Современные методы упрочнения инструментальных сталей и твердого сплава при производстве дереворежущего инструмента
Надежный инструмент – прочный инструмент
В настоящей статье автор попытался обобщить информацию о перспективных методах и способах упрочнения быстрорежущей инструментальной стали (HSS) и инструмента из твердого сплава (HW), а также о перспективах развития этого направления в производстве дереворежущего инструмента в современной России.
В деревообрабатывающем производстве проблема использования новых ресурсосберегающих и экологически чистых технологий для изготовления экономичного и высокопроизводительного дереворежущего инструмента всегда актуальна. Применение подобного инструмента в деревообработке позволяет использовать интенсивные режимы резания, сократить простои станочного оборудования и расход дорогостоящих инструментальных материалов и сплавов. В настоящее время в нашей стране, как и за рубежом, ведутся активные поиски путей повышения эффективности и надежности дереворежущего инструмента, изготовленного как из обычной инструментальной быстрорежущей стали, так и из разных твердых сплавов. Одно из направлений этих исследований - применение методов, опробованных в производстве инструмента для металлообработки, в производстве дереворежущего инструмента.
К подобным методам в первую очередь относится нанесение разного рода покрытий на рабочие поверхности режущего инструмента, то есть создание модифицированных поверхностных слоев толщиной, как правило, не более 5 мкм, с высокой износостойкостью, стойкостью к химическому и электрохимическому окислению (что важно, например, при обработке влажной древесины) и многими другими улучшенными характеристиками, которые получены методами химико-термической обработки рабочей поверхности инструмента, химического и физического осаждения, а также плазменно-вакуумного осаждения.
Из вышеперечисленных методов наибольшее распространение в последние годы получили методы плазменно-вакуумного осаждения, особенно в производстве металлорежущего инструмента. Наиболее эффективными являются покрытия, формируемые карбидами и нитридами переходных металлов: титана, вольфрама и других, - а также оксидами алюминия и кремния, оксидом и нитридом бора. Исследования, проводимые разными исследовательскими институтами и лабораториями при крупнейших мировых производствах дереворежущего инструмента, показали, что не все покрытия из названных выше карбидов, нитридов и оксидов обеспечивают повышение эксплуатационных свойств режущего инструмента из-за принципиального различия в теплофизике резания древесных материалов и металлообработки. Обусловлено это не только различиями в конструктивных особенностях инструмента и технологических режимах резания (например, скорости резания и подачи), но и особенностями строения древесины (анизотропии) и древесных материалов, а также использованием в металлообработке смазочно-охлаждающих жидкостей (СОЖ), способствующих значительному съему излишнего тепла с режущих элементов инструмента и снижению износа последнего. В деревообработке (за исключением лесопиления) СОЖ в таком виде, как в металлообработке, не применяется. В лесопилении СОЖ в основном применяется в виде аэрозоли, которая подается в зону пиления и предназначена для снижения засмаливания пил при пилении древесины хвойных пород, а также для охлаждения режущих инструментов. Составы СОЖ для металлообработки и лесопиления сильно различаются.
Причины износа и затупления дереворежущего инструмента
Микрогеометрия лезвия. Лезвие любого дереворежущего инструмента при резании древесного материала под действием разных сил, в том числе трения, изнашивается.
Различают два понятия: износ лезвия и затупление лезвия и других режущих кромок инструмента. Износ - это величина, характеризующая изменение формы и размеров лезвия и режущих кромок. При изучении физической природы износа используется показатель массового износа - массы изношенной части инструмента, которая измеряется в миллиграммах. Затупление лезвия характеризуется изменением его микрогеометрии в процессе резания, причем линейные показатели износа на процесс резания не влияют, важна только микрогеометрия профиля затупившегося лезвия. Износ и затупление - это взаимообусловленные процессы.
Параметрами износа и затупления служит степень износа по задней поверхности (грани резца), по передней поверхности, по высоте лезвия, по биссектрисе угла заточки, площади износа и радиусу кривизны режущей кромки. Изменение указанных параметров в процессе резания приводит к изменению переднего и заднего углов резания. Численные значения указанных параметров затупления находятся в определенной зависимости от общего пути лезвия в обрабатываемом материале. Доминирующее влияние на динамику и качество обработки оказывает радиус закругления лезвия (режущей кромки) ρ, то есть радиус закругления окружности, условно вписанной в поверхность режущей кромки лезвия.
