Новые технологии – новые возможности. В чем суть?
Торцовочная установка с функцией оптимизации – что это?
На многих заводах по разным причинам до сих пор используется технология, в соответствии с технологической цепочкой которой сначала выполняется выторцовка дефектов и только после этого пиломатериал раскраивается по длине. Возможно, станки, выполняющие эти функции, удовлетворяют потребности производителя и работают исправно, но... Наверняка ктонибудь из производственников задавался следующими вопросами: «Сколько времени занимает этот цикл и насколько эффективно использовано оборудование?», «Какое количество человек требуется для работы на таких станках, и как это отражается на операционной прибыли?», «Каков процент потерь пиломатериала (в объемах и в денежном выражении), уходящего в отходы в связи с неточностью раскроя?». Если ответы на эти вопросы удовлетворяют предпринимателя, то, наверное, стоит оставить все как есть. Но если нет, то есть смысл задуматься над новыми технологическими решениями, которые предлагает современный рынок деревообрабатывающего оборудования.
К примеру, лесопильный завод Worch, расположенный в г. Зангерхаузене (Германия), недавно приобрел торцовочный станок фирмы Dimter с целью решить проблему: применявшаяся до недавнего времени технологическая схема перестала справляться с возросшими объемами и повышенными требованиями заказчиков. Что же изменилось после покупки и пуска нового оборудования?
Теперь технологическая цепочка выглядит так. Ламели по ленточному транспортеру направляются на новую высокопроизводительную торцовочную установку Dimter OptiCut 200 Elite, на которой материал измеряется сразу на входе. «Для измерения ширины мы используем ультразвук. Длина распознается с помощью станции измерения, оснащенной приводным механизмом, исключающим проскальзывание материала. Линия оснащена на входе ленточным транспортером Vario, запатентованным фирмой Dimter, который максимально уменьшает наличие разрывов между досками, возникающие в процессе маркировки. Станок также оснащен системой управления OptiComDirect, которая позволяет установить прямую связь с ПК в офисе, за счет чего можно эффективно контролировать процесс производства вплоть до передачи карты раскроя в режиме онлайн непосредственно в систему управления станка. Эта система, исходя из данных измерения заготовки и карты раскроя, автоматически вычисляет размеры деталей, которые можно получить из этой заготовки. Использование системы позволяет существенно снизить количество отходов, а также отслеживать статистику производительности оборудования, в том числе и все необходимые данные по конкретному заказу. Эта установка обеспечивает одновременную выторцовку дефектов и раскрой материала по длине при сохранении высокой скорости подачи. При этом качество пропила отвечает всем требованиям заказчика». (По материалам издательства Holzkurier)
После OptiCut 200 Elite отторцованный материал перемешается на семь буферных станций и штабелируется работниками. В среднем, через новую линию на заводе Worch проходит около 2500 м3 пиломатериалов в год.
Высококачественные клеевые швы и ровная поверхность при производстве столярного щита. Какие предложения для малых и средних предприятий?
На международной выставке Ligna 2011 фирма Dimter представила новую модель пресса ProfiPress L II с автоматической системой загрузки. Эта установка компактной конструкции, использующая токи высокой частоты, может с успехом эксплуатироваться всеми производителями высококачественного щита из массивной древесины. «Наилучшим образом она подходит для малых и средних предприятий», - отмечают специалисты фирмы Dimter. Благодаря короткому периоду времени на переоснастку оборудования изготовление щита даже при условии часто меняющихся размеров плит остается рентабельным.
Одной из особенностей нового пресса является эффективное воздействие токов высокой частоты на клеевой шов, что сокращает расход энергии в процессе изготовления продукции за счет сокращения времени рабочего цикла прессования и обеспечивает при этом полное отверждение швов сразу после выгрузки из пресса. Благодаря этому обеспечивается эффективный контроль качества продукции. Точные, почти скрытые швы обеспечивают высокое качество столярного щита. Изготовленный щит сразу же можно отправлять на дальнейшую обработку. Еще одним существенным достоинством этой технологии является то, что в процессе прессования нагревается только сам шов, остальная часть древесины не подвергается воздействию высокой температуры, в результате в заготовке не возникает напряжение.
Вряд ли возможно достичь постоянно высокого качества плит при ручном клеенанесении с минимальным сдвигом и приемлемыми расходами. При использовании пресса PPL II гарантируется требуемое выравнивание ламелей во время прессования для того, чтобы обеспечить наименьший сдвиг по высоте и ровную поверхность. Таким образом, отпадает необходимость в последующей затратной обработке щита, такой как, например, рейсмусовые работы. В результате выход продукции существенно увеличивается.
У модели PPL II автоматическая система выгрузки пресса. Пресс может быть снабжен разными вариантами системы загрузки (ручная/автоматическая) и клеенанесения.
Изготовление сращенных ламелей в объеме до 25 тыс. пог. м в смену - это реально!
Компании Lilleheden (г. Хиртсхальс, Дания), которая является одним из крупнейших производителей многослойной клееной древесины в Северной Европе с объемом производства около 40 тыс. пог. м сращенных ламелей (еловая древесина) в день, требовалась линия сращивания, способная обеспечить необходимую производительность и сохранить качество выпускаемой продукции. У компании Lilleheden уже имелся положительный опыт работы с фирмой Weinig GreСon, поставившей Lilleheden пять лет назад механизм загрузки и пресс для установки после имевшейся на тот момент линии шипового сращивания. Поэтому руководство компании приняло решение перевести всю линию шипового сращивания на установки Weinig GreСon. Задача была непростой, так как более мощную, чем то оборудование, которое использовалось ранее, линию необходимо было с высокой точностью вписать в площадь действующего цеха. Помимо этого, согласно пожеланиям заказчика, установка должна была отвечать весьма высоким требованиям относительно рабочих параметров. Поставленные задачи решались на основе недавно разработанной высокопроизводительной линии шипового сращивания TurboLH. В процессе доработки были изменены основные рабочие параметры оборудования, а именно: на линии стало возможным обрабатывать заготовки толщиной до 50 мм (ранее - до 25 мм), шириной до 260 мм (75 мм) и длиной заготовок на входе до 5,2 м (2 м).
В результате компания Lilleheden получила возможность изготавливать сращенные ламели для производства клееных конструкций длиной до 24 м с производительностью до 25 тыс. пог. м в смену.
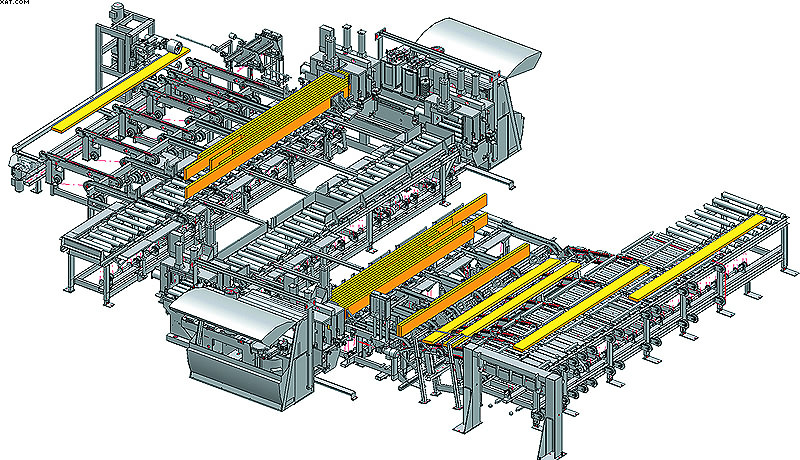
Высокопроизводительная линия шипового сращивания Turbo-LH на заводе компании Lilliheden
Возможно ли достичь скорости прессования ламелей при шиповом сращивании до 160 м/мин?
Перед деревообрабатывающим предприятием Bullinger (г. Нойруппин, Германия) стояла задача повысить мощности имеющегося производства. Специально для него фирма Weinig GreСon разработала и изготовила проходной пресс новейшего поколения, предназначенный для использования в производстве клееных конструкций. Согласно технологической цепочке, заготовки непрерывно подаются в продольном направлении на загрузочный стол, где они соединяются и затем запрессовываются на скорости до 160 м/мин. Проходной пресс оснащен толкателем и тормозным устройством, которые при дифференцированной скорости дают постоянно контролируемое усилие прессования в 115 кН или 11,5 т благодаря тяжелым цепным приводным механизмам. Тормозной путь между механизмом подачи и прессом обеспечивает соблюдение предписанного времени цикла прессования, сообщают в фирме GreСon. После запрессовки ламели раскраиваются при помощи плавающей торцовой пилы (без остановок) на нужную длину. Изменение размеров происходит автоматически, без вмешательства оператора.
По материалам ООО «Эдис-Групп», официального представителя компании Weinig
www.edisgroup.ru
www.weinig.ru