Производство шпона и фанеры. Часть 6
Прессование и послепрессовая обработка фанеры
Производство шпона и фанеры. Часть 1. Подготовка сырья к лущению
Производство шпона и фанеры. Часть 2. Лущение шпона
Производство шпона и фанеры. Часть 3. Сушка шпона
Производство шпона и фанеры. Часть 4. Сортирование и обработка сухого шпона
Производство шпона и фанеры. Часть 5. Технологии склеивания фанеры
Все существующие сегодня прессы в деревообработке можно классифицировать по следующим признакам:
- температуре: холодные и горячие (с нагревом или без нагрева);
- этажности: одно-, двух- и многоэтажные;
- характеру работы: периодического или непрерывного действия;
- виду привода: гидравлические, пневматические (в том числе вакуумные), механические, электромагнитные;
- виду средств, передающих давление: с жесткими плитами, гусеницами, роликами, мембранами, эластичными диафрагмами, лентами;
- виду теплоносителя: с обогревом паром, горячей водой, электричеством (в том числе ТВЧ), минеральными жидкостями;
- конструкции станины: колонные, рамные и коробчатые.
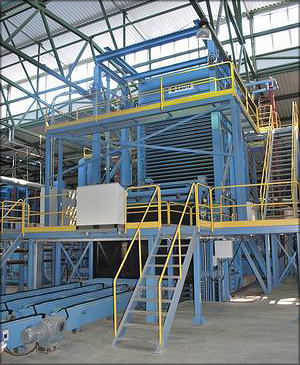
Универсальный 30-пролетный горячий пресс Raute
Select для большеформатной фанеры 4x8 и 5х10 футов
Для обеспечения лучшей работы горячего пресса выполняют холодную подпрессовку пакетов шпона. После нанесения клея и сборки пакет шпона поступает в холодный одноэтажный пресс с верхним давлением.
В течение короткого периода и под невысоким давлением (примерно 1 МПа) происходит пропитка шпона клеем и нарастание вязкости клея. В результате устраняется волнистость шпона, пакеты приобретают правильную форму, что облегчает и ускоряет их загрузку в горячий пресс.
В качестве головного оборудования фанерных предприятий почти повсеместно используются горячие гидравлические многоэтажные прессы. На многих фанерных заводах России эксплуатируется отечественный пресс П-714Б. Это 15-этажный пресс с нижним давлением, жесткими плитами и паровым обогревом.
В основании пресса литая станина со встроенными цилиндрами из высокоуглеродистой стали. Внутри цилиндров находятся поршни с манжетами из маслостойкой резины (срок службы - 3-5 месяцев). Профиль манжет таков, что при повышении давления увеличивается плотность их прилегания к поверхности цилиндров. У пресса П-714Б один главный цилиндр диаметром 600 мм - для создания рабочего давления (до 2,2 МПа) и два вспомогательных цилиндра диаметром 160 мм - для быстрого смыкания и размыкания плит пресса.
Гидросистема пресса включает в себя бак с рабочей жидкостью (маслом ИГП-30, ТП-22) объемом 630 л, насосы высокого и низкого давления, распределители и трубопроводы.
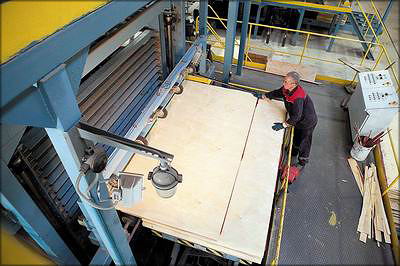
Загрузочное устройство пакетов Raute
Нагревательные плиты обеспечивают плотный контакт склеиваемых слоев шпона и упрессовку. Габариты плит пресса П-714Б - 1650 х 1750 х 42 мм, поверхность плит шлифованная. В плитах, которые свободно лежат на плитодержателях, есть система каналов диаметром 20 мм для циркуляции теплоносителя (пара). Система нагрева плит включает паропроводы, коллектор для распределения пара по плитам и гибкие шланги, позволяющие не нарушать герметичность системы при вертикальном перемещении плит. Вместо гибких шлангов могут использоваться шарнирные или телескопические трубки.
Наиболее удобным теплоносителем является насыщенный пар; температура плит зависит от давления пара. При использовании перегретой воды уменьшаются потери тепла из-за парообразования, сокращается время прогрева, увеличивается равномерность температурного поля. В целом экономия тепла достигает 25%. Существуют также высокотемпературные теплоносители в виде минеральных жидкостей с температурой кипения до 300°С при нормальном давлении, например, ароматизированный минеральный теплоноситель АМТ-300. Его применение позволяет отказаться от системы паропроводов, использовать электронагрев жидкости и ее циркуляцию без потерь, под минимальным избыточным давлением.