Численное значение радиуса закругления ρ принято считать мерой остроты лезвия. Радиус закругления острых лезвий ρ равен 4-6 мкм для фрез и 10 мкм для пил. У тупых лезвий радиус закругления 30 мкм и более.
Критерии затупления лезвия. Радиус закругления лезвия не может в полной мере характеризовать работоспособность режущего инструмента. Каждое лезвие для одних условий считается тупым, неработоспособным, а для других - достаточно острым и работоспособным. Показатели работоспособности и затупления всегда следует рассматривать во взаимосвязи с результатами работы лезвия: шероховатостью обработанной поверхности, величиной энергопотребления, производительностью и параметрами шума.
Степень затупления характеризуется максимально допустимым значением износа режущего инструмента, после достижения которого наступает его отказ, то есть неработоспособное состояние. Продолжение резания подобным лезвием приведет к недопустимым режимам резания и нарушению установленных показателей обработки материала по качеству и геометрии.
Период стойкости инструмента. Отказ режущего инструмента, то есть его неработоспособное состояние, может быть стойкостным или точностным.
Стойкостный отказ - это постепенный отказ режущего лезвийного инструмента после достижения им определенной степени затупления.
Точностный отказ - постепенный отказ режущего лезвийного инструмента после достижения размером или формой обработанной поверхности допустимого предела поля допуска обрабатываемой заготовки или детали. При наступлении отказа дереворежущий инструмент часто восстанавливают.
Восстановление - приведение рабочей части режущего лезвийного инструмента в работоспособное состояние.
Продолжительность работы инструмента характеризуется периодом стойкости. Период стойкости - это отрезок времени, затраченный на резание новым или восстановленным режущим лезвийным инструментом от начала резания до отказа инструмента.
Различают также полный период стойкости, равный сумме периодов стойкости режущего лезвийного инструмента от начала резания новым инструментом до достижения предельного состояния затупления.
Этапы износа лезвий дереворежущего инструмента
Изображение закономерности нарастания износа лезвий за время работы инструмента называется кривой износа. Кривые износа можно построить по каждому параметру износа и затупления. Форма кривых зависит от многих аспектов процесса резания древесины и древесных материалов.
Весь период стойкости режущего инструмента можно разделить на три этапа нарастания износа: приработки, монотонного износа и аварийного (катастрофического) износа. Износ лезвий на первом этапе происходит главным образом в результате изменения формы режущей кромки (обломов или отгибов) на отдельных ее участках. Сначала выкрашиваются участки лезвия с малыми размерами и глубиной, затем - с возрастанием сил резания - происходит разрушение участков режущих элементов больших размеров. Разрушение и выкрашивание лезвий продолжается до тех пор, пока прочность их сечения не будет противостоять изгибающему моменту сил резания.
Износ на втором этапе протекает в сложных условиях, когда при резании древесины одновременно проявляются несколько факторов: высокое давление, температура на поверхности лезвия 240-840°С, окисление, действие статического электричества, электрохимическая коррозия, абразивный износ (разрушение инструмента вследствие чрезмерного увеличения сил резания и температуры на лезвии) и др.
Температура на поверхности режущих элементов
При резании древесины в результате трения и деформирования контактных поверхностей инструмента и обрабатываемого материала выделяется тепло и лезвия режущего инструмента нагреваются. Интенсивность их нагрева возрастает с увеличением радиуса закругления режущих кромок. Образовавшееся тепло локализуется в малом объеме лезвия. Температура нагрева по мере удаления от режущей кромки снижается. Действие температуры на лезвие внешне проявляется в образовании на нем тонких окисных пленок разных цветов, так называемых цветов побежалости. Температура на лезвиях зубьев дисковых пил и насадных фрез достигает 700-850°С, на зубьях концевых фрез - 700-800°С.
