Удаление влаги из древесины в акустических полях
Под сушкой древесины принято понимать процесс удаления влаги (свободной и связанной) из древесины сортиментов и пиломатериалов путем ее испарения за счет воздействия подведенного сушильного агента. От того, насколько своевременно и качественно проведена сушка, зависят сохранность, сортность, область применения и в конечном счете рыночная стоимость пиломатериалов. Именно по этой причине сушка пиломатериалов является важнейшим этапом переработки древесины, и стоимость этой операции соизмерима со стоимостью самой древесины (а нередко и превышает ее).
Сушку древесины традиционно выполняют после распиловки, что в условиях современного глобального кризиса вряд ли разумно. От лесозаготовительного (лесопогрузочного) пункта до лесопильного (деревообрабатывающего) участка предприятия вместе с древесиной (20% массы бревна) транспортируют древесную влагу (80% массы бревна), а процесс распиловки сырой древесины сопровождается значительными финансово-временными затратами и существенным объемом отходов (в виде опилок).
Сегодня во всем мире широко распространены и отработаны разные варианты конвективной и конвективно-термической технологий сушки пиломатериалов. Но именно термическое воздействие на материал, который подвергается сушке, таит в себе множество минусов. В высушиваемом материале возникают механические напряжения, и при высокой скорости сушки древесина частично разрушается, что ведет к выбраковке значительной (30% и более) части товарного продукта и, соответственно, снижению процента его выхода, а неравномерность распределения влаги по длине и толщине пиломатериала ведет к внутренним деформациям и к дополнительной выбраковке части товарного продукта. В процессе сушки по разным причинам нередко возникают нештатные технологические ситуации, в результате которых температура сушильного агента поднимается выше нормы для данного технологического этапа сушки, древесина перегревается и значительная ее часть приходит в негодность. И самое главное: такой способ сушки отличает низкий коэффициент полезного действия. В частности, на сушку 1 м3 пиломатериалов затрачивается, в зависимости от толщины пиломатериалов и начальной и конечной влажности древесины, от 400 до 800 кВт·ч.
Следует заметить, что в настоящее время на рынке полностью отсутствуют отечественные конвективно-тепловые сушильные установки, а те, что выпускают за рубежом, очень дорогие. С учетом затрат на их приобретение, доставку, монтаж и пусконаладочные работы (даже без последующего сервисного обслуживания) срок их окупаемости составляет 5-7 лет, что явно неприемлемо в современных экономических условиях России.
Именно по этой причине в последние годы для сушки пиломатериалов в нашей стране и за рубежом активно пытаются применять и другие технологии: кондуктивные, вакуумные и т. д. Однако процессы сушки древесины с использованием этих технологий также предполагают создание разности содержания влаги в теплоносителе и пиломатериале, что приводит к возникновению внутренних напряжений в древесине и, как следствие, ухудшению качества высушиваемого материала (появлению трещин, коробления, скручивания и т. д.).
Поэтому повышение качества высушиваемого материала и производительности оборудования для удаления влаги из древесины при одновременном снижении энергоемкости оборудования и сегодня остаются основными задачами технологов и конструкторов и производителей оборудования для сушки древесины.
В настоящей публикации предложены технологические схемы низкотемпературного (температура атмосферного воздуха - до 25°С) удаления влаги из сортимента древесины на открытом воздухе (под навесом) и среднетемпературного (температура сушильного агента 30-35°С) удаления влаги из пиломатериалов в акустической сушильной камере (АКСК) под действием акустических волн относительно малой интенсивности (130-140 дБ относительно порогового уровня).
Первые сообщения о том, что интенсивные ультразвуковые колебания способны воздействовать на процессы тепло- и массообмена, и в частности на сушку материалов, появились более 50 лет назад как в нашей стране, так и за рубежом [4]. Однако касались они, в основном, сушки термочувствительных (фармацевтических) препаратов, горючих и взрывчатых материалов. При этом высушиваемый материал подвергался со стороны газовой среды воздействию ультразвукового поля с интенсивностью 145 дБ, обычно создаваемого газоструйными излучателями.
Наибольший интерес к акустической сушке компонентов взрывчатых веществ проявлялся в начале 1980-х годов не только в СССР, но и в США и Японии. В частности, появлялись сообщения о том, что фирма Macrosonic (США) выпускает лабораторные акустические модули, предназначенные для сушки небольших партий термочувствительных материалов. Однако следует признать, что акустическая сушка так и не вышла за пределы лабораторных исследований. Основная причина - технологическая, и связана она с отсутствием необходимых (по мощности и диапазону частот) генераторов и акустических излучателей.