Система управления прессом предусматривает возможность его работы в автоматическом или полуавтоматическом режиме. Большинство действующих прессов П-714Б были модернизированы: старая система управления в них заменена современной. С пульта управления прессом можно задать все необходимые параметры прессования: температуру плит, время срабатывания насосов подъема и смыкания плит, настройки рабочего давления и времени прессования и т. п.
Пресс П-714Б относится к прессам без этажерок, его загрузка осуществляется с подъемного стола вручную.
Среди других прессов для производства фанерной продукции следует отметить 20-этажные прессы ОАО «Днепропресс» (г. Днепропетровск, Украина) с механизированной загрузкой пакетов и выгрузкой фанеры.
У пресса Д-4042 Ф1 имеются загрузочная и разгрузочная этажерки, которые могут перемещаться вертикально. Собранные пакеты шпона загружаются поэтажно в загрузочную этажерку по мере ее опускания. Полностью загруженная этажерка находится в крайнем нижнем положении, что позволяет специальному устройству с толкателями выталкивать все листы фанеры из открывшегося пресса в разгрузочную этажерку. После этого загрузочная этажерка поднимается и те же толкатели загружают пакеты шпона в горячий пресс, который быстро смыкается, и начинается новый цикл прессования.
Размер горячих плит пресса Д-4042 Ф1 - 3300 х 1700 мм, пресс предназначен для изготовления специальных видов фанерной продукции (декоративной, бакелизированной), получаемых с использованием поддонов. В прессе возможно охлаждение плит в каждом цикле запрессовки, стабилизация толщины продукции за счет изменения давления прессования. Возможна поэтажная загрузка этажерок с конвейера.
Днепропетровская фирма «Волев» выпускает комплексы для производства фанеры формата 1525 х 525 и 2440 х 1220 мм на базе 15-ти и 20-этажных прессов. Производительность прессов - 20-5 тыс. м2 фанеры в год. В состав комплекса входят:
- два участка сборки пакетов (столы подстопные подъемные, транспортеры дисковые пульсирующие, столы сборки пакетов, приводные рольганги, рольганг продольно-поперечной подачи к подпрессовщику);
- подпрессовщик с автоматизированной загрузкой и выгрузкой стопы пакетов;
- горячий пресс с автоматизированной загрузкой и выгрузкой (рольганг подъемный, механизм загрузки этажерки, этажерка).
Среди зарубежных производителей прессов для выпуска фанеры следует отметить финскую фирму Raute, итальянскую Italpresse и японскую Jamamoto.
Компания Raute предлагает серию прессового оборудования (Pro, Select, Smart) с системами загрузки/выгрузки. Максимальное число этажей пресса - 36. Все прессы оснащены автоматическими системами управления, в том числе с контролем толщины готовой продукции. Давление прессования - до 2 МПа, производительность - до 60 тыс. м3 фанеры в год.
Фирма Italpresse выпускает широкий спектр прессового оборудования с размерами плит пресса от 1000 х 1000 до 3000 х 10000 мм и числом этажей от одного до 50, в том числе прессы с механизмами одновременного смыкания плит (симультантными механизмами).
Многоэтажный пресс выпускает также японская фирма Jamamoto. У этого пресса 45 этажей, усилие прессования - 500 т, размеры горячих плит - 2700 х 3500 х 70 мм, обогрев выполняется паром. Главные достоинства пресса - патентованные системы автоматического управления и новая система загрузки/выгрузки пакетов. Конструкция обеспечивает быструю и надежную загрузку пакетов шпона в горячий пресс и быстрое смыкание плит пресса, что позволяет сократить до минимума время закрытой выдержки (время от сборки пакета до приложения полного давления) и избежать преждевременного отверждения клея.
Послепрессовая обработка фанеры
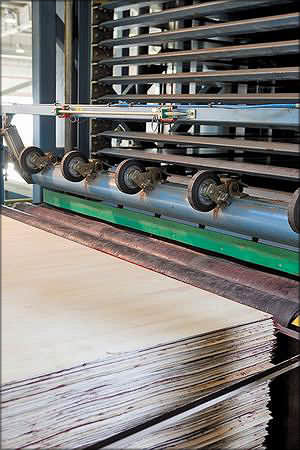
Устройство выгрузки пакетов Raute
Послепрессовая обработка фанеры включает в себя операции по охлаждению, форматной обрезке, сортированию и шлифованию фанерной продукции.
