Производство мебельных деталей сложной объемной формы
Оборудование для производства мебели
В деревообработке и производстве мебели вот уже несколько десятилетий как победила тенденция к максимальному упрощению формы деталей почти любого изделия, что во многом было связано с широким использованием плитных материалов взамен цельной древесины. Это предельно упростило технологию и привело к сокращению номенклатуры используемого оборудования.
Производство мебели из массивной древесины, в особенности той, которая копирует стили прошлых веков, связано с изготовлением не только плоских щитовых и брусковых, но и объемных деталей.
Объемные неплоские мебельные детали
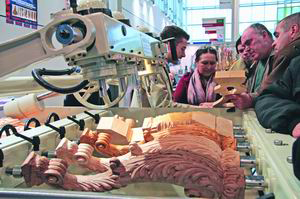
Точные размеры таких деталей, как правило, на обычном чертеже не указываются, поскольку их форма определяется сложной конфигурацией поверхности. Размеры этих деталей не могут быть определены сочетанием дуг окружностей разного радиуса, прямых линий или кривых, описываемых простыми математическими формулами.
Такие конструктивные объемные детали изделий могут представлять собой и скульптуру весьма сложной формы.
Классическим примером объемных деталей сложной формы, наиболее часто использующихся в изделиях мебели до сих пор, являются ножки, получившие название кабриоль (от итал. cabriole - прыжок козленка), а также близкие к ним по форме подлокотники кресел, диванов и т. д. Кроме того, поверхности объемных деталей могут частично или даже полностью покрываться резьбой, что еще больше усложняет процесс их формирования.
Помимо ножек типа кабриоль, к деталям сложной объемной формы относятся детали стульев, кресел, а также корпусной мебели в ретро-стиле, деревянные обувные колодки, весла, ружейные приклады, авиационные винты и т. д.
В конце XIX - начале XX века, когда мебель изготавливалась в основном по индивидуальным проектам, такие детали выполнялись столярами высокой квалификации вручную, с использованием ручного измерительного и обрабатывающего инструмента.
Но увеличение спроса на подобные изделия из древесины и стремление к их одинаковой форме вскоре заставили производителей изготавливать такие детали с применением копиров. Так, повышение спроса на обувь по окончании Первой мировой войны привело к созданию станков для машинного способа изготовления обувных колодок, а недостаток мастеров-резчиков обусловил разработку станков для выполнения плоской и объемной резьбы.
Повторение формы объемных мебельных деталей вручную
Производство объемных деталей вручную предусматривает изготовление образца из какого-то пластичного материала, например глины или воска. После проверки соответствия образца замыслу столяра из цельной древесины выпиливаются заготовки нужного размера, затем выполняется их черновое обтесывание, после чего им придается необходимая форма.
Для того чтобы форма объемного изделия максимально приближалась к форме образца, что особенно важно при изготовлении комплекта одинаковых деталей, используются вырезные шаблоны. При этом поверхность исходного образца как бы рассекается рядом параллельных плоскостей, находящихся на одном и том же расстоянии друг от друга, форма каждого сечения копируется и по полученному очерку вырезается наружный шаблон.
Этим шаблоном постоянно проверяется количество материала, удаленного с поверхности обрабатываемой заготовки в зоне определенного ее сечения. Такой способ, конечно же, не может быть использован в промышленном, даже мелкосерийном, производстве.
В начале ХХ века производство обуви перестало быть уделом сапожников и перешло на промышленную основу, особенно - при выполнении заказов для армии. Технология обувного производства предусматривала тогда применение деревянных колодок, которые отличались размерами, и их изготовление вручную не могло удовлетворить огромные потребности.
То же относилось и к производству ружейных прикладов, авиационных воздушных винтов, а также разных деревянных моделей для литья из металла, где использовалась только твердая древесина и требовалась высокая точность обработки, которой невозможно достичь с помощью ручного инструмента.
Станки объемно-копировальные с насадными фрезами
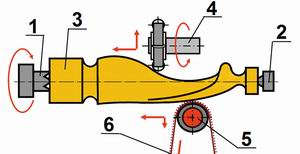
Рис. 1. Схема объемно-копировального станка:
1 – приводной шпиндель передней бабки;
2 – неприводной шпиндель задней бабки;
3 – обрабатываемая заготовка;
4 – фреза, с управлением ее перемещением от объемного
копира;
5 – прижимной ролик шлифовального суппорта с
управлением его перемещением от объемного копира;
6 – лента шлифовальная
Первый объемно-копировальный станок для производства обувных колодок с вращающимся металлическим копиром в 1930-х годах изготовила немецкая фирма Fagus Werke. Затем его принципиальная конструкция была использована многими другими изготовителями, в том числе и в СССР. При этом его технологическая схема (рис. 1) не изменилась и по сей день.
В составе такого станка - станина в виде вертикальной рамы, на которой один над другим установлены три вращающихся шпинделя; один из них (обычно средний) предназначен для зажима объемной модели, а два других, вращающихся в противоположных направлениях, - для обрабатываемых заготовок. На горизонтальных направляющих станины установлен суппорт, перемещаемый вдоль них отдельным приводом; на суппорте смонтирована отклоняемая рама, несущая на себе два вертикальных фрезерных агрегата и копирующий упор или ролик, постоянно контактирующий с копируемой моделью. В старых станках эту раму к модели прижимали пружины, а в современных станках это делают пневмоцилиндры.
В процессе работы на одном из шпинделей станка закрепляется копир (модель), а на других - обрабатываемые заготовки, которым может быть на другом оборудовании предварительно придана форма, в наибольшей степени соответствующая форме модели. Все эти шпиндели одновременно приводятся во вращение, скорость которого обычно составляет от 20 до 40 об./мин. Регулирование расстояния на длину обрабатываемых заготовок выполняется сдвиганием задней бабки, установленной на отдельных направляющих станины.
Вместе с вращением шпинделей приводится в движение рама с обрабатывающими фрезерными агрегатами, движение которой в направлении заготовок ограничивается копирующим роликом, постоянно находящимся в контакте с моделью. Таким образом достигается повторение формы модели на обработанных заготовках. Скорость продольной подачи фрез зависит от материала заготовок и сложности формы модели и бесступенчато регулируется в пределах 75-200 мм/мин.
После совершения рамой с фрезами рабочего хода рама с фрезерными агрегатами возвращается в исходное положение, готовые детали освобождаются от зажима и заменяются новыми.
Во всех подобных станках в качестве режущего инструмента используются сборные насадные фрезы со сменными режущими пластинами круглой формы, что позволяет добиться более высокого качества обработки в процессе поперечного резания, чем при использовании цилиндрических фрез, и дает возможность копировать вогнутые поверхности радиусом от 18 мм (при диаметре лезвий 35 мм).
Современные станки этого типа могут дополнительно оснащаться ленточно-шлифовальными агрегатами, устанавливаемыми на второй отдельной раме, перемещаемой синхронно с фрезерными агрегатами и также повторяющими на деталях профиль исходной модели.
Шпиндели в таких станках могут располагаться горизонтально или вертикально. Но при горизонтальном расположении шпинделей на станках можно одновременно обрабатывать до 24 заготовок, что невозможно при вертикальном размещении заготовок из-за ограничений по высоте загрузки.
Станки с горизонтально расположенными шпинделями для установки обрабатываемых заготовок изготавливались немецкой фирмой Reichenbacher, итальянской компанией Bаlleri и австрийской фирмой Zuckermann.
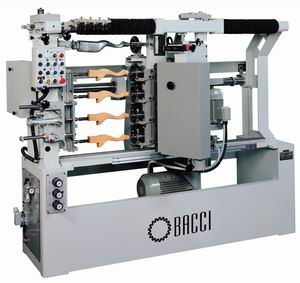
Рис. 2. Станок объемно-копировальный и
шлифовальный мод. T4M-O 250 (BACCI)
Сегодня из подобных станков наиболее известна только одна модель с вертикальным расположением шпинделей, выпускаемая итальянской фирмой Bacci: Т4М-О (рис.2), на которой возможна обработка одновременно четырех заготовок. Длина рабочей зоны этого станка может достигать 1000 и 1500 мм. Производятся также его аналоги, изготавливаемые предприятиями Тайваня.
