Как измерить твердость режущего инструмента
Любой производственник, которому приходилось сталкиваться с вопросами обслуживания дереворежущего инструмента, знает, как иногда бывает сложно найти причины быстрого износа инструмента или его поломки.
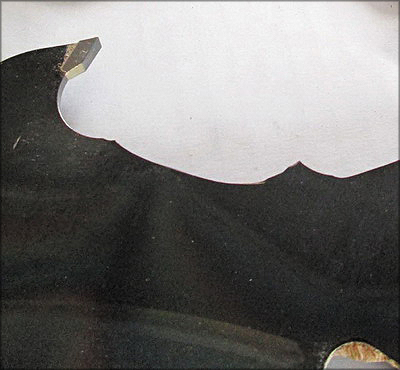
Рис. 1. Причина обрыва зуба пилы – чрезмерная твердость (неправильная
закалка) ее корпуса. Брак предприятия-изготовителя
На стойкость режущего инструмента и его длительную эксплуатацию без проблем влияют следующие факторы: качество сталей и материалов, из которых сделан инструмент, а также соблюдение технологии при его изготовлении; эксплуатация в соответствии с рекомендациями производителя; качественное сервисное обслуживание. Результатом несоблюдения этих условий является 90% проблем - поломок или выхода из строя режущего инструмента.
Как правило, производственники не любят признаваться в нарушении правил эксплуатации режущего инструмента и появление проблем оправдывают его низким качеством. Бывает, что поставщики, которые не хотят портить отношения с крупными клиентами, идут на замену инструмента без выяснения причин его выхода из строя. Но при повторении подобной ситуации рано или поздно клиент и поставщик прекращают сотрудничество. Ведь, как показывает практика, источник проблем надо искать на производстве клиента. Но на производстве это сделать сложнее, чем в компании - производителе режущего инструмента, так как у предприятий, эксплуатирующих инструмент, обычно нет необходимого оборудования и специалистов.
Крупные европейские инструментальные фирмы строго соблюдают технологии на своих производствах, много средств вкладывают в НИОКР и внедрение в производство новых видов дереворежущего инструмента, ревностно относятся к проблемам, которые выявляются при эксплуатации инструмента на предприятиях клиентов, и чаще всего заменяют инструмент без проблем, если обнаруживаются признаки некачественного изготовления, то есть заводской брак.
А при серьезных проблемах, например выходе из строя сразу нескольких инструментов, технические представители инструментальных фирм обязательно выезжают на производство и пытаются установить причины произошедшего, обследуют основное технологическое и заточное оборудование, проверяют соблюдение технологических режимов резания и другие факторы, которые могли стать причиной дефекта. Схема разрушения корпуса круглой пилы из-за неправильной (повышенной) твердости корпуса пилы приведена на рис. 1.
Рассмотрим основные факторы, оказывающие влияние на качество выпускаемого режущего инструмента.
Виды термической обработки стали для режущего инструмента
Свойства стали, подвергнутой термической обработке, зависят от ее химического состава, времени (или скорости) и температуры нагрева, времени выдержки при этой температуре и времени (скорости) охлаждения. В зависимости от режимов нагрева и охлаждения различают несколько основных видов термической обработки стали.
Отжиг. Этот процесс включает в себя нагрев стали до температуры фазовых превращений, выдержку при этой температуре и медленное охлаждение вместе с печью. Отжиг инструментальных сталей осуществляют для снижения их твердости с целью улучшения обрабатываемости на станках, снятия внутренних напряжений и подготовки структуры стали к другим видам термической обработки.
Нормализация. Ее производят почти так же, как и отжиг, но изделие охлаждают не вместе с печью, а на воздухе, то есть быстрее. Нормализацию применяют для исправления структуры перегретой стали, снятия внутренних напряжений и улучшения обрабатываемости. Этот процесс требует значительно меньше времени, чем отжиг.
Закалка. Это нагрев стали до температуры критического диапазона или выше, выдержка при этой температуре и последующее быстрое охлаждение. Закаливают сталь для повышения твердости, прочности и износостойкости. Исходной структурой при закалке является аустенит, который в зависимости от скорости охлаждения переходит в мартенсит, троостит или сорбит.
