Череповецкий фанерно-мебельный комбинат (ЧФМК)
Территория заботы
Прекрасное своей одухотворенностью слово «забота» как-то исподволь уходит если не из нашей жизни и языка вообще, то из официальных и деловых текстов точно. Разные новомодные «вызовы» и «лидеры рынка» - это пожалуйста. Но отчего-то забывают, что человек, стремящийся твердо стоять на земле и думающий о будущем - не только собственном, но и своих детей и детей их детей, - просто обязан заботиться о том, что делает и что делается вокруг него. Между тем, именно слово «забота» то и дело приходило в голову нашим корреспондентам во время разговора с сотрудниками Череповецкого фанерно-мебельного комбината.
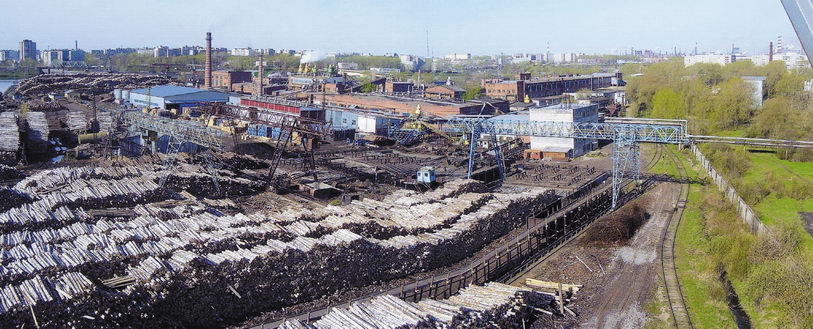
Прежде и теперь
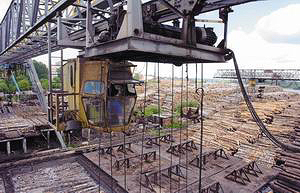
История Череповецкого фанерно-мебельного комбината начиналась странным, почти невероятным для советской плановой экономики, образом: едва в Череповце начали строить спичечную фабрику, как вслед за возведением первого же цеха назначение предприятия было изменено: оно стало фанерно-трубным заводом и до 1956 года выпускало фанерные трубы, используемые для линий электропередач, шахтных опор, производства мебели и стульев. А в 1958 году на базе фанерно-трубного завода был образован завод «Фанеродеталь», проведено комплексное опробование смонтированного оборудования и выпущена первая партия фанеры. Этот момент и принято считать днем рождения Череповецкого фанерно-мебельного комбината.
В 1960 году запущен в эксплуатацию цех по производству древесно-стружечных плит экструзионного прессования, а уже в следующем, 1961-м, здесь началось строительство еще одного цеха по производству древесно-стружечных плит (плоского прессования). Цех ДСП-2 мощностью 25 тыс. м3 плит в год заработал в 1964 году, и тогда же решением Северо-Западного Совнаркома завод «Фанеродеталь» был переименован в Череповецкий фанерно-мебельный комбинат. В том же году на Череповецком ФМК было выпущено 14,1 тыс. м3 фанеры и 12 тыс. м3 плит.
К 1965 году, когда здесь началось производство стульев, ЧФМК уже экспортировал свою продукцию в десятки стран мира.
На основании договора аренды с правом выкупа ЧФМК с 1 января 1991 года вошел в состав промышленно-хозяйственной ассоциации арендаторов «Мебельдрев», а 25 июня 1992 года было создано акционерное общество закрытого типа «Череповецкий фанерно-мебельный комбинат», обладающее полной производственной, хозяйственной и финансовой самостоятельностью. ЗАО входит в состав промышленной компании «Рослеспром».
В 2002 году состоялся ввод в эксплуатацию первой линии ламинирования ДСП, проведены реконструкция и модернизация фанерного производства. Годом позже пущен цех по производству пиломатериалов.
Контракт с немецкой фирмой Dieffenbacher на поставку оборудования (2006 год) позволил ЧФМК к 2008 году организовать массовое производство плит ДСП. В 2009-м пущена вторая линия ламинирования компании Wemhoener AG.
В 2010 году выпущено товарной продукции на сумму 2,4 млрд руб. (в сравнении с 2009 годом рост составил 22,7%). Ввод в эксплуатацию в 2011 году сушильной камеры СРГ-25 № 7 в лущильном цехе стал первым этапом реализации проекта по увеличению объемов производства фанеры до 100 тыс. м3 в год.
