В ожидании курганских OSB
Весной-летом 2015 года в Курганской области ожидается ввод в эксплуатацию завода по производству плит ОСП (OSB) производительностью 60 тыс. м3 в год. Этот проект заинтересовал редакцию ЛПИ по целому ряду причин. Ехать на производственную площадку, пока там идет проектный монтаж линии (установлен и тестируется 24-пролетный пресс, подготовлены участок обработки OSB-щепы, транспортеры и цех изготовления клея), нам показалось преждевременным, а вот пообщаться с представителем компании, осуществляющей техническое сопровождение проекта, поставку и наладку оборудования, сейчас, пожалуй, в самый раз.
С этими мыслями ваш покорный слуга отправился в Москву, на встречу с директором по маркетингу и стратегии ООО «ТехЛесПром» (торговый бренд LESPT) Сергеем Крупенским.
От проекта - к заводу OSB
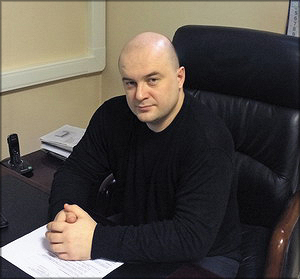
Сергей Крупенский
- Сергей Юрьевич, по понятным причинам некоторые сведения о заводе, который еще только строится, не могут быть обнародованы. И все же давайте попробуем описать проект поподробней. Начать предлагаю с истории.
- В начале 2013 года к нам обратился глава фермерского хозяйства из Курганской области Анатолий Невзоров (почти год назад он установил у себя один из крупнейших зерновых элеваторов в РФ стоимостью около полумиллиарда рублей. Это к примеру)...
- То есть хозяин завода не специалист в области ЛПК?
- Он из тех, кто «погружается» в тему глубоко и на совесть и знает многое из того, что неизвестно даже самым титулованным спецам, разумеется, в той сфере, которой занимается или собирается заниматься. Вот так произошло и в случае с линией OSB. Все нарабатывается практикой.
- Где будет находиться завод по производству?
- Производственная площадка располагается в 60 км от г. Кургана, в нескольких сотнях метров от федеральной трассы «Байкал», то есть транспортную доступность можно считать идеальной. Место было выбрано клиентом очень удачно: участок хорош с точки зрения логистики, к тому же он находится недалеко от других объектов г-на Невзорова. Площадка абсолютно новая, там в ноябре 2013 года был заложен первый камень, а сейчас уже построено новое здание, подведено электричество (электроэнергией завод обеспечивают два трансформатора суммарной мощностью 1,5 МВт), функционируют все коммуникации (тепло- и водоснабжение). Подключение электроэнергии дало возможность пускать и тестировать каждый станок в устанавливаемой линии.
- А как решается вопрос обеспечения тепловой энергией?
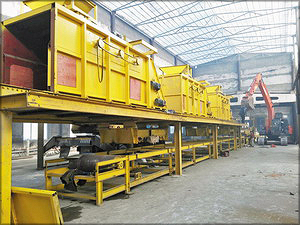
Установка оборудования участка формирования
трехслойного ковра плиты
- Сейчас тепло подается от сторонней организации, в дальнейшем нужды завода будут обеспечиваться тремя котлами-бойлерами, установленными на предприятии. Бойлеры работают на древесных отходах, которые образуются в результате деревообработки. Мы довольно долго выбирали это оборудование, руководствуясь критериями максимальной надежности, эффективности и простоты обслуживания. Не обошли вниманием и такую серьезную тему, как пожарная безопасность. На этом деле экономить не стоит, поэтому мы выбрали систему искрогашения от GreCon - простую в установке и эксплуатации.
- Качество древесной стружки для производства плит зависит от процесса сушки. Какие сушилки используете?
- Сушилки роторного типа были изготовлены на предприятиях КНР под контролем европейских специалистов и оборудованы системой искрогашения GreCon, а также приборами видео-наблюдения за технологическими операциями.
- Как организована на предприятии система аспирации?
