Холдинг RFP Group: «Развитие – ключевое слово в стратегии»
Основная стратегическая цель дальневосточного холдинга RFP Group - отказ от экспорта кругляка и переход к полной переработке заготавливаемого сырья. Компания развивается в соответствии с выбранным направлением и намерена достичь поставленной цели к 2020 году.
Проект «Создание Дальневосточного центра глубокой переработки древесины»
Площадь - 100 га. Общая сумма инвестиций - более 15 млрд руб. Число рабочих мест - до 1000.
Начало строительства - 2010 год. Окончание строительства - 2018-2020 годы.
Планы по обработке древесины:
в 2014 году - 330 тыс. м3, в 2015 году - более 700 тыс. м3, в 2017 году - более 1 млн м3
Холдинг RFP Group был создан в 2004 году на базе лесопромышленной компании «Дальлеспром» и Амурского речного пароходства. Дальше развитие компании пошло по пути вертикальной интеграции - объединения предприятий, относящихся к разным профилям, но составляющих при этом единый технологический цикл. Нынешняя структура RFP Group - это бизнес-единицы «Лесозаготовка», «Лесопереработка», «Транспорт и логистика» и «Торговый дом», работающие под руководством управляющей компании с штаб-квартирой в Хабаровске.
Базовое направление
RFP Group - крупнейший лесозаготовитель на Дальнем Востоке. Холдинг занимает второе место в России по площади находящегося в управлении лесного фонда, который составляет 20% всех переданных в аренду лесных массивов в регионе. Компания располагает 6,4 млн га леса, при этом эксплуатационный запас оценивается в 453,4 млн м3 древесины в год, а объем разрешенной ежегодной вырубки составляет 4,5 млн м3.
С момента основания холдинг наращивал объемы лесозаготовки: за шесть последних лет они увеличились более чем в два раза, с 1 млн м3 в 2008 году до 2,3 млн3 в 2013 году. В 2012 году RFP Group по объемам заготовленной древесины заняла второе место в России. Компания располагает возможностями дальнейшего увеличения лесозаготовок и к 2018 году может довести их до 4,6 млн м3. В прошлом году холдинг получил сертификат FSC на весь арендуемый лесосечный фонд.
RFP Group создавалась как компания, ориентированная в первую очередь на заготовку древесины с последующей отправкой ее на экспорт. Сырье поставлялось в виде кругляка, основными покупателями стали Китай, Япония, Южная Корея. (Сейчас КНР выступает в роли генерального партнера, закупающего 90% лесоматериалов холдинга, на долю RFP Group приходится более 10% всей экспортируемой в Китай российской необработанной древесины.)
Закономерным образом за бизнес-единицей «Лесозаготовка» в RFP Group закрепилась ведущая роль. Сейчас по сравнению с другими подразделениями холдинга в нее входит наибольшее число предприятий - свыше 20 (крупнейшие из них - ОАО «Дальлеспром» и ОАО «Флора»). Эта бизнес-единица приносит наибольшую выручку: $180 млн, или 53% в структуре доходов холдинга, по данным за первый квартал 2014 года, - и находится на первом месте по численности штата: на ее предприятиях трудится более 3 тыс. человек.
Лесозаготовители RFP Group работают в Хабаровском и Приморском краях и Амурской области, заготавливая древесину преимущественно механизированным способом, с применением комплексов «харвестер + форвардер». На лесозаготовках используется техника марок Ponsse, John Deere, Komatsu, лесовозы Mercedec-Benz. Заготавливается древесина хвойных пород, за рубеж идут ель и лиственница (доля каждой в структуре экспорта - 50%).
По новой стратегии
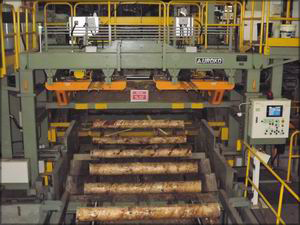
Сейчас 70% заготавливаемой предприятиями RFP Group древесины идет на экспорт в необработанном виде. Однако, по планам руководства холдинга, к 2017 году этот показатель будет снижен до 30%, а к 2020 году холдинг будет перерабатывать все древесное сырье, которое заготовит.
