Организация производства плит ДСтП и OPB на одном комплекте оборудования
Ослабление рубля обуславливает острую актуальность проектов импортозамещения в деревообработке. Согласно прогнозу Комитета по лесам и лесной промышленности ЕЭК ООН, в России в 2016 году импорт плит OSB достигнет 620 тыс. м3, что на 120 тыс. м3 больше, чем в предыдущем году1. Объем потребления этих плит составит 1,2 млн м3, то есть собственное производство будет обеспечивать лишь половину объема рынка, а это значит, что импорт будет определять цены на рынке.
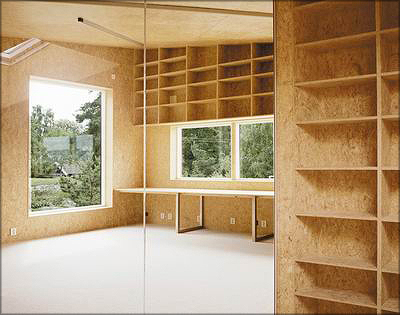
Рис. 1. Сфера применения плит OSB постоянно расширяется – сегодня они
используются и в качестве отделочного материала
В России получил распространение подход к строительству плитных предприятий, который заключается в выборе производственной линии максимальной мощности и приобретении ее целиком у одного из двух ведущих изготовителей прессов: компании Siempelkamp или Dieffenbacher. Но сегодня приобретение подобного оборудования для производства плит OSB требует не только внушительных капиталовложений, которые при нынешних курсах валют стали просто неподъемными, но и сосредоточения в одном месте значительного объема осиновой древесины. Дополнительные проблемы заключаются в ярко выраженной сезонности российского рынка строительных плит, а также в более высоких затратах на производство плит OSB в зимнее время, что связано с необходимостью содержания бассейна для пропарки мерзлой древесины. Эти факторы крайне негативно влияют на рентабельность производства плит OSB в нашей стране.
OPB толщиной 10–18 мм

В публикации, предлагаемой вниманию читателей, рассматривается альтернативный подход: создание комбинированной производственной линии, на которой в зависимости от сезонной конъюнктуры можно выпускать мебельные древесные плиты - ДСтП или конструкционные плиты OPB (от Oriented Particle Board - древесно-стружечные плиты из ориентированной стружки), которые являются полноценным аналогом плит OSB и во многих случаях весьма похожи на последние даже внешне. Отличие состоит в том, что плиты OSB получают из стрендов - длинных узких стружек, а плиты OPB - из тонких лепестковых стружек. Стренды в плитах OSB ориентированы в определенном направлении, что позволяет добиваться высоких прочностных характеристик по главной оси (см. табл. 1). При изготовлении плит OPB получается более изотропный материал, характеристики которого одинаковы в продольном и поперечном направлениях, и по свойствам он скорее близок к фанере, чем к плитам OSB. В некоторых случаях применения изотропность плит OPB может быть более ценным качеством, чем сосредоточение прочностных свойств вдоль главной оси, как в плитах OSB.
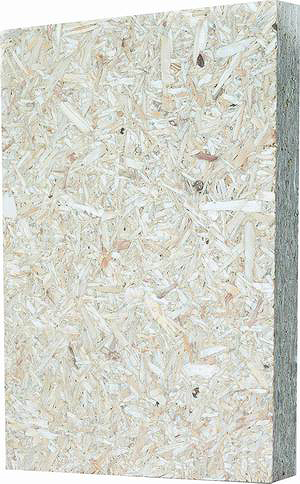
Рис. 2. Плиты германской компании Elka-Holzwerke,
которые предлагаются под маркой ESB, являются
типичным примером конструкционной древесно-
стружечной плиты OPB
Плиты OSB появились в качестве альтернативы клееной фанере как строительного материала. Одной из причин стал острый дефицит высококачественного сырья (фанерного кряжа) для производства фанеры, тогда как для большинства предприятий, выпускающих плиты OSB, сырьем служат балансы осины (85-90%), реже - низкосортная хвойная древесина. В то же время березовые балансы используются в производстве плит OSB крайне мало, поскольку при измельчении твердой древесины образуется слишком много некондиционной мелкой стружки, и выход готовой продукции из сырья падает. Даже при использовании подходящего сырья полезный выход при производстве плит OSB составляет около 65%, что, впрочем, является неплохим результатом в сравнении с фанерными предприятиями, где выход продукции из сырья обычно не превышает 50%. Однако при производстве плит OPB полезный выход достигает 80%, и это при том, что в технологическом процессе можно использовать любые породы древесины! Мелкая стружка при изготовлении плит OPB используется для внутренних слоев, и в этом одно из немногих отличий от технологического процесса производства ДСП - там из мелкой фракции формируются наружные слои.
