Технология изготовления клееных брусков
Трехслойные бруски для оконных блоков стали самостоятельной товарной продукцией на нашем рынке, что отражает разумное разделение труда. Производители столярно-строительных изделий могут сосредоточиться на изготовлении окон и дверей, а полуфабрикаты могут выпускать цеха или предприятия, оснащенные специализированным оборудованием для склеивания древесины, на которых функционирует служба контроля качества.
Производство клееных брусковых заготовок развивается за счет специализированных предприятий, полностью ориентированных на переработку круглого леса на клееные заготовки, а также специализированных цехов при лесопильных заводах, изготавливающих клееную продукцию, основная часть которой - коммерческие пиломатериалы. Во многом это объясняется тем, что на лесопильных предприятиях есть возможность выпиливать пиломатериалы целевого назначения для собственного производства по спецификациям, которые трудно или невозможно выполнить при переработке покупных коммерческих пиломатериалов. Это учет таких параметров, как расположение годичных колец, скорость роста, положение в стволе, способ доставки круглого леса (сухопутный, водный), места произрастания, нестандартная толщина и др.
Главная задача, которую необходимо решать при организации производства клееных заготовок на лесопильных предприятиях, заключаются в том, чтобы обеспечить экономическую конкурентоспособность их товарного производства. Решить эту задачу возможно только за счет экономного использования древесины, сокращения трудозатрат и экономии энергии.
Обеспечить экономное использование древесины в условиях лесозавода возможно как за счет разумных размернокачественных спецификаций на стадии лесопиления, так и за счет комбинации производства клееных заготовок для окон с производством других видов продукции первичной деревообработки, особенно - тех, в которых используется склеивание. Очевидно, что лесопильное предприятие, организующее углубленную обработку пиломатериалов, не может ориентироваться на выпуск только одного вида продукции как с точки зрения объемов обработки, так и с точки зрения эффективного использования всего объема выпиливаемых пиломатериалов.
Экономия трудозатрат возможна за счет применения механизированного и автоматизированного технологического оборудования, которое можно использовать лишь при довольно больших объемах обработки. В этом плане у лесопильного завода имеются безусловные преимущества по сравнению со столярным производством, где объем изготовления брусков ограничивается лишь собственными потребностями.
Экономия энергии - важное требование, предъявляемое к любому деревообрабатывающему производству. В условиях лесозавода, где возможно использование высокопроизводительного оборудования, имеет значение как эффект снижения удельных затрат, так и эффект от использования менее энергоемких методов ускорения процесса склеивания.
К примеру, применение высокочастотного нагрева клееных швов в параллельном поле позволяет в 1,5-1,8 раза уменьшить энергозатраты по сравнению с методами предварительного или периферийного нагрева, но высокая стоимость высокочастотных генераторов окупается лишь при больших объемах склеивания.
Экономия энергии за счет устранения теплопотерь при аспирации и вентиляции, использование для сушки пиломатериалов и отопления помещений генераторов тепла на древесных отходах - также важнейший фактор снижения себестоимости продукции.
В производстве должны быть обеспечены условия, при которых исключается смешение пород древесины на всех этапах подготовки заготовок к склеиванию.
Исключительно высокие требования к древесине для оконных брусков приводят к образованию в технологическом процессе большого количества реек и отрезков. Они отбраковываются по таким признакам, как положение годичных колец, наличие заболони и присердцевинной древесины, скорость роста и другим признакам, которые без ограничений допускаются в таких видах продукции, как клееные щиты и бруски для потребительского рынка.
Представляется разумным предусмотреть возможность изготовления указанной продукции в основной технологии производства оконных брусков. Если производство оконных брусков является составной частью широкого производства клееной продукции, полуфабрикаты, непригодные для изготовления оконных брусков, перейдут на соответствующие участки другого производства.
Подготовка пиломатериалов
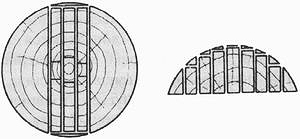
Рис. 1. Развально-сегментная схема раскроя пиловочных
бревен на заготовки
Обеспечение деревообрабатывающего производства пиломатериалами в условиях лесопильного завода лучше организовать с использованием схемы специального раскроя сырья, т. е. развально-сегментным способом (рис. 1). При этом сегменты раскраивают на полуобрезные пиломатериалы, которые после предварительной оторцовки острых концов поступают на сушку вместе с центральными необрезными досками. Этот вариант получения досок для производства клееных брусков считается наиболее эффективным, поскольку позволяет обеспечить максимальный выход заготовок радиальной распиловки, а в сочетании со склеиванием пиломатериалов по ширине - наиболее полное использование объема бревна.