Физическая сущность износа режущего инструмента
Механическое диспергирование - истирание, отделение мелких частиц металла лезвия от тела лезвия является основной причиной монотонного износа. Интенсивность истирания зависит от величины сил трения при резании. Механическое диспергирование можно объяснить также и усталостью металла инструмента при многократной нагрузке лезвия силами резания. Различают несколько видов износа дереворежущего инструмента, проявляющихся в процессе резания.
Тепловой износ. Высокая температура, возникающая в поверхностных слоях лезвия, приводит к снижению прочности металла. Металл тонкого поверхностного слоя размягчается и «размазывается», в слоях глубиной 2-3 мкм изменяется структура металла. В результате подобных преобразований понижается прочность и твердость металла режущего инструмента. Износ на микроучастках лезвия происходит в результате постоянного образования и износа текучего пластического поверхностного слоя инструмента. Микроподвижность поверхностных слоев материала режущего инструмента из инструментальной стали весьма значительна, и древесина при резании как бы «размазывает» новую поверхностную структуру металла, в результате чего на передней поверхности лезвия иногда образуется лунка, а на задней - наплыв металла. Износ твердосплавного инструмента несколько отличается от износа инструмента из стали.
Окислительный износ. Окислительный износ металла лезвия при резании протекает при сложном сочетании адсорбции кислорода на поверхности трения, диффузии кислорода в поверхностные слои и пластического течения слоев металла с образованием химических адсорбированных пленок твердых растворов и химических соединений металла с кислородом. Пластические деформации тонких слоев металла режущего инструмента, вызванные его нагревом, создают благоприятные условия для диффузии кислорода в металл и образования пленок. Наиболее вязкоподвижная часть продуктов деформации «размазывается» по лезвию с образованием наплывов.
Электрохимическая коррозия. При резании в результате трения, а также пьезоэлектрического эффекта при деформировании древесины на лезвии и в стружке образуются электрические заряды. Если древесина сырая, то органические кислоты и влага образуют электролит, который при совместном действии с электрическими зарядами поражает металл лезвия электрохимической коррозией.
Электрическая коррозия. Статическое электричество, возникающее при резании в результате трения лезвия о древесину, может привести к возникновению искровых разрядов и электролитному разрушению поверхности металла. На поверхности лезвия образуются кратеры от искровых разрядов.
Абразивный износ. Под абразивным износом принято понимать процесс интенсивного разрушения поверхности лезвия при трении скольжения, обусловленный абразивной средой и выражающийся в местной пластической деформации. Абразивный износ лезвий инструмента наблюдается чаще всего при обработке клееных древесных материалов, клеевые слои которых действуют на лезвие подобно абразиву, оставляя на его поверхности царапины, а также способствуют его быстрому разрушению.
Результаты исследований механизма износа дереворежущего инструмента говорят о том, что нагрев инструмента в процессе резания является одним из решающих факторов потери им работоспособности, особенно при превышении предельной температуры нагрева инструментального материала. Так, для инструмента, изготовленного из быстрорежущих сталей, эта температура, как правило, не должна превышать температуру отпуска соответствующей стали.
Типы износостойких покрытий дереворежущего инструмента
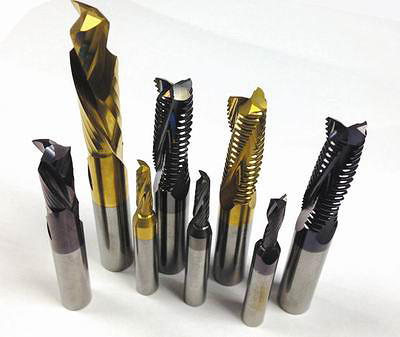
Рис. 1. Концевые твердосплавные фрезы с разными покрытиями
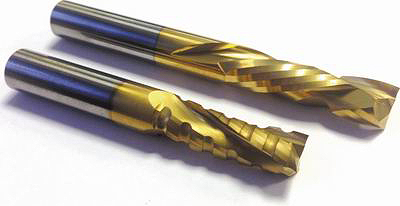
Рис. 2. Нитрид титана TiN обладает кубической (алмазоподобной)
структурой, высокой твердостью, низким коэффициентом трения, высокой
химической стойкостью

Рис. 3. Нитрид титана алюминия TiAlN довольно часто применяется в
последнее время для покрытия режущего инструмента. Инструмент с
подобным покрытием, стойким к температурному окислению,
характеризуется высокой твердостью при повышенной температуре