Тем не менее по составу комплекты оборудования для выпуска ДСтП и плит OPB очень близки, что с учетом сезонности рынка этих плит наводит на мысль о создании комбинированного комплекта, позволяющего с успехом производить как ДСтП широкого диапазона толщины и плотности, так и плиты OPB разной толщины и плотности. К сожалению, такие комплекты в настоящее время не изготавливаются ни одним ведущим производителем оборудования. Однако под контролем опытных специалистов подобный комплект может быть собран из оборудования разных изготовителей. Более того, он может быть создан на базе действующего производства ДСтП.
В предлагаемом обзоре изложены принципы и пример подбора оборудования для комплекта, на котором можно выпускать плиты ДСтП и OPB.
Подготовка стружки
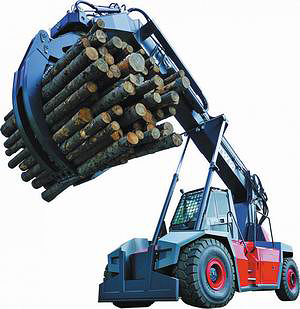
Рис. 3. Грузоподъемность некоторых машин модельного
ряда Kalmar RTD (сейчас марка KURO) достигает 31 т
Оборудование для реализации комбитехнологии (в широком понимании этим словом можно обозначать любую технологию, предполагающую комплексное использование оборудования и организацию производства древесных плит двух или нескольких типов) ничем не отличается от того оборудования, которое применяется для производства древесных плит. Однако у его сочетания в производственной линии имеется ряд особенностей, на которые стоит обратить внимание при переходе на комбитехнологию. Рассмотрим комплекс и порядок построения оборудования на производственной площадке применительно к производству ДСтП и OPB.
В состав оборудования склада технологических дров должна входить разгрузочно-погрузочная техника и узел подачи сырья в производство. Для этого подходят, например, погрузчики KURO фирмы SKS Toijala Works (известные ранее под маркой Kalmar), погрузчики модельного ряда MHL фирмы Terex Fuchs, перевалочные экскаваторы Sennebogen (при оснащении двухчелюстным грейфером). Компании Volvo и Liebherr предлагают примерно схожий набор колесных погрузчиков, включающий как традиционные машины с фронтальным захватом, способные благодаря быстросменяемому навесному оборудованию трансформироваться из лесопогрузчиков в ковшовые погрузчики, так и машины с верхним захватом: Volvo 180H High Lift и Liebherr L 580 Log Handler.
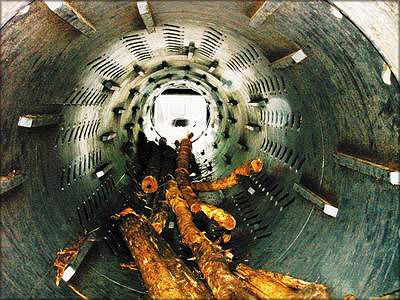
Рис. 4. Бревна внутри окорочного барабана
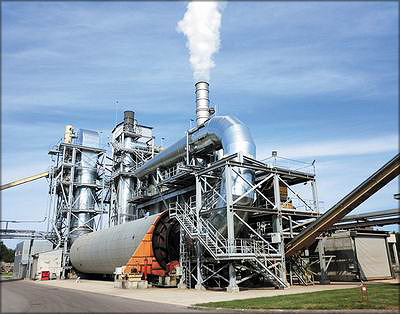
Рис. 5. Сушильный комплекс Büttner на заводе по производству ДСтП
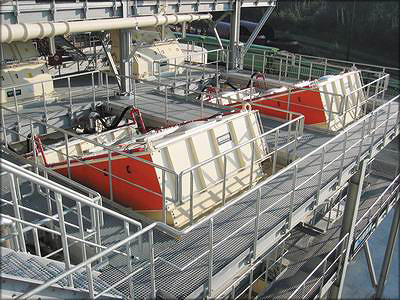
Рис. 6. Установка Quadradyn
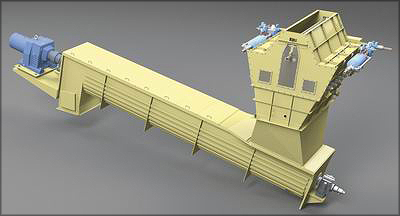
Рис. 7. Установка EcoResinator
Подготовка древесного сырья заключается в правильно организованном хранении сырья, пропаривании перед подачей на переработку в лепестковую стружку. В случае применения комбитехнологии можно отказаться от энергоемкого процесса пропарки и строительства бассейнов или камер пропарки проходного типа. Процесс пропарки, кроме того, требует сооружений и оборудования для очистки использованной воды, что тем не менее не позволяет полностью исключить негативное влияние на окружающую среду. Поэтому лучше отказаться от пропарки в холодный период и перейти на производство древесно-стружечных плит пониженной плотности. Производство же плит OPB в летний период не требует операции пропарки.