В зависимости от химического состава стали, формы, размеров и назначения дереворежущего инструмента применяют разные способы закалки:
- закалка в одной среде: инструмент, нагретый до температуры закалки, полностью охлаждается только в одной среде. Это самый простой и наиболее распространенный способ. Его недостаток в том, что при быстром охлаждении в инструменте возникают сильные внутренние напряжения, вызывающие коробление, а иногда и появление трещин. Такой способ закалки применяется для инструментов простой формы;
- закалка в двух средах: инструмент охлаждается в двух охладителях. Обычно сначала инструмент быстро охлаждают в воде до 350-450 °С, а затем погружают в масло до полного охлаждения. Период выдержки для инструментов средних размеров - 3-5 с. Момент переноса детали из воды в масло определяют по прекращению дрожания щипцов, которыми держат инструмент, или по исчезновению слабого звенящего звука, возникающего в результате интенсивного кипения воды вокруг детали, или по потемнению детали. Разновидность этого способа - закалка путем многократного погружения инструмента в воду с промежуточными выдержками (несколько секунд) на воздухе. Таким образом можно закаливать инструменты больших размеров, в основном из углеродистой стали.
Изотермическая закалка заключается в том, что инструмент, нагретый до температуры закалки, охлаждают в закалочной среде, постоянная температура которой 250-400 °С (отсюда и название «изотермическая закалка», то есть закалка при постоянной температуре), а затем на воздухе. Обычно горячая закалочная среда - расплавленная селитра KNO3 или нагретое до 150-180 °С минеральное масло. Изотермическая закалка позволяет резко понизить внутренние напряжения, а также риск коробления и образования трещин. Достоинством этого способа также является возможность рихтовки (корректировки незначительного коробления) инструмента сразу после его выгрузки из охлаждающей среды, так как температура инструмента в этот момент достигает нескольких сотен градусов и некоторое время он сохраняет пластичность. Применяется этот способ для инструментов, от которых требуются высокие твердость и вязкость, особенно важные для дереворежущих инструментов с малыми углами заточки (например, для корпусов алмазного инструмента).
Закалка с самоотпуском характеризуется тем, что процесс происходит в ходе нагрева инструмента. Инструмент, нагретый до температуры закалки, охлаждают в воде так, чтобы он прокалился на заданную глубину (контролируется по времени в зависимости от вида стали). Дальнейшее охлаждение осуществляется на воздухе. При этом за счет внутреннего тепла нагревается охлажденная часть инструмента под отпуск. При достижении требуемой под отпуск температуры (ее обычно определяют по цветам побежалости, появляющимся на зачищенной поверхности инструмента) инструмент опять погружают в воду до полного охлаждения. При изготовлении высококачественного инструмента, например круглых пил, которые эксплуатируются при скорости подачи свыше 100 м/мин., производители часто применяют несколько видов закалки.
Отпуск. Этот процесс заключается в нагревании закаленной стали до температуры ниже фазовых превращений, в результате чего характеристики стали приближаются к равновесному состоянию. За счет вызова распада мартенсита закалки на ферритоцементитную смесь при отпуске снижаются остаточные напряжения и повышается пластичность стали наряду с некоторым снижением твердости.
Отпуск стали выполняют сразу же после закалки. Чем выше температура отпуска, тем ниже твердость стали.
Низкий отпуск выполняется при 150-300 °С, твердость и внутренние напряжения стали снижаются незначительно. Низкий отпуск в термообработке режущего инструмента применяют в тех случаях, когда требуется высокая твердость (59-60 HRC), например, при изготовлении ножей лущильных и рубительных машин, некоторых ножевых валов и головок. Отпуск при более низкой температуре (120-150 °С) называют старением.
Средний отпуск выполняется при 300-500 °С. При такой температуре внутренние напряжения и твердость инструмента заметно снижаются, а пластичность повышается. Применяется средний отпуск для инструментов, требующих значительной прочности и упругости при твердости 45-50 HRC (например, для инструментов, работающих при ударной нагрузке: пил для раскроя мороженой древесины, стандартных ножей и фрез для продольно-фрезерных станков).
Высокий отпуск выполняется при 500-600 °С. Твердость стали снижается до 30-35 HRС. При высоком отпуске избегают посадки инструмента в печь с высокой температурой, так как закаленный инструмент при быстром нагреве может растрескаться. Высокий отпуск выполняют, например, на зубчатых венцах круглых пил, предназначенных для работы при скорости подачи более 50 м/мин. В зависимости от того, какой температуры нужно достичь, инструмент при отпуске нагревают в масляных или селитровых ваннах. Выдержка при температуре отпуска зависит от диаметра или толщины изделия: при толщине до 20 мм она составляет 1 ч, а при толщине 20-40 мм - 1,5-2 ч. После отпуска инструмент обычно охлаждают на воздухе.
Применение на заводах (как правило, небольших) одного и того же вида отжига, нормализации, закалки и отпуска для разных режущих инструментов (пил, ножей, фрез), предназначенных для обработки разных материалов (плит, древесины и композитных материалов), может привести к снижению стойкости инструмента, а также к его полному или частичному разрушению в процессе работы.
При появлении проблем в процессе эксплуатации инструмента необходимо выявить их причины и понять, как их избежать в дальнейшем. Очень важно проверить твердость стали как корпуса, так и режущих элементов - зубьев (резцов) дереворежущего инструмента. Зная основные правила конструирования инструмента и его требуемую твердость по результатам замеров на производстве у покупателей инструмента, можно сделать выводы и выработать необходимые рекомендации.
Рекомендуемые границы твердости при изготовлении режущего инструмента из инструментальной стали, а также корпусов, оснащенных пластинками твердого сплава:
- низкая твердость - 40-47 HRС (для пил, подверженных пластической деформации: разводу, плющению, для корпусов пил, оснащенных твердым сплавом);
- средняя твердость - 52-57 HRC (для инструмента небольших размеров, например концевого: сверл, фрез, как правило, до 15 мм диаметром);
- высокая твердость - 57-61 HRC (для насадных фрез и ножей, включая те, на которые напаян твердый сплав).
Оборудование для измерения твердости сталей
тарированных напильников
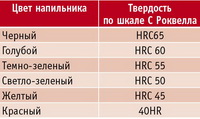
Есть три способа измерения твердости сталей при механических испытаниях: упругого отскока; вдавливания (внедрения); царапания.
В производстве режущего инструмента используется множество разных металлов и их сплавов с разнообразными механическими свойствами. В настоящее время существует около трех десятков методов испытания твердости, относящихся к перечисленным выше способам измерения твердости, причем каждый имеет вполне определенную область применения. Можно выделить несколько наиболее распространенных методов, основанных на одних и тех же принципах.
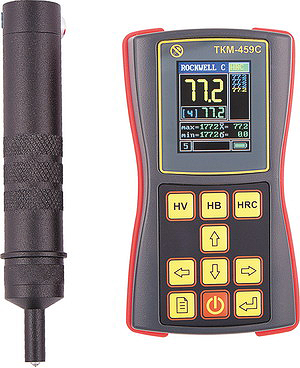
Рис. 2. Переносной твердомер
Под твердостью материала понимают его способность сопротивляться пластической или упругой деформации при внедрении в него более твердого тела (индентора).
Этот вид измерений твердости не связан с разрушением металла и, кроме того, в большинстве случаев не требует приготовления специальных образцов.
Все методы измерения твердости можно разделить на две группы в зависимости от вида движения наконечника (индентора): статические и динамические. Наибольшее распространение получили статические методы определения твердости.
Статическим методом измерения твердости называется такой способ, при котором индентор медленно и непрерывно вдавливается в испытуемый металл с определенным усилием. К статическим методам относят измерение твердости по Бринеллю, Роквеллу и Виккерсу.
