«Полеко». Комбинат на северном Юге
В этом заголовке нет оговорки или ошибки. Пока мы ехали на машине от железнодорожной станции Шарья, что в Костромской обл., до пос. Демьяново, что в Кировской обл., дорога трижды пересекла этот правый приток Северной Двины. Река Юг играла и играет важную роль в судьбах поселка и комбината «Полеко», расположенных на ее берегу.
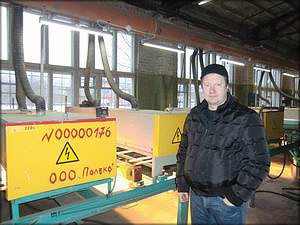
Представитель совета директоров ГК «Демьяновские мануфактуры» Станислав Полынько: «Мы и далее будем следовать курсу на модернизацию оборудования и освоение новой продукции»
Поселок Демьяново, с которым неразрывно связана история ООО «Полеко», в этом году отмечает «круглую» дату - 60 лет со дня образования. 18 августа 1951 года Совет Министров СССР принял решение о строительстве в Кировской области, на правом берегу реки Юг, в 10 км от пос. Подосиновец лесоперевалочной базы. Стройка была объявлена всесоюзной комсомольско-молодежной, и воплощать в жизнь задуманное по комсомольским путевкам сюда приехали 97 человек из Кировской области и 350 из разных республик и областей СССР. В хвойном лесу через заболоченные участки, небольшие реки и буреломы была проложена железная дорога, возведены дома для строителей. Так был заложен пос. Демьяново, годом рождения которого считается 1954-й.
В 1960 году был образован Подосиновский лесоперерабатывающий комбинат, в состав которого вошли: железнодорожная ветка Юг - Панасюк протяженностью 32 км, временное домостроительное предприятие, лесопилка, участок перевалки леса, подразделение механизаторов. Заготовленную древесину пилили на лесорамах, пиломатериалы шли на строительство самого поселка и на другие нужды. На момент образования комбината в его штате числилось 243 человека. С 1960 года началась поэтапная модернизация предприятия. В 1964 году был пущен четырехрамный лесопильный цех, в 1966 году - цех готовой продукции, в 1968-м - деревообрабатывающий цех. В 1977 году был подписан акт государственной комиссии по приемке комплекса по производству древесноволокнистой плиты, в состав которого вошли два потока, оснащенных оборудованием польской компании Zemak с общей проектной мощностью 20 млн м2 плиты в год, котельная на семь котлов, водопроводные очистные сооружения и канализационные очистные сооружения биологической очистки, которые до сих пор обслуживают не только комбинат, но и весь поселок.
Старожилы вспоминают, что выпуск первой плиты 24 декабря 1977 года был большим праздником: при стечении большого количества людей ковер перед загрузкой в пресс был остановлен, и все присутствовавшие положили на него листочки бумаги со своей подписью, после запрессовки плита была распилена на множество частей, которые были разобраны участниками мероприятия.
В доперестроечный период комбинат был одним из крупнейших в стране: здесь в больших объемах велось лесопиление (по реке Юг был организован молевой сплав древесины из Вологодской обл.), помимо ДВП выпускались пиломатериалы, погонаж, паркет, коллектив предприятия насчитывал почти две тысячи человек. Плитная продукция комбината пользовалась спросом и вся потреблялась внутренним рынком - в СССР тогда были большие объемы строительства, ДВП требовалась и машиностроителям - для упаковки оборудования, и торговым организациям - для продажи населению, и производителям мебели. Но с наступлением перестройки многие производства были закрыты, линии остановлены, производственные корпуса пришли в негодность, обветшали...
Возрождение предприятия началось с приходом нового собственника. Сегодня ООО «Полеко» (название образовано от слов «Подосиновский лесоперерабатывающий комбинат»), которое безусловно является градообразующим предприятием (здесь трудятся 600 человек из 6200 жителей поселка), прочно удерживает за собой место в числе ведущих производителей ДВП в России и развивает новые, перспективные направления деятельности.