Объемы производства на ЧФМК ЗАО «Череповецкий фанерно-мебельный комбинат» производит фанеру березовую листовую марок ФК и ФК-Э класса эмиссии Е-1 (90 тыс. м3 в год); ДСП (208 тыс. м3 в год) и ламинированную ДСП для мебели (10,5 млн м2 в год); гнутоклееные заготовки из лущеного березового шпона для выпуска мебели; синтетические карбамидно-формальдегидные смолы (10 тыс. т в год). За пять лет, с 2003 по 2008 год, выпуск ДСП увеличился более чем в 1,5 раза - с 95 тыс. до 150 тыс. м3, проектная мощность предприятия достигает 210 тыс. м3 в год. Производство фанеры за тот же период увеличилось с 64 тыс. до 90 тыс. м3 в год. |
Инвестпроект ЧФМК
С 2006 по 2009 год на комбинате реализован крупный инвестиционный проект «Техническое перевооружение производства древесно-стружечных плит», в рамках которого проведена реконструкция существующего производства ДСП с установкой линии непрерывного прессования Dieffenbacher (Германия) и линии ламинирования Wemhoener (Германия).
В ходе реализации проекта были увеличены объемы производства ДСП и ЛДСП в два раза, расширен ассортимент выпускаемой продукции высокого качества. Объем инвестиций по проекту составил 1,2 млрд рублей.
Череповецкий фанерно-мебельный комбинат и его люди
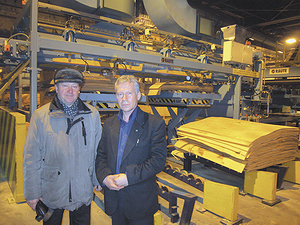
Александр Иванович Ремезов, главный инженер, и
Сергей Анатольевич Федотов, зам. директора по
развитию производства, начальник отдела
Наш гид по предприятию Александр Ремезов - человек удивительно душевный и очень опытный: 35 лет на комбинате, последние восемнадцать - в должности главного инженера. Далее мы будем приводить главным образом фрагменты его рассказов.
- В этом году нашему комбинату исполняется 55! С чем мы подошли к этой дате? Выпускаем три основных вида продукции: клееную фанеру марки ФК, древесно-стружечные плиты (в том числе ламинированные ДСП) и пиломатериалы, - рассказывает Александр Иванович. - Кроме этого, выпускаем детали из фанеры для производства мебели. На комбинате работает 1860 человек. Помимо основной деятельности, комбинат ведет лесозаготовку на арендованных лесных участках, где работают три комплекса «харвестер - форвардер» (машины John Deere, Komatsu, Timberjack). Заготовка ведется в основном в Череповецком и Кирилловском районах Вологодской области, есть арендованные участки и в Никольском районе.
Мы себя почти полностью обеспечиваем технологическим сырьем, с учетом того что производство ДСП потребляет (помимо технологического сырья) отходы фанерного производства и отходы лесопиления. То есть технологическая щепа и шпон-рванина, которые образуются в процессе производства, полностью используются в производстве ДСП. То, чего не хватает, мы дополняем технологическим сырьем, которое почти полностью обеспечиваем своей заготовкой.
Лесозаготовка и сырьевая база
Производственная площадка Череповечкого ФМК - 29 га. На территории две внушительные сырьевые (лесные) биржи.
- В 2009 году в сотрудничестве с Dieffenbacher мы провели серьезную модернизацию производства, реализовав тем самым один из приоритетных инвестиционных проектов в области освоения лесов, - продолжает рассказ г-н Ремезов. - Примерно тогда же рассматривался вариант строительства фанерного завода на новой площадке в Соколе, то есть планировалось не только наращивание мощностей производства, но и размещение его в другом месте. Не сложилось. А в соответствии с условиями этого приоритетного проекта мы получили в аренду лесные участки, до сих пор выбираем эти объемы леса. В Череповецком районе нам хватит еще лет на семь, в Кирилловском побольше, еще побольше в Никольском - но там и заготавливать сложнее. Четыре подрядчика работают на арендуемых нами участках.
Заготавливают они примерно 140 тыс. м3 в год. Расчетная лесосека - более 200 тыс. м3. Заготовка только сортиментная, хлыстовой нет. Пилим все диаметры, используем древесину полностью. В этом году получили сертификат FSC.
Свои объемы невелики, как видите. И это в основном береза. Изначально аренда рассматривалась как возможность обеспечить потребности комбината в фанерном сырье в период осенней распутицы.
- И лесовосстановлением занимаетесь?
- Конечно.
- Какова годовая потребность комбината в сырье?