Итак, сырье поступило на склад, обработано, отсортировано, выдержано и подается на переработку.
Производство стружки необходимо начать с окорки бревен на окорочном оборудовании, в качестве которого может выступать роторный окорочный станок производства фирм Söderhamn Eriksson (марка Cambio), Valon Kone, Nicholson. При скорости подачи 120-130 м/мин. эти станки могут обеспечивать довольно большие объемы переработки даже при малом диаметре сырья.
Еще более производительным способом, обеспечивающим к тому же надежную окорку кривых и коротких бревен, является окорка в барабанах, например, серии HRE от HOMBAK.
Изготовление стружки выполняется на стружечных станках из круглых лесоматериалов, минуя стадию производства щепы. На этой операции используется станок типа HMU или HMZ фирмы Hombak. При производстве двух продуктов - ДСтП и OPB, необходима стружка с разными характеристиками. Получение стружки нужной геометрии достигается установкой на барабан ножей с требуемыми параметрами. С момента получения стружки необходимо избежать ее измельчения или повреждения. По этой причине для транспортировки стружки по всему технологическому процессу используются ленточные конвейеры. У бункеров для создания буферного технологического запаса по ходу технологического потока тоже должно быть ленточное дно, чтобы не менялась геометрия стружки. Для этого неплохо подходят бункеры типа BBSO компании IMAL или аналогичные им. В частности, неплохо зарекомендовали себя бункеры фирмы BINOS.
Полученная стружка направляется в бункер и далее дозированно подается в сушильное отделение.
Для сушки стружки может быть использована двухступенчатая сушилка, первой ступенью которой является аэрофонтанная система, а второй - трехходовой барабан. Подобное оборудование изготавливает, например, фирма Büttner Energie- und Trocknungstechnik GmbH. Также возможно использование ленточных сушилок. Известно, что в технологических дровах начальная влажность довольно нестабильна; по этой причине сырье необходимо выдерживать на складе для выравнивания влажности, что позволяет стабилизировать процесс сушки, однако при этом нельзя слишком снижать влажность исходного сырья для обеспечения хорошего стружкообразования и получения крупной плоской стружки для производства плит OPB. Равномерные начальная влажность, фракционный состав и объем стружки на входе в сушильную установку позволят стабилизировать процесс сушки и получить на выходе из сушильной установки стружку с постоянной заданной влажностью. При производстве плит пониженной плотности из лепестковой стружки допустима повышенная влажность стружки перед осмолением. Таким образом можно поднять производительность сушильной установки, если выпускать лепестковую стружку с влажностью 2,0-4,0%. Если же стружку высушить до более низкой влажности (0,5%), можно повысить степень осмоления для получения более прочной плиты, за счет чего можно улучшить физико-механические свойства плит ДСтП и OPB.
К названному выше требованию сохранения геометрических параметров стружки по ходу технологического потока здесь добавляется требование обеспечения обязательной аспирации всех ленточных и скребковых конвейеров. Конвейеры должны быть герметично закрыты и подключены к аспирационной установке, в состав которой входят трубопроводы, вентиляторы, фильтровальные установки, например фирмы Scheuch, или аналогичное оборудование, в том числе российских изготовителей (компании «Консар», «Эковент»). Для сбора пыли необходимы бункеры, например Silobin от компании IMAL. Пыль и мелкую древесную фракцию после аспирации конвейеров необходимо отправлять на сжигание или на производство продукции: пеллет, брикетов, древесно-полимерных композиционных материалов.