Основное производство комбината «Полеко»
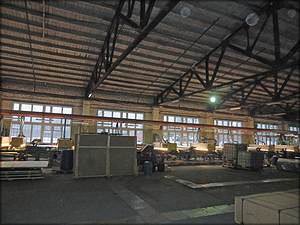
В цехе окраски древесноволокнистой плиты
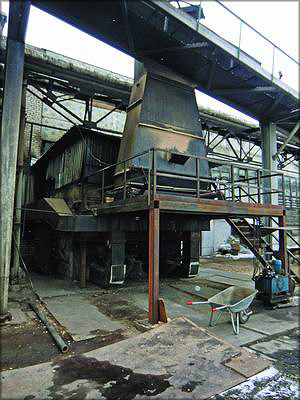
Выносная топка котельной с бункером загрузки
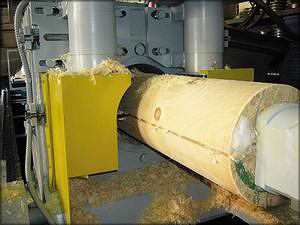
Для изготовления оцилиндрованного бревна закуплено современное оборудование
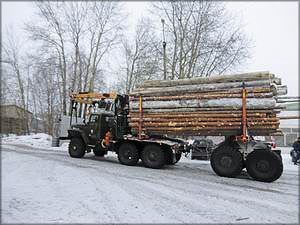
В ворота комбината одна за одной въезжают груженые сортиментами и продуктами лесопиления автомашины
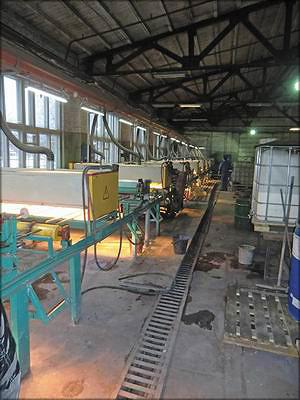
Линия окраски ДВП
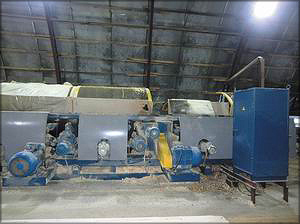
Станок «Шервуд 692С»
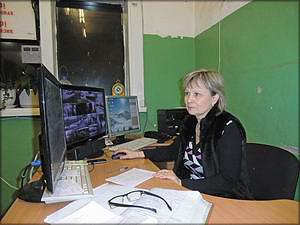
Начальник комплекса ДВП Екатерина Бестужева
Так на комбинате называют комплекс по выпуску древесноволокнистых плит «мокрым» способом. Ежемесячно здесь производят более 2 млн м2 твердой ДВП толщиной 2,5 и 3,2 мм (в том числе 250 тыс. м2 окрашенной), которая весьма востребована как на внутреннем рынке, так и за рубежом.
«Некоторые специалисты считают, что время ДСП и ДВП прошло, что их сейчас на рынке все больше теснят такие современные материалы, как MDF и OSB. Но мы-то видим, что спрос на качественную древесноволокнистую плиту только растет, - говорит временно исполняющий обязанности генерального директора ООО «Полеко» Валерий Пахолков. - Среди потребителей нашей продукции - предприятия мебельной отрасли, строители, машиностроители, торговые компании из разных регионов России. Наша плита востребована в странах СНГ, например, в Киргизии, Казахстане, Узбекистане. Есть у нас партнерские отношения и с заказчиками из Швеции, Бельгии...» В сутки предприятие отгружает заказчикам от 100 до 120 тыс. м2 плит, причем почти 80% из объема - экспортная продукция.
На фоне того, что в странах Западной Европы закрываются даже крупные лесопильные, деревообрабатывающие, плитные производства с высокой степенью автоматизации, перспективы увеличения объемов выпуска продукции на комбинате «Полеко» и расширения ее ассортимента обретают все более зримые черты. Тем более что здесь для этого имеются все условия: надежное высокопроизводительное оборудование, которое содержится в хорошем состоянии и постоянно модернизируется, обеспеченность необходимым сырьем, квалифицированные кадры, реальная программа перевооружения производственных мощностей, освоения новых технологий и новых видов продукции.