- На прессе и охладителе используются «зонты» c мощной вентиляцией для отвода вредных клеевых паро-образований. На других участках (торцевания ковра плиты, участке подготовки щепы) используем мобильную аспирацию отвода мелкой стружки и пыли. Устройства спроектированы по нашим параметрам и произведены в Китае. Пожароопасность в мобильных установках значительно ниже, чем в циклонах, прежде всего поэтому мы и отдаем им предпочтение. Немаловажна и цена, конечно.
- Что сейчас происходит на площадке?
- Все оборудование доставлено на место, идет монтаж. Пресс уже работает в тестовом режиме, он прогревается, проверяется функционирование всех механизмов, прогоняются рабочие режимы. Фундамент у него семиметровый, а высота самого пресса двенадцать метров - это довольно серьезное сооружение.
Пресс - сердце линии, он и места в здании требует больше всего, и времени для настройки и отладки. Пресс 24-пролетный. В отличие от подобных прессов, установленных на других предприятиях, у нашего механизм загрузки - это система конвейеров без участия толкателя: сформированный ковер подходит к прессу, осуществляется позиционирование одного из загрузочных мест по высоте с конвейером и лентой основного конвейера ковер подается на ленту загрузочного механизма. Такое решение позволяет экономить время, тем самым увеличивая производительность, кроме того, отсутствие толкателя избавляет торец ковра плиты от повреждения.
К сожалению, толкатель так деформирует край плиты, что даже после пресса остаются микроскопические расслоения.
- Кто занимается монтажом оборудования?
- Монтаж ведет интернациональная команда, в ее составе итальянские, китайские специалисты, наши сотрудники. На установку блока фрез приедут немцы. Контроль осуществляют наши лучшие инженеры.
Сырье для производства OSB
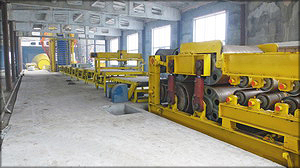
Сборка участка линии препресса
- Где и какими силами будут заготавливать сырье для производства? Где планируется брать лесозаготовительную технику?
- Лесозаготовку для завода будут вести на лесных участках клиента. По приблизительным оценкам, запаса древесины хватит больше чем на 10 лет.
Транспортное плечо для доставки леса на предприятие - менее 10 км. А техника у владельца завода уже есть, это машины John Deere, давно работающие для обеспечения сырьем имеющегося у г-на Невзорова лесопильного цеха.
- Древесина каких пород будет использоваться для изготовления плит OSB?
- Бытует мнение, что для получения качественных плит OSB годится только березовая или только сосновая древесина. Но, как сказал нам в неформальной беседе один канадский эксперт, ориентированно-стружечная плита по строению напоминает пирог: в нем допустимы разные ингредиенты, лишь бы он получился «вкусным». Мы считаем, что главное - показатели качества итоговой продукции. Ограничения обусловлены только рецептурой и технологией производства. Мы настраиваем технологические режимы линии на основе природного состава расчетной лесосеки, определяем, сколько в составе сырья будет сосны, сколько березы. В основном сырье будет сосновое.
- С сырьем разобрались. Но из-за санкций и событий, связанных с ними, слабым звеном производства может стать связующее...
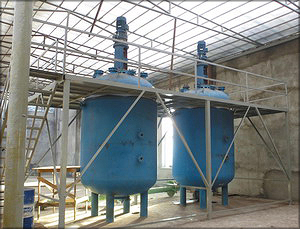
Участок подготовки клея
- Связующее тоже будет российское: от ОАО «УралХимПласт», г. Нижний Тагил. Мы путем проб и ошибок вышли на это предприятие, которое готово поставлять клей с эмиссией Е1 по приемлемой цене (менее 30 руб. за килограмм). Клей приходит готовый, в жидком виде, хотя на нашем производстве есть участок подготовки клея. Наш клиент смотрит вперед и планирует в перспективе выпускать плиту с использованием клея, уровень эмиссии которого понижен до Е0. Это необходимо для выхода предприятия со своей продукцией на новые рынки, в том числе и западноевропейский. Экологические нормы внедряются и ужесточаются повсеместно, поэтому лет через десять единственно допустимым уровнем эмиссии клея, используемого для производства плит OSB, будет Е0. Вероятно, это приведет к удорожанию плиты, но здоровье ведь бесценно, правда?