- Одного только фанерного сырья 270-280 тыс. м3, 160 тыс. - технологического сырья (дровяная древесина - осина, березовые и хвойные балансы), хвойного пиловочника - около 60 тыс. м3, 20 тыс. м3 - привозной щепы. С сырьем проблем нет, вопрос разве что в том, как сохранить его до зимы.
Лесопиление
- В 2003 году на ЧФМК запущена линия лесопиления, - говорит г-н Ремезов. - Оборудование закупалось в Швеции, в пяти разных местах. Линия на базе лесопильного станка Linck типа MKV, находящегося в эксплуатации уже более 20 лет, что в свою очередь говорит о высоком качестве и надежности. Производительность - около 100 м3 пиломатериалов в смену (23 тыс. м3 в год). Пиломатериалы в основном идут на экспорт, небольшая часть остается на внутреннем рынке. Образующаяся технологическая щепа идет на производство ДСП. Цех лесопиления работает большей частью на покупном сырье.
В декабре 2012 года завершены работы по монтажу и пусконаладке новой линии рубки и стопоукладки к станку 3VKKT от компании Raute. Линия позволяет увеличить производительность - скорость рубки листов на роторных ножницах достигает 130 м/мин. С вводом нового оборудования гарантируется качество и точность рубки, уменьшается количество неформатного шпона, сокращаются расходы на обслуживание линии. В дальнейшем планируется модернизация лущильного станка и установка нового ЦЗУ для увеличения его производительности до 7,5 м3 сырого шпона в час с выходом шпона 67%. Raute и ЗАО «Череповецкий фанерно-мебельный комбинат» в 2013 году планируют продолжить сотрудничество: намечается модернизация линий лущения и установка новых линий сортировки шпона и шпонопочинки. |
Производство фанеры на ЧФМК
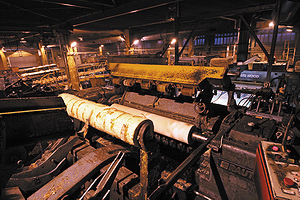
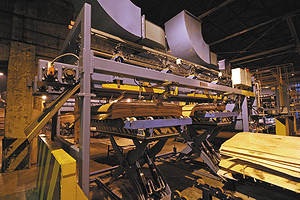
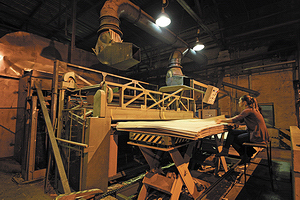
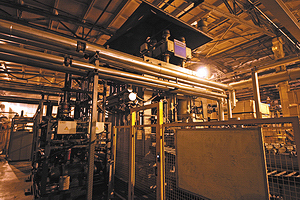
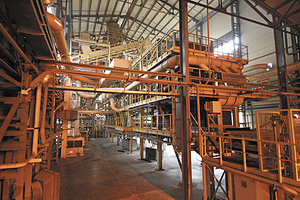
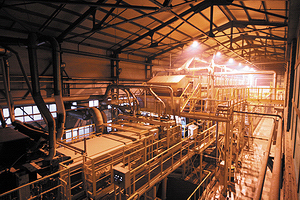
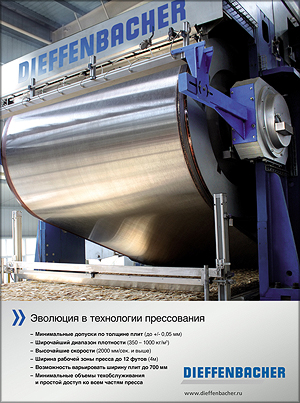
Dieffenbacher. Оборудование для производства
древесных плит
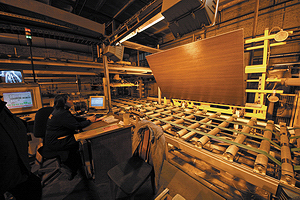
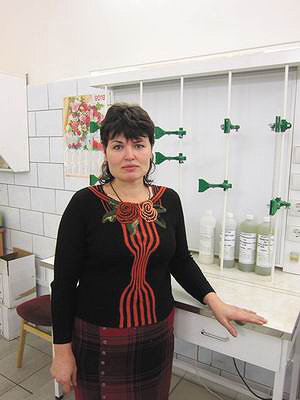
Татьяна Николаевна Войтова, зам. начальника цеха,
старший технолог
В состав фанерного производства ЧФМК входят: цех по обеспечению сырьем, цех лущения шпона, цех клейки фанеры, участок раскроя фанеры.