Территориально можно раскраивать толстые пиломатериалы на заготовки и сегменты на полуобрезные пиломатериалы в деревообрабатывающем цехе перед сушкой, однако организационно эти операции лучше выполнять на лесопильном производстве (в цехе или на участке), поскольку сырые рейки и отрезки, получающиеся при раскрое, лучше перерабатывать вместе с отходами лесопильного производства.
Сушка пиломатериалов
Для сушки пиломатериалов необходимы камеры, обеспечивающие равномерную влажность в пределах 2% по всему объему загружаемых в камеру пиломатериалов. Камеры должны быть оснащены системой кондиционирования, обеспечивающей снятие внутренних напряжений в пиломатериалах.
Заготовки для склеивания следует хранить в условиях, исключающих повышение их влажности по сравнению с влажностью, установленной для сушки пиломатериалов.
В отличие от крупногабаритных клееных конструкций, у заготовок для изготовления которых большое сечение, в нашем случае выравнивание влажности может произойти в процессе раскроя, сортировки и накопления заготовок, но очевидно, что такие заготовки перед строганием необходимо контролировать на соответствие заданной влажности.
В соответствии с принятой схемой подготовки пиломатериалов для деревообрабатывающего производства, на сушку поступают доски толщиной не более 40 мм, из них не менее 90% должны быть не толще 25 мм. Хотя сушка тонких пиломатериалов сопряжена со снижением заполнения сушильных камер, однако скорость сушки намного перекрывает эти потери, обеспечивая, в конечном счете, экономию тепловой энергии. Существенным достоинством сушки тонких пиломатериалов является обеспечение высокого качества при небольших затратах энергии на кондиционирование пиломатериалов в камерах и короткие сроки стабилизации влажности на буферных площадках цеха деревообработки. Вместе с тем, сушка тонких досок чревата сильным короблением верхних рядов в сушильном штабеле, и потому необходимо предусматривать способы сжатия пакетов в процессе сушки.
Раскрой пиломатериалов
Предварительный поперечный раскрой досок преследует две основные цели. С одной стороны, он позволяет более эффективно выполнить раскрой досок по ширине, используя сбеговую зону бревен, с другой стороны, дает возможность облегчить обращение с досками, использовать транспортные механизмы с меньшими габаритами и сократить производственные площади.
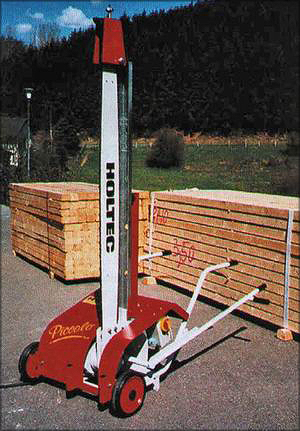
Рис. 2. Передвижная цепная пила с длиной реза 1–2,5
м для пакета пиломатериалов (Holtec)
В последнее время на зарубежных предприятиях поперечный раскрой досок чаще всего выполняется при помощи специальной цепной электропилы, которой сушильный пакет перерезают пополам (рис. 2).
Недостатком способа «слепого» раскроя является то, что на последующих операциях снижается выход мерных заготовок, что ограничивает возможности изготовления брусков с цельными наружными слоями. С этой точки зрения более эффективно использование скоростных торцовочных станков, обеспечивающих индивидуальный раскрой досок на две-три части. Однако такая технология требует для выполнения этой операции постоянного рабочего места. По мнению зарубежных изготовителей клееных брусков, получаемая выгода не оправдывает потери от использования рабочих и специальных станков на этой операции. Потери древесины при предварительном поперечном раскрое связаны с образованием коротких отрезков досок, длина которых не позволяет вести их обработку на деревообрабатывающих станках.
