Андрей Степанов: «Мы пытаемся сломать стереотип ущербности российского машиностроения»
Несмотря на кризисные явления в экономике страны, проектирование и строительство заводов по переработке древесины не теряет своей актуальности. Более 18 лет на российском рынке работает компания «Древмаш-Евразия» (г. Вологда), которая оказывает отечественным деревообработчикам полный перечень услуг по строительству линий лесопиления, изготовления клееных деревянных конструкций и плит OSB. Компания комплектует линии станками собственного производства, а также сотрудничает с иностранными производителями. О подробностях реализации проектов компании рассказал ее представитель Андрей Степанов.
- Расскажите, пожалуйста, почему вы решили создать собственное предприятие, которое занимается проектированием, производством и монтажом линий по переработке древесины.
- Наша компания была создана с целью поддержать отечественных машиностроителей и составить конкуренцию зарубежным станкостроителям. Генеральный директор компании Давид Хачиров является главным конструктором и идеологом всех технологических решений. Вся его трудовая деятельность связана с деревообработкой: защитил диплом в вузе на тему «Несущие деревянные конструкции», длительное время работал в Вологде на крупном деревообрабатывающем предприятии технологом, конструктором и, впоследствии, главным конструктором.
В конце 1990-х годов в Вологде работали несколько крупных станкостроительных заводов, на которых трудились высококвалифицированные специалисты. Но в силу сложной ситуации в стране в тот период профессионалы стали невостребованными на собственных предприятиях. Отрасль станкостроения для деревообработки в целом приходила в упадок. Крупные заводы были неконкурентоспособны. Они выпускали продукцию низкого качества. Новых разработок не было. Опытные сотрудники этих заводов либо уходили в частный бизнес, либо меняли сферу деятельности. Поэтому было принято решение создать в Вологде новое предприятие по производству современного конкурентоспособного оборудования.
- «Древмаш-Евразия» начала работать с 1998 года. Сколько технологических линий специалисты вашей компании спроектировали, разработали и смонтировали за 18 лет работы?
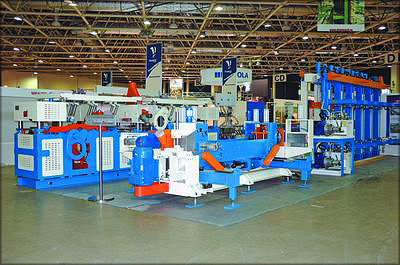
На выставке «Лесдревмаш-2008»
- В первое время компания занималась производством отдельных единиц оборудования, комплектов пристаночной механизации. Но скоро стало понятно, что наш потенциал гораздо больше, да и заказчикам нужны законченные технологические решения, а не набор станков. Довольно крупными проектами компания занималась в последние десять лет. В этот период были спроектированы, изготовлены и введены в эксплуатацию более десяти автоматических высокопроизводительных линий по выпуску клееных деревянных конструкций, которые успешно работают и в настоящее время. В последние два года разработаны и смонтированы две высокопроизводительные лесопильные линии, не уступающие по техническим возможностям европейским аналогам. До недавнего времени все наши заказчики были сосредоточены в центральной части России (Московская и Вологодская области, Республика Карелия, Пермский край). А с 2015 года мы начали более активно представлять нашу продукцию на Урале и в Сибири. В настоящий момент производится технологическая линия для заказчика из Хакасии.
- Какое оборудование было разработано для ваших первых заказчиков?
- Первыми нашими разработками стали линии для производства клееных деревянных конструкций. Это были линии по изготовлению клееного стенового бруса и деревянных несущих балок. В конце 1990-х годов в нашей стране отрасли, выпускающей «тяжелые» станки для производства КДК, не было. На рынке были только европейское оборудование и значительно уступающие ему по качеству, техническим возможностям и уровню исполнения отечественные разработки новых небольших российских предприятий.
- Назовите, пожалуйста, основные достоинства оборудования, которое изготавливает ваша компания.