- В настоящее время мы занимаемся реконструкцией фанерного производства, - продолжает свой рассказ Александр Ремезов. - Устанавливаем новую, шестую по счету, линию лущения, рубки и укладки шпона. Как и предыдущие пять, она произведена финской компанией Raute. Готовимся к установке нового фанерного пресса днепропетровского производства. Также собираемся установить дополнительно две тайваньские ребросклейки.
К разговору подключается главный технолог ЧФМК Павел Мосеев:
- Сейчас работают три ребросклейки. В планах запустить четыре или пять, в зависимости от количества работающих прессов. Не так давно мы ввели в эксплуатацию дополнительный пресс П714Б (15-пролетный с двумя наборными столами, он произведен в Днепропетровске), и сейчас у нас на основном производстве пять прессов (Д40-38 и П714Д), шестой - в цехе деталей мебели. Еще один пресс будет запущен летом. Что называется, пляшем от головного оборудования: для определенного количества действующих прессов мы должны производить определенный объем шпона (отсюда мощность и количество лущильных станков - запускаем в работу шестой), соответственными должны быть и мощности сушки. Итак, в 2013 году будет семь прессов и к ним пять сушилок СРГ25М, а к трем ребросклейкам (две Hashimoto, одна Plytec) добавятся еще две тайваньские.
Нашим прессам уже много лет, но они хорошего качества и работают исправно. Раз в неделю мы обязательно проводим профилактику, чистку всего оборудования. В замене они пока не нуждаются. Раз в год выполняем обязательный капитальный ремонт. Так что, возможно, еще наши внуки на них поработать смогут.
Форматно-обрезной станок Infor (Raute) - довольно старый, планируем его скорую замену. Выбираем между моделями немецких или японских производителей. Но пока и он справляется с обрезкой всей фанеры, которую мы выпускаем.
Шлифовальный станок Steinemann установлен в цехе лет восемь или десять назад. На нем шлифуем высшие сорта фанеры, это примерно 25-30% всего объема.
Сортировка фанеры выполняется вручную. Этот способ, конечно, трудоемкий, но зато позволяет добиться высокого качества.
Подходит стопа и здесь отсортировывается: в листах выявляются механические повреждения, определяется качество склейки. Если лист фанеры соответствует норме, он укладывается в готовую пачку. Если же есть какие-то отклонения, например, дефект по кромке, такой лист складывается в стопу переобреза, дефектный участок отпиливается и на реализацию уходит фанера меньшего формата. Если же повреждение не механическое, а есть просто дефект на поверхности листа, например непрошлифовка, то такой лист отправляется на участок ремонта, где дошлифовывается вручную, после чего возвращается в пачку готовых листов и отправляется потребителю. Бывает и так, что обнаруживаются дефекты, которые сложно ликвидировать, тогда этот лист фанеры просто переходит в более низкий сорт. Но это редко.
Хрупкие женщины своими руками за смену перебирают десятки тонн фанеры - мужчина здесь работать не сможет: работа монотонная, связана с постоянной физической нагрузкой, какой мужик с этим справится! Женщин на производстве много, основная тяжесть ложится именно на женские плечи, а мужчины работают водителями погрузчиков и т. п.
Вот, слышите, работница простукивает молоточком лист? Проверяет на внутренний непроклей: звонкий звук - все нормально, глухой - лист отправляют в выбраковку. Доля брака у нас на производстве 1-1,5%, не более.
Всего у нас выпускается четыре сорта фанеры, классификация по шпону согласно ГОСТу 39-16 - от первого до четвертого сорта. Фанеру для внутреннего рынка мы маркируем цифрами, для экспорта есть буквенные обозначения, как принято за границей.
Производство ДСП на ЧФМК
- В 2008 году мы выполнили реконструкцию в цехе ДСП, - говорит г-н Ремезов. - Поставили линию непрерывного прессования Dieffenbacher и сейчас выпускаем плиту трех форматов: традиционного российского 1750×3500, самого ходового европейского 1830×2750, а также 1830×3060 (который, например, используется для производства подоконников методом постформинга). Линия была куплена с прессом CPS длиной 28 м, рассчитанным на производительность 215 тыс. м3
ДСП в год.
В принципе, мы способны делать любые форматы, хотя это довольно сложно в условиях действующего производства - у каждого формата свои остатки, разносортица, все это надо где-то складировать, - поэтому мы остановились на трех форматах. Толщина - в зависимости от того, что хочет потребитель.
На производстве ДСП две линии ламинирования: одна 2002 года выпуска, немецкой фирмы Burkle, вторая линия - от Wemhoener, 2008 года.