После сушки стружка направляется в бункеры сухой стружки, оборудованные системами пожаробезопасности и взрывоподавления, - это наиболее опасное с точки зрения взрыво- и пожароопасности место на производстве. Здесь могут быть рекомендованы уже упомянутые бункеры Silobin компании IMAL или их аналоги.
В этой точке производственный поток разделяется. Если на предыдущих операциях материал для ДСтП и OPB обрабатывался одним и тем же оборудованием, только с изменением режимов, то далее необходима небольшая специализация оборудования. После «сухих» бункеров стружка делится на два потока: первый - для производства ДСтП, второй - для производства OPB.
Поток OPB
.jpg)
Рис. 8. Формующая машина Dynaformer
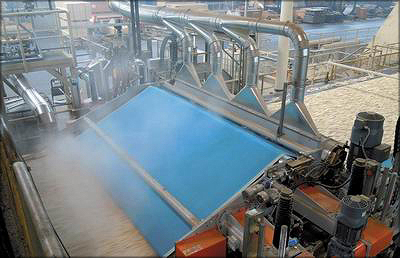
Рис. 9. Установка предварительного прогрева ковра Dynasteam
Стружка направляется в отделение сортировки, где разделяется на три фракции: крупную, мелкую и некондиционную (пылевидную). В производстве плит OPB используются только первые две фракции, причем, в отличие от производства ДСтП, где наиболее крупные фракции идут на изготовление внутренних слоев, а для наружных слоев используется мелкая фракция, в производстве OPB крупная фракция идет на наружные слои, а мелкая - на внутренние.
Разделение фракций можно осуществлять в барабанной сортировочной установке. Альтернативный подход состоит в использовании технологии дисковой сепарации, которая применяется в производстве плит OSB. Подобные установки, поставляемые, к примеру, компаниями CMC-Texpan или PAL (система Quadradyn), обращаются со стружкой очень бережно, но они значительно дороже барабанной установки.
Сухая стружка после сортировки по конвейерам поступает в бункеры, где накапливается и хранится.
Параллельно с обработкой стружки ведется приготовление клея и его компонентов в отделении приготовления и дозирования клея. В современных автоматизированных системах дозирования для каждого химического компонента выделена отдельная линия, состоящая из насоса, расходомера и промежуточного накопительного бака. Наиболее очевидным достоинством такой конфигурации является возможность изменения химического состава клеевой смеси в процессе производства и немедленной проверки оказываемого эффекта, что позволяет оперативно решать проблемы качества плиты или перенастраивать производство на другую продукцию. При каждой смене продукции система дозирования быстро адаптирует химические формулы клеевой смеси к заданным параметрам, подавая нужное количество компонентов в смеситель для выбранного типа производства. При использовании же традиционной системы баков, прежде чем увидеть результаты изменений, внесенных в химическую формулу, необходимо дождаться, пока клеевая смесь полностью не закончится, что затрудняет оперативный контроль качества продукции и ведет к производственным потерям. Система приготовления клеевой смеси партиями, кроме того, не позволяет быстро перенастраивать производственную линию на выпуск другого вида продукции.
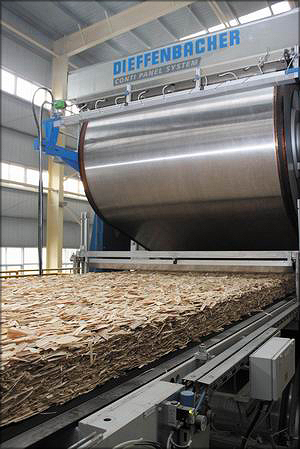
Рис. 10. Стружечный ковер на входе в пресс
Dieffenbacher CPS
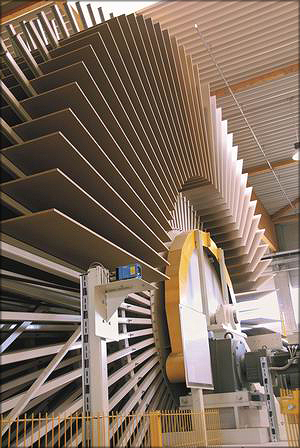
Рис. 11. Веерный охладитель на предприятии компании
Egger
Процесс смешивания стружки со смолой и парафином контролируется самым тщательным образом. В производстве OPB для внутреннего и внешнего слоев используют один тип смол, но с разной концентрацией и рецептурой клея.
