Обработка низкотоварной древесины на комплексных лесопромышленных предприятиях. Часть 6
Производство технологической щепы из низкотоварной древесины
Часть 1. Направления диверсификации с использованием инновационных технологий
Часть 2. Известные виды продукции из низкотоварной древесин
Часть 3. Инновационные виды продукции из низкотоварной древесины
Часть 4. Эффективные технологии заготовки и обработки низкотоварной древесины
Часть 5. Как решить проблему экологической эффективности лесопользования
Часть 7. Математическая модель обезвоживания древесины в процессе прессования и сушки
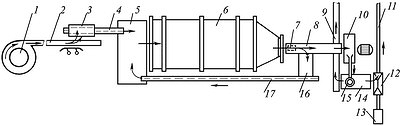
Рис. 1. Схема линии по производству технологической щепы:
1 – тарельчатый питатель; 2 – транспортер; 3 – гидроколун;
4 – транспортер; 5 – загрузочная воронка; 6 – окорочный барабан;
7 – металлоискатель; 8 – транспортер; 9 – транспортер отходов;
10 – рубительная машина; 11 – пневмопровод; 12 – шлюзовой питатель;
13 – вентилятор; 14 – сортировочная установка; 15 – циклон; 16 – лоток;
17 – возвратный транспортер
Стандартная технологическая цепочка работы древесно-подготовительного цеха для выработки технологической щепы (рис. 1) такова: бревна, отсортированные по породам, через тарельчатый питатель и ленточный транспортер поштучно подают на колун, которым раскалывают на четыре или шесть частей так, чтобы максимальное сечение расколотого полена соответствовало размерам загрузочного патрона рубительной машины.
Бревна без внутренней гнили, диаметр которых соответствует размерам загрузочного патрона рубительной машины, раскалыванию не подлежат. Бревна и колотые поленья подаются транспортером, расположенным под колуном, в загрузочную воронку, откуда поступают в окорочный барабан непрерывного действия. Вышедшие из барабана окоренные бревна и поленья по ленточному транспортеру (под которым установлен металлоискатель) подаются в рубительную машину.
Плохо окоренные бревна и поленья с ленточного транспортера через лоток сбрасывают вручную на транспортер, возвращающий их в загрузочную воронку для повторной обработки в окорочном барабане. Качество окорки визуально оценивает оператор, который сбрасывает лесоматериал на возвратный транспортер.
Если на выходе из окорочного барабана образуется значительный объем плохо окоренных лесоматериалов, например бревен с содержанием коры на древесине более 30%, то принимают решение продлить период нахождения лесоматериалов в барабане за счет уменьшения сечения выхода путем перемещения шиберного щита (шандора), например, вверх, в зависимости от конструкции барабана. И наоборот: если объем окоренных лесоматериалов чрезмерно велик, то сечение выхода увеличивают путем опускания шандора, что обеспечивает повышение производительности барабана и сокращение потерь древесины.
Физико-механические свойства сырья, поступающего в древесно-подготовительный цех, постоянно меняются. Прежде всего они зависят от размеров (длины и диаметра), породы, влажности и температуры древесины.
Для того чтобы обеспечить требуемое качество окорки, лесоматериалы разной длины следует подвергать окорке разной продолжительности. Короткомерные лесоматериалы окариваются быстрее длинных.
Барабан разгружается тогда, когда все лесоматериалы достигают требуемой степени окорки. Различие в продолжительности окорки бревен разной длины отрицательно сказывается на производительности барабана, трудоемкости окорки 1 м3 лесоматериалов, энергоемкости процесса, а в итоге - на себестоимости окорки 1 м3 древесины, поскольку от продолжительности нахождения бревен в окорочном барабане напрямую зависят потери древесины, возникающие в процессе окорки.
Часто технологи для получения щепы высшего качества ставят окорочный барабан в режим, рассчитанный на наихудшие условия окорки (низкая влажность, отрицательная температура окариваемых бревен), что существенно увеличивает время нахождения бревен в барабане и снижает его производительность и энергоэффективность окорки.
Если условия окорки меняются в лучшую сторону (повышаются влажность и температура окариваемой древесины), то требуемое время окорки существенно сокращается. При отсутствии оперативного контроля, без уменьшения времени нахождения бревен в барабане начинается перекор - значительный объем древесины отделяется от бревен и удаляется вместе с отходами окорки из окорочного барабана через специальные прорези на выносной транспортер, находящийся под барабаном.