Подходящий вариант был найден в области исследований устойчивости и автоколебаний сверхзвуковых струй, которые проводятся при эксплуатации объектов ракетно-космической техники: компрессор снабжал сжатым воздухом пневмоакустические излучатели [7].
Однако особенностью такой ультразвуковой сушки является высокая стоимость используемой акустической энергии и низкий (20-25%) КПД излучателей. Именно поэтому она применялась главным образом при производстве дорогостоящих биологических и фармацевтических препаратов, в частности, термочувствительных порошков из антибиотиков, гормональных препаратов и т. д.
Говоря о теоретических аспектах удаления влаги из древесины, необходимо отметить, что ТМО обычно называют физический процесс переноса энергии и массы вещества из одних областей пространства в другие [4]. Во многих технологических процессах ТМО протекает при фазовых и химических превращениях. Сегодня в разных технологических целях конструируют аппараты с применением либо одной, либо нескольких форм ТМО и стараются оптимально использовать их особенности. Известно, что во многих случаях комплексное применение разных форм ТМО позволяет существенно интенсифицировать технологические процессы [4].
В свое время было предпринято много попыток ускорить процессы переноса энергии и массы путем комбинированных и периодических физических воздействий (в том числе акустическими волнами) на субстрат; для чего использовались инфракрасные лучи, токи высокой частоты, сброс давления, переменные электрические и магнитные поля, упругие колебания инфразвукового, звукового и ультразвукового диапазонов частот. Попытки применения ультразвука в технологических процессах были впервые предприняты еще в 30-е годы прошлого столетия в области диспергирования твердых и жидких тел, а также коагуляции аэрозолей. Ускорение процессов массопереноса акустическими колебаниями доказано многочисленными экспериментами.
Сущность многоэтапного метода удаления влаги из древесины и пиломатериалов в акустических полях относительно малой интенсивности, разработанного автором этой публикации, отражена на рис. 1, 2, 3 и 4. Этапы метода описаны ниже.
Первый этап осуществляется на лесопогрузочном участке (рис. 1):
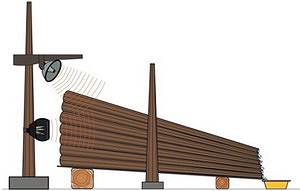
Рис. 1. упорядоченная укладка бревен
- сортименты (бревна) укладывают в штабель нижними частями (комлями) в одну сторону, а верхними частями (верхушками) - в другую; приподнимают нижние части сортиментов на несколько (не менее трех) градусов; штабель ориентируют с учетом розы ветров в данной местности, и т. д.;
- развертывают модуль мобильной акустической установки на базе дизель-генератора электрической мощностью 3-4 кВт, а также восемь акустических излучателей, размещенных определенным образом относительно штабеля; два генератора специальных сигналов и два четырехканальных усилителя мощности в термошкафу габаритами 1 х 1 х 1 м;
- устраивают непрерывное (при помощи четырех излучателей) и импульсное (также четыре излучателя) излучение акустических волн, направленных на штабели со всех сторон: сверху вниз и вдоль поверхности сортиментов (бревен).
Как показали результаты полупромышленных (сушка ограниченного объема древесины с использованием промышленного оборудования) испытаний, проведенных в России, Республике Корея и Вьетнаме, на первом этапе этого метода можно достичь следующих результатов:
- уменьшения примерно на 15% транспортной влажности сортимента древесины, что позволяет повысить приблизительно на 15% загрузку транспортного средства (автомобиля) по объему при сохраняемых на прежнем уровне нагрузках на оси транспорта, если бы в автомашину загружались сортименты естественной влажности;
- перемещения в акустических полях свободной влаги из центральной части сортимента на его периферию, в первую очередь в кору и заболонь, а также создания наиболее благоприятных условий для последующей распиловки сортиментов.
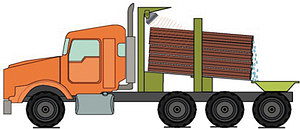
Рис. 2. Реализация метода на автомобиле с прицепом
Второй этап реализуется на транспортном средстве (рис. 2):
- сортименты укладывают на транспортное средство в мини-штабель нижними частями к кабине с акустическими излучателями, а верхними частями - в противоположную сторону, приподнимают нижние части на несколько (не менее трех) градусов, и т. д.;
- выполняют развертывание модуля мобильной акустической установки на базе дизель-генератора автомобиля электрической мощностью 1-2 кВт, а также четырех акустических излучателей, размещенных определенным образом относительно штабеля, двух генераторов специальных сигналов и двух двухканальных усилителей мощности в термошкафу габаритами
0,4 х 0,4 х 0,4 м; - осуществляют непрерывное (с помощью двух излучателей) и импульсное (с помощью двух излучателей) излучение акустических волн, направленное на штабели сверху вниз и вдоль поверхности сортиментов (бревен).