В общих чертах смеситель для стружки наружного слоя представляет собой цилиндрический барабан, который вращается с заданной скоростью. Внутрь барабана по отдельным трубопроводам подаются парафин, смола и другие компоненты клея. Атомайзеры (распылители), расположенные в пространстве барабана в определенном порядке, позволяют вносить и равномерно распределять компоненты по всему объему смеси. Парафин, сырой или эмульгированный, вводится исключительно перед вводом смолы. Все эти решения реализованы в смесительных барабанных установках фирмы COEL (Канада). Есть и альтернативное решение, предлагаемое ведущими изготовителями оборудования: нанесение клея форсуночными распылителями при поступлении стружки в смесительный барабан. Фирма IMAL изготавливает подобные установки под маркой Hi-Jet (в общей сложности на плитные производства во всем мире уже поставлено 87 подобных систем). Форсуночные распылители здесь объединены в сменные кассеты. Основной процесс нанесения клея протекает в клеевой воронке над смесителем: стружки обволакиваются смесью, проходя сквозь мелкодисперсный туман, создаваемый форсунками. В самом смесителе, оснащенном лишь смесительным валом, происходит стабилизация смеси. Аналогичное решение компания Dieffenbacher предлагает под маркой EVOjet P, а компания Siempelkamp - под маркой EcoResinator P. У установок есть ряд важных различий, рассмотрение которых может быть темой для отдельной статьи, но все три названных изготовителя заявляют о существенном сокращении расхода клея и минимизации воздействия на стружку при названном способе смешивания. Отмечаются также сокращение износа смесительного оборудования и абсолютная пожаробезопасность процесса.
Нанесение связующего на стружки внутреннего слоя может осуществляться любым высокоскоростным смесителем. На этой же установке при производстве плит ДСтП выполняется осмоление стружек внутреннего слоя.
После осмоления стружка наружных слоев по ленточному конвейеру с аспирацией поступает в бункеры-дозаторы крайних механических формующих машин, а осмоленные стружки внутреннего слоя по ленточному конвейеру - в бункер-дозатор внутренней механической формирующей машины. Для этой операции могут быть рекомендованы формующие машины Dynaformer компании IMAL или аналогичные установки от компаний Dieffenbacher и Siempelkamp.
Формашины Dynaformer для наружных слоев OPB работают следующим образом. Материал из бункера формашины через загрузочную воронку самотеком падает вниз, проходя через центральное устройство с гребенчатыми вальцами. Благодаря конструкции и непрерывному вращению вальцы выполняют функцию распределения и сепарации материала мелких размеров, который проходит через них и попадает дальше в основной механизм, в то время как более крупные фракции стружки отбрасываются в переднюю часть формашины. Отсортированный таким образом материал попадает в нижнюю часть, состоящую из вращающихся зубчатых дисков. Они формируют однородный слой стружки. Головка формашины автоматически регулируется по высоте и наклону насыпки на ленту формирующего конвейера. Те частицы материала, которые не прошли через серию зубчатых дисков, собираются и извлекаются ленточным конвейером. В формашине предусмотрена система регулировки ширины насыпки ковра. В бункере установлен специальный весовой мост для определения веса и плотности материала в режиме реального времени внутри головки, гарантирующий тем самым точность насыпки. Ряд специальных датчиков позволяет постоянно поддерживать бункер полным.
В формашине для внутреннего слоя OPB сортировка стружек осуществляется рядом лопастей и вращающихся гребенчатых валов. Отсортированная стружка падает на механизм основания, состоящий из серии лопастей и ребристых валов; последние упорядочивают слои стружки, укладывая их на ленту конвейера.