Рассказ о производственном процессе изготовления ДВП и потенциале предприятия мы начнем с описания возможностей основного технологического оборудования, поставленного в Демьяново в далеком 1977 году, потому что надежность и стабильность этого оборудования - краеугольный камень успешной работы предприятия. Это оборудование польской фирмы Zemak безотказно работает на комбинате уже почти 37 лет! Конечно, за эти годы оно не раз проходило плановые и капитальные ремонты, почти треть его узлов и агрегатов уже заменены отечественными аналогами (компания Zemak уже не существует, и поэтому не приходится говорить о запчастях, которые можно было бы получать от производителя). Но серьезных проблем не возникало, ежегодно на польском оборудовании изготавливали плиты, в объеме, который не только соответствовал заявленной проектной мощности, но и превосходил ее.
«20 млн м2 плиты в год - для нас не предел, - говорит Валерий Васильевич. - Еще в советское время на одном из потоков мы провели модернизацию пресса и к 25 заводским этажам добавили еще три, изготовленные собственными силами. В результате общая мощность оборудования достигла 20,872 млн м2 в год. А в 2006-2007 годах мы добились рекордной годовой выработки - 23,443 млн м2. Забегая вперед, скажу, что в результате реализации ряда мероприятий по модернизации этого оборудования мы рассчитываем достичь годового объема выпуска плиты на уровне 25 млн м2».
О том, что добиться такого показателя вполне реально, говорят результаты выработки, достигнутые в двух последних месяцах 2013 года. В ноябре и декабре прошлого года на предприятии проводилось соревнование четырех смен, целью которого было достижение максимальной производительности. Для победы требовалось выполнить 58 запрессовок за смену на первом потоке и 55 запрессовок - на втором. Работники комбината с энтузиазмом включились в трудовое состязание, и в результате в ноябре 2013 года было произведено 2 106 535 м2 древесноволокнистой плиты, в декабре - 2 214 611 м2. Такие рекордные объемы выработки были достигнуты впервые за все время существования комбината.
Рекордных результатов удалось достичь не только благодаря техническому перевооружению производства, совершенствованию технологий и производственному опыту, но и за счет прекрасного знания возможностей оборудования и внимательного, бережного отношения к нему. Раз в год линии останавливают на капитальный ремонт, в соответствии с графиком выполняются работы по планово-предупредительному ремонту.
«Часть работ по модернизации и обновлению оборудования мы проводим своими силами, - говорит генеральный директор комбината. - А для выполнения сложных операций капремонта приглашаем подрядчиков, квалифицированных отечественных специалистов, заранее составляем план мероприятий. В прошлом году специалисты вологодской компании "Союзлесмонтаж" заменили несущую колонну пресса».
Еще одним ярким примером того, что на «Полеко» работают настоящие профессионалы, болеющие за судьбу своего комбината и умеющие находить блестящие организационные решения, которые положительно влияют на эффективность работы предприятия, стал перевод котельной с жидкого топлива (мазута) на биотопливо (отходы деревообработки). До 2010 года комбинат сильно зависел от поставок мазута, который использовался в качестве топлива для котельной, а котельная не только снабжает технологическим паром основное производство, но и обеспечивает в зимнее время отопление всех производственных помещений предприятия, а также части домов в поселке. С вступлением страны в рыночную экономику и резким ростом цен на нефтепродукты комбинат столкнулся с большими проблемами. Чтобы понять их масштаб, достаточно сказать, что общая производительность четырех котлов отечественного производства (трех - ДКВР-10 и одного - ДКВР-20) - 40-45 т пара в час, для выработки которых требуется большой объем топлива.
«Дошло до того, что доля тепловой энергии, вырабатываемой котельной комбината, в себестоимости продукции достигла 55%! Это было просто губительно для производства, которое день ото дня становилось все более нерентабельным, - рассказывает г-н Пахолков. - В этой непростой ситуации руководством комбината было принято решение, которое поддержали наши акционеры, - перепрофилировать котельную с мазута на твердое топливо - опилки, щепу, обрезки пиломатериалов. Но требовалось решить две непростые задачи: провести техническое переоборудование котлов и обеспечить постоянное снабжение котельной необходимым количеством биотоплива. Было подсчитано, что для бесперебойной работы котельной в сутки надо сжигать в топках котлов более 550 м3 биотоплива».
Специалисты комбината блестяще решили обе задачи, а попутно и еще несколько, которые оказали влияние не только на повышение рентабельности и эффективности работы ООО «Полеко», но и способствовали улучшению экономики и экологии в Подосиновском районе. Для того чтобы стало понятно, о чем речь, коротко пройдемся по основным этапам технологической цепочки изготовления древесноволокнистой плиты на комбинате.
Сырье для ДВП, топливо для котельной
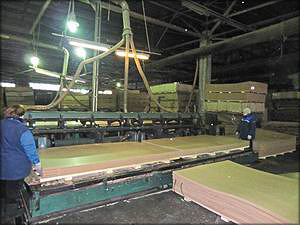
Так формируются пачки из листов ДВП
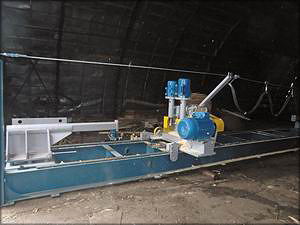
Станок «Шервуд ОФ32»
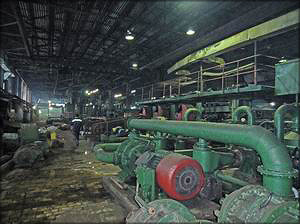
Оборудование польской фирмы Zemak, на котором изготавливают ДВП, безотказно работает на комбинате уже почти 37 лет!
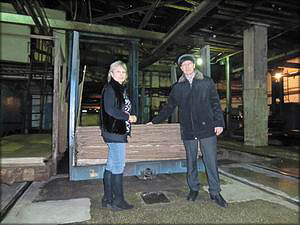
Врио генерального директора ООО «Полеко» Валерий Пахолков и начальник комплекса ДВП Екатерина Бестужева оценивают качество готовой продукции
Сырье для переработки в технологическую щепу комбинат закупает у многочисленных небольших компаний, занимающихся лесозаготовкой и деревообработкой как в Подосиновском районе, так и в соседних с ним районах. В ворота предприятия круглосуточно, почти без перерывов, одна за одной въезжают груженые сортиментами и продуктами лесопиления автомашины, что неудивительно, ведь суточная потребность комбината в сырье - 1200 м3: не менее 650 м3 древесины хвойных пород и 500-550 м3 березовой и осиновой. Для наглядности: это приблизительно 200 КамАЗов с наращенными бортами, груженных доверху лесоматериалами и технологической щепой. А в связи с переводом котельной на твердое биотопливо требовалось обеспечить его бесперебойное поступление также в огромном объеме.
«Когда встал вопрос - где брать твердое топливо для котельной, мы сразу обратили внимание на частные лесопилки и малые деревообрабатывающие предприятия в нашем районе, у которых в результате их деятельности скапливается большое количество древесных отходов - реек, обрезков, горбыля, опилок, - говорит Валерий Васильевич. - Все это раньше просто выбрасывалось на свалку, что создавало большие проблемы как для окружающей среды, так и для самих предпринимателей, которым приходилось платить штрафы. Мы предложили этим предприятиям выгодное сотрудничество, и теперь эти отходы поставляются для нашей котельной. Довольны все: у нас нет проблем с биотопливом, у местных бизнесменов не болит голова о том, куда девать отходы производства, с территории района исчезли свалки древесных отходов».
В связи с резко выросшим объемом поступающего древесного сырья на комбинате разработали и реализовали специальную программу перевооружения участка приготовления щепы и установили на нем дополнительные рубительные машины, которые эксплуатировались на нижнем складе комбината еще в те времена, когда бревна доставлялись на рейд предприятия на реке Юг молевым сплавом. В составе оборудования участка - рубительные машины отечественного производства: две МРН-40 и МРГ-40 - для переработки в щепу реек и горбыля, МРГ-8-50 ГН - для переработки толстомерного сырья - сортиментов диаметром до 850 мм, а также две МРН-100, на которых перерабатываются бревна диаметром до 450 мм и длиной до 6 м.
Далее щепа ленточным транспортером доставляется на ситочные сортировки, после чего по одному транспортеру фракционная щепа отправляется на размол, а отсеянная некондиционная мелочь по другому транспортеру - в накопительный бункер, откуда загружается в самосвал и отвозится к котельной, где используется в качестве топлива. К котельной мы еще вернемся, чтобы рассмотреть - каким оригинальным и в то же время простым способом была решена проблема переоборудования котельных топок. А пока продолжим своеобразную экскурсию по технологической цепочке изготовления ДВП, в которой меня в качестве экскурсоводов сопровождали генеральный директор «Полеко» и начальник комплекса ДВП Екатерина Бестужева.