Охлаждение фанеры выполняют для снижения температуры и влажности листов, выгруженных из горячего пресса. Для ускорения процесса используют веерные или конвейерные охладители. При длине конвейера 6,5 м и скорости подачи 1 м/мин. время охлаждения листов фанеры составляет 6,5 мин.
Обрезка фанеры необходима для получения листов заданного формата. Допускаемое отклонение габаритов от заданных составляет 4...5 мм. Обрезку выполняют на круглопильных станках. Наиболее широкое применение нашли четырехпильные агрегаты, составленные из двух двухпильных станков, расположенных перпендикулярно. Особенность обрезки фанеры заключается в том, что у листов, выгруженных из пресса, нет ни одной строго прямолинейной базовой кромки. По-этому базирование листа относительно пил на первом станке лучше выполнять с помощью гусеничной подачи. При обрезке второй пары кромок можно использовать станок с цепной подачей, в котором базирование выполняется с помощью упоров цепи.
Помимо поштучной, широко распространена обрезка фанеры в пачках. Ярославский завод «Пролетарская свобода» выпускает линию обрезки фанеры ЛОФ; она состоит из подъемного стола, на котором формируется пачка необрезной фанеры высотой до 850 мм, и двух двухпильных станков с кареткой, на которую загружается пачка фанеры толщиной 20-40 мм. Скорость подачи - до 22 м/мин.
Ввиду высокой твердости клеевых швов при обрезке следует использовать пилы с пластинками твердого сплава. Для измельчения срезок (реек, образующихся после опиливания фанеры) на одном валу с пилой иногда устанавливают фрезу. Известен вполне удачный опыт использования срезок в качестве среднего слоя комбинированной фанеры.
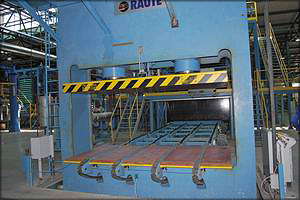
Холодная подпрессовка Raute
В последние годы многие предприятия создали полуавтоматические поточные линии по обработке клееной фанеры. В их состав обычно включают веерный охладитель фанеры, подъемный стол-накопитель листов, два двухпильных обрезных станка, устанавливаемых под углом 90° друг к другу, и транспортер.
Среди зарубежного оборудования следует отметить угловую линию обрезки и раскроя фанеры и плит фирмы Schelling (Австрия). Линия оснащена устройством автоматической загрузки плит, пильными агрегатами с подрезными пилами для устранения сколов на нижней стороне листов, встроенной линией сортирования фанеры.
Компания Raute выпускает линии форматной обрезки фанеры трех моделей: Pro, Select и Smart. Они изготовлены в угловом исполнении с двумя двухпильными станками и отличаются друг от друга уровнем автоматизации на операциях подачи материала и настройки.
Для операции переобреза фанеры, цель которой опиливание листа фанеры на меньший стандартный размер из-за наличия недопустимого дефекта, используют однопильный станок типа ЦФ-5 с кареткой. Часто обрезанные полосы фанеры могут найти спрос как попутная продукция.
Сортирование фанеры выполняют по породам шпона наружных слоев, форматам, толщине, маркам и сортам. Процесс сортирования предусматривает три стадии:
- предварительное сортирование, в ходе которого определяют фанеру экспортную, общего назначения и направляемую в переобрез;
- сортирование экспортной фанеры;
- сортирование фанеры общего назначения.
Фанера общего назначения для внутреннего рынка подразделяется по внешнему виду на сорта. Каждый лист осматривается с двух сторон и простукивается деревянным молоточком на предмет обнаружения пустот (непроклея). В современных линиях сортирования фанеры для этой цели используются ультразвуковые приборы. На участке сортирования выполняют также мелкий ремонт листов: заделку выпавших сучков, разошедшихся трещин, запрессовку слабых углов, удаление пузырей, обзола и т. п. Затем на лист ставят штамп, содержащий информацию о сорте фанеры и номере сортировщика.
В линии сортирования Raute интегрированы современные устройства автоматического видеоконтроля, которые идентифицируют все дефекты, влияющие на сорт фанеры, такие как: трещины, выпадающие сучки, неотшлифованные поверхности, изменения в цвете. Общее состояние поверхности фанерного листа оценивается с помощью лазеров.
Для увеличения доли выпуска фанеры высших сортов необходимо увеличивать объемы починки форматного шпона, ребросклеивания кускового шпона, наращивать выпуск неравнослойной фанеры с наружными слоями из тонкого высококачественного шпона, а также выполнять качественную починку фанеры.