Формирующий конвейер монтируется в зависимости от необходимости и желания его комплектации узлами и машинами по транспортировке и параллельной обработке настеленного ковра. В необходимой комплектации формирующий конвейер должен включать в себя:
- устройство контроля плотности и веса ковра по ширине (например, рентгеновский плотномер ковра ISO30X компании IMAL);
- устройство контроля влажности ковра;
- устройства поиска металлических включений;
- систему предварительной подпрессовки (лучший вариант - подпрессовщик Siempelkamp);
- устройство обрезки продольных кромок;
- систему увлажнения наружной поверхности ковра (например, систему увлажнения ковра TS100 компании IMAL);
- установку предварительного прогрева ковра (например, паровую установку Steam Booster или Dynasteam компании IMAL);
- систему удаления ошибочной насыпки;
- очистительные и аспирационные системы.
Прессование плит целесообразно выполнять на прессах проходного типа (лучше не каландровых), например HDKR4200 или более современных прессах фирм Siempelkamp, Dieffenbacher и IMAL. В конструкцию пресса IMAL включена установка парового прогрева ковра.
Типовой набор оборудования для послепрессовой обработки:
- система разгрузки пресса;
- установки контроля толщины и плотности (например, установка FBC100 компании IMAL);
- установки удаления бракованной плиты;
- установки охлаждения (веерный охладитель);
- установки обрезки и раскроя готовой плиты;
- установка штабелирования и транспортировки пачек готовой продукции.
Готовая плита OPB может быть обработана на линии шлифования или же поставлена покупателю нешлифованной.
Поток ДСтП
Стружка направляется в отделение сортировки, где разделяется на три фракции: крупную, мелкую и некондиционную, удаляемую - самую мелкую фракцию и пыль. Причем, в отличие от производства плит OPB, крупные фракции идут на изготовление внутреннего слоя, а для производства наружных слоев используется мелкая фракция. Выполняется эта операция на дисковой установке сортировки, например Dynascreen компании IMAL. Сухая стружка после сортировки по конвейерам поступает в бункеры для накопления и хранения.
Параллельно с обработкой стружки ведется приготовление клея и его компонентов в отделении приготовления и дозирования клея.
Процесс смешивания стружки со смолой и парафиновой эмульсией проходит в двух смесителях. В общих чертах скоростной смеситель для стружек наружного слоя представляет собой цилиндрический барабан, в котором вращается ротор с установленными на нем билами. В остальном конструкция смесителя схожа с конструкцией барабанной установки в потоке OPB. И точно так же, как в технологии производства плит ОРВ, для внутреннего и внешнего слоев используют один тип смол, но с разной концентрацией и рецептурой клея. Нанесение связующего на стружки внутреннего слоя осуществляется в том же смесителе, который используется для осмоления внутреннего слоя стружки при производстве OPB.
После осмоления стружка для наружных слоев по ленточному конвейеру, оснащенному аспирацией, поступает в бункеры-дозаторы крайних механических формующих машин, а стружка для внутреннего слоя - в бункер-дозатор внутренней механической формующей машины по ленточному конвейеру. Формирование трехслойного ковра выполняется на той же формующей машине Dynaformer компании IMAL, что и формирование ковра для производства плит OPB.
Формирующий конвейер для производства плит ДСтП используется в той же конфигурации, что и для плит OPB.
Прессование плит ДСтП осуществляется на том же оборудовании, что и прессование плит OPB. При производстве плит ДСтП пониженной плотности из лепестковой стружки целесообразно одновременно выполнять отделку (ламинирование).
Прессование древесных плит с одновременной отделкой декоративными бумагами, пропитанными меламиновыми смолами, известно с 60-х годов прошлого века. Наиболее широко этот способ отделки применялся при работе на комплектах оборудования BISON, выполненных на базе каландровых прессов, которые были поставлены в СССР в 1980-е годы.
Выполнение ламинирования одновременно с прессованием имеет массу достоинств: экономятся как капитальные затраты и трудозатраты за счет исключения из производственного процесса отдельного участка ламинирования, так и затраты материала и энергии за счет исключения из технологического процесса промежуточной операции шлифования.
Особенностями производства плит с одновременной отделкой являются: во-первых, необходимость использования для основы плит с пониженной плотностью из окоренного сырья с мелким волокном (микростружкой), а во-вторых, необходимость использования пропитанной декоративной бумаги плотностью не выше 80 г/м2, то есть также пониженной плотности. Эти ограничения возникают из-за необходимости организации облегченного удаления парогазовой смеси при прессовании. Кроме того, режим прессования плит из микростружки пониженной плотности близок по параметрам режиму ламинирования.
Следует заметить, что плиты из микростружки пониженной плотностью отнюдь не уступают по своим потребительским свойствам обычным плитам ДСтП. Наоборот, производство плит с пониженной плотностью предполагает пониженный расход материалов, в том числе клеевых, а значит и невысокое содержание свободного формальдегида. Кроме того, мебель из подобных плит при прочих равных условиях значительно легче, чем из других плит, что также можно считать достоинством. Прессование с одновременной отделкой может быть осуществлено на любых прессах проходного типа путем дооборудования этих линий узлом наложения бумаги. Для отделки используется рулонная бумага, ширина которой соответствует ширине прессования древесных плит с технологическими припусками.
Послепрессовая обработка готовых плит также выполняется на оборудовании, которое используется для аналогичной обработки плит OPB.
Готовая плита ДСтП может быть обработана на линии шлифования, разумеется, если на основной линии не было выполнено одновременно ламинирование и прессование.
Заключение
Технология выпуска ДСтП и OPB на одной производственной линии отлично подходит для регионов с суровым климатом (а таковыми являются почти все лесоизбыточные регионы России) и с ярко выраженной сезонностью на рынках плит. Подобная технология позволяет предприятию эффективно использовать свои производственные мощности и не зависеть от конъюнктуры на одном из рынков. Описанное выше оснащение комбилинии позволяет выпускать такой перспективный продукт, как плиты ДСтП пониженной плотности.
В настоящее время поставку комплектов, работающих по комбитехнологии, активно предлагает только инжиниринговая компания BINOS. Однако ничто не мешает приобрести оборудование для такого комплекта по отдельности у разных изготовителей. Составить из этого оборудования автоматизированную линию помогут специалисты инжиниринговой компании «Вк-инжениринг».
С целью сокращения капитальных затрат удачным решением могла бы стать глубокая реконструкция отечественных цехов с линиями стружечных плит проектов ПИ2 вместо строительства нового производства.
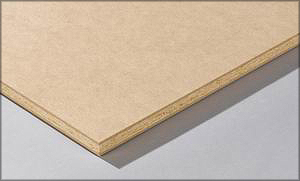
Рис. 12. Плита Egger OSB Combiline
В настоящей статье рассмотрен вариант производства на одной линии плит ДСтП и OPB. Однако есть и другие комбинации древесных плит. К примеру, австрийская компания Egger выпускает плиты Combiline, представляющие собой комбинацию плиты OSB в качестве армирующей основы и плиты MDF в качестве наружных слоев. В результате обеспечивается сочетание высокой прочности с характерным для плит MDF разнообразием способов отделки и дополнительной обработки (например, фрезерованием на небольшую глубину). В плитах Combiline тонкие плиты MDF, вероятно, просто наклеены на плиту OSB, однако надо отметить, что получение такой комбиплиты за один цикл прессования даст существенное сокращение затрат и позволит предложить рынку продукт с отличным соотношением цены и качества.
В числе примеров других комбинаций можно назвать волокнисто-стружечные плиты, волокнисто-фанерные и стружечно-фанерные сэндвичи и т. п.
Прессование древесных плит с одновременной отделкой декоративными бумагами целесообразно при применении в качестве основы так называемых легких ДСтП или MDF, то есть плит пониженной плотности. При этом себестоимость плиты существенно падает, так как не требуется шлифовка, и часть древесной пыли с максимальным содержанием клея не идет в отходы, а сокращаются выбросы в атмосферу вредных веществ, образующихся при сжигании этой пыли. Одновременно благодаря отсутствию операции шлифовки на 3,5% повышается производительность линии и существенно сокращаются расходы на оборудование для ламинирования, поскольку не требуется приобретать отдельную линию ламинирования.
Разумеется, каждый комплект оборудования комбитехнологий целесообразно проектировать на основе данных о доступной сырьевой базе и с учетом других условий строительства. Кроме того, необходимо опираться на результаты исследования рынка и долгосрочную маркетинговую стратегию предприятия.
Михаил УШАКОВ, генеральный директор ООО «ВК-инжениринг»
Владимир ВАСИЛЬЕВ, технический директор ООО «ВК-инжениринг»
Вячеслав КРИВЧИКОВ, главный инженер ООО «ВК-инжениринг»
Артем ЛУКИЧЕВ, эксперт в области деревообработки