Как показали результаты полупромышленных испытаний, благодаря реализации разработанного метода на этом этапе можно достичь следующих результатов:
- уменьшения примерно на 10% транспортной влажности древесины сортиментов;
- перемещения в акустических полях свободной влаги из центральной части материала на его периферию и создание благоприятных условий для распиловки сортиментов.
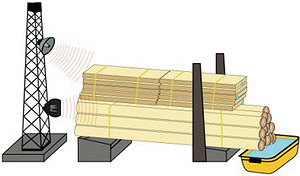
Рис. 3. Реализация метода на лесопильном участке
Третий этап реализуется на лесопильном участке (рис. 3):
- пиломатериалы укладывают в пакет нижними частями (согласно структуре волокон древесины) в одну сторону, а верхними частями - в другую, каждый слой перекладывают специальными прокладками, приподнимают нижние части сортиментов на несколько (не менее трех) градусов, пакет жестко фиксируют и ориентируют с учетом розы ветров в данной местности, и т. д.;
- выполняют развертывание модуля мобильной акустической установки на базе дизель-генератора автомобиля электрической мощностью 3-4 кВт, восьми акустических излучателей, размещенных определенным образом относительно пакета пиломатериалов, двух генераторов специальных сигналов и двух четырехканальных усилителей мощности в термошкафу габаритами 1 х 1 х 1 м;
- осуществляют непрерывное (с помощью четырех излучателей) и импульсное (с помощью четырех излучателей) излучение акустических волн, направленное на штабели сверху вниз и вдоль поверхности сортиментов (бревен).
Как показали результаты полупромышленных испытаний, на этом этапе можно достичь следующих результатов:
- уменьшения примерно на 30% транспортной влажности пиломатериалов, которое позволяет увеличить почти на 30% объем сортиментов, загружаемых в транспортное средство (автомобиль) при тех же нагрузках на оси автомашины, если бы в нее загружались сортименты естественной влажности;
- равномерного распределения влаги по всей толщине пиломатериалов в акустических полях, что создает благоприятные условия для последующей сушки пиломатериалов (конвективной, конвективно-тепловой, акустической и т. д.).
Максимальный эффект акустической сушки на открытом воздухе (под навесом) - в течение первых суток скорость снижения абсолютной влажности древесины в час составила 0,78% при 100% сохранении качества пиломатериалов и продукции - наблюдался при следующих параметрах: скорость ветра 3-5 м/с, температура воздуха 20-25°С, относительная влажность 40-50%; интенсивность излучения акустических волн более 135 дБ относительно порогового уровня, два направления одновременного воздействия излучения на пиломатериал (сверху и сбоку) и два типа сигналов (импульсный и непрерывный).

Рис. 4. Акустическое удаление влаги из пиломатериалов
на деревообрабатывающем участке
Четвертый этап реализуется на деревообрабатывающем участке (рис. 4):
- пакеты пиломатериалов укладывают в акустическую сушильную камеру нижними частями (согласно структуре волокон древесины) в одну сторону, а верхними частями - в другую, приподнимают нижние части сортиментов на несколько (не менее трех) градусов, и т. д.;
- выполняют развертывание модуля мобильной акустической установки на базе восьми акустических излучателей, размещенных определенным образом относительно пакета пиломатериалов, двух генераторов специальных сигналов и двух четырехканальных усилителей мощности в термошкафу габаритами 1 х 1 х 1 м;
- осуществляют непрерывное (с помощью четырех излучателей) и импульсное (с помощью четырех излучателей) излучение акустических волн, направленное на штабели сверху вниз и вдоль поверхности сортиментов (бревен).
В результате полупромышленных испытаний способа среднетемпературного удаления влаги из пиломатериалов (пакеты тарной дощечки) и продукции (EUR-палеты) в акустической сушильной камере (АКСК), проведенных в Испании (компания Maderas, 2013 год), установлено:
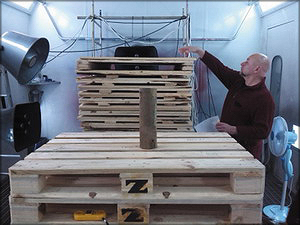
- скорость акустической сушки определяется (в порядке приоритетности): скоростью движения сушильного агента, его температурой и относительной влажностью, а также интенсивностью, направлением воздействия и формой акустических волн;
- максимальный эффект акустической сушки пиломатериалов в АКСК (средняя за первые сутки скорость уменьшения абсолютной влажности в час - 1,13% при 100% сохранении качества пиломатериалов и продукции) наблюдался при следующих параметрах: скорость сушильного агента 1-2 м/с, температура 30-350С; относительная влажность 30-35%; интенсивность излучения акустических волн более 135 дБ относительно порогового уровня, два направления одновременного воздействия на пиломатериал (сверху и сбоку) и два типа сигналов (импульсный и непрерывный);
- наиболее целесообразно укладывать в одну связку три тарные дощечки. В этом случае скорость акустической сушки, при всех прочих равных условиях (параметрах сушильного агента и акустических волн), увеличивается почти в два раза.