Отсортированная фракционная щепа поступает в гидромойку, где очищается от пыли, грязи, песка, после чего с помощью реверсной тележки засыпается в бункеры, которые расположены над дифибраторами; здесь после пропарки выполняется первая ступень размола. Затем распаренные волокна по массопроводу отправляются в горизонтальные ванны, а оттуда - на рафинаторы, в которых волокна измельчаются еще больше, и далее - в массные бассейны. Из этих бассейнов масса, в которую, исходя из конкретного задания - какую именно плиту надо изготовить в соответствии с заказом, добавлены связующие вещества и другие необходимые ингредиенты, поступает в отливную машину - на формирование ковра.
«Открою один из наших секретов, - делится нюансами технологии Валерий Пахолков. - Для изготовления плиты марки ТС мы отправляем часть волокон после рафинатора на дополнительное измельчение. Этой тонко размолотой массой заливается верхний слой ковра, и поверхность плиты после выхода из пресса получается очень ровной, гладкой и красивой. Такая плита используется для окраски или для специальных целей заказчика».
Сформированный ковер проходит между валами, из массы отжимается часть воды, которую отсасывают вакуумные насосы, ковер распиливается на полотна определенной длины, и по транспортерам мокрого ковра эти полотна поступают на пресс. Здесь они в автоматическом режиме загружаются на полки этажерок, на транспортные листы и на сетки спецназначения. Затем эти полки проталкиваются в пресс, где и выполняется запрессовка. Одновременно с загрузкой полок в пресс автоматически выполняется выгрузка из него запрессованных полотен. После сушки и закалки полотна по наклонному транспортеру поступают на типель - этажерки, которые доставляются к станку форматной резки, и станочники раскраивают их на листы в соответствии с ГОСТом или с условиями заказчика. Готовые ДВП либо упаковывают в пачки для отправки автомобильным транспортом, либо готовят для погрузки в железнодорожные вагоны.
Ну а теперь самое время рассказать о том, как был выполнен перевод котельной с мазута на твердое биотопливо и как это повлияло на эффективность работы комбината. Обычно в таких случаях либо происходит замена котлов на оборудование, которое предназначено для использования твердого биотоплива, либо конструкция котлов претерпевает серьезные изменения. Специалисты предприятия нашли простое решение, не потребовавшее ни того, ни другого.
К каждому из четырех котлов на улице под специальным навесом высотой 11 м пристроили выносные топочные устройства, которые соединены с котлами особыми каналами. Причем, работа эта была выполнена в сжатые сроки и в непростых погодных условиях - в Демьяново тогда трещали морозы под 40°C.
Из приемного бункера, в который после сортировки поступают некондиционная щепа, привозимые с лесопильных и деревообрабатывающих предприятий района опилки и дробленые обрезки пиломатериалов, твердое топливо по ленточному транспортеру длиной 80 м подается в эти выносные топки. Год назад к каждому выносному устройству специалисты компании «Лесэнерго» смонтировали воздухоподогреватели, что позволило существенно повысить эффективность горения древесного топлива.
«Горячий воздух от экономайзера по воздуховодам поступает к топкам и подсушивает влажные щепу и опилки, которые подаются на ворошители топок. Таким образом обеспечивается устойчивое, эффективное горение и исключаются заминки в режиме подготовки пара, - рассказывает врио генерального директора ООО «Полеко». - Вырос кпд котлов, резко - на 56 тыс. м3 в год - сократились вредные выбросы в атмосферу, повысилась рентабельность производства, что не могло не сказаться на себестоимости продукции и ее конкурентоспособности».
Развитие и конкурентоспособность комбината «Полеко»
Из сказанного выше вполне можно сделать вывод о том, что на комбинате работают настоящие профессионалы, знатоки своего дела, творческие люди, которые не успокаиваются на достигнутом и постоянно думают над совершенствованием технологии и улучшением кондиций выпускаемой ДВП. Вот еще один пример, подтверждающий это. Известно, что для изготовления древесноволокнистых плит в качестве связующего используется фенолформальдегидная смола, и всем производителям плитных материалов приходится решать проблему - как обеспечить соответствие своей продукции строгим требованиям экологических нормативов.
«Наши технологи, взяв за основу тот факт, что в хвойной древесине содержится природная смола, которая вполне может играть роль связующего, разработали рецептуры массы без использования ФФ смолы, - говорит Валерий Васильевич. - В сутки наши рубилки МРН перерабатывают в щепу 600 м3 хвойной древесины, что позволяет нам выпускать в полном смысле слова экологически чистую ДВП. Такая плита особенно ценится производителями детской и школьной мебели, мебели для учреждений здравоохранения».
Безусловно, рынок не мог не отреагировать на изменения, которые происходят на комбинате, и сегодня у «Полеко» нет недостатка в заказчиках и деловых партнерах. Тем более что у плитной продукции комбината прекрасная репутация среди потребителей, которые ценят ее за отличные характеристики и высокое качество. К качеству продукции здесь особое внимание. Конечно, на всю продукцию имеются все необходимые сертификаты. На предприятии есть собственная сертифицированная лаборатория, сотрудники которой ведут круглосуточное наблюдение за всеми нюансами режимов производства. В каждой смене лаборант-технолог следит за соблюдением параметров процесса, установленных старшим технологом для конкретной партии плит в зависимости от условий заказа (длина ковра, его геометрия, толщина, прочность на разрыв, показатель влагостойкости и т. д.).
«Для нас критериями качества были и остаются советские ГОСТы, в которых требования к продукции по некоторым позициям гораздо жестче, чем в действующих сегодня европейских нормативах. Безусловно, это один из факторов того, что наше предприятие экономически устойчивое и конкурентоспособное, - говорит г-н Пахолков. - В то же время мы понимаем, что нельзя останавливаться на достигнутом, надо смотреть в будущее, развиваться, осваивать новые сегменты рынка, выпускать новые, соответствующие современным требованиям потребителей, материалы». Творческий поиск технических специалистов комбината привел к созданию особой технологии глубокой переработки древесины, в результате чего на российском рынке древесных плит появился инновационный продукт - уникальная, перспективная сверхпрочная плита Steelboard.
«Перед нами была поставлена задача - в условиях существующего производства, на действующем оборудовании организовать выпуск сверхпрочной плиты с такими характеристиками, которых нет у продукции наших конкурентов, работающих на аналогичном оборудовании, - рассказывает врио генерального директора комбината «Полеко». - Трудность состояла в том, что для производства плит такого типа требуются закалочные камеры, которых у нас нет, и которые в России выпускает только единственный завод. Нашим специалистам удалось разработать особую рецептуру и технологию изготовления сверхтвердой плиты, соответствующей требованиям ГОСТа, без использования закалочных камер. Не раскрывая всех секретов, скажу только, что результата удалось добиться благодаря подбору ингредиентов массы, в составе которой решающее значение играет щепа хвойных пород, а также корректировке параметров технологических режимов, начиная с участка приготовления щепы и заканчивая запрессовкой, да плюс после пресса готовой плите надо выстояться определенный отрезок времени».
Была выпущена опытная партия плиты Steelboard, которая по твердости соперничает с фанерой и другими твердыми древесными материалами, кроме того, у этой плиты самый низкий среди древесных плит коэффициент водопоглощения и разбухания, а ее однородная плотная структура обеспечивает отличные возможности ее механической обработки. А благодаря уникальному технологическому процессу производства в процессе эксплуатации и утилизации изделий из такой плиты сохраняется экологичность продукта, что подтверждено гигиеническими сертификатами и европейским знаком качества NFB (Natural FiberBoard).
«Свою новинку мы презентуем на разного рода мероприятиях, на выставках, предлагаем своим постоянным заказчикам небольшие партии для ознакомления с этим материалом. Уверены, плита Steelboard по достоинству будет оценена рынком и найдет своего потребителя так же, как нашла его наша новая продукция - окрашенная плита», - говорит Валерий Пахолков.
Какое-то время назад менеджмент комбината обратил внимание на то, что некоторые постоянные заказчики демьяновской ДВП после получения очередной партии плит красили их на своих производствах, а затем перепродавали на рынке уже как другой продукт - окрашенную ДВП. На «Полеко» быстро сориентировались и купили линию окраски, организовали собственное производство окрашенной плиты.