Понимая, что будущее за клеем с эмиссией Е0, наш клиент и решил заранее приобрести это оборудование. Возможно, первое время участок и не будет задействован, однако это отличный потенциал для развития.
Сбыт продукции
- Коль скоро в ближайшие годы уровень эмиссии будет сохраняться на уровне Е1, речь идет о продажах внутри страны. Насколько хорошо продуман и просчитан сбыт продукции, может быть, есть уже какие-то договоренности?
- Я уже говорил об оптимальном местоположении завода, он строится всего в нескольких сотнях километров от границы с Казахстаном.
А это на текущий момент один из крупнейших потребителей плит OSB. И, конечно же, наш клиент рассчитывает наладить реализацию продукции в России.
- А можно ли «разогнать» устанавливаемую линию и повысить производительность, или 60 тыс. м3 в год - это ее потолок?
- Нет, такое невозможно. Технология производства требует жесткого соблюдения производственных параметров для получения продукции надлежащего качества. Кроме того, надо понимать, откуда взялась цифра 60 тыс. м3. Такова оптимальная производительность мини-завода, необходимая для того, чтобы выйти на рентабельность и полностью окупить затраты в течение двух лет! Да-да, мы рассчитали срок полной окупаемости проекта с момента выхода на заявленную мощность. Два года - таков дисконтированный период окупаемости, заверенный экспертами PriceWaterhouse Coopers, которым мы представляли проект для консультации и оценки.
Мощность предприятия рассчитана с учетом доступности сырья. Можно построить завод мощностью 500 тыс. м3, но через год негде будет брать сырье - с такой ситуацией некоторым предприятиям отрасли уже приходилось сталкиваться. Производительность должна быть привязана к реальным возможностям, в том числе по лесосеке. Мы надеемся, что после недавнего визита на площадку губернатора Курганской области с сырьем проблем быть не должно.
- Насколько помню, он приезжал на предприятие в первых числах января этого года?
- Да, и обещал всемерную поддержку проекту. Так что значимость в рамках области проекту уже обеспечена, а там, кто знает, может, и на федеральный уровень выйдет.
Персонал и рабочий процесс
- Чего область ждет от завода - налоговых отчислений в бюджет региона?
- Разумеется. Но еще больше - задействованности людей. Для Курганской области 150 человек персонала на предприятии - это очень неплохо, ведь экономика региона в упадке. Единственная статья серьезного дохода - фермерство, крупных предприятий очень мало. Поэтому в области к предприятию большой интерес.
- Но, привлекая для работы местных жителей, владелец столкнется с традиционной проблемой: отсутствием необходимой квалификации у работников. Прямо на производстве придется учить?
- Мы этот вопрос прорабатывали. Оборудование сложное, поэтому на производстве обязательно должно быть несколько высококвалифицированных, компетентных специалистов, как минимум три-четыре профессионала на уровне мастеров участков или инженеров, которых придется нанять. Эти опытные деревообработчики смогут и операторов на производстве обучать, и постоянно руководить действиями персонала и контролировать процесс.
- Каков уровень автоматизации оборудования? Оператор просто нажимает на кнопки или многое придется делать вручную?
- Наша линия будет бесперебойно работать 11 месяцев в году, отключать ее экономически нецелесообразно. И задача людей, задействованных в обслуживании техники, будет заключаться в том, чтобы отслеживать ее корректную работу. Оператор будет управлять всей линией с единого центрального пульта. При возникновении нестандартных ситуаций к решению проблем будут подключаться те самые приглашенные спецы.
Почему OSB?
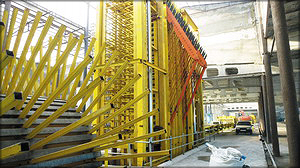
Финишный участок линии
- Расскажите, пожалуйста, почему ваша компания остановила свой выбор на производстве плит OSB.
- В 2009-2010 годах в отрасли стали все больше понимать, что обработка массива древесины отходит на второй план: мониторинг доступной лесосеки показывал, что невыгодно перерабатывать деловой лес, акценты стали смещаться в сторону глубокой переработки древесины и создания композитных материалов. Интересно, что толчком для нашей деятельности в этом направлении стал не модный европейский тренд, а китайская «подсказка». В то время в Поднебесной появилось много плитных предприятий, а также заводов, выпускающих оборудование для этих производств. Начинали они с копирования техники известных компаний Dieffenbacher и Siempelkamp, постепенно переходили на собственные разработки и достигли достойного уровня качества.
С азиатскими компаниями мы работаем с 2004 года, и весьма успешно. У нас в Китае два своих представительства, на юге и на севере, и именно их сотрудники сообщили нам об этих тенденциях. В 2011 году мы активно посещали китайские предприятия, изучая все нюансы ценообразования, технологии производства плит OSB и других плитных материалов.
На основании этого нового опыта постепенно стало понятно, чего мы хотим добиться и что можем предложить российскому рынку. Опираясь на китайское оборудование, обеспечить полный цикл производства плит OSB было невозможно, законченной оптимальной технологии не существовало. Поэтому мы стали привлекать к сотрудничеству специалистов из Европы, Канады, США. Канадский опыт особенно важен, один из лидеров производства OSB-щепы - канадская компания Carmanah Technologies, Inc. (а вопрос получения щепы был на тот момент узким местом производств плит OSB). В результате сотрудничества пришло понимание того, каким мы видим основной участок предприятия - участок производства кондиционной щепы. Многим производителям из-за несовершенства технологии изготовления щепы не удалось выйти на заявленные объемы, достичь необходимого качества продукции. Мы также сначала пошли по пути производства щепы из лущеной деловой древесины. Однако такая технология обуславливает высокую стоимость итогового продукта, да еще и зависимость предприятия от качества поступающего сырья, поэтому мы отказались от такого способа. К такому решению нас подвели и пожелания клиентов, говоривших нам, что доступной по цене деловой березовой древесины уже почти нет. Почти год мы потратили на проектирование участка подготовки щепы, о чем сейчас нисколько не жалеем. Тщательно выбирали и необходимое оборудование.
В результате остановили свой выбор на станке европейского производства, который устраивал нас по технологии подачи, выгрузки материала и получения самой щепы. Мы полностью заменили на нем блок ножевых головок - обратились в одну немецкую компанию (я бы предпочел не называть), которая по нашему техзаданию и с участием наших инженеров изготовила фрезы для линии. Это наш эксклюзив. К слову сказать, стоимость блока фрез составляет почти треть стоимости оборудования, согласитесь, это очень серьезно. Но мы решили, что тут нельзя экономить, и заказали этот узел именно у немцев, рассчитывая на надежность и долговечность инструмента.
Нам предстояло решить и другую непростую задачу: добиться, чтобы оборудование соответствовало самым строгим требованиям качества и в то же время было не очень дорогим. Проанализировав возможности и пожелания потенциальных клиентов, мы поняли, что сейчас предлагаются и развиваются крупные, дорогостоящие - миллиардные проекты федерального значения, которых не может быть много. И это ведет к своеобразной монополии на рынке, когда два-три производителя диктуют цены. По нашему мнению, это неправильно. Постепенно мы пришли к оптимальному комплекту оборудования для завода в Курганской области. В первую очередь мы постарались обеспечить комплектацию предприятия высококачественным, высокопроизводительным, но не очень дорогим оборудованием для главных участков производства: получения кондиционной щепы, формирования трехслойного ковра, прессования и получения плиты, соответствующей всем европейским нормам, а также участка сушки и нанесения связующего на щепу. А затем по тому же принципу оптимального соотношения цены и качества оснастили оборудованием остальные участки. По конечному решению каждого звена технологической линии мы консультировались с авторитетными специалистами. Можно сказать, наш проект полностью завизирован опытнейшими технологами производства плит OSB.
- Давайте резюмировать. За несколько лет удалось разработать и подготовить оптимальную комплектацию для мини-завода плит OSB. В его проектировании участвовали видные специалисты из разных стран. А кто был привлечен для комплектования «железа»?
- Комплектация, скажем так, сборная: оборудование линии как от китайских, так и от европейских (Германия, Италия) производителей, которые согласовали между собой все сочленения в ней. Некоторые участки мы вместе с технологами компаний дорабатывали на основе приобретенного опыта и проведенных изысканий. Улучшить нашу линию позволил в том числе и опыт действующих российских предприятий. При производстве составных частей линии на нескольких китайских заводах каждый ее компонент - от бункера сырой стружки до линии калибровки и шлифования готовой плиты - обязательно тестировался и согласовывался с нами. Производителей мы выбирали исходя из опыта их участия в подобных проектах, учитывая их репутацию, оценивая производственные условия, в которых они выпускают продукцию, интересуясь мнением пользователей станков. Отбор был довольно жесткий, но позволил создать качественную линию в поставленных условиях. Мы выбирали те производства, где китайцы выпускали детали для европейских машин или станки, поставляемые в Западную Европу, и где контроль качества был на самом высоком уровне.
Перспективы и ожидания
- Можно считать этот проект пилотным в области OSB как для вашей компании, так и для покупателя завода. Но и риски были для обеих сторон. Почему клиент заказывает завод компании, которая раньше не занималась подобными проектами и почему вы беретесь за столь непростой и трудоемкий проект именно для этого покупателя?
- Тут все совпало. Знаете, говорят, что людей с одинаковыми интересами притягивает. Прежде всего, этот проект был нам интересен! Наш клиент ездил с нами в командировки в Китай, Европу, Америку, заодно знакомился с отраслью, и загорелся идеей и лучшим из возможных способов ее реализации.
Кстати, г-н Невзоров не новичок в деревообработке, у него уже давно действует лесопильное производство, в течение десяти лет он успешно поставляет пиломатериалы в Казахстан, где большой спрос на деловой лес и обрезную и необрезную доску. Кстати, именно казахские деловые партнеры г-на Невзорова и высказали желание покупать плиты...
Мы и прежде поставляли г-ну Невзорову довольно много оборудования. Другое дело, изначально у клиента не было уверенности в осуществлении затеи, он знал о крупных OSB-проектах, знал, сколько они стоят, и понимал, что проекты такого масштаба не осилит. А мы в цифрах и фактах доказали, что за умеренные деньги можно создать рентабельный мини-завод.
- Так вот чего ждет от реализации курганского проекта «ТехЛесПром»!
- Мы никогда не замахивались на создание огромных производств, поскольку четко понимали: много мини-заводов для нашей экономики лучше, чем два-три предприятия-гиганта, которые станут манипулировать ценами на продукцию. А если удастся реализовать в разных регионах России десяток небольших производств, они в конкурентной борьбе придут к высокому качеству продукции и цены на нее предложат по-настоящему рыночные.
Затевая проект, мы не ставили перед собой цель заработать, наша прибыль минимальна, зато ожидания велики. Отработав технологию на этом предприятии, оптимизировав процессы, поняв, где можно сэкономить без потери качества, мы готовы предложить эту разработку многим российским предпринимателям. Завод под ключ за полтора года - согласитесь, совсем неплохо.
- Ну и наконец хотя бы намекните, какое развитие производства планирует ваш клиент?
- По результатам работы линии на заводе под Курганом владелец предприятия решит, что делать дальше: устанавливать еще одну для увеличения производительности или в качестве альтернативы приобретать оборудование для выпуска MDF.
Беседовал Максим ПИРУС