Продолжительность типовой конвективно-тепловой сушки (при температуре сушильного агента 60°С) тарных дощечек в сушильной камере объемом 200 м3 компании Maderas составляет пять суток.
Для реализации вышеописанного метода на предприятии существует насколько вариантов построения технологического процесса в зависимости от объемов и сроков поставки продукции, потенциальных возможностей и текущего состояния склада полуфабрикатов, сезонных погодно-климатических условий и т. д.
Необходимо отметить, что в настоящее время в России (регионах Крайнего Севера, Дальнего Востока и т. д.) и за рубежом (во Франции, Испании, Финляндии, Вьетнаме и т. д.) отмечается повышенный интерес к созданию мобильных акустических сушилок (например, на базе 10-ти или 20-футового контейнеров), а также к теоретическим аспектам акустической сушки (например, такие исследования ведутся в институте Теоретической и прикладной механики СО РАН, г. Новосибирск).
Основных причин того, что до сих пор не создано эффективных акустических устройств, а процессы акустической сушки не вышли за пределы лабораторий, несколько:
- высокая стоимость акустической энергии. Все пневмоакустические излучатели, используемые до настоящего времени в акустических сушилках, обладают довольно низким (менее 25%) КПД. Поэтому существует необходимость не только совершенствования газоструйных излучателей, но и поиска новых источников акустической энергии;
- недостаток знания теории акустической сушки у разработчиков акустических сушильных камер, а отсюда недостаточно эффективное использование акустических колебаний. Поэтому им необходимо обратиться к теории акустической сушки;
- неэффективные инженерно-конструкторские решения при разработке акустических сушильных камер; отсюда неравномерное высушивание материала, обусловленное разной удаленностью его участков от источника акустических колебаний. Известно, что существует т. н. критический уровень звукового давления (от 140 до 150 дБ), и если процесс сушки проводить без соблюдения этого уровня излучения, то он ничем не будет отличаться от процесса обычной конвективной сушки. Поэтому необходимо обеспечить интенсивность акустической энергии на уровне не менее 150 дБ на самых удаленных участках сушилки. Этого можно добиться только путем увеличения интенсивности колебаний, излучаемых газоструйным излучателем, до 165-170 дБ, что технически реализовать очень сложно; кроме того, требуются специальные меры защиты обслуживающего персонала от воздействия акустических колебаний;
- нерациональное использование энергии акустических колебаний в существующих сушилках. Это объясняется отсутствием концентрации акустической энергии на высушиваемом материале. Энергия от газоструйного преобразователя (излучателя) распространяется равномерно по всему объему сушильной камеры и не концентрируется на высушиваемом материале. Многократные отражения от стенок сушильной камеры приводят к появлению стоячих волн.
В процессе сушки в объеме сушилки и на поверхности высушиваемого материала появляются участки с разной интенсивностью акустического воздействия. На некоторых участках интенсивность может быть меньше т. н. критического уровня, что приводит к неравномерности сушки и снижению качества высушиваемого материала; - риск возникновения недопустимого для разных материалов поверхностного нагрева. Он обуславливается формированием высушенного поверхностного слоя (поверхностной корки), особенно у той части высушиваемого материала, которая располагается вблизи источника ультразвуковых колебаний;
- высокая сложность и значительная стоимость акустических сушилок, когда требуется обеспечить большой объем акустической сушки, и т. д.
Все вышеперечисленные недостатки технологии акустической сушки древесины и техники для использования этого метода сдерживают широкое применении акустической сушки капиллярно-пористых материалов, а в некоторых случаях делают его экономически невыгодным или вообще недопустимым (из-за возможного поверхностного нагрева).
За последние два десятилетия ситуация в области акустической сушки древесины существенно изменилась. Этому, с одной стороны, способствовало создание новых конструкций акустических излучателей (например, электроакустических). С другой стороны, необходимость создания малогабаритных акустических сушилок обусловлена появлением большого числа малых предприятий лесопромышленного комплекса.
Очевидно, что использование мобильных акустических сушилок на лесозаготовительном, лесопогрузочном, лесопильном и деревообрабатывающем участках позволит на 30-50% сократить финансово-временные затраты на сушку единицы объема древесины, а также полностью исключить брак сушки пиломатериалов из-за их внутренних и внешних деформаций.
Сергей БАХАРЕВ, д-р техн. наук, проф.