По прошествии многих лет работы и с ней случаются небольшие проблемы, но нет такого оборудования, которое не ломается, важно, что вопросы ее ремонта оперативно решаются. Но в целом техника Wemhoener очень хорошая, без всяких проблем на ней можно ламинировать плиты разного формата, толщины и с различными декорами - только делай корректировки в программе. Все исходные данные в нее внесены.
О клеях и смолах
- Смолы мы варим сами, - рассказывает Александр Иванович. - Смола была разработана еще ЦНИИФом, другое дело, что в процессе каждого конкретного производства всегда существуют свои нюансы, свои секреты. От того, какая используется смола, напрямую зависит производительность линии. Очень важна реакционная способность смолы, влияющая на склеивание: чем этот показатель выше, тем большую скорость можно задать линии. Нужно, чтобы ковер, пока он проходит в прессе, успел спрессоваться и затвердеть. Если этого до конца не происходит, то, во-первых, на выходе может получиться расклей, а во-вторых, плита будет сильно «фонить». Процесс полимеризации смолы таков, что чем больше формальдегид вступит в реакцию, тем меньше его будет выделяться из готового продукта. Здесь необходимо упомянуть о классе эмиссии: мы работаем на плите класса эмиссии Е1 как по фанере, так и по ДСП. Прошлым летом пробовали использовать новую низкотоксичную смолу собственной варки со специальными добавками и получили Е0,5. Улучшили характеристики: если показатель эмиссии для Е1 до 8 мг на 100 г абсолютно сухой плиты, то для Е0,5 - до 4 мг.
Это совсем свежая разработка. Уникальность этой смолы в том, что все заводы, которые делают Е0,5 (в России в прошлом году сертифицировалось восемь заводов), используют смолу с добавкой меламиновых смол. Мы меламин не используем, применяем другие акцепторы, которые снижают токсичность.
- У нас используется смола СКФ, - добавляет Павел Мосеев. - На ней почти никто больше не работает; даже один из изобретателей смолы, г-н Кондратьев из ЦНИИФа, удивился, узнав, что мы ее используем. Многие предприятия вообще не варят смол - пользуются покупными, но своя смола лучше тем, что можно экспериментировать, стараться сделать низкотоксичную смолу или смолу с повышенной реакционной способностью - менять мольное соотношение, делать какие-то добавки при варке, менять параметры под конкретную задачу.
Контроль по токсичности (ДСП, деталей мебели) мы осуществляем сами. Данные проверок отправляем в Ростехнадзор.
Низкотоксичные ДСП стоят, конечно, дороже. Мы делаем их под конкретные заказы. Минимальная рентабельная партия плит по стандарту E0,5 - 350 м3 (выпуск в сутки - 700 м3), в рублевом эквиваленте это примерно 1,6 млн.
Лаборатории и сертификация на ЧФМК
- Сертификаты по ДСП получаем в «Лесертике» (г. Балабаново), что касается фанеры, ее сертифицируем по токсичности в соответствии с CARB. CARB - это сертификат, который составляется по требованиям управления воздушных ресурсов США (штат Калифорния). Сертификация выполняется в институте VKI (Германия). Каждый квартал приезжает инспектор, выбирает листы фанеры, расписывается на них, и мы их отправляем в Германию. Там их пилят и проверяют на токсичность. Получаем сообщение: все нормально - и нам продлевают сертификат.
- Это по фанере. А по ДСП нет такого международного контроля?
- Почему же, плиты тоже можно сертифицировать в VKI, но это необходимо только в том случае, если мы будет отгружать продукцию в Европу или в Соединенные Штаты. А пока наш экспорт ДСП ориентирован в основном на республики Средней Азии. Фанера сертифицирована вся. А также и детали из фанеры - в Европе сильно беспокоятся: «А вдруг какая-нибудь деталь из вашей фанеры попадет в Калифорнию? Проблемы же будут!» Поэтому все довольно жестко.
- А при покупке оборудования у того же Dieffenbacher не возникало проблем по смоле? Немецкие станкостроители ведь отчетливо понимают взаимосвязь между условиями эксплуатации их техники и качествами связующего. Наверняка есть определенные требования...
- Им, как продавцам, без разницы, чем мы будем клеить. Другое дело, что, в соответствии с контрактом, они предупреждают, что для максимального увеличения скорости их линии необходимо использовать смолу с определенной реакционной способностью. И могут порекомендовать смолу конкретной фирмы и марки, которая обеспечит нам возможность разогнаться.
