Отходы фанерного производства как топливо для котельных
Древесина и побочные продукты ее обработки и переработки являются возобновляемым источником энергии с нейтральным уровнем эмиссии углерода и могут быть эффективно использованы в качестве топлива для котельных, вырабатывающих тепловую и электрическую энергию. Правительствами индустриально развитых стран для снижения воздействия парниковых газов на климат планеты активно поощряется замена ископаемых топлив биотопливом.
PRD-22000
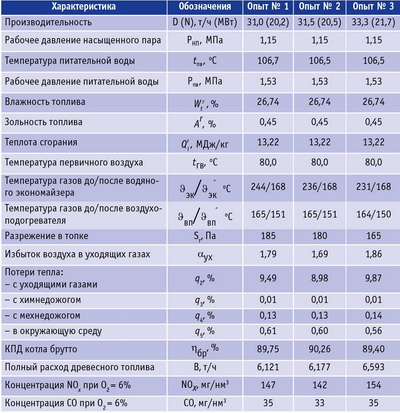
Для снижения себестоимости тепловой энергии, влияния факторов внешней среды на устойчивость и стабильность развития предприятия и для комплексного сокращения выбросов вредных веществ в окружающую среду в ЗАО «Архангельский фанерный завод» в 2015 году был смонтирован и введен в эксплуатацию котлоагрегат PRD 22000 австрийской фирмы Polytechnik Luft- und Feuerungstechnik GmbH. Котло-агрегат установлен в котельной, предназначенной для обеспечения паром технологического цикла фанерного производства, оборудован дымовой трубой высотой 34 м и автоматической системой управления процессами. Котлоагрегат рассчитан на выработку насыщенного пара с рабочим давлением 1,2 МПа, его номинальная паропроизводительность - 34,0 т/ч.
Топливом для котлоагрегата является смесь дробленки фанеры, березовой коры, древесно-шлифовальной пыли (ДШП), опилок от обработки фанеры и рубленого шпона. Компоненты этой топливной смеси значительно различаются как по теплотехническим характеристикам (влажности, зольности, теплотворной способности), так и по технологическим показателям (сыпучести, взрывоопасности), но особенно сильно - гранулометрическим составом. Размеры частиц топливной смеси отличаются друг от друга более чем в тысячу раз, что обеспечивает ее уникальность, а также ставит задачу обеспечения эффективного и взрывобезопасного энергетического использования. Так, ДШП и опилки с линий обрезки фанеры являются мелкофракционным материалом и относятся к IV группе взрывоопасности, их критерий взрываемости (Кт) (КтДШП = 10,85; Ктопил = 9,66 соответственно) обеспечивает высокую степень взрыво- и пожароопасности состава сжигаемого древесного топлива, что серьезно усложняет условия эксплуатации котлоагрегата PRD 22000.
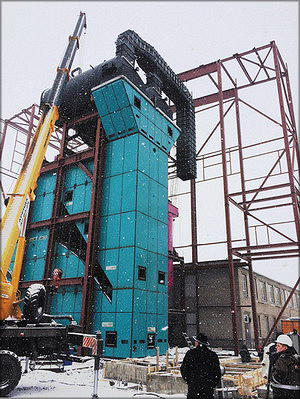
Монтаж
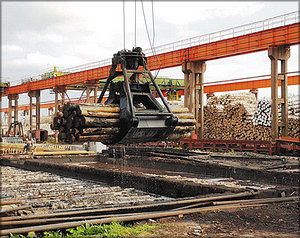
бассейн
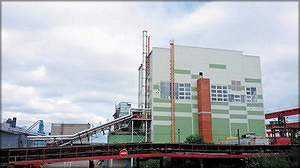
здание котельной
Для комплексной оценки эффективности работы установленного оборудования было проведено энергетическое обследование котельной, в ходе которого паропроизводительность котлоагрегата менялась в диапазоне 89,0-96,0% от номинальной.
У здания котельной (размером в плане 19,0×33,0 м) имеется один склад топлива, который оборудован системой топливоподачи. Топливо с помощью шести толкателей подается на цепной скребковый транспортер, который расположен под углом 90° к топливному складу с подвижным дном. Транспортер оснащен штангой со скребками и приводится в действие гидравлическим цилиндром от маслостанции.
Транспортер обеспечивает подачу топлива в загрузочную шахту автоподатчика, уровень топлива в которой контролируется фотоэлектрическими датчиками. Для защиты от возгорания шахта и цепной скребковый транспортер оснащены тепловой и электрической защитой. Из шахты топливо поступает на толкатель, который обеспечивает его транспортировку через загрузочное устройство на колосниковую решетку. Загрузка топочного устройства осуществляется в тактовом режиме в зависимости от расхода тепла потребителями, состава и влажности топлива.
Топка оборудована наклонно-переталкивающей колосниковой решеткой. В обмуровке боковых стен над колосниковой решеткой устроены пять «фотобарьеров» для контроля высоты слоя топлива. Под колосниковой решеткой с помощью перегородок организованы четыре зоны с индивидуальным подводом в них с одной стороны - первичного воздуха, а с другой - рециркулирующих продуктов сгорания. Подача горячего воздуха после воздухоподогревателя в каждую из зон колосниковой решетки осуществляется вентилятором.
Воздух на вторичное дутье может забираться как из верхней, так и из нижней частей помещения котельной, с помощью вентилятора он вводится в объем топочной камеры рассредоточено - через сопла, расположенные в шахматном порядке на боковых стенах камеры.
В топочной камере котлоагрегата реализована трехступенчатая схема сжигания топлива. Для дополнительного снижения выбросов оксидов азота, повышения надежности работы колосниковой решетки и обмуровки топки установлены две системы рециркуляции продуктов сгорания и дополнительные дымососы. Забор продуктов сгорания в линии рециркуляции осуществляется из газохода после основного дымососа. Продукты сгорания с помощью дымососа рециркуляции № 1 направляются в объем топочной камеры над колосниковой решеткой со стороны боковых стен. Под колосниковую решетку котла газы рециркуляции подаются позонно с помощью дымососа рециркуляции № 2. Суммарная доля газов рециркуляции составляла rрец = 0,35...0,40. У всех тягодутьевых установок частотное регулирование производительности.
Котлоагрегат оборудован двухходовыми дымогарными парогенераторами, расположенными горизонтально вдоль продольной оси, непосредственно над топочной камерой. На выходе из топки продукты сгорания разделяются на два потока и поступают в парогенераторы. При проведении энергообследования температура насыщенного пара на выходе из парогенераторов составляла 189-191оС, т. е. была близка к нормативной. Температура газов на входе в парогенераторы менялась в диапазоне 850-868 оС, а после них - в диапазоне 231-244 оС. (см. табл.).
Стены топочной камеры выполнены из огнеупорной шамотной обмуровки, для увеличения времени пребывания дымовых газов в топке установлен один промежуточный свод. Температурный уровень обмуровки топочной камеры контролируется с помощью термопар в восьми точках по ходу движения продуктов сгорания.
Продукты сгорания, совершив два хода в каналах топочной камеры, поступают в водоохлаждаемые поворотные камеры парогенераторов, в которых разворачиваются на 90о и совершают два хода, проходя внутри дымогарных труб, а затем поступают в газораспределительную камеру водяного экономайзера, из которой по 400 трубам направляются вниз, отдавая тепло питательной воде. Подвод воды осуществляется в нижнюю часть корпуса экономайзера, а ее отвод из верхней части.
При проведении энергообследования скорость газа при совершении первого хода в парогенераторах составляла 16,4-17,0 м/с; при совершении второго хода она повышалась до Wг = 17,5-18,2 м/с. Скорость газов в трубах водяного экономайзера в исследованном диапазоне нагрузок составляла Wг = 15,8-16,4 м/с.
После экономайзера дымовые газы поступают в мультициклон RGE 22000, где очищаются от твердых частиц. Очищенный газ направляется в рекуперативный трубчатый воздухоподогреватель LUVO 22000, в котором, совершая два хода, обеспечивает подогрев первичного воздуха.
Для очистки поверхностей дымогарных труб парогенераторов, водяного экономайзера и воздухоподогревателя от золовых частиц котлоагрегат оборудован системой пневмообдувки. Мелкодисперсная зола, просыпающаяся через зазоры колосников каждой зоны наклонно-переталкивающей решетки, поступает в бункеры. Крупнодисперсная зола и шлак с колосниковой решетки, а также зола, сепарирующаяся из газового потока при его развороте у задней стены топки, поступают в отдельный бункер. Все очаговые остатки, в том числе золовые частицы из-под экономайзера, золоуловителя и воздухоподогревателя с помощью системы транспортеров поступают в сборный контейнер емкостью 12 м3, при заполнении которого зола и шлак вывозятся автотранспортом.
У сжигаемой топливной смеси была высокая степень неоднородности гранулометрического состава (средний коэффициент полидисперсности n = 0,655, а коэффициент, характеризующий крупность состава b = 3,258·10-3). Влажность древесного топлива была ниже проектной (30-32%), что связано с большим содержанием в смеси мелких взрывоопасных фракций (ДШП и опилок с линии обрезки фанеры). Массовая доля частиц размером менее 2 мм составляла более 32% (рис. 1).
Результаты балансовых опытов показали, что конструкция котлоагрегата и система автоматического регулирования режимов его работы обеспечивают высокую полноту выгорания оксида углерода, концентрация которого не превышала 35 мг/нм3 при КO2 = 6%.
Температура воды на входе в экономайзеры котлоагрегатов была стабильной, что позволяло обеспечить ее дегазацию и довольно глубокое охлаждение дымовых газов.
Конструкция воздухоподогревателя позволила обеспечить подогрев первичного воздуха до 79-81 оС. Продукты сгорания при прохождении через воздухоподогреватель охлаждались до 151-154оС. Температура вторичного воздуха составляла 30-32оС. Указанные факторы обеспечили невысокий уровень температуры обмуровки топочной камеры - 920оС.
Сопротивление котлоагрегата по газовому тракту зависит от его нагрузки, доли рециркуляции продуктов сгорания и характеристик сжигаемого топлива. При проведении балансовых опытов суммарное сопротивление котлоагрегата с парогенератором, водяным экономайзером, золоуловителем и воздухоподогревателем менялось в диапазоне 3,87-3,92 кПа. При этом сопротивление отдельных элементов составляло: топочной камеры с парогенераторами - 1,02-1,09; водяного экономайзера - 0,60-0,65; золоуловителя - 1,29-1,30; воздухоподогревателя - 0,88-0,91 кПа.
Исследования гранулометрического состава очаговых остатков показали, что у летучей золы, отобранной из-под золоуловителя и воздухоподогревателя, были высокая степень полидисперсности гранулометрического состава (n = 0,405) и очень тонкодисперсный состав (b = 0,207). Причем в летучей золе доминировали частицы размером менее 45 мкм, массовая доля которых превышает 64%. Указанный гранулометрический состав летучей золы косвенно свидетельствует о высокой степени улавливания золоочистного оборудования.
У золы и шлака, отобранных из-под топочной камеры, была определена высокая степень полидисперсности гранулометрического состава (n = 0,537), причем в составах золы и шлака доминировали частицы размером > 250 мкм, массовая доля которых составляла 55,56%.
Для определения запыленности дымовых газов и эффективности работы золоуловителя использовался метод внешней фильтрации. Отбор запыленного потока проводился при изокинетических условиях. Для измерения и регулирования расхода отбираемых продуктов сгорания применялось аспирационное устройство ОП-442 ТЦ. Результаты замеров поля скорости и концентраций твердой фазы в дымовых газах до водяного экономайзера показали, что структура газового потока в этом измерительном сечении не позволяет получить объективные результаты и для определения эффективности очистки дымовых газов от взвешенных частиц следует использовать массовый метод топливно-золового баланса.
Структура газового потока в измерительном сечении газохода перед дымовой трубой позволяет получить объективные данные по концентрации твердой фазы в продуктах сгорания. Среднее значение концентрации взвешенных веществ в продуктах сгорания указанного газохода составило 111,8 мг/нм3 при нагрузке котлоагрегата 96% от номинальной.
Выполненные исследования позволили определить значения эмиссий твердых частиц, которые составили 57,08-62,84 г/ГДж, причем коэффициенты выбросов сажевых частиц менялись в диапазоне 7,99-8,80 г/ГДж.
Анализ условий тепловой работы котлоагрегата показал умеренные значения потерь тепла с уходящими газами, что объясняется невысокой температурой этих газов. Конструкция наклонно-переталкивающей решетки и системы охлаждения ее рамы обеспечили отсутствие шлаковых наростов и надежную работу установки шлакоудаления при высокой полноте выгорания горючих веществ в очаговых остатках (С гшл = 9,0 %, С гун = 15,8%). Потери тепла с механической неполнотой сгорания составили q4 = 0,13-0,14%, а с физической теплотой шлака - q6 ≤ 0,02%.
Для определения потерь тепла в окружающую среду использовался относительный метод, при этом ограждающие конструкции разбивались на отдельные участки, в каждом из которых с помощью пирометра измерялись средние температуры. На основании результатов замеров средних показателей температуры в 810 участках были рассчитаны коэффициенты теплоотдачи, а затем - потери тепла в окружающую среду (удовлетворительное качество обмуровочных и теплоизоляционных материалов позволило обеспечить низкий уровень этой потери, которая для номинальной нагрузки котлоагрегата составила q5 ном = 0,54%).
КПД брутто котлоагрегата в исследованном диапазоне нагрузок составил 89,40-90,26%, а удельный расход условного топлива на выработку 1 ГДж - 37,78-38,14 кг усл. т.
Конструкция основного и вспомогательного оборудования котлоагрегата обеспечили его работу с высокими экологическими показателями. Так, концентрации вредных веществ, приведенные к коэффициенту избытка воздуха 1,4, составили: монооксида углерода - 33-35; оксидов азота - 142-154; твердых частиц - 111,8 мг/нм3.
Реализация проекта по энергетическому использованию отходов фанерного производства для выработки тепловой энергии позволила значительно ослабить загрязнение окружающей среды, а также в полном объеме обеспечила потребности завода в технологическом паре.
Энергообследование показало, что у котлоагрегата PRD-22000 есть резервы для повышения технико-экономических и экологических показателей.
Виктор ЛЮБОВ, д-р техн. наук, проф., директор УНЦЭИ САФУ