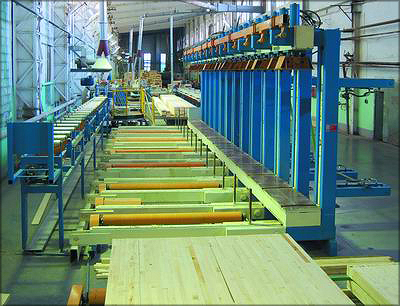
Вертикальный пресс с механизмом загрузки
- В течение всего времени существования нашего предприятия мы пытаемся своими разработками высококачественных станков и технологий сломать стереотип ущербности российского машиностроения. И я считаю, что делаем это вполне успешно. Для изготовления нашего оборудования используются лучшие импортные комплектующие для оснащения ответственных и наиболее подверженных износу узлов. Мы принципиально не применяем узлов и комплектующих китайского производства. Цена оборудования ниже импортных аналогов за счет использования отечественного металла, отсутствия затрат на дорогостоящую перевозку тяжелого оборудования. Хоть в конструкциях и есть импортные комплектующие, цены на нашу продукцию гораздо меньше подвержены колебаниям курсов валют, чем импортные аналоги. Технологические возможности нашего производства позволяют изготавливать оборудование на самом высоком технологическом уровне. Наше предприятие оснащено несколькими станками, которыми не располагает ни одно станкостроительное предприятие деревообрабатывающей отрасли страны. В настоящий момент ведется закупка нового оборудования для максимальной локализации производства. У некоторых разработок нашего предприятия нет аналогов ни в России, ни в мире. Мы всегда следим за мировыми тенденциями в станкостроении и стараемся всегда быть на шаг впереди конкурентов.
- У вашей компании есть разработки, защищенные в 2007-2008 годах патентами. Например, вертикальный пресс для клееных деревянных изделий, модульный четырехсторонний станок, устройство для формирования штабелей и пакетов пиломатериалов. Расскажите, пожалуйста, какое оборудование было разработано после 2008 года.
- В реалиях России патентование новых разработок теряет всякий смысл. Каждый может начать выпускать аналогичное оборудование, несущественно изменив конструкцию, и это будет вполне законно. Подобная история произошла с патентом на вертикальный пресс с механизмом загрузки заготовок. Мы первые в мире изготовили и показали на выставке «ЛесДревМаш-2008» это оборудование. Суть изобретения заключается в полной механизации процесса загрузки-выгрузки прессуемых пакетов и настройки пресса на требуемые размеры бруса, а также, в значительном увеличении усилия на выравнивающих боковых упорах за счет специальной конструкции замкового механизма (что обеспечивает экономию материала до 15% при дальнейшей обработке). Спустя некоторое время аналогичные прессы с незначительными изменениями появились как минимум у трех крупных российских производителей оборудования для изготовления клееных деревянных изделий и даже у европейских компаний, которые на выставке с большим интересом подробно изучали конструкцию нашего пресса.
Конечно, и после 2008 года мы подготовили множество эксклюзивных разработок. Патентовать их не стали по указанным выше причинам. В числе последних наших разработок автоматический фрезерно-брусующий лесопильный комплекс без кантования бревна, стружечный и окорочный станок барабанного типа для линий по производству плит OSB.
- В 2014 году на вашем предприятии началось строительство нового цеха площадью 4800 м2 для увеличения производственных мощностей в связи с растущим спросом на оборудование. Завершено ли строительство? Какое оборудование сейчас пользуется повышенным спросом: для лесопиления, изготовления КДК или плит OSB?
- Новый цех еще строится - процесс затянулся в связи модернизацией и дооснащением имеющегося производства. С повышением курсов мировых валют в настоящее время вырос спрос на всю нашу производственную программу. Повышенный интерес заказчиков проявляется к технологическим линиям по выпуску ориентировано-стружечных плит, аналогов которым в России не производит никто кроме нас. Немалую роль в росте спроса на оборудование для производства плит OSB играет постоянно растущий спрос в России на этот вид продукции, сокращение объемов деловой древесины в нашей стране, ужесточение законодательства в сфере лесопользования и контроля оборота лесов.
Сейчас в Вологде на нашем предприятии идет процесс изготовления оборудования для завода по выпуску плит OSB в г. Соликамске (Пермский край). Работы по монтажу линии на производственной площадке в Соликамске начались в январе 2016 года. Их планируется завершить уже к осени. Предположительно с ноября 2016 года завод начнет отгружать плиты заказчикам.
- Ваша компания не раз принимала участие в крупной выставке «Лесдревмаш», которая проходит в Москве каждые два года. По вашему мнению, что изменилось за последние пять-шесть лет в отечественном машиностроении?
- За последние несколько лет поменялась система продаж оборудования. Если раньше основной объем реализуемого оборудования осуществлялся через станкоторговые компании, то сейчас выходит на первый план сам производитель. Связано это с несколькими причинами: повсеместным развитием интернета, отсутствием у посредников должной квалификации и информации о характеристиках продаваемого оборудования, стремлением конечных потребителей и производителей исключить посредников из цепочки.