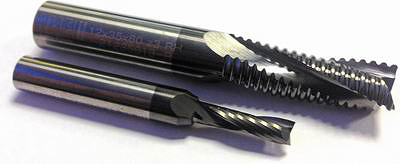
Рис. 4. Покрытие из нитрида хрома CrN высокотермостойкое и обладает
ярко выраженными антиадгезионными свойствами. Нитрид хрома CrN
используется для напыления на дереворежущий инструмент, что позволяет
в процессе резания древесины обходиться без дополнительного
охлаждения
В начале 1980-х годов начали применяться и сразу же продемонстрировали экономическую эффективность износостойкие покрытия металлообрабатывающих инструментов из нитрида титана TiN. Затем были созданы двухслойные покрытия, состоящие из последовательно нанесенных на лезвие инструмента слоев карбида титана TiC или карбонитрида титана TiCN и тонкого поверхностного слоя оксида алюминия Al2O3. Альтернативным вариантом двухслойным служили многослойные покрытия типа TiC, TiCN, TiN. Понятие «многослойные» во многих случаях весьма условно, поскольку методы напыления позволяют добиться отсутствия четко выраженных межфазных границ между слоями и между покрытием и подложкой. Многослойные износостойкие твердые покрытия обладают повышенной трещиностойкостью, улучшенной адгезией, высокой ударной прочностью, низким уровнем внутренних напряжений и напряжений на границе «покрытие - подложка» вследствие выравнивания коэффициентов термического расширения. Например, у покрытия TiCN многослойная двухфазная структура TiN-TiCN, что обеспечивает повышение прочностных и вязкостных характеристик по сравнению с покрытием TiN.
Исследования в области упрочнения дереворежущего инструмента из быстрорежущей стали и нанесения разных покрытий на лезвия за счет изменения физико-химических свойств поверхностного слоя показали, что нанесение этих покрытий должно выполняться без образования резких переходных границ между упрочненным слоем (покрытием) и материалом инструмента (подложки). Выявлено также, что достичь этого результата можно с помощью комбинированной плазменно-вакуумной обработки, включающей в себя формирование диффузионного слоя на поверхности инструмента путем ионного азотирования в плазме тлеющего разряда, а также последующее осаждение вышеперечисленных износостойких покрытий способами плазменно-вакуумного осаждения, вакуумно-дуговым разрядом, магнетронным распылением либо их сочетанием.
Было также установлено, что указанный диффузионный слой способствует сглаживанию резких границ между свойствами инструментального материала и покрытия и повышению стойкости инструмента в процессе эксплуатации.
В настоящее время ведутся разработки технологий нанесения износостойких покрытий на дереворежущие инструменты, изготовленные из быстрорежущей стали (фуговальные и профильные ножи, насадные фрезы), а также инструменты, изготовленные целиком из твердосплавных материалов (спиральные концевые фрезы, сверла, сменные пластинки и т. п.). В связи с недостаточным объемом статистических данных об экономическом эффекте этих разработок говорить об их эффективности пока рано. На рис. 1 показаны концевые твердосплавные дереворежущие инструменты с разными покрытиями.
На рис. 2, 3 и 4 представлен концевой дереворежущий инстумент с разными покрытиями и краткое описание его достоинств.
Методы формирования и нанесения износостойких покрытий
Качественные изменения в процессах изготовления режущего инструмента связаны с интенсивным развитием в конце прошлого века ионно-плазменных технологий нанесения износостойких покрытий. В числе технологий упрочнения поверхности инструмента наиболее известны два метода: химического осаждения покрытий (Chemical Vapour Deposition, CVD) и физического осаждения покрытий (Physical Vapour Deposition, PVD). В нашей стране наиболее широкое промышленное применение получили PVD-способы нанесения защитных покрытий. Дело в том, что технологии CVD предполагают использование дорогостоящих высокочистых химических реагентов (TiCl4, NH3 и т. д.) и прецизионных дозаторов химических прекурсоров, точный контроль продуктов химических реакций в рабочей камере и т. п. А нанесение PVD при помощи дугового или тлеющего разряда (магнетронa) обеспечивает большую производительность и не столь чувствительно к незначительным отклонениям технологических параметров, как метод CVD.