Такая узость современного ассортимента этих станков связана в первую очередь с отходом деревообрабатывающих предприятий от производства мебели из цельной древесины, распространением обрабатывающих центров и переходом обувных производств на пластмассовые и металлические колодки.
Станки с концевыми фрезами
Принцип фрезерования деталей на таких станках с помощью фрез, ось вращения которых параллельна оси вращения заготовки, позволяет делать в деталях лишь небольшие поперечные углубления, радиус которых составляет не более половины наружного диаметра фрезы. На таких станках невозможно формирование мелких рельефов.
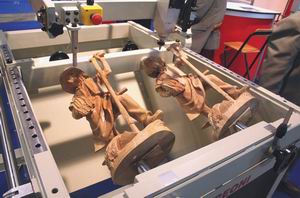
Рис. 3. Станок объемно-копировальный с концевыми
фрезами
Поэтому более полувека назад были разработаны копировальные станки, работающие по принципу пантографа (рис. 3). На их станине, внутри горизонтальной сварной рамы, размещены шпиндели для зажима заготовок, которые можно одновременно поворачивать вручную на одинаковый угол (рис. 4а). Зажим заготовок в каждом шпинделе осуществляется вручную с помощью индивидуального винтового устройства. Снизу под каждым шпинделем установлены подъемные поддерживающие опоры, служащие для начального базирования обрабатываемых заготовок.
На двух параллельных направляющих в задней части станины станка на двух опорах установлена еще одна, составленная из нескольких рычагов, рама, которая может качаться вокруг горизонтальной оси, смещаться вправо и влево и перемещаться вперед и назад. На балке в передней части этой рамы размещены вертикальные фрезерные агрегаты - каждый напротив соответствующего шпинделя для зажима обрабатываемых заготовок. В самом центре этой балки имеется вертикальный консольный копирующий упор (копирующий палец), постоянно контактирующий с моделью, зажимаемой в шпинделе, который расположен в середине станка. Качающаяся рама снабжена противовесами, настраиваемыми так, чтобы не происходило ее самопроизвольное смещение вверх. Горизонтальное движение балки с фрезерующими агрегатами и ее качание осуществляются вручную - с помощью укрепленной на ней рукоятки.
Перед началом работы в каждый фрезерный агрегат устанавливаются концевые фрезы - таким образом, чтобы у всех них был одинаковый вылет, полностью соответствующий вылету копирующего упора.
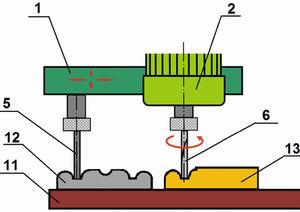
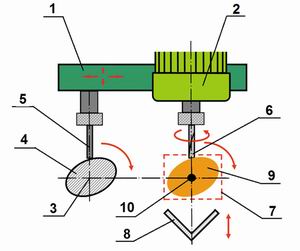
Рис. 4. Схема объемно-копировального станка с концевыми фрезами
а – при обработке заготовок, закрепленных в центрах;
б – при фрезеровании заготовок, закрепленных на столе:
1 – рама с фрезерными агрегатами, перемещаемая в трех направлениях (вверх-вниз, вправо-влево, вперед-назад),
2 – фрезерный агрегат, 3 и 5 – ось вращения копира, 4 – вращающийся копир, 6 – фреза концевая, 7 – исходная
заготовка, вращающаяся синхронно с копиром, 8 – подъемная опора для начального базирования заготовки;,
9 – сечение детали, обрабатываемое в данный момент, 10 – ось вращения заготовки, 11 – неподвижный стол станка,
12 – неподвижный копир, 13 – заготовка, закрепленная на столе
При работе на станке в его центральный шпиндель устанавливается модель, изготовленная из металла или твердой древесины. Затем одновременно поднимаются все поддерживающие опоры под рабочими шпинделями. В них вкладываются предварительно прирезанные в одинаковый размер деревянные заготовки, которые поочередно зажимаются винтовыми устройствами шпинделей.
Далее рабочий включает фрезы и подводит копирующий палец к модели. Одновременно, повторяя это движение, синхронно перемещаются и все концевые фрезы, начиная обработку всех заготовок.
