандарты на продукцию существенно отличаются от европейских. Это приводит к сужению ассортимента и снижению конкурентоспособности российских компаний, затрудняет проведение экспортных сделок. Необходимо приведение в соответствие отечественных стандартов по ассортименту продукции и частично по экологическим требованиям с аналогичными европейскими и международными стандартами.
Полную версию статьи с таблицами и иллюстрациями смотрите в PDF-версии журнала.
Александр Шалашов,
генеральный директор ЗАО «ВНИИДРЕВ»