Повышение производительности ленточнопильных станков
Ленточное пиление - одна из наиболее эффективных технологий лесопиления, которая обеспечивает минимальную толщину реза, индивидуальный раскрой бревна и за счет этого позволяет добиться максимального выхода полезной продукции, причем не требуется предварительная сортировка пиловочника, что существенно снижает производственные затраты. Однако принцип ленточного пиления содержит в себе нереализованный на текущий момент потенциал повышения производительности - возможность пиления обеими ветвями ленточной пилы.
В свое время в отечественном леспроме предпринимались отдельные попытки ввести в практику технологию одновременного пиления обеими ветвями. Однако из-за ряда недостатков они не получили развития.
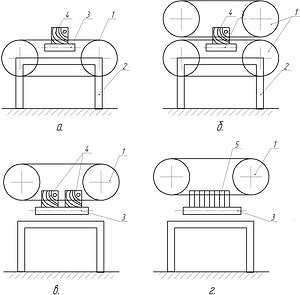
Рис. 1. Принципиальная схема горизонтального ленточно-делительного станка: 1 – ленточнопильный агрегат, 2 – станина, 3 – механизм подачи, 4 – брус, 5 – клееный брус
Широко известны горизонтальные ленточно-делительные станки (ЛДС), у которых пильный агрегат расположен ниже уровня подающего стола, что обеспечивает компактность ЛДС (рис. 1а). На этих станках пиление выполняется верхней ветвью пилы.
Также известны сдвоенные ЛДС, в которых пильные агрегаты расположены один над другим, за счет чего одновременно осуществляются два реза (рис. 1б): один агрегат выполняет пиление нижней ветвью ленточной пилы, а другой - верхней. Таким образом, очевидно, что пиление можно вести как одной, так и другой ветвью пилы. Часто применяется на практике и вариант, когда одной ветвью одновременно распиливаются два бревна и более или несколько брусьев (рис. 1в), что обеспечивает заметное увеличение производительности. Кроме того, на ЛДС ведется распиловка значительных по ширине клееных заготовок на мебельный щит (рис. 1г). Следовательно, при использовании ленточной пилы можно выполнять пропил (рез) довольно большой ширины или несколько резов одновременно.
Возникает вопрос: нельзя ли часть этих резов перенести на вторую ветвь?
Движение резания ленточной пилы осуществляется за счет полезной силы трения, возникающей на участках огибания пилой шкивов, на которые эта пила натянута. В большинстве случаев у величины указанной силы трения имеется определенный запас. Кроме того, коэффициент трения может быть увеличен, например, за счет дополнительного фрикционного покрытия шкивов, как это часто делается на столярных ленточнопильных станках (ЛПС). Полезная сила трения также может быть увеличена за счет использования пил, для изготовления полотен которых применена сталь, допускающих повышенное предварительное натяжение. Подводя итог сказанному, приходим к заключению: усилие, требуемое для протяжки ленточной пилы при пилении обеими ветвями, может быть обеспечено.
Для полноты картины следует упомянуть, что при работе станка натяжение ветвей отличается согласно так называемому соотношению Понселе - это вызвано, в основном, моментом трения подшипников ведомого шкива и его (т. е. шкива) трением о воздух. На практике этой разностью можно пренебречь.
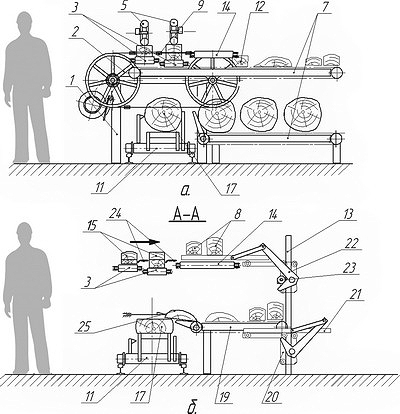
Рис. 2. Схема станка с бревнопильной кареткой при реализации метода пиления второй ветвью ленточной пилы (из патента «Ленточнопильный станок, RU 2547551»)
1 – станина, 2 – ленточнопильный агрегат,
3 и 5 – механизмы подачи второй ветви,
7 – буферные накопители первой и второй ветвей,
9 – промежуточный успокоитель второй ветви пилы,
11 – бревнопильная тележка,
12 – брус на буферном накопителе второй ветви,
14 – возвратный рольганг, 17 – бревно
Приведенные доводы позволяют заключить, что теоретически пиление второй ветвью ленточной пилы возможно. Реализация схем станков на основе подобных теоретических выкладок потребовала поиска новых технических решений (см. патент «Ленточнопильный станок, RU 2547551»*). Одним из рациональных решений проблемы представляется схема с бревнопильной кареткой (рис. 2).
