Новые технические решения для повышения эффективности лесозаготовительного производства. Часть 3
Повышение эффективности групповой механической окорки лесоматериалов в окорочных барабанах
Часть 1. Способ определения степени затупления ножей рубительных машин для линии производства технологической щепы
Часть 2. Повышение эффективности облагораживания низкокачественной древесины для подготовки к производству технологической щепы
Часть 4. Устройства для снижения потерь древесины при окорке в окорочных барабанах
Часть 5. Использование сканеров для повышения эффективности чистой окорки лесоматериалов
Стандартная технологическая цепочка работы древесно-подготовительного цеха для выработки технологической щепы (рис. 1) заключается в следующем: бревна, отсортированные по породам, через тарельчатый питатель и ленточный транспортер поштучно подают на колун, которым раскалывают на четыре или шесть частей так, чтобы максимальная ширина сечения расколотого полена соответствовала размерам загрузочного патрона рубительной машины.
Бревна без внутренней гнили и соответствующие по диаметру загрузочному патрону рубительной машины раскалыванию не подлежат.
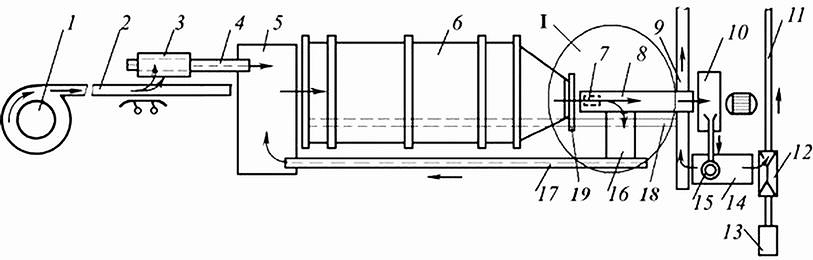
Рис. 1. Схема цеха для выработки технологической щепы:
1 – тарельчатый питатель; 2 – транспортер; 3 – гидроколун; 4 – транспортер; 5 – загрузочная воронка; 6 – окорочный барабан; 7 – металлоискатель;
8 – транспортер; 9 – транспортер отходов; 10 – рубительная машина; 11 – пневмопровод; 12 – шлюзовой питатель; 13 – вентилятор;
14 – сортировочная установка; 15 – циклон; 16 – лоток; 17 – возвратный транспортер; 18 – транспортер для выноса отходов окорки из-под барабана;
19 – шандор; I – модернизируемый узел
Бревна и колотые поленья транспортером, расположенным под колуном, подают в загрузочную воронку, откуда они поступают в окорочный барабан непрерывного действия. Вышедшие из барабана окоренные бревна и поленья по ленточному транспортеру (под которым установлен металлоискатель) подают в рубительную машину.
Плохо окоренные бревна и поленья с ленточного транспортера через лоток сбрасывают вручную на транспортер, возвращающий их в загрузочную воронку для повторной обработки в окорочном барабане. Причем оценку качества окорки визуально дает оператор, который сбрасывает лесоматериал на возвратный транспортер.
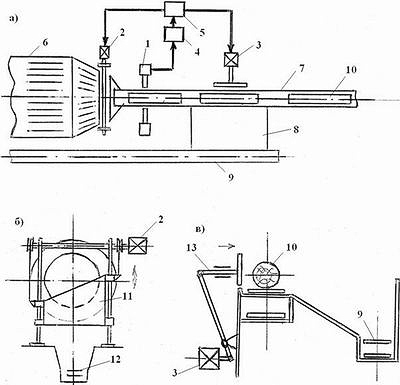
Рис. 2. Модернизируемый узел:
а – схема узла после модернизации; б – вид на шандор;
в – сбрасыватель плохо окоренных бревен; 1 – узел сканирования;
2 – привод шандора; 3 – привод сбрасывателя плохо окоренных бревен;
4 – блок информации; 5 – блок программного обеспечения;
7 – транспортер окоренных бревен; 8 – лоток;
9 – транспортер возврата плохо окоренных бревен на доокорку в барабан;
10 – окоренное бревно; 11 – шандор;
12 – транспортер выноса отходов окорки;
13 – толкатель сбрасывателя бревен
Если на выходе из окорочного барабана образуется значительное количество плохо окоренных лесоматериалов, например бревен с содержанием коры на древесине более 30%, то принимают решение увеличить период нахождения лесоматериалов в барабане. Это достигается за счет уменьшения живого сечения выхода путем перемещения шиберного щита (шандора), например вверх (рис. 2, а), в зависимости от конструкции барабана. И наоборот: если качество окоренных лесоматериалов высокое, то увеличивают живое сечение выхода путем опускания шандора, увеличивая производительность барабана и снижая потери древесины.
Физико-механические свойства сырья, поступающего в древесно-подготовительный цех, постоянно меняются. Прежде всего они зависят от размеров (длины и диаметра), породы, влажности и температуры древесины.
Установлено, что для обеспечения требуемого качества окорки лесоматериалы разной длины требуют разной продолжительности окорки. Короткомерные лесоматериалы окариваются быстрее длинных.
Причем загрузка и разгрузка барабана осуществляются единовременно, а разгрузка производится тогда, когда все лесоматериалы достигают требуемой кондиции. Различие оптимальной продолжительности окорки бревен разной длины отрицательно сказывается на производительности барабана, трудоемкости окорки 1 м3 лесоматериалов, энергоемкости процесса, а в итоге на себестоимости окорки 1 м3 древесины.