К идее постепенной смены вектора развития RFP Group пришла в 2008 году. «C 1990-х годов лесопромышленные предприятия Дальнего Востока работали в основном на экспорт кругляка, - рассказывает вице-президент по развитию, инвестициям и контролю RFP Group Владимир Григорьев. - Но со временем государство пришло к пониманию того, что от сырьевых потоков необходимо переходить к экспорту продуктов с более высокой добавленной стоимостью, и стало проводить политику, направленную на стимулирование компаний к укрупнению и переходу к проектам, предполагающим строительство мощностей по лесопереработке. Это стратегическое решение затронуло и RFP Group. Мы изучили, как перерабатывают круглые лесоматериалы в странах - импортерах нашей продукции. Выяснилось, что из дальневосточной лиственницы японцы делают фанеру, которую затем используют в типовом домостроении. Дело в том, что лиственница - уникальный по надежности строительный материал, идеально подходящий для строительства в районах высокой сейсмической активности. Мы проанализировали возможность поставки на японский рынок шпона как сырья для производителей фанеры и выяснили, что проект завода по лущению шпона вполне жизнеспособный, что нам гарантирован стабильный спрос и крупные, серьезные партнеры со стороны Японии».
Убедившись в перспективности производства шпона на экспорт, руководство холдинга приняло решение о развитии лесоперерабатывающего направления и запуске нового стратегического проекта - Дальневосточного центра глубокой переработки древесины. Планируется, что центр станет крупнейшим в регионе, состоящим как минимум из трех производств: заводов лущеного шпона и сухих пиломатериалов и предприятия - утилизатора древесных отходов (рассматриваемые варианты его продукции - плиты, пеллеты, электроэнергия). Проект получил одобрение на федеральном уровне: в сентябре 2009 года по приказу Минпромторга он был включен в перечень приоритетных инвестпроектов, а в мае 2013-го - утвержден премьер-министром РФ Дмитрием Медведевым.
«Государство, стимулируя лесозаготовителей переходить к лесопереработке, содействовало тому, чтобы они получали финансовую поддержку, - говорит Владимир Григорьев. - Внешэкономбанк предоставил нам льготный кредит на $97 млн. Эти деньги были вложены в строительство первого завода в Амурске - по производству лущеного шпона. Общие инвестиции в него составили $156 млн».
Кроме того, Дальневосточный центр глубокой переработки древесины стал первым проектом в регионе, в который вложил средства Российский фонд прямых инвестиций (РФПИ).
Первый набирает обороты
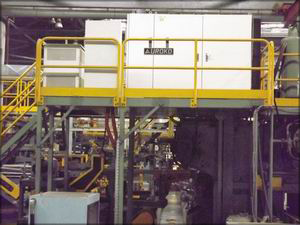
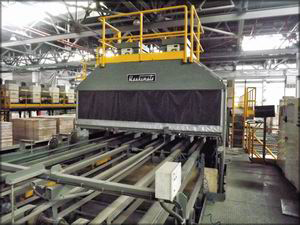
Завод по производству лущеного шпона начали строить в 2010 году, в конце 2012 года запустили в эксплуатацию. Управляет им входящее в RFP Group ООО «Амурская ЛК».
«Строительство производства велось по классической схеме, - поясняет Владимир Григорьев. - Сначала отбор основного технологического оборудования, его инжиниринг. Победителем тендера стала японская корпорация Hashimoto Denki, которая давно специализируется на выпуске оборудования для производителей фанеры. Мы выбрали эту компанию, потому что понимали: продукция, изготовленная на ее оборудовании, будет точно соответствовать высоким требованиям японского рынка и наше предприятие гарантированно сможет работать с такой капризной, отличающейся высоким содержанием смолы породой, как лиственница. Оборудование было поставлено в кратчайшие сроки, несмотря на то что в Японии в то время случилось цунами. Монтаж выполнила петербургская компания "Электроавтоматика"».