Починка фанеры выполняется с целью ликвидации дефектов и повышения сортности листа фанеры. К числу устранимых дефектов относятся трещины, слабые углы, пузыри, отверстия от выпавших сучков. Починку выполняют на отдельном рабочем месте, оборудованном инструментом для фрезерования канавок и постановки заплаток, нанесения клея и запрессовки слабых углов в винтовом прессе и т. п. Широко используют замазки на основе смеси карбамидной смолы, казеина и древесной муки. С экономической точки зрения починка фанеры вполне себя оправдывает.
Компания Raute производит как автоматические, так и ручные линии ремонта фанерных плит. Имеются полностью автоматизированные системы, в состав которых входит видео- и робототехника, они используются для ремонта лицевых сторон листов фанеры. В основе технологии использование интеллектуальной системы сортировки посредством видеокамеры, которая идентифицирует подлежащие починке дефекты и выдает в ПК системы информацию для позиционирования фрезерной головки. После устранения дефекта вырез автоматически заполняется быстротвердеющей пастой и выравнивается шлифованием. Система может быть запрограммирована на ремонт любых видов дефектов, возникающих после прессования плит, ее возможности могут быть расширены за счет включения в ее состав дополнительных ремонтных блоков.
Шлифование фанеры выполняется выборочно, по требованию заказчика. Барабанные шлифовальные станки сегодня почти не используются, так как они требуют частой смены шлифовальной шкурки и не обеспечивают нужного качества обработки. Наиболее эффективна обработка на широколенточных двухсторонних станках, характеризующихся высокой производительностью и точностью обработки.
Шлифование совмещается с калиброванием фанеры, то есть с получением точного размера по толщине (обычно с точностью не менее ±0,2 мм). Для этого на станке устанавливается не менее четырех шлифовальных головок - по две на каждую сторону листа фанеры. Сначала ведется обработка грубой шкуркой для снятия припуска и калибрования фанеры, а затем второй агрегат выполняет выглаживание поверхности материала.
Оптимальная скорость резания при шлифовании составляет 25-30 м/с. Зернистость шкурок для грубого шлифования - 50-40, для чистового - 32-25. Скорость подачи составляет 10-17 м/мин. для наружных слоев из форматного шпона и 8-12 м/мин. - для слоев из ребросклеенного шпона. Усилие прижима шкурки к материалу составляет 7-12 Н/см, глубина сошлифовывания - 0,1-0,2 мм. Удельная длина шлифования, то есть число метров шлифованной поверхности на 1 м шкурки для обычной фанеры составляет 1000-1200 м/м, а для сосновой - всего 120-180 м/м, из-за смолистости древесины.
Упаковка фанеры может осуществляться на специальных механизированных или автоматических линиях. Пачку перевязывают металлической лентой, проволокой или веревкой. Вес пачки при механизированной упаковке может доходить до 1 т. Производительность автоматической линии (например, фирмы Raute) - до 40 м3/ч. На пачке указывают наименование предприятия, размеры листа фанеры, марку, сорт, породу древесины, из которой изготовлен шпон, вид обработки, число листов в пачке и номер стандарта, по которому изготовлена упакованная продукция.
Компания Raute осуществляет поставки линий упаковки плит для автоматической либо ручной обвязки как стальной, так и пластиковой лентой. Имеется у этой фирмы также упаковочная система бережного обертывания всех краев и углов пакета, обеспечивающая надежную защиту от холода, влаги и перегрева. В качестве упаковочного материала используется полиэтиленовая пленка, пригодная для переработки. Герметично упакованная пачка фанеры не требует дополнительной обвязки и обертывания углов.
Для производства большеформатной фанеры используют технологию склеивания листов фанеры. Тонкую фанеру соединяют «на ус» (длина стыка равна 6-8-кратной толщине листа фанеры). Ус зарезают на специальном станке фрезой с частотой вращения 3 тыс. об. мин-1. Склеивание выполняют в узкоплитном прессе УСПГ фенольным клеем при температуре 200°С в течение 15-20 с. Для склеивания толстой фанеры (Sф > 12 мм) можно применять соединение на зубчатый шип. Шипы длиной 8-15 мм зарезают по кромке короткой стороны листа фанеры вертикально или горизонтально. Прочность зубчатого соединения довольно высока, а потери материала ниже, чем при усовании. Компания Raute выпускает линию сращивания и облицовки фанерных плит, в составе которой имеется двухсторонний усовочный станок и горячий пресс. Перед прессованием стык фиксируется нагелями. Выходящая из пресса бесконечная лента фанеры разрезается полуавтоматом на листы длиной 6 или 12 м. Затем на линии выполняется облицовка фанеры в одноэтажном прессе бумагой, пропитанной фенольной смолой. Продукция может использоваться в строительстве, например, для опалубки.
Владимир ВОЛЫНСКИЙ