Качество, уровень исполнения и технические решения выпускаемого заводами оборудования растут. Производители все больше дорожат своей репутацией. Непростая экономическая ситуация, которая отражается на работе деревообрабатывающей отрасли, повлияла на число производителей оборудования. Многие «гаражные» компании не смогли работать дальше в непростых условиях. Станкостроительным предприятиям приходится бороться за своих клиентов: повышать качество выпускаемого оборудования, снижать цену на него, расширять номенклатуру продукции.
- Приходят ли в вашу компанию запросы на реконструкцию существующих производств? Если да, то каких?
- Если говорить о частичной замене оборудования в существующих технологических линиях, то таких обращений немного. Процесс внедрения какого-либо станка в имеющуюся технологическую линию (особенно автоматическую) довольно сложен. Если линия представляет собой единое целое, то износ всего оборудования примерно одинаков, и когда ресурс вырабатывается на 100%, то правильнее всего заменить весь комплекс, а это уже трудно назвать реконструкцией. Поставкой полного комплекта оборудования, связанного в единую технологическую линию, и занимается наше предприятие.
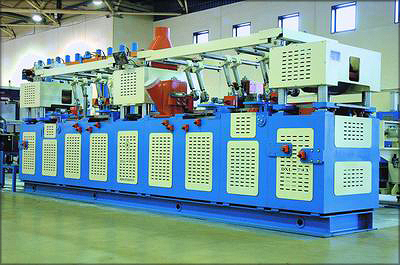
Четырехсторонний тяжелый строгальный станок
- В компоновке линий, например для производства плит OSB, вы используете электрооборудование, автоматику, высокоточные механизмы европейского производства (компаний Швеции, Германии, Италии). Правильно ли я понимаю, что в изготовлении станка, который будет устанавливаться в линию, используются только детали иностранных производителей?
- Наиболее ответственные узлы, обеспечивающие бесперебойность работы всей линии в целом, мы комплектуем только импортными частями и узлами известных европейских производителей. Хоть это и приводит к удорожанию оборудования, зато гарантирует минимум простоев по причине выхода из строя того или иного узла и, как следствие, отсутствие финансовых потерь, связанных с остановкой производства. Надежность отдельных узлов особенно актуальна в поточных автоматических линиях, когда по причине выхода из строя небольшой детали останавливается весь производственный процесс. Отечественные комплектующие мы применяем только в тех случаях, если гарантирована их надежность и безотказность или если при их поломке можно, не останавливая основной производственный процесс, выполнить ремонт в максимально короткие сроки. Мы не стремимся минимизировать число импортных или отечественных комплектующих, а подбираем оптимальное решение, обеспечивающее максимальную надежность и ремонтопригодность оборудования.
- В каких случаях вы комплектуете технологические линии готовым оборудованием иностранного производства (Sоderhamn Eriksson, Pessa impianti srl, Pagnoni Impianti srl, Instalmec srl)? Это стандартное оборудование, или выше названные компании изготавливают машины с учетом запросов и требований ваших заказчиков?
- Оборудование иностранного производства, в том числе перечисленных компаний, мы используем, если заказчик настаивает на применении в технологической линии именно этого оборудования или если в нашей производственной программе отсутствует нужная позиция (хотя это бывает крайне редко). В случае необходимости использования оборудования других производителей мы встраиваем в технологическую линию стандартные агрегаты, которые адаптируются с нашим оборудованием.
- Обратила внимание, что ваша компания развивает направление, которое связано со строительством в России мини-заводов по выпуску древесных плит (OSB, ДСтП, ДВП, MDF) малой производительности. Скажите, сколько в среднем проходит времени с момента проектирования до их пуска?
- В настоящее время срок ввода в эксплуатацию предлагаемых нами плитных мини-заводов - не более полутора лет с начала финансирования и до выхода на проектную мощность. В ближайшее время мы надеемся сократить этот срок до одного года за счет применения имеющихся наработок и мощностей серийного производства. Для примера - срок пуска заводов производительностью от 200 тыс. м3/год - от трех лет.
- Есть ли принципиальная разница при проектировании и производстве оборудования для линий по выпуску плит OSB мощностью 15-60 тыс. м3 в год и от 100 тыс. м3 в год?
- Линии по производству плит OSB производительностью от 100 тыс. м3 в год - это совместные итало-российские проекты. Основные станки поставляют наши партнеры из Италии. Итальянские специалисты выполняют их пусконаладку, настройку, отладку технологического процесса. Мы поставляем только металлоемкое, крупногабаритное и вспомогательное оборудование. В этом случае нам гораздо проще работать, так как с нас снимается значительная часть ответственности и в меньшей степени загружается наше производство. Только наша компания занимается проектированием и разработкой линий мощностью до 100 тыс. м3 в год.