На операции продольного раскроя получают заготовки с параллельными и непараллельными кромками. Основное требование к операции заключается в том, чтобы получить максимум заготовок, свободных от тангенциальной, заболонной и присердцевой зон. Заготовки, содержащие заболонь, используются для изготовления внутренних слоев брусков, заготовки тангенциального распила с углом наклона годичных колец менее 45°, заготовки, содержащие сердцевину, используются при изготовлении клееных брусков и щитов для менее ответственной продукции.
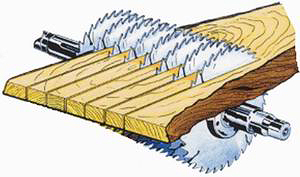
Рис. 3. Схема работы многопильного станка
Операция раскроя выполняется на станке, оснащенном минимум четырьмя пилами (рис. 3), установленными параллельно. Две средних пилы вырезают среднюю зону доски, содержащую сердцевину или тангенциальную зону, а две крайних пилы формируют основную ширину заготовок и отделяют рейки заболонной зоны, которые используются для склеивания по ширине. Если позволяет ширина досок, на станке устанавливают дополнительные пары пил для получения большего количества заготовок требуемой ширины.
При раскрое необрезных досок базовым ориентиром является сердцевина, и для ориентации доски обычно используют лазерный разметчик. При раскрое полуобрезных досок пользуются направляющей линейкой. Для обрезки обзольной кромки по сбегу применяют однопильные станки с гусеничной подачей, оснащенные лазерным разметчиком.
Для того чтобы боковые рейки с непараллельными кромками и рейки из средней зоны доски можно было склеить по ширине, на станках используют пилы, обеспечивающие требуемое качество обработки.
Все заготовки требуемой ширины, полученные на участке продольного раскроя, подвергаются предварительному двухстороннему строганию. Операция выполняется с целью создания оптимальных условий при оценке качества древесины на участке вырезки дефектов и для обеспечения надежной работы оборудования на участке склеивания пиломатериалов по длине. Поскольку широкие заготовки необходимо раскроить на рейки требуемой ширины, эту операцию совмещают со строганием, используя специальные комбинированные строгально-пильные станки. Обычно ширина обработки на этих станках составляет 300 или 600 мм. При обработке цельных реек их подают на строгание, максимально используя рабочую ширину станка. Потери на операции определяются величиной снимаемого слоя, которая обычно принимается 1 мм на сторону. При средней толщине пиломатериала 22 мм потери составляют 9%.
Для продольной распиловки используют пилы минимального диаметра - 250-275 мм, обеспечивающие ширину пропила 2-2,5 мм. При средней ширине рейки 60 мм потери на пропилы составляют около 3%.
Вырезка дефектов
Операция вырезки дефектов определяет качество брусковых заготовок и является весьма трудоемкой. Через эту операцию проходят все заготовки независимо от качества древесины, поскольку помимо вырезки дефектных участков необходимо оторцевать в размер заготовки для наружных слоев в тех случаях, когда они изготовляются цельными.
В настоящее время в зарубежной практике для выполнения этой операции используются только автоматические торцовочные станки и линии оптимизированного раскроя, работающие по меткам. Применение такого оборудования повышает производительность на операции в 3,5-4 раза по сравнению с ручным управлением торцовочными станками, за счет чего сокращаются текущие производственные затраты.
Автоматические торцовочные станки снабжены управляемым механизмом подачи, обеспечивающим перемещение доски со скоростью 90-120 м/мин. и ее точную остановку над пильным диском торцовочного станка по сигналу датчика, обнаруживающего метку, которая нанесена на доску оператором-разметчиком. Станок предназначен только для вырезки дефектов. После раскроя получаются немерные отрезки для склеивания по длине.
Линии оптимизированного раскроя также работают по меткам, однако рез выполняется по сигналу компьютера, в программу которого заложены данные о длине заготовки. В том случае, когда все слои брусков склеиваются по длине, линия работает по программе вырезки дефектов как автоматический торцовочный станок.
Потери на операции определяются насыщенностью пиломатериалов пороками. При средней сортности пиломатериалов, соответствующей третьему сорту по ГОСТ 8486-86, потери на вырезку дефектов составляют 15%.