При динамическом испытании контролируется величина отскока испытательного инструмента от поверхности испытываемого образца. К динамическим методам относят определение твердости по Шору и Польди.
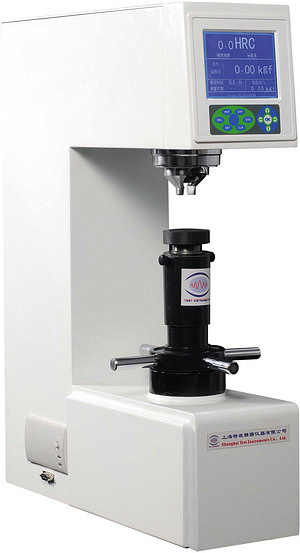
Рис. 3. Стационарный твердомер
Твердомеры бывают стационарные и переносные. В инструментальной промышленности России наибольшее распространение получили несколько методов определения твердости: по Бринеллю, Роквеллу, Виккерсу, Шору, Польди и др.
В технической литературе твердость обозначается буквой Н (от англ. hardness - твердость). Следом за буквой Н всегда пишется одна или две буквы, обозначающие метод испытания твердости, например: НВ - твердость по Бринеллю; HRA, HRB, HRC - твердость по Роквеллу (по шкалам А, В и С); HV - твердость по Виккерсу; HSD - твердость по Шору; HP - твердость по Польди; Нµ - микротвердость и т. д.
В настоящее время наряду с механическими методами определения твердости стали получили распространение и другие методы, например, ультразвуковые. Твердомеры для определения твердости стали ультразвуковым методом целесообразно использовать для измерения тонкостенного режущего инструмента (толщина стали до 6 мм), например, для измерения корпусов пил, причем эти приборы можно устанавливать в труднодоступных местах, в частности на пильных шпинделях. На рис. 2 и 3 показаны переносной и стационарный твердомеры.
Стоимость стационарных твердомеров довольно высока - несколько сотен тысяч рублей, поэтому для предприятий (особенно небольших и средних) целесообразно приобретать портативный (переносной) твердомер, например универсальный. Подобный прибор (его стоимость не больше 100 тыс. руб.) позволяет с помощью динамической и ультразвуковой систем измерения определять твердость любого инструмента (от пил и ножей до насадных фрез).
Тарированные напильники
Есть и простой, дешевый и довольно надежный метод измерения твердости корпуса инструмента - с использованием так называемых тарированных напильников.
Тарированные напильники предназначены для качественного определения твердости закаленных деталей инструмента и стальных корпусов режущего инструмента по шкале твердости C Роквелла и шкале твердости Виккерса. Подобные напильники используются для установления, например, твердости режущих инструментов (пил, ножей и фрез, а также их зубьев и т. п.) и других объектов, твердость которых измерить иным способом невозможно. Тарированные напильники применяются, в частности, для определения твердости внутренних полостей насадных фрез и пил, концевого инструмента, краев (углов) изделий, а также межзубной впадины и зубьев пил и фрез, корпусов ножей.
Порядок работы
Начните с черного напильника (HRC65) и проведите им по контролируемой поверхности инструмента. Если на ней осталась царапина, твердость поверхности ниже HRC65. Если после проведения голубым напильником (HRC60) по поверхности инструмента на ней не осталось царапин, значит, напильник мягче поверхности и твердость поверхности изделия от HRC60 до HRC65. Если же голубой напильник оставляет царапину, используйте тёмно-зеленый (HRC55), затем светло-зелёный (HRC50) и далее, до тех пор, пока напильник не станет проскальзывать по поверхности изделий без царапин (то есть пока твердость поверхности инструмента не будет выше твердости напильника).
Качественная (приближенная) твердость поверхности инструмента находится в интервале между твердостью царапающего и проскальзывающего напильника.
В процессе эксплуатации острота зубьев тарированного напильника должна периодически проверяться аналогично проверке зубьев обычных напильников.
Не рекомендуется восстанавливать затупленные тарированные напильники химическим способом, как это делается с обычными напильниками. По мере износа тарированные напильники следует менять.
Владимир ПАДЕРИН