Завод находится в 4 км от города Амурска и занимает участок около 5 га: на 2 га построен цех, 2 га отведены под складские помещения, остальное - под инженерную инфраструктуру и котельную.
Предприятие работает в двухсменном круглосуточном режиме, но проектной мощности - 300 тыс. м3 шпона в год - пока не достигло. «Сейчас набираем заказы, выйдем на заявленный объем в этом году», - уверен Владимир Григорьев. Планируется, что выручка ООО «Амурская ЛК» за 2014 год составит около $70 млн (это более 20% в структуре доходов холдинга).
Штат завода уже укомплектован, всего на производстве лущеного шпона занято около 300 человек. Основной персонал привлекали из Амурска и Комсомольска-на-Амуре (находится в 50 км от Амурска), а высококвалифицированные работники приехали из Хабаровска, им компенсируют стоимость аренды жилья. По словам руководства холдинга, в регионе большая текучка кадров, поэтому приходится искать способы закрепить людей на предприятии. Например, эффективным оказался такой мотивационный механизм, как предоставление возможности бесплатно повысить квалификацию - и, соответственно, разряд и зарплату - или обучиться дополнительной профессии (например, водителя погрузчика).
Производство
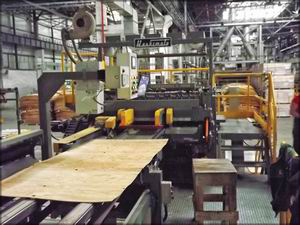
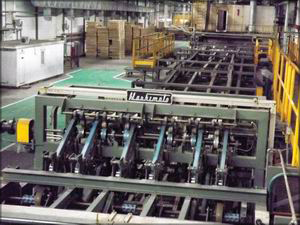
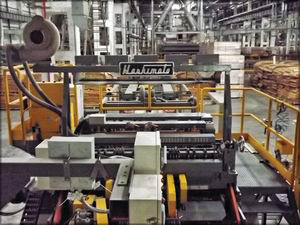
«Основной принцип, которым мы руководствовались, приобретая оборудование для первого завода в Амурске, - возможность создания единой технологической линии, чтобы минимизировать технологические риски по стыковке оборудования и по балансировке мощностей каждой машины в технологической цепи», - рассказывает Владимир Григорьев.
Бревна окаривают на двух станках Eno (Япония), пропаривают в камерах гидротермической обработки (всего работают восемь камер, процесс в среднем длится 10 ч). Затем заготовки поступают на раскряжевку и лущение, которые осуществляются на трех станках Uroko-Hashimoto (Япония). Лущильные станки позволяют изготавливать шпон толщиной от 1,5 мм и обрабатывать бревна до сердцевины диаметром всего 4 см - таким образом достигается высокий выход продукции при небольшом объеме отходов.
«Процесс производства шпона можно сравнить с заточкой карандаша точилкой - в нашем случае бревно тоже поворачивается вокруг своей оси и из-под ножа выходит непрерывное полотно древесины, - поясняет Владимир Григорьев. - Дальше это полотно нарезается на отрезки приблизительно метр на два, укладывается стопой высотой около метра и отправляется на сушку».
Сушильных камер в цеху тоже три, все - марки Uroko. На сушильных линиях применены уникальные теплоизоляционные материалы, способствующие оптимизации энергозатрат. В среднем процесс сушки продолжается 15 мин. - за это время влажность шпона снижается до 8-10%.
Для формирования полотна из кускового и неформатного шпона в технологическую линию включены четыре ребросклеивающих станка Uroko, производительность каждого 30-40 м3 шпона в сутки. Упаковка готовой продукции осуществляется на упаковочной машине марки Nagai.
Контроль качества продукции ведется на всех этапах производства: технологическая линия оснащена влагомерами и сканерами, позволяющими оценивать и сортировать шпон в соответствии с японскими стандартами JAS.