Сращивание коротких отрезков
Операция склеивания начинается с приготовления клея. Клей должен смешиваться перед использованием строго в соответствии с указаниями изготовителя и должен использоваться в течение периода его жизнеспособности. Добавление в готовый клей новых порций клея, приготовленных в другое время, не допускается. Очевидно, что такое требование относится только к клеям, содержащим активный отвердитель, с коротким периодом жизнеспособности. Двухкомпонентные поливинилацетатные клеи содержат отвердитель с более длительным сроком действия, нежели у карбамидных клеев. По истечении определенного отрезка времени клей не отверждается, но отвердитель теряет свою способность превращать термопластичный клей в термореактивный. Следовательно, по окончании периода жизнеспособности дорогой турбоотвердитель (изоцианат) теряется безвозвратно, а ПВА-клей остается термопластичным с ограниченной водостойкостью клеевого шва.
Клей должен наноситься в объеме, достаточном для полного смачивания поверхностей склеивания, что визуально оценивается по сплошному выдавливанию его из клеевых швов после достижения расчетного давления прессования. Естественно, что это выдавливание должно быть минимальным с точки зрения экономии клея и загрязнения механизмов, однако оно должно быть обязательно зафиксировано, поскольку нет иного способа проконтролировать достаточность нанесения клея.
Особое внимание обращается на периоды открытого и закрытого сборочного времени, поскольку использование клеев, не соответствующих по этим показателям применяемому оборудованию, приводит к весьма крупным дефектам склеивания. Сборочное время зависит от температуры и влажности воздуха в цехе. Обычно оно не должно превышать 10 мин. При использовании поливинилацетатных клеев на этот технологический показатель приходиться обращать особое внимание с учетом усиленной впитываемости клея в древесину. Поэтому необходимым условием качественного склеивания является контроль температуры пиломатериалов, клея и производственного помещения, а в зимнее время и влажности воздуха. Применяемые клеи должны соответствовать используемому оборудованию с точки зрения методов прессования и способов ускорения процесса отверждения клея.
Операция сращивания должна быть рассчитана на склеивание по длине всех слоев клееных заготовок. То обстоятельство, что в некоторых спецификациях могут быть бруски с цельными наружными слоями, не означает, что производительность участка склеивания по длине может быть снижена.
Высокая загрузка оборудования на этом участке определяется не столько физическим объемом производства, сколько размерами склеиваемых отрезков. Толщина отрезков обычно колеблется от 30 до 35 мм и очень редко доходит до 40 мм. Ширина - от 50 до 100 мм. Длина отрезков зависит от качества пиломатериалов и требования к качеству наружных слоев. По опыту работы зарубежных предприятий можно считать, что длина обычно находиться в диапазоне от 150 до 1500 мм, при средней величине около 500 мм. Столь малые размеры отрезков, поступающих на склеивание, требуют применения очень высокопроизводительного оборудования. Наиболее разумным представляется использование линии с конвейерными шипорезами.
Потери древесины на операции сращивания определяются размерами шипов и средней длиной отрезков. При использовании шипов длиной 10 мм зона формирования шипов занимает 15 мм. При средней длине отрезков 500 мм потери на зашиповку составляют 3%. Качество обработки зубчатых шипов должно быть таким, чтобы при незначительном усилии шипы равномерно смыкались, и зазор между боковыми поверхностями не превышал 0,1 мм.
Учитывая особую сложность получения надежных клеевых соединений при склеивании на зубчатый шип, в большинстве стран эта операция регламентируется специальными стандартами. В нашей стране действует ГОСТ 19414-90 «Древесина клееная массивная. Общие требования к зубчатым клеевым соединениям», в странах Евросоюза - EN 385 «Зубчатые соединения конструкционных пиломатериалов. Технические требования и минимальные требования к производству».
Главное требование к процессу создания зубчатых соединений заключается в том, чтобы величина торцового давления соответствовала параметрам применяемых зубчатых шипов, а время поддержания расчетного давления было не менее 2 с. Величина давления прессования для шипов длиной 10 мм для хвойной древесины принимается равной 10 МПа (по отношению к площади торца).
Склеивание слоев по толщине
Для обработки поверхностей склеивания после сращивания используются четырехсторонние строгальные станки легкого класса. Сложность организации работы на участке связана с тем, что при подготовке заготовок к склеиванию иногда необходимо формировать сборки из заготовок разного сечения для наружных и внутренних слоев. При небольших объемах производства партии заготовок разного сечения обрабатывают на одном строгальном станке. При массовом производстве заготовок используют два или три строгальных станка, настроенных на разные сечения и работающих на одну линию склеивания брусков. Чтобы не увеличивать количество обслуживающего персонала, станки оснащаются загрузочными магазинами, что позволяет одному рабочему обслуживать все станки на участке.