Производство мебели, теперь уже бывшее
- Производство стульев на комбинате было прекращено в 2011 году, - говорит Александр Ремезов. - На предприятии делали гнуто-клееные стулья С1, С2 - до 500 тыс. шт. в год. Они были простенькие, сбыт их с каждым годом становился меньше и меньше. Постепенно стали нарастать убытки. Поддерживали выпуск стульев за счет других производств, но в итоге все же решили отказаться от этого вида деятельности. Цех теперь на консервации - хотели ставить линию импрегнирования, но пока это только планы, требуются немалые деньги: вместе со стоимостью оборудования для варки карбамид-формальдегидной и меламиновой смол требуется не меньше 3,5 млн евро. Расчетный срок окупаемости проекта настолько большой, что коммерческий интерес теряется. Поэтому сейчас ищем альтернативные варианты.
- Производство мебели, таким образом, совсем перестало существовать?
- Нет. Остался цех по производству деталей мебели. Мебель как таковую мы не делаем, но делаем комплектующие для нее, а также древки для хоккейных клюшек, прорезную фанеру, ламели плоские и гнутые.
Безопасность производства
- Во избежание хлопков и взрывов в июне 2012 года на комбинате, вместо не устроившей нас ранее системы искрогашения GreCon, мы установили защитную искровую систему Firefly, реагирующую на инфракрасное излучение от искр и других опасных горячих частиц. Мы ее постоянно тестируем и проверяем - как положено, раз в 2 недели делаем профилактику, вынимаем датчики - подводим источник с инфракрасным излучением, она срабатывает и распыляет воду, - продолжает рассказ о предприятии Александр Ремезов. При запуске зимой мы столкнулись с неадекватными срабатываниями детекторов, установленных в точках с высокой температурой. Как оказалось на систему влияло неудовлетворительное качество охлаждающего воздуха, в нём было масло и влага. После того как мы установили маслянные фильтры, проблема была решена. В настоящее время система работоспособна и уже несколько раз защитила производство от возгорания, система нашему процессу не мешает, поскольку отсутствуют ложные срабатывания
- А на линии шлифования какие возможны угрозы?
- Как правило, на шлифовке если и случаются хлопки, они происходят в системах пневмотранспорта. Ведь когда работали на старой линии, случалось, на линию попадала плита, в теле которой находилась гайка, электрод или что-то подобное. При шлифовке такого включения образовывался сноп искр. И может произойти хлопок. Чем он чреват? Может разорвать циклон, поджечь фильтр. Порча оборудования.
- Что необходимо для эффективного использования систем искрогашения?
- В первую очередь, нужен грамотный специалист в этих системах, который может оперативно разобраться с любой возникающей в них проблемой. У нас такой есть - его обучили прямо на производстве сотрудники Firefly, проявил себя очень хорошо.
- Что бы вы могли им посоветовать поставщикам для усовершенствования систем и улучшения работы с клиентами?
- Прежде всего, честно предупреждать о проблемах, существующих с их оборудованием. К чести поставщика надо сказать, что они никогда не отказывают в помощи и стараются делать все, чтобы системы работали нормально.
Забота об окружающей среде
- На нашем предприятии действует абсорбционно-биохимическая установка для очистки формальдегида, - рассказывает г-н Ремзов. - В 2008 году мы пытались запустить газоконвекторную установку «Ятаган» одной из московских фирм и вскоре убедились в ее неудовлетворительном качестве. Возможно, в лабораторных условиях она и чистила формальдегид, а в условиях производства на ее газоразрядных ячейках помимо формальдегида оседали пары воды, масла, аэрозоли, древесная пыль. Оседают эти пары на лампах, лампы постепенно перегорают, их можно менять до бесконечности, а толку чуть.
Менять лампы надо каждую неделю, а стоят они недешево. Сейчас купили у белорусской компании «Промышленно-экологические системы» (технопарк Белорусского госуниверситета) установку, работа которой основана на принципе растворения формальдегида в воде: газовые выбросы пропускаются в установке сквозь кипящий слой, смешиваются с водой и растворяются в ней. Загрязненная вода поступает в биореактор, где обитают микроорганизмы, поедающие формальдегид. Выделяется углекислый газ, а вода возвращается в установку, то есть цикл замкнутый.
На предприятии ведется серьезная работа для обеспечения экологической безопасности продукции - это не просто модное веяние, а насущная необходимость. Экологическая безопасность - это не только выпуск нетоксичной плиты, но и снижение выбросов в атмосферу, безотходное использование сырья.
Надлежащее качество выпускаемой нами продукции обеспечивает ее долговечность - а это тоже вопрос экологической безопасности.