Горизонтальный ленточнопильный агрегат установлен неподвижно. На его нижней ветви при помощи бревнопильной тележки выполняется распиловка бревна на горбыль и трехкантный брус. Тележка оснащена зажимами бревна и кантователем. Отпиленные полуфабрикатные пиломатериалы в конце хода тележки сталкиваются на приемную эстакаду и далее подъемником перемещаются на «второй этаж» - ко второй ветви пилы, где по возвратному рольгангу поступают на буферную эстакаду-накопитель. Их дальнейшая распиловка выполняется верхней ветвью. Готовые доски уходят на сортировку, недопиленные пиломатериалы сталкиваются на возвратный рольганг и возвращаются на повторный раскрой.
Пиление на второй ветви происходит в режиме «торец в торец». Скорость подачи может регулироваться за счет обратной связи в зависимости от нагрузки, напряжений в теле пилы и других параметров. При загрузке бревна, его возврате и кантовании скорость подачи на второй ветви можно увеличивать, поскольку нагрузка на пилу снижается. В целом как установка размеров отпиливаемых пиломатериалов на обеих ветвях, так и управление распиловкой могут быть в значительной степени автоматизированы. Например, это можно сделать с помощью программно-логических контроллеров (ПЛК) с автоматическим определением карт оптимального раскроя бревна. Таким образом, производительность станка при работе по подобной схеме теоретически может быть увеличена в два раза и более по сравнению с оборудованием, не оснащенным автоматикой.
Представляет интерес и реализация принципа пиления обеими ветвями в ленточно-делительных станках. Если применить обычный подход к проектированию ЛДС, то на каждой ветви пилы следовало бы установить линию возврата недопиленных брусьев на дальнейшую распиловку. Однако каждая линия возврата состоит из двух поперечных и одного продольного транспортеров. Причем длина продольного транспортера возврата должна превышать две длины распиливаемого пиломатериала, а это более 12 м. В этом случае станок становится неоправданно громоздким. Усложняется и работа оператора, так как требуется одновременно следить за обеими ветвями ЛДС.
Для решения этой проблемы был найден принцип распиловки, значительно упрощающий как конструкцию станка, так и работу на нем. Условно назовем его принципом «деления на два». Он заключается в том, что на второй ветви ЛДС распиливаются брусья, полученные на первой ветви, толщина которых равна: А + В + σ, где А и В - толщина кондиционных досок, σ - толщина реза. Благодаря такому алгоритму, при распиловке на второй ветви из бруса получаются две доски кондиционной толщины А и В, не требующие возврата на повторную распиловку. Далее они поступают непосредственно на сортировку и укладываются в штабели готовых пиломатериалов. Конструкция ЛДС упрощается и удешевляется, а распиловка на второй ветви может быть легко автоматизирована. Надо лишь установить на станок механизм передачи брусьев с первой ветви на вторую и буферный накопитель перед второй ветвью.
Какие проблемы могут возникнуть при реализации подобного принципа раскроя?
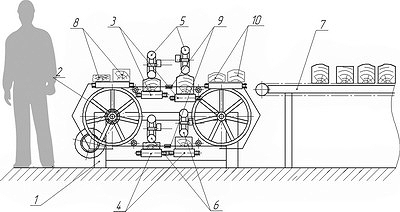
Рис. 3. Схема станка для работы методом пиления второй ветвью ленточной пилы (из патента «Ленточнопильный станок, RU 2547551»):
1 – станина, 2 – ленточнопильный агрегат,
3, 4, 5, 6 – механизмы подачи первой и второй ветвей,
7 – буферный накопитель, 8 – возвратный рольганг нижней ветви,
9 – промежуточные успокоители, 10 – возвратный рольганг верхней ветви
Одна из возможных проблем: при распиловке трехкантного бруса значительной длины и сечения может иметь место отклонение от прямолинейности по базовой пласти (деформация), обусловленное высвобождением внутренних напряжений в бревне. Такая ситуация характерна прежде всего для распиловки древесины лиственных пород. В этом случае усилия прижимных вальцов подающего рольганга может оказаться недостаточным для точного базирования бруса по направляющим роликам в зоне резания (для обеспечения точного пиления пила в резе должна быть строго параллельна пласти бруса). Поэтому не исключено, что для обеспечения точной геометрии пиломатериалов для первой ветви может потребоваться установка рольганга плавающего типа с адаптивным механизмом регулировки заднего конца бруса по высоте (оговорюсь: это теоретическое предположение требует проверки на практике). Проблема повышенного нагрева пилы может быть решена за счет ее дополнительного охлаждения на участках огибания шкивов, а также подачи из форсунок охлаждающей жидкости, прошедшей охладительное устройство.
Поскольку пила за единицу времени распиливает существенно больший объем древесины, чем на обычном станке, пропорционально возрастает и ее затупление. Поэтому целесообразно применять пилы с повышенной стойкостью зубьев, в том числе биметаллические, а возможно, и стеллитированные. К тому же у зубьев пил, оснащенных стеллитом, поперечное сечение «ласточкин хвост», обеспечивающее лучший вынос опилок, а, следовательно, высокую скорость пиления. Для повышения ресурса работы дорогостоящих пил целесообразно оснащать станок шкивами диаметром 800 мм и более. Также целесообразно предварительно выполнять окорку пиловочника и пропускать его через металлодетектор.