Потери древесины на операции строгания определяются величиной снимаемого слоя древесины с заготовок. При обработке предварительно калиброванных заготовок съем стружки составляет 1 мм на сторону, что позволяет ликвидировать незначительные уступы в зубчатых соединениях и обеспечить наиболее качественную обработку поверхности склеивания. На этой операции обрабатывают кромки заготовок с целью калибрования их по ширине. Съем стружки на этой операции составляет 1 мм на сторону. При среднем сечении калиброванных заготовок 30 х 90 мм общие потери на операции составляют около 10%.
Качество обработки поверхностей склеивания заготовок должно контролироваться особенно тщательно, и лучшим вариантом реализации такого контроля является наблюдение за состоянием и режимом работы строгальных станков. Поверхность заготовки перед склеиванием должна быть полностью гладкой и плоской, без видимых глазом волн, образованных на поверхности заготовки в результате фрезерования. Шлифование поверхностей склеивания или устранение дефектов фрезерования с помощью шлифования исключается. Совершенно недопустимо сминание волокон фрезерным инструментом, приводящее к появлению блеска на строганой поверхности или отслоению годичных колец.
Особо оговаривается требование к чистоте обработанных поверхностей, на которых не должно быть пыли, масляных пятен или пятен клея, а также выступившей на поверхность древесной смолы. Обработка поверхностей в любом случае должна выполняться не более чем за 24 часа до склеивания.
На участке склеивания заготовок по толщине выполняются операции комплектования набора заготовок в соответствии с их положением в поперечном сечении клееного бруска, нанесения клея, формирования набора брусков в рабочем промежутке пресса, прессования и, если необходимо, прогрева клеевых швов.
При использовании поливинилацетатных клеев особое внимание следует обращать на сборочное время, которое для этих клеев должно быть сведено к минимуму. Чтобы выполнить это требование, заготовки для брусков должны быть заранее сформированы в количестве, достаточном для загрузки пресса, после чего в возможно короткий срок на них необходимо нанести клей, полностью загрузить пресс и выполнить прессование с требуемым давлением.
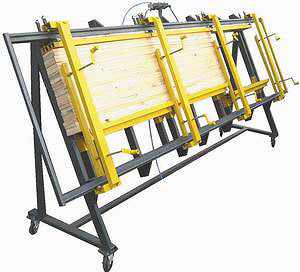
Рис. 4. Пресс вертикальный для склеивания бруса
Для оснащения участков склеивания брусков в настоящее время выпускается самое разнообразное оборудование, отличающееся прежде всего своей производительностью. На рис. 4 представлен общий вид вертикальной ваймы с гидроприжимом. Оборудование такого рода может быть оснащено гидроцилиндрами для создания основного давления (на уровне до 1 МПа) и пневмоцилиндрами для создания бокового давления, которое устраняет поперечное смещение склеиваемых слоев.
Основное требование к процессу прессования заключается в возможности создания и поддержания требуемого давления прессования и его равномерного распределения по всей площади клеевого шва.
Величина давления прессования при склеивании хвойной древесины, плотность которой не превышает 600 кг/м3, должна быть не менее 0,6 МПа. При использовании термопластичных клев и оборудования с нагревательными плитами температура плит не должна превышать 60°С. При использовании нагрева клеевых швов в высокочастотном поле должно быть предусмотрено время на охлаждение шва до 60°С после отключения генератора.
При склеивании «холодным способом» в помещении должна постоянно поддерживаться температура в пределах 16-20°С. При склеивании горячим способом температура воздуха в цехе должна быть не ниже 15°С. В любом случае температура выше 20°С приводит к сокращению сборочного времени, что должно учитываться при отработке режима склеивания в летнее время.
Для склеивания по толщине можно использовать и более производительные импортные прессы, предназначенные для склеивания реечных щитов, поскольку между склеиванием по ширине и по толщине нет принципиальной разницы. Нужно только, чтобы толщина продукции была не менее ширины склеиваемых слоев.