Тем самым мы сохраняем больше лесов... В общем, аспектов у этой проблемы очень много, и все они у нас на комбинате учтены. С 1 июня 2013 года вода, которую мы собираем (техническая вода с охлаждения оборудования и вода с дождеприемников) передается на городские очистные сооружения, а не сбрасываться в реку Серовку.
Персонал Череповецкого фанерно-мебельного комбината
- Скажите, пожалуйста, сколько в среднем получают на ЧФМК?
- 27 тыс. руб. С 1 ноября прошлого года подняли зарплату всему персоналу примерно на 10%. Для нашей отрасли это довольно высокий уровень.
- А обучением персонала занимаетесь самостоятельно?
- Считаю, что наиболее эффективно готовить специалистов именно для своего производства: приходят ребята из техникумов, проходят здесь «обкатку», своего рода испытание делом. Если мы видим, что у человека есть и желание работать, и способности, его обучают, продвигают по служебной лестнице. Тех, кто хочет дальше учиться, тоже стимулируем, помогаем поступить в ЛТУ, поддерживаем во время учебы. И от таких людей наибольшая отдача в работе, именно они остаются на предприятии, связывают с ним свою жизнь, двигаются вперед. Стараемся мотивировать их к развитию. Также у нас стажируются студенты Санкт-Петербургского лесотехнического университета.
В этом году к нам пришли два выпускника СПбГТУ и одна выпускница ЧГУ. Они приглашены по специальной программе, стажируются в течение года. По результатам стажировки руководство примет решение: если они хорошо себя покажут, им будут предложены определенные условия договора. Сейчас им оплачивается не только эта стажировка, но и квартира - мы снимаем жилье для приезжих. Тестирование проходили много ребят, но в результате довольно жесткого отбора выбрали мы только нескольких. С кадрами у нас сегодня проблем нет, в том числе с руководящими, но мы задумываемся о будущем и готовим квалифицированную смену.
Социальная политика ЧФМК
Много внимания уделяется на комбинате здоровью и благополучию его сотрудников.
- В городе остался один подведомственный стадион - это наш, комбинатский, - продолжает рассказ Александр Ремезов. - Мы, конечно, никому не запрещаем там свободно заниматься спортом, стадион открыт для жителей всего Северного микрорайона, но его главное назначение в том, чтобы там могли заниматься наши сотрудники и их дети. В этом году построили новый теннисный корт. Думаю, лучший в городе. Тут же, рядом с комбинатом, есть санаторий-профилакторий. Туда по путевкам отправляются отдыхать и лечиться наши работники, часть путевок мы продаем и всем желающим. У нас тут очень хорошие специалисты, таких в городе очень мало. В этом лечебном учреждении есть и физиопроцедуры, и массаж, и пиявки, и иглотерапия...
- Все это для сотрудников бесплатно?
- Работники комбината оплачивают 10% от стоимости путевки. По себе знаю, что за две недели в профилактории можно хорошо восстановиться. Даже молодые ребята у нас следят за своим здоровьем, хотя, конечно, больше всего услуги врачей востребованы у наших пенсионеров.
Твердо стоять на земле
- Александр Иванович, какой объем фанеры идет на экспорт?
- Эти цифры колеблются от 70 до 90% в зависимости от месяца.
- Это как-то связано с низким спросом на внутреннем рынке?
- Не совсем так. За рубежом клиенты постоянные. Такого на внутреннем рынке нет: здесь сегодня один купил, завтра - другой, послезавтра - третий... Так нельзя работать. Производство должно быть обеспечено постоянными заказами. Пусть в их составе будет самая разная продукция, но это должны быть постоянные заказы. Постоянные надежные клиенты - основа стабильной работы комбината.
- Нынешнее увеличение мощностей приведет к увеличению экспорта, продажам этим постоянным клиентам?
- Хотелось бы, но так не бывает, чтобы все шло за рубеж. Мы развиваем производство с расчетом на перспективу, одновременно формируя портфель заказов, учитывающий растущие мощности. Не все просто - сейчас цены на фанеру немного упали, на внутреннем рынке вообще какое-то затишье, но, возможно, именно им и следует воспользоваться, чтобы выходить на новый уровень.
- А запуск в стране производств плит OSB вас не пугает?