Так, перемещая раму с фрезерными агрегатами вперед и назад, вправо и влево, вверх и вниз, постоянно касаясь копирующим пальцем модели, рабочий обрабатывает одновременно все заготовки. Когда одна их сторона будет обработана, синхронно с моделью выполняется поворот всех шпинделей с заготовками и обработка продолжается до полной готовности деталей.
В таких станках шпиндели для зажима заготовок, расположенные справа и слева от копира, могут синхронно вращаться влево и вправо, что позволяет одновременно получать парные детали, зеркально симметричные.
Для обработки рельефов на плоских заготовках такие станки оснащаются столом, на котором устанавливается копир и закрепляются заготовки (рис. 4б).
Для достижения точного воспроизведения формы и рельефа модели диаметр и форма заточки концевых фрез должны всегда соответствовать форме рабочего конца копирующего упора. В подобных станках некоторых моделей фрезерные агрегаты оснащены вертикальными шпинделями с поворотными головками, в которых могут закрепляться одновременно две фрезы, например для черновой и чистовой обработки. Их замена выполняется вручную простым поворотом головки на 180° вокруг горизонтальной оси. При этом так же поворачивается и головка с копирным пальцем.
В этих станках может быть две и больше позиций для обработки, причем их количество ограничивается лишь жесткостью конструкции качающейся рамы, биение или деформация которой приводят к искажению повторяемой формы модели.
Станки подобного типа ранее производились, например, немецкой фирмой Reichenbacher и итальянской Bаlleri, а сегодня на их изготовлении специализируются итальянская компания Andreoni и некоторые фирмы Тайваня.
Обрабатывающие центры
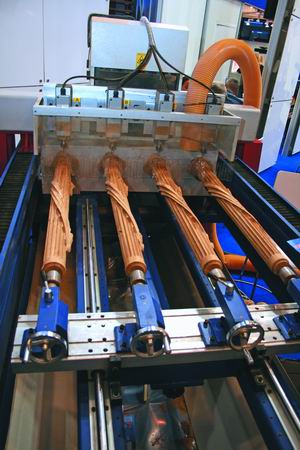
Основное различие станков обоих описанных типов в том, что в первом обработка ведется боковой стороной фрезы, а во втором - преимущественно торцовой.
Поэтому в станках первого типа качество фрезерованной поверхности выше, но на них невозможно получать узкие рельефы с углубленной поверхностью, а вторые обеспечивают такую возможность, но зато полученные заготовки требуют серьезной ручной доработки.
К тому же производительность станков с ручным копированием невысока - в зависимости от сложности рельефа и формы заготовки цикл фрезерования может составлять несколько часов. Поэтому общее число полученных деталей будет прямо пропорционально числу рабочих позиций станка. При этом их качество и объем необходимых доработок напрямую зависят от квалификации оператора - сделанные им пропуски на поверхности детали повторяются многократно.
Чтобы устранить этот недостаток и повысить качество обработки, фирмой Andreoni на основе выпускаемых ею станков был создан многошпиндельный обрабатывающий центр мод. Progress M20, в котором оператора заменило автоматическое устройство, перемещающее копирующий упор и вместе с моделью автоматически поворачивающее заготовки, зажатые в шпинделях.
Но без участия человека все равно не обойтись - загрузка этого центра заготовками выполняется вручную.
В последние два десятилетия для фрезерования деревянных деталей сложной объемной формы стали использоваться обрабатывающие центры с управлением рабочим перемещением инструмента одновременно по пяти пространственным координатам. Они обеспечивают обработку поверхностей как цилиндрическими, так и концевыми фрезами, то есть могут и выполнять объемное фрезерование, и формировать рельефные рисунки. Но недостаток этого оборудования - невысокая производительность, поскольку такие центры оснащены по большей части только одним фрезерующим шпинделем.
Поэтому сегодня объемно-копировальные станки и станки для фрезерования резьбы, в которых используется механическое копирование модели, не потеряли значения и по-прежнему применяются при изготовлении изделий сложной объемной формы и рельефных деталей.
Андрей ПЕТРОВ, компания «МедиаТехнологии», по заказу журнала «ЛесПромИнформ»