«Сейчас при двухсменной работе на этом участке мы выпускаем в месяц примерно 250 м2 окрашенной плиты в цветовой гамме от белого до имитации под натуральную древесину. В основном заказчики такой плиты - предприятия мебельной промышленности, спрос растет, и если тенденция сохранится, то мы сможем легко организовать работу в четыре смены и добиться выпуска 500 м2 окрашенной плиты в месяц», - делится планами руководитель комбината.
«Демьяновские мануфактуры»
Итак, в последние годы ООО «Полеко» активно развивалось и вышло на новый уровень: вырос объем, повысилось качество производства древесноволокнистой плиты, создан цех окраски и освоен выпуск окрашенной ДВП. Одним из серьезных шагов в плане развития предприятия станет организация на территории комбината «Полеко» лесопильного производства и домостроительного комплекса, что позволит предприятию получить новый статус. На базе «Полеко» создается группа компаний - технопарк под единым названием «Демьяновские мануфактуры». Название «Демьяновские мануфактуры» отражает суть стратегии развития промышленной площадки. Образцы новых видов продукции, выпускаемые сегодня комбинатом, - ДВПО, евровагонка, пиломатериалы, а также проекты деревянных домов под брендом «Демьяновские мануфактуры» были представлены в рамках выставки «Деревянное домостроение» в марте 2014 года. Как показали опросы, проводившиеся во время выставки, новое название бренда «Демьяновские мануфактуры» - и стратегия развития группы компаний были положительно восприняты рынком.
Немного подробнее о развитии нового направления - производстве материалов для деревянного домостроения и домокомплектов деревянных домов. На территории комбината «Полеко» организован участок лесопиления, который занимается обработкой круглого лесоматериала для изготовления оцилиндрованного бревна и обрезной доски. Участок оснащен современным высокопроизводительным оборудованием. Многофункциональный (оцилиндровочно-фрезерно-пильный) станок марки «Шервуд 692С» предназначен для переработки круглых тонкомерных лесоматериалов с целью изготовления высококачественного обрезного пиломатериала, заготовки под доску пола и обшивочную доску. За одну подачу из бревна, которое подвергается сразу трем операциям - оцилиндровке, фрезерованию и распиловке, можно получить пиломатериал точных размеров, с высоким качеством поверхности. Кроме того, был приобретен один из лучших отечественных станков - оцилиндровочно-фрезерный станок «Шервуд ОФ32», а также станок для вырезки на оцилиндрованном бревне замковых соединений. Это оборудование позволит изготавливать оцилиндрованные бревна диаметром до 320 мм, которые будут использоваться для производства комплектов домов по индивидуальным заказам, а также бань и беседок. Домокомплекты сначала будут изготавливать по типовым проектам, а затем, по мере увеличения количества заказов, и по индивидуальным.
«Уверены - недостатка в заказах у нас не будет, сейчас уже в нашем "портфеле" несколько десятков заказов есть, - добавляет заместитель генерального директора ГК «Демьяновские мануфактуры» Андрей Дешин. - Мы серьезно подготовились к выходу на рынок домостроения. Помимо производства оцилиндрованного бревна и домокомплектов из него, мы планируем изготавливать клееный брус, из которого также будем делать домокомплекты».
С этой целью у компании «КАМИ» приобретена линия для высокоточной деревообработки: строжки ламелей, зарезки шипов, сращивания ламелей, укомплектованная высокопроизводительными современными станками Beaver. Кроме того, здесь будут выпускать евровагонку, доску пола, блок хаус и другие погонажные изделия. Станочники прошли подготовку под руководством специалистов ООО «Шервуд» (г. Киров) и Ассоциации «КАМИ».
«Уже приобретен и готовится к установке современный сушильный комплекс», - говорит представитель совета директоров Станислав Полынько.
С развитием домостроительного комплекса руководство холдинга связывает большие надежды.
«Есть у нас идея создания в регионе, на местном уровне, компактных экопоселков, которые будут построены из наших домов из оцилиндрованного бревна, - делится планами Станислав Полынько. - Для того чтобы сделать эту идею привлекательной для потребителя, мы планируем оформить наше предложение в виде пакета услуг. Мы хотели бы, чтобы обратившись к нам, клиент мог получить "из одних рук" земельный участок, дом из оцилиндрованного бревна и ипотеку под приемлемый процент на длительный срок. С этой идеей мы обратились к руководству Кировской области и местным органам власти, к банковским структурам, надеясь на их поддержку. Идея получила предварительное одобрение у властей региона».