В качестве механизма натяжения пилы желательно применять пневматическое или пневмогидравлическое устройство, способное обеспечить постоянство усилия натяжения и минимальное время реакции при температурных удлинениях пилы, это повышает стабильность пиления и увеличивает ресурс пил.
Рассмотрим дополнительные возможности, которые предоставляет технология пиления обеими ветвями.
Особый интерес представляет применение этого метода в ленточнопильных станках с узкой пильной лентой. У подобных станков, как известно, невысокие производительность и экономическая эффективность. С другой стороны, в отличие от широких пил, узкие не требуют сложных и дорогостоящих процедур, связанных с подготовкой пил к работе: вальцовки, рихтовки, обкатки. С учетом этих факторов в перспективе могут быть разработаны довольно недорогие, экономически эффективные станки для пиления двумя ветвями.
С точки зрения повышения производительности интерес представляет также групповая распиловка. Например, реализация пиления на ветвях в два потока. Устройства подачи материала на распиловку предпочтительно должны быть независимы друг от друга - для независимой установки размеров отпиливаемых брусьев (досок). Ленточная пила в промежутке между зонами резания потоков может оснащаться дополнительным успокоителем щелевого типа с подачей охлаждающей жидкости и, возможно, продувкой пазух зубьев от опилок.
Поскольку на текущий момент действующего прототипа станка пока не создано, попытаемся хотя бы приблизительно, с учетом допущений, оценить возможную производительность ЛДС со схемой пиления в два потока на каждой из ветвей.
Примем во внимание результаты проведенного в реальном времени хронометража пиления на хорошо налаженном ЛПС Wood-Mizer LT-40: время пиления одной 6-метровой доски из бруса толщиной 150 мм составляет в среднем 20 с.
Если предположить, что подача на ЛДС установлена в два раза меньше, то есть на один рез аналогичной доски отводится 40 с, то за одну минуту, согласно принципу «деления на два», на второй ветви будет распилено шесть досок, за час - 360 досок, то есть примерно 10 м3/ч обрезной доски. Таким образом, предполагаемая производительность ЛДС с учетом принятых допущений может составить около 70 м3 обрезного пиломатериала за 8-часовую смену (из расчета: 7 ч работы станка + 1 ч на обслуживание оборудования).
Из приведенных расчетов следует: если объединить в одном лесопильном комплексе узколенточный бревнопильный станок, выполняющий распиловку бревен на горбыль и трехкантный брус, и ЛДС, подобный тому, о каком только что шла речь, можно достичь существенного повышения экономических показателей процесса пиления. Конечно, приведенный вариант также требует проверки на практике.
Принцип пиления обеими ветвями может быть применен и в вертикальных ЛПС, в том числе широколенточных. Ухудшения выноса опилок на второй ветви из-за действия силы тяжести с учетом динамики процесса пиления не ожидается. Вертикальный шлейф опилок на второй ветви может улавливаться аспирационной системой. Устройство подачи бруса на второй ветви должно быть дополнено роликами со стороны верхней пласти бруса, ограничивающими смещение бруса вверх ввиду действующего на него усилия резания.
Большой диаметр шкивов, устанавливаемых на широколенточных станках, позволяет применить на второй ветви схему, аналогичную схеме вертикальных делительных станков с возвратом брусьев на дораспиловку, причем возвратный транспортер может быть общим для обеих ветвей. Согласно такой схеме, на первой ветви бревно распиливается на горбыль, подгорбыльные доски и трехкантный брус. Далее горбыль и подгорбыльные доски уходят на переработку, а трехкантный брус по возвратному транспортеру поступает на вторую ветвь, на которой распиливается на доски. Готовые доски поступают на сортировку, недопиленный брус - на возвратный транспортер и дальнейшую распиловку.
Как вариант, пиление на второй ветви может выполняться в те промежутки времени, когда на первой ветви проводятся вспомогательные операции: возврат тележки, установка очередного размера, кантование, зажим бревна, подача и установка очередного бревна.
Реализация подобной схемы с учетом возможности автоматизации операций позволила бы значительно сократить непроизводительные потери времени. Производительность станка может возрасти в два и более раз. Возможно также некоторое повышение ресурса пил на единицу продукции и сокращение удельных затрат на подготовку пил. Таким образом, принцип пиления второй ветвью ленточной пилы теоретически позволяет значительно повысить производительность и экономическую эффективность технологии ленточного пиления.
Необходима проверка предложенных схем на практике: постановка эксперимента, изучение особенностей поведения пилы при пилении второй ветвью, создание и отработка действующего образца и, в случае достижения положительных результатов, внедрение новой технологии в производство.
Виктор ШЕРШНЕВ