У каждого из названных методов физического осаждения есть свои достоинства и недостатки, поэтому широкое распространение в последнее время получили разные гибридные методы напыления. Общие требования к этим технологиям: отсутствие селективного распыления мишеней, высокая степень ионизации и управляемая энергетика потока, а также возможность ионной очистки подложки (поверхности нанесения). Многообразие применяемых сейчас способов физического осаждения износостойких покрытий укладывается в общую схему: испарение или ионное распыление титана или его сплавов, ионизация и гетерогенная реакция на поверхности инструмента атомов и ионов металла и реакционного газа (например, азота), приводящая к формированию нитридных, карбидных, карбонитридных и других покрытий. Структуру и адгезию покрытий, а также их эксплуатационные характеристики определяет целый ряд факторов: повышение степени ионизации, скорости и плотности потока напыляемых частиц, оптимизация температуры нанесения покрытий, применение ионной очистки подложки, ускоряющих напряжений (смещения) и др. Тот или иной материал покрытия (химический состав) сам по себе не может являться гарантией повышения износостойкости. Разные режимы нанесения, конфигурация технологической оснастки, проведение предварительного ионного травления или легирования и многие другие особенности определяют структуру самих покрытий и строение межфазной границы «покрытие - подложка».
Использование металлорежущего инструмента с предварительно нанесенными тонкими (1-5 мкм) износостойкими покрытиями обеспечивает повышение производительности обработки резанием на 20-200%, увеличение срока службы инструмента в 1,5-10 раз при обработке конструкционных сталей, до 4 раз - при резании коррозионностойких и жаропрочных сталей, в 1,5-2,5 раза - при обработке титановых и никелевых сплавов. Кроме того, достигается снижение расхода сложнопрофильного инструмента вследствие сокращения числа его переточек. Однако не всегда применение покрытий для режущего инструмента экономически обосновано и приводит к ожидаемому эффекту. Для того чтобы оценить целесообразность и эффективность их использования, необходимo обладать знаниeм основных принципов применения инструмента с износостойкими покрытиями. Тонкие износостойкие покрытия не могут существенно влиять на износ инструмента с невысокими механическими характеристиками. В этом случае поверхностные свойства снижаются до уровня объемных механических свойств инструмента. Другими словами, высокотвердый тонкий слой покрытия на мягкой или недостаточно прочной подложке (мягкой низкокачественной инструментальной стали) работать не будет.
Механизмы износа, при которых оправдано применение износостойких покрытий, имеют место преимущественно при высокой скорости обработки. В случае применения покрытий для инструмента с износостойкими покрытиями можно говорить о предотвращении ими окислительного изнашивания, обусловленного взаимодействием кислорода с материалом инструмента. В свою очередь, сверхтвердый алмазный инструмент, режущая оксидная керамика, кубический нитрид бора и другие используются в основном для финишной обработки или обработки плитных материалов - как правило, в этих случаях нет смысла использовать инструмент с подобными износостойкими покрытиями, так как по твердости и химической стойкости они не превосходят материал инструмента.
Износ режущего инструмента может быть снижен путем предварительного нанесения износостойких покрытий только в том случае, если изначально в технологический процесс механической обработки не заложены следующие механизмы фатального разрушения материала инструмента:
- пластическая деформация корпуса инструмента, возникающая при неправильном подборе соотношения нагрузки на инструмент и твердости материала инструмента;
- макроскалывание на лезвиях инструмента, возникающее при неправильно подобранном соотношении нагрузки и вязкости (пластичности) инструмента;
- трещинообразование и, как следствие, разрушение инструмента, возникающее в результате чрезмерной нагрузки на инструмент из-за его низкой ударной вязкости.
Эффективность применения износостойких покрытий также существенно снижается при использовании несовершенного технологического оборудования или при выборе режимов обработки, предопределяющих значительные ударные нагрузки на инструмент. К сожалению, изношенность основного технологического оборудования многих лесопильно-деревообрабатывающих и мебельных предприятий может свести достоинства инструмента с износостойкими покрытиями к минимуму.
Подготовил Владимир ПАДЕРИН