Перечисленные выше изменения в структуре предприятия, продолжение курса на обновление машинного парка и освоение новых видов конкурентоспособной продукции обеспечат устойчивое развитие предприятия, дадут возможность сделать большой шаг вперед в социальной политике и в привлечении молодых специалистов.
Основа успехов, залог развития
Таковыми руководство холдинга и комбината «Полеко» считают трудовой коллектив предприятия. Первое, на что я обратил внимание, когда наша машина подъехала к административному корпусу и воротам комбината, был стенд с Доской почета «Гордость нашего комбината», на котором представлены фото лучших работников. Большим уважением и авторитетом пользуются на предприятии слесарь-ремонтник Александр Шехирев, бункеровщица Надежда Мургина, шлифовщик Геннадий Павлов, прессовщик Павел Пономарев, машинист рубительной машины Николай Момотов, машинист отливной машины Алексей Воробьев, размольщик Владимир Злобин, начальник производственно-диспетчерского отдела Людмила Костяева, начальник комплекса ДВП Екатерина Бестужева, начальники смен комплекса ДВП Надежда Некипелова, Галина Белозерцева, Галина Воробьева, Евгения Корякина и другие люди, отдавшие работе на комбинате многие и многие годы и активно участвующие в его жизни. «Благодаря таким золотым кадрам наше предприятие сегодня является успешным и развивающимся», - отметил генеральный директор комбината.
Руководители компании подчеркивают, что без проведения политики, направленной на обеспечение профессионального роста и социального благополучия людей, работающих на «Полеко», без создания сплоченного, социально защищенного, творческого и экономически мотивированного коллектива, без мер по повышению безопасности труда невозможно добиться статуса современного высокоэффективного и социально ответственного предприятия, невозможно получать высокие производственные результаты, успешно конкурировать на рынке и реализовывать планы по развитию и модернизации. И, надо отметить, что для создания благоприятных условий труда и достойной оплаты на комбинате делается немало. Мне показали и комнаты для приема пищи, оборудованные холодильниками и микроволновками, и удобные и чистые раздевалки с душевыми кабинами.
Несмотря на непростую ситуацию на рынке, руководство предприятия старается держать заработную плату специалистов на достойном уровне. Так, в прошлом году в среднем на 30% была увеличена зарплата работникам наиболее ответственных участков: сотрудникам единой ремонтной службы, машинистам крана, размольщикам, сортировщикам и некоторым специалистам комплекса ДВП. Средняя заработная плата сотрудников ООО «Полеко» в период с января по март 2014 года составила 21 200 руб., для сравнения: среднемесячная заработная плата по отрасли (обработка древесины и производство изделий из нее) в Кировской области за январь-март 2014 года составила 14 168 руб. Еще пример: грузчики на «Полеко» получают около 70 тыс. руб., а водители - около 50 тыс. руб.
На комбинате широко используют различные меры для дополнительного поощрения работников. Взять хотя бы уже упоминавшееся соревнование смен за достижение максимальной выработки. Процент мотивации напрямую зависел от достигнутого результата, максимальный процент премии составил 95% от должностного оклада, максимальная зарплата в рамках соревнования составила 33800 руб. для размольщика, 39 345 руб. для прессовщика, 44 800 руб. для крановщика, 39 960 руб. для навальщика-свальщика, 39 000 руб. для машиниста рубительной машины, 49 500 руб. для раскряжевщика. Помимо премий участники соревнований получили ценные подарки: фотоаппараты, DVD-плееры и ноутбуки.
По мнению руководства предприятия, несмотря на нестабильность российского рынка плит, в ближайшее время уровень заработной платы на предприятии будет только расти, поскольку активное развитие и модернизация производства невозможны без участия высококвалифицированных специалистов.
Словом, можно смело сказать, что у холдинга, в который входит ООО «Полеко», есть все основания для того, чтобы с уверенностью смотреть в будущее. И мы надеемся в ближайшее время рассказать о новых высотах, взятых дружным, творческим коллективом этой компании.
Александр РЕЧИЦКИЙ, фото автора