По словам руководства предприятия, проект был изначально ориентирован на максимально полное использование входящего сырья и минимизацию отходов. Поэтому, в частности, котельная установка, предназначенная для производства технологического пара и горячей воды, работает исключительно на отходах производства шпона. Ее разработчик и поставщик - австрийская компания Polytechnik. Сейчас в установке два котла мощностью по 18 МВт (или 27,5 т пара в час), планируется строительство еще одного такой же мощности.
Древесные отходы, не востребованные в производственном цикле завода, реализуются муниципальным котельным. Предприятие располагает парком транспортной спецтехники: на разгрузке круглых лесоматериалов работают погрузчики Doosan Mega 400 (Южная Корея), для выгрузки кругляка из вагонов используются два манипулятора на базе экскаваторов этой же фирмы. В цеху в транспортировке упакованного шпона задействованы вилочные японские погрузчики Komatsu DT 35.
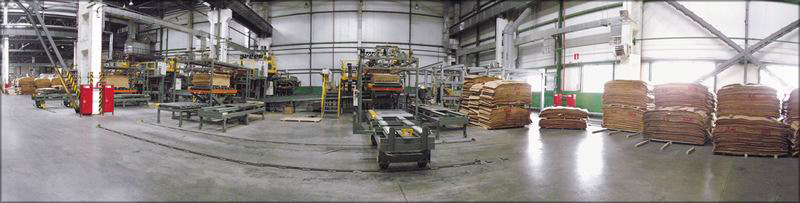
Продукция
На заводе в Амурске производят лиственничный шпон двух типоразмеров: 3 х 6 футов (или 0,9 х 1,8 м) - японский стандарт, и 4 х 8 футов (или 1,2 х 2,4 м) - стандарт, принятый в Европе, Китае, США. Вся продукция имеет сертификат соответствия цепи поставок FSC.
«Поскольку проект изначально был рассчитан в первую очередь на японский рынок, сейчас мы выпускаем в основном шпон японского стандарта, - говорит Владимир Григорьев. - Но китайский рынок нам тоже интересен как достаточно стабильный и емкий. Кстати, китайцы заказывают нам шпон не своего, а японского стандарта, потому что сами делают из него фанеру и продают ее в Японию. Корейский потребитель тоже в основном ориентирован на размер 4 х 8.
Весь шпон, произведенный на амурском заводе, идет на экспорт в страны АТР: 70% - в Японию, остальное - в Китай и Южную Корею».
Российский рынок дальневосточному производителю пока недоступен. В своем регионе потребителей с постоянным спросом найти сложно, а поставки, например, в Центральную Россию трудноосуществимы из-за больших расстояний и высоких затрат на логистику, а также из-за плотной конкурентной среды: придется делить рынок с такими серьезными игроками, как «Свеза», основные мощности которой находятся в центральной и северо-западной частях РФ.
Следующий на подходе
«Развитие - ключевое слово в стратегии нашего холдинга», - подчеркивает Владимир Григорьев. Запустив завод по производству лущеного шпона, RFP Group строит следующее предприятие Дальневосточного центра глубокой переработки древесины: завод по производству пиломатериалов.
Общая сумма инвестиций в строительство завода - $102 млн, из них 87 млн - средства Внешэкономбанка, который по-прежнему остается партнером холдинга.
«Сейчас мы работаем над устройством склада сырья, площадок для складирования продукции и ее отгрузке на транспортные единицы, готовим цех для размещения в нем технологического оборудования, занимаемся созданием инженерных сетей и транспортной инфраструктуры, в частности укладываем железнодорожное полотно и строим автомобильную дорогу, - рассказывает Владимир Григорьев. - Идет поставка оборудования на склад - мы уже получили около половины. Думаю, к середине лета придет все, осенью начнем монтаж».
Пуск завода запланирован на 2015 год. В качестве поставщиков оборудования для этого предприятия RFP Group выбрала двух ведущих европейских производителей: линию распиловки поставляет компания Linck (Германия), линию сортировки - Springer (Австрия).