Качество окорки и ее продолжительность также зависят от диаметра лесоматериалов. У бревен разного диаметра толщина коры разная: чем больше диаметр, тем толще кора. Для разрушения массивов коры бревен разного диаметра требуется разная продолжительность окорки в барабане.
Следует отметить, что с момента начала поступления брака (выхода из барабана плохо окоренных бревен) до момента принятия решения об изменении режима работы барабана проходит некоторый период, в течение которого значительный объем лесоматериалов подается на повторную окорку, что снижает производительность потока, приводит к повышенному расходу энергии и потерям древесины.
Хорошо окоренную древесину направляют в рубительную машину для производства технологической щепы.
Из рубительной машины щепа через циклон подается на верхнее сито плоской сортировочной установки. Отсортированная кондиционная щепа через шлюзовой питатель поступает в пневмопровод пневмотранспортной установки и доставляется на склад готовой продукции. Воздушный напор в пневмопроводе создается вентилятором высокого давления. Крупные щепки и мелочь, выявленные на сортировочной установке, а также отходы из-под окорочного барабана выносятся из цеха ленточным транспортером.
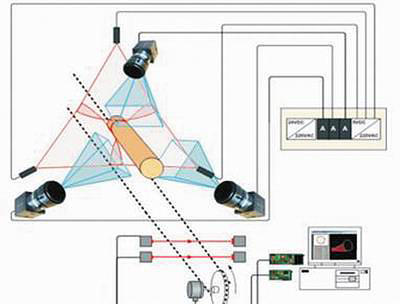
Рис. 3. 3D-сканер
Для повышения эффективности работы описанного выше производственного потока за счет обеспечения точной оперативной автоматизированной оценки качества окорки и управления процессом возврата бревен на дополнительную окорку, повышения производительности линии, снижения энергоемкости процесса и потерь древесины сотрудники ЛИФ СПбГЛТУ разработали оригинальное техническое решение: между окорочным барабаном и ленточным транспортером устанавливается лазерный 3D-сканер (рис. 3).
В качестве такого сканера можно использовать, например, сканер «ВЕКТОР.3D», который состоит из системы видеокамер и лазерных маркеров, расположенных под углом друг к другу. Лазерные лучи, следуя по контуру бревна, создают его трехмерное изображение, которое с видеокамер передается в процессор компьютера, где оно преобразуется в цифровой вид и обрабатывается специальным программным обеспечением. Результатом обработки контура сечения бревна является определение размеров и формы бревна, а также выявление пороков древесины на поверхности бревна: выпуклостей (сучков, наростов) и впадин (дупел), пятен коры, оставшейся после окорки. Прочие параметры бревна (объем, кривизна, сбег и т. д.) вычисляются на основании результатов измерения диаметра и длины бревна.
Достоинства 3D-сканера:
- реалистичные результаты 3D-измерений;
- возможность монтажа на все типы транспортеров;
- отсутствие необходимости разрыва конвейера;
- надежность в эксплуатации;
- устойчивость к климатическим изменениям.
Технологические операции процесса окорки выполняются в такой же последовательности, как описано выше, вплоть до прохождения бревен и поленьев, вышедших из окорочного барабана, через узел оценки качества окорки. Информация о качестве окорки бревен и поленьев, прошедших через узел сканирования, поступает в блок информации и обрабатывается в блоке программирования, после чего качественно окоренные бревна и поленья по ленточному транспортеру (под которым установлен металлоискатель) подают в рубительную машину.
Плохо окоренные бревна и поленья по команде блока программирования с ленточного транспортера с помощью приводного сбрасывателя через лоток сбрасывают на транспортер, возвращающий «некондицию» через загрузочное отверстие в окорочный барабан для повторной обработки в окорочном барабане. Привод шандора по команде блока программирования будет перемещаться вниз, уменьшая живое сечение выгрузочного отверстия, что обеспечивает повышение качества окорки благодаря длительной окорке бревен и поленьев.
Необходимую степень окорки бревна П (%) в зависимости от требуемой марки изготавливаемой щепы в соответствии с табл. 1 компьютерная программа блока программирования определит по формуле
где S - площадь боковой поверхности бревна, м2; S1 - площадь неокоренной поверхности бревна, м2.
Хорошо окоренную древесину направляют в рубительную машину для производства технологической щепы.
Из рубительной машины щепу через циклон подают на верхнее сито плоской сортировочной установки. Отсортированная кондиционная щепа через шлюзовой питатель поступает в пневмопровод пневмотранспортной установки и доставляется на склад готовой продукции. Воздушный напор в пневмопроводе создают вентилятором высокого давления. Крупные щепки и мелочь, выделенные на сортировочной установке, а также обломки коры, отщепы древесины и прочее, выпадающее из барабана, выносятся из цеха ленточным транспортером.
Предлагаемое техническое решение позволит повысить эффективность линии изготовления технологической щепы за счет обеспечения точной автоматизированной оценки качества окорки и оперативного управления процессом возврата бревен на дополнительную окорку, повышения производительности линии, снижения энергоемкости процесса и уменьшения потерь древесины.
Игорь ГРИГОРЬЕВ, д-р техн. наук,
Борис ЛОКШТАНОВ, канд. техн. наук,
Ольга КУНИЦКАЯ, канд. техн. наук,
Антон ГУЛЬКО, аспирант,
кафедра технологии лесо-заготовительных производств СПбГЛТУ