- Нас нельзя считать конкурентами таких производств. Плиты OSB предназначены для строительства, а наша сфера - мебель и упаковка. Много нашей фанеры С6 и С8 идет на Запад именно для изготовления упаковки - в частности, там есть довольно развитый бизнес по изготовлению качественных ящиков для хранения и перевозки парфюмерии, дорогостоящих запчастей и другой продукции. Интересное применение нашей фанере нашли в Египте - там на мебельном производстве ее особым образом выгибают, покрывают шпатлевкой, особыми лаками, и выходит очень необычная и красивая продукция. Глядя на эту мебель из «массива», никогда не подумаешь, что сделана она из нашей С3! Из нее в Египте еще и строительные щиты делают.
- Что вы можете сказать о географии экспорта?
- География поставок нашей продукции компании охватывает более 50 стран Северной Америки, Западной и Восточной Европы, Африки и страны СНГ. Арабские страны покупают у нас тонкую фанеру.
- Какие качества вашей продукции вы считаете своими конкурентными преимуществами?
- Мы на рынке давно, нас хорошо знают. Могу сказать, что крупные перекупщики, приобретающие для последующей продажи крупные партии фанеры сразу на нескольких предприятиях, стремятся, чтобы в этих партиях непременно был определенный объем именно нашей фанеры, - улыбается Александр Иванович.
- Это потому, что потребитель уверен в стабильно высоком качестве череповецкой продукции, непрерывном контроле его параметров, постоянстве нашей системы качества, - добавляет Павел Николаевич. - Нам скрывать нечего, мы готовы в любой момент по запросу предоставить все данные о нашей продукции.
Беседовала Светлана ЯРОВАЯ
Подготовил Максим ПИРУС
Фото Андрея Забелина
Лаборатории на ЧФМК
В каждом производственном подразделении комбината есть своя лаборатория, контролирующая качество изделий. Вся выпускаемая продукция сертифицирована. Фанерная продукция сертифицирована на соответствие производственного контроля завода требованиям стандарта 0765-CPD-0510 и на соответствие требованиям CARB Phase 2 No. 697-2009-01-ТРС-4.
Уменьшение вредных выбросов
В 2006 году для снижения содержания формальдегида в воздухе рабочей зоны в цехе ДСП были установлены четыре генератора озона «Озотрон». За эту установку компания получила диплом победителя областного конкурса «За вклад в сохранение окружающей среды» по итогам 2006 года.
В 2008 году в цехе ДСП с целью снижения выбросов пыли проводилась замена фильтровальных рукавов на фильтре Steinemann и системы аспирации «Консар». Выполнены мероприятия по переносу источника выброса от линии прессования цеха древесно-стружечных плит и увеличению высоты трубы, направленные на улучшение экологической ситуации в Северном районе г. Череповца.
В 2010 году на ЧФМК введены системы вторичного использования загрязненной воды от вакуум-насосов в цехах смол № 1 и 2, что позволило снизить концентрацию формальдегида и существенно уменьшить расход воды. Согласован проект по организации санитарно-защитной зоны (СЗЗ) с целью снижения уровня воздействия вредных факторов на среду обитания и здоровье населения до требуемых нормативов.
В 2011 году выполнен ряд мероприятий, направленных на улучшение экологической ситуации в Северном районе г. Череповца.
Проведены работы по внедрению второй ступени очистки газовоздушной смеси (ГВС) после отделения сухой некондиционной стружки на линии прессования древесно-стружечных плит, что позволило сократить выбросы древесной пыли на 32,5 т.
В 2012 году была установлена абсорбционно-биохимическая установка (АБХУ) производительностью 30 тыс. м3/ч, предназначенная для очистки газовоздушной смеси, удаляемой от пресса CPS 1/S фирмы Dieffenbacher, и призванная уменьшить попадание вредных веществ в атмосферу.
Лучший экспортер
ЧФМК входит в первую десятку предприятий лесного комплекса России по объемам выпускаемой продукции. За выдающийся вклад в расширение внешних экономических связей Российской Федерации и высокую профессиональную культуру предприятие многократно удостаивалось звания «Лучший российский экспортер».
Достоинства череповецкой ДСП:
- высокая плотность и твердость наружных слоев, которые достигаются за счет использования в качестве сырья древесины северных пород березы и ели (в оптимальном соотношении);
- высокотехнологичная новая линия непрерывного прессования Dieffenbacher мощностью 208 000 м3 ДСП в год, которая позволяет получать продукцию высокого качества при минимальном использовании персонала, что почти исключает влияние человеческого фактора;
- 45-летние традиции производства качественной ДСП;
- безотходное производство плиты с соблюдением европейских стандартов экологической безопасности; по содержанию формальдегида продукция соответствует европейскому классу эмиссии Е1;
- экономичность производства: выход 1-го сорта при ламинировании ДСП составляет 99%.