Проектная мощность предприятия - около 250 тыс. м3 пиломатериалов в год, но при необходимости оборудование можно быстро модернизировать для производства большего объема, до 450 тыс. м3. «Поэтому, - поясняет Владимир Григорьев, - если потребность в экспорте нашей продукции вырастет - а рыночные предпосылки для этого есть, - мы будем готовы увеличивать объемы отгрузок».
Основным сырьем для производства пиломатериалов будут ель и пихта. Таким образом, с запуском второго завода структура потребления сырья Дальневосточным центром глубокой переработки древесины придет в соответствие структуре лесозаготовок холдинга, в которой 50% отводится лиственнице и столько же ели и пихте.
В среднесрочной перспективе
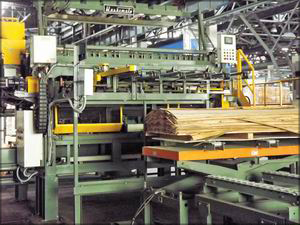
В проект Дальневосточного центра глубокой переработки древесины входит создание плитного производства. Его планируется развернуть на базе Амурского ДОКа. Это предприятие вошло в RFP Group в 2008 году, выпускало ДСП, в том числе ламинированную.
«Сейчас завод на реконструкции, - рассказывает Владимир Григорьев, - но производство полностью не остановлено, функционируют участок ламинирования и линия по выпуску давальческого сырья в виде ДСП. Мы выпускаем небольшие партии продукции, чтобы сохранить клиентскую базу производителей мебели».
Реконструкция предполагает полное обновление прессового оборудования (решено приобрести его у немецкой фирмы Dieffenbaсher) и участка подготовки сырья. Точные сроки завершения проекта пока не определены, сейчас прорабатываются вопросы, связанные с его экономической целесообразностью.
Проектная мощность завода после реконструкции составит 50 тыс. м3 плит ДСП и MDF в год. Выходить на международный рынок с этой продукций руководство холдинга не намерено - слишком высока конкуренция со стороны китайских производителей, поэтому основным направлением сбыта плит станет российское. «Близость к мебельщикам Дальнего Востока - одно из ключевых конкурентных преимуществ этого предприятия», - подчеркивает Владимир Григорьев.
По словам руководства холдинга, проект интересен прежде всего тем, что полностью вписывается в концепцию создания безотходного комплекса предприятий в составе RFP Group. Для производства будут использоваться отходы лесопильного и шпонового производств.
«Мы ориентированы на максимальное использование заготавливаемого сырья, - поясняет Владимир Григорьев, - поэтому обдумываем проекты по переработке низкосортной древесины. Это может быть не только плитное производство, но и производство пеллет, генерация электрической и тепловой энергии - как на шпоновом заводе, продажа щепы».
Кроме того, по его словам, сейчас холдинг нацелен на дальнейшее углубление переработки древесины и освоение российского рынка: «Поработав на японском и китайском рынках, мы пришли к пониманию необходимости производить продукцию более глубокой обработки, чем шпон или пиломатериалы. Например, фанеру или LVL-балки из лиственницы, которые широко используются в строительстве, в том числе в деревянном домостроении - перспективном направлении не только в странах Азии, но и в России. Мы убеждены, что такая продукция будет востребована не только за рубежом, но и в нашей стране».
Сбыт и перевозки
Помимо предприятий по заготовке и обработке лесоматериалов, RFP Group как вертикально интегрированная структура имеет в своем составе подразделения, занимающиеся продажей продукции (бизнес-единица «Торговый дом») и ее транспортировкой (бизнес-единица «Транспорт и логистика»).
ООО «Торговый дом РФП» организует экспорт продукции обеих производственных бизнес-единиц холдинга - «Лесозаготовки» и «Лесопереработки». В 2012 году компания заняла первое место в конкурсе «Лучший экспортер Хабаровского края», проводившимся краевым министерством экономического развития, в категории предприятий с объемом экспорта свыше $10 млн в год. По данным за 2013 год, «Торговый дом» экспортировал 1,6 млн м3 круглого леса, 200 тыс. м3 шпона и пиломатериалов.