- Одна из составляющих качества выпускаемой продукции - квалифицированный персонал, который участвует в ее производстве. После пусконаладочных работ проводится ли обучение персонала новой линии настройке и обслуживанию оборудования?
- Пусконаладка и обучение в обязательном порядке выполняются специалистами нашей компании. Мы разрабатываем оборудование с автоматическими режимами работы, что позволяет минимизировать влияние человеческого фактора на результаты производства. Также стараемся максимально автоматизировать весь технологический процесс - от подачи сырья на линию до упаковки готовой продукции, чтобы роль человека в производстве сводилась только к контролю параметров процесса.
- Какие инвестиции могут понадобиться при оснащении завода по выпуску плит OSB мощностью, например, 15 тыс. м3 в год?
- Объем инвестиций на строительство целого завода оценить трудно, так как это зависит от конкретной ситуации и от того, что имеется у заказчика на момент принятия решения (готовая производственная площадка, земля, инфраструктура и т. д.). Мы можем только оценить размер инвестиций в само технологическое оборудование. На февраль 2016 года стоимость линии для выпуска плит OSB производительностью 15 тыс. м3 в год составляла около 200 млн руб. (в зависимости от региона поставки), это цена уже с доставкой, монтажом, наладкой оборудования и обучением персонала.
- Срок окупаемости вложенных средств больше при строительстве завода мощностью 15-60 тыс. м3 в год или более 100 тыс. м3 в год?
- Как было сказано ранее, мы предлагаем нашим заказчикам два типа линий по производству плит OSB: линию, полностью укомплектованную оборудованием нашего предприятия (производительность - 15, 30, 45, 60 тыс. м3 в год), и линию, в комплектации которой использованы головные итальянские станки (производительность - от 100 тыс. м3 в год). Безусловно, линия с использованием большого числа европейского оборудования дороже и менее рентабельна сейчас, чем линия, в составе которой исключительно отечественное оборудование.
Проще и правильнее сравнивать комплексы разной мощности нашего производства. К примеру, если окупаемость линии мощностью 15 тыс. м3 в год немногим более пяти лет, то для 30-тысячной линии этот срок уже менее четырех лет (с учетом инвестиционной фазы). Сроки окупаемости указаны при условии монтажа оборудования на готовой производственной площадке и отсутствия у заказчика других затрат (стоимость строительства зданий, приобретения подъемно-транспортного оборудования, организации и оснащения складских площадей и т. д.).
- При проектировании новых мини-заводов или линий закладываются риски на увеличение курса евро? Или клиент оплачивает полностью стоимость заказа до начала работ по изготовлению линии?
- Поскольку наше оборудование производится в России, все цены указываются в рублях. Стоимость нашего оборудования не меняется уже почти год, несмотря на довольно большие колебания курсов мировых валют. Стараемся как можно дольше удерживать цены на одном уровне, чтобы заказчики при общении с инвесторами знали, что стоимость оборудования не возрастет с учетом постоянно меняющегося курса мировой валюты и не придется пересчитывать бизнес-планы. Хоть в нашем оборудовании немало европейских комплектующих, риски по увеличению курса евро при их закупке мы берем на себя. Кроме того, клиент вносит предоплату, а не оплачивает полную стоимость заказа. Это стандартная мировая практика: вся сумма распределяется на несколько платежей, которые вносятся в течение периода изготовления линии. Мы обговариваем индивидуальные условия оплаты оборудования, которые зависят от реальных возможностей заказчика, вплоть до предоставления рассрочки на часть стоимости оборудования.
- Как вы считаете, кризис - это период застоя или, наоборот, перемен, когда можно заниматься проектированием новых производств и развитием новых направлений в деревообработке?
- Кризис - это период снижения деловой активности. В кризисные времена, как никогда, необходимо развивать новые направления в работе предприятий и диверсифицировать бизнес. Сейчас в стране снижается зависимость от мировых цен на нефть. Все сферы бизнеса, так или иначе связанные с добычей углеводородов, постепенно пойдут на спад. В тренде реальный сектор экономики, импортозамещение, развитие новых технологий и отраслей промышленности, до недавнего времени считавшихся низкорентабельными, к которым в том числе относится и деревообработка.
Беседовала Екатерина МАТЮШЕНКОВА