Послепрессовая обработка клееных брусков
В указаниях по использованию клеев их разработчики указывают рекомендуемое время склеивания в прессе при разных способах нагрева или при температуре воздуха в цехе. Считается, что в течение указанного времени клеевое соединение достигает примерно 30-40% его максимальной прочности, но этого достаточно, чтобы извлечь изделие из пресса, перемещать и обрабатывать его на станках без риска разрушения клеевых швов. Однако это обстоятельство означает также и то, что после снятия давления и выемки из пресса изделие должно находиться в отапливаемом помещении цеха или в теплой камере не менее 24 часов при температуре 18-20°С.
При использовании двухкомпонентных поливинилацетатных клеев необходимо иметь в виду, что требуемая водостойкость клеевых швов достигается в течение 7-10 дней при температуре 16-20°С. В летнее время, когда температура окружающего воздуха довольно высока, этот процесс может завершиться при транспортировании или хранении клееных изделий на стройплощадке, однако если таких условий нет или они не могут быть гарантированы в течение указанного периода времени, изделия должны быть выдержаны в отапливаемом складе изготовителя.
Выполнять операцию чистовой оторцовки клееных брусков после их кондиционирования не обязательно, она выполняется чаще всего для придания брускам хорошего товарного вида. Обычно это делается в цехах, оснащенных ваймовыми прессами, в которых бруски формируются вручную. В этом случае выравнивание торцов заготовок затруднено, и это приходиться делать отдельно. В прессах с механической загрузкой торцы выравниваются автоматически, и необходимости в выполнении дополнительной оторцовки нет, если это не оговорено в заказе.
Высокие требования к влажности клееных брусков заставляют обращать внимание на их упаковку. Как правило, транспортные пакеты брусков упаковывают в пленку или водонепроницаемую бумагу.
В отличие от оконных брусков, которые предназначены для промышленного использования, бруски и щиты для потребительского рынка упаковывают поштучно в прозрачную пленку. Поскольку на лесопильно-деревообрабатывающем предприятии вырабатываются и другие виды продукции деревообработки, операция упаковки может выполняться на общем специализированном упаковочном участке.
Контроль качества изделий
Производство клееных брусков требует безусловного и непрерывного контроля качества изготовления. Применительно к клееным брускам в производственных условиях достаточно выполнять лишь два теста: испытание на скалывание по клеевому слою для оценки качества пластевых и кромочных соединений и испытание на статический изгиб для оценки качества зубчатых клеевых соединений.
Согласно требованиям зарубежных стандартов на клееные конструкции, на предприятиях, изготовляющих продукцию, которая эксплуатируется в атмосферных условиях, должны проводиться производственные испытания на расслаивание. Необходимость использования специального оборудования для проведения такого испытания ограничивает возможности его применения в цехах столярных изделий, однако в условиях лесопильных предприятий, при больших объемах производства (и особенно - при выработке других видов клееной продукции) контроль качества клеевых соединений методом расслаивания клеевых швов представляется разумным.
В тех случаях, когда в производстве используются водостойкие термореактивные клеи, метод расслаивания позволяет отказаться от испытаний на скалывание, поскольку он дает более объективные показатели качества склеивания.
При испытаниях продукции, изготовленной с применением двухкомпонентных поливинилацетатных клеев, использование метода расслаивания для текущего контроля качества нецелесообразно, поскольку двухкомпонентный клей приобретает водостойкость только через 7-10 суток после склеивания. Получение результатов через столь длительное время после склеивания не позволяет оперативно влиять на ход технологического процесса. Испытания на скалывание могут выполняться максимум через сутки, при этом можно не принимать во внимание степень водостойкости соединения.
Сказанное относится только к текущему контролю качества клеевых соединений, который выполняется предприятием для поддержания производства на требуемом уровне. Сертификационные испытания, выполняемые третьей стороной при периодических проверках и при аттестации продукции, предусматривают все методы, включая испытания на водостойкость, термостойкость, скалывание по клеевому шву, изгиб зубчатых соединений, расслаивание клеевых швов.
Учитывая особые условия работы лесопильных предприятий, заинтересованных в организации производства продукции на экспорт, представляется разумным при изготовлении опытных партий продукции выполнять испытания по методикам, рекомендуемым институтом оконной техники в г. Розенхайме (ФРГ) для оценки водостойкости, термостойкости и стойкости к расслоению клеевых швов.
Владимир ВОЛЫНСКИЙ