В числе основных стратегических задач «Торгового дома» заявлено расширение рынков сбыта и продвижение продукции Дальневосточного центра глубокой переработки древесины. Поэтому компания постоянно ищет новых партнеров на уже знакомых рынках - японском, китайском, южнокорейском, а также ведет переговоры с компаниями США, Малайзии, Новой Зеландии.
Бизнес-единица «Транспорт и логистика» обеспечивает круглогодичную перевозку продукции RFP Group - как на экспорт, так и по внутренним маршрутам, доставляя сырье на предприятия холдинга. Базовая компания подразделения - ГК «Амурское пароходство», занимающаяся речными и морскими грузовыми перевозками по Амуру, прибрежным водам российского Дальнего Востока и в ближайшие к России страны АТР - Японию, Корею, Китай.
В структуре доходов RFP Group бизнес-единице «Транспорт и логистика» принадлежит 23,5% ($80 млн за 2013 год). При этом, в отличие от «Торгового дома», она работает не только с продукцией холдинга. «50% ее бизнеса - это услуги сторонним компаниям, - поясняет Владимир Григорьев. - У этого подразделения и "Торгового дома" коммерческие отношения. И если "Торговый дом" находит перевозчика с более низкими ценами, чем те, что предлагают транспортные компании, входящие в холдинг, то для перевозки нашей продукции привлекают этих сторонних перевозчиков». Пока 90% перевозок бизнес-единицы «Транспорт и логистика» - водные, тогда как структура перевозок RFP Group следующая: около 50% - автомобильные (главным образом вывоз сырья из леса), 25% - железнодорожные (доставка кругляка до границы РФ или на предприятия холдинга) и 25% - водные (перевозка продукции в страны-импортеры). Холдинг, в свою очередь, пользуется не только услугами бизнес-единицы «Транспорт и логистика», привлекая другие транспортные компании на условиях подряда.
В планах транспортно-логистического подразделения RFP Group освоение новых видов грузов и перевозок. Руководство холдинга рассчитывает в ближайшее время получить от ОАО «РЖД» разрешение на обработку контейнеров, что позволит увеличить плечо перевозки шпона и оптимизировать загрузку своих судов: контейнеры со шпоном будут перевозить по железной дороге и грузить на крышки трюмов судов. Для этого уже приобретен манипулятор-погрузчик фирмы Sunny (Китай). Кроме того, бизнес-единица «Транспорт и логистика» намерена в скором будущем выйти на рынок международных мультимодальных перевозок (door-to-door), а также освоить другой профиль - добычу и продажу нерудных строительных материалов.
Подготовила Инна Родионова
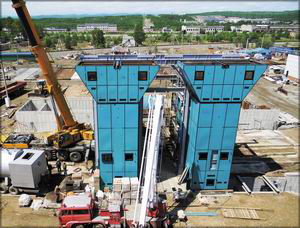
Мария Королева, исполнительный директор компании Polytechnik по работе с РФ и странами Восточной Европы:
В декабре 2010 г. австрийская компания Polytechnik Luft- und Feuerungstechnik GmbH заключила контракт с ООО «Амурская лесопромышленная компания» на производство и поставку оборудования для утилизации древесных отходов, образующихся в технологическом цикле предприятия, и выработки технологического пара. Основу комплекса составляют две топки с гидромеханической колосниковой решеткой и теплообменники насыщенного пара общей мощностью 36 МВт. Оборудование было введено в эксплуатацию в начале 2012 г.
В 2012 г. компании подписали ряд контрактов на поставку еще одной установки мощностью 18 МВт, а также турбины для выработки 3100 кВт электроэнергии. Сейчас идет отгрузка этого оборудования.
В конечном счете поставленное оборудование в комплексе будет представлять собой мини-ТЭЦ общей мощностью 54 МВт с возможностью выработки 3,1 МВт электроэнергии и около 50 МВт насыщенного пара для технологических целей и отопления производственных помещений.