технологической щепы, %
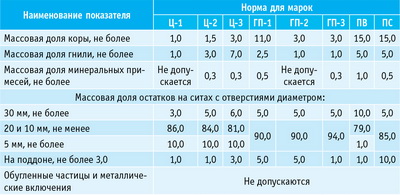
Основными требованиями, предъявляемыми к качеству технологической щепы, согласно ГОСТ 15815-83 «Щепа технологическая. Технические условия», являются: массовая доля коры; массовая доля гнили; массовая доля остатков на ситах; отсутствие обугленных частиц и металлических примесей; состав щепы по породам; массовая доля минеральных примесей; массовая доля щепы с мятыми кромками; угол среза.
Значения качественных показателей разных марок технологической щепы приведены в таблице.
Содержание в технологической щепе коры, гнили и минеральных включений зависит от природно-производственных условий ее заготовки (таксационных характеристик, сезона и способа заготовки), а также от качества выполнения окорки и облагораживания в случае переработки низкокачественной древесины.
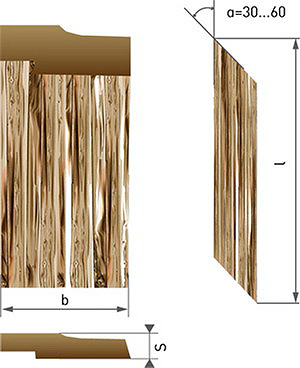
Рис. 2. Геометрические параметры щепы:
l – длина, b – ширина, s – толщина, α – угол среза
Геометрические размеры щепы (длина, ширина, толщина, угол среза; рис. 2), а также процентное содержание кондиционной и некондиционной (крупной и мелкой) фракций щепы во многом зависят от настроек и оптимальности работы рубительной машины.
Приведем некоторые необходимые определения. Итак, согласно ГОСТ 23246-78 «Древесина измельченная. Термины и определения» и ГОСТ 18110-72 «Плиты древесно-стружечные. Технология. Термины и определения»:
- длина щепы - размер древесной частицы в направлении волокон древесины;
- ширина щепы - наибольший размер древесной частицы в направлении, перпендикулярном ее продольной кромке;
- толщина щепы - наименьший размер древесной частицы в направлении, перпендикулярном ее продольной кромке;
- кондиционная фракция щепы - совокупность древесных частиц, размеры которых соответствуют требованиям, предъявляемым к щепе в зависимости от ее дальнейшего назначения;
- крупная фракция щепы - совокупность древесных частиц, оставшихся на сите с наибольшим (в соответствии с требованиями) проходным сечением отверстий сита сортирующих устройств;
- мелкая фракция щепы - совокупность древесных частиц, прошедших через сито сортировочных устройств, на котором задерживается кондиционная фракция;
- угол среза щепы - угол, образованный поверхностью среза и направлением волокон.
В общем виде процесс производства технологической щепы балансовой древесины включает следующие операции: окорку балансов; рубку окоренных балансов на технологическую щепу; сортировку технологической щепы на размерные фракции.
Сортировка щепы обычно выполняется при помощи плоскоситовых сортировок с поэтажной компоновкой наклонных сит с определенными размерами ячеек, под которыми установлен поддон для сбора мелких частиц.
После сортировки крупная фракция щепы может подаваться назад в рубительную машину (или в дезинтегратор) для доизмельчения, кондиционная фракция направляется в дальнейшее производство, мелкая является отходом и отправляется, например, на сжигание в топке котельной предприятия.
Требование однородности щепы по размерам связано прежде всего с необходимостью получения конечной продукции с однородными физико-механическими свойствами.
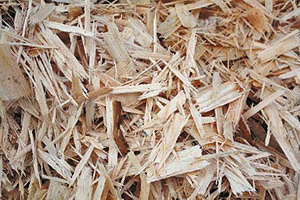
Рис. 3. Непровар при варке крупной фракции щепы
Например, в целлюлозно-бумажном производстве при малых размерах щепы улучшаются пропитка и нагрев, но возрастает расход варочных растворов и ухудшаются физико-механические свойства целлюлозы как результат повреждения древесных волокон, а варка щепы крупной фракции обеспечивает выход целлюлозы с высокими прочностными свойствами, но с неравномерным проваром и повышенным содержанием непровара (рис. 3).
Рубка балансов в щепу выполняется при помощи рубительных машин разной конструкции. В процессе работы машины происходит затупление ножей, что приводит к сокращению выхода кондиционной фракции щепы и росту процента выхода мелкой фракции.
В настоящее время степень затупления ножей рубительных машин при производстве технологической щепы определяют путем измерения радиуса затупления режущей кромки ножей во время периодической остановки рубительных машин. Частота остановки назначается директивно, например, зимой - два раза в смену, летом - один раз в смену.
Подобный подход к остановке рубительной машины и замене ножей не учитывает многие, часто меняющиеся показатели предмета труда: породу древесины, ее качество и количество.
При остановке рубительной машины используют следующие методы определения степени затупления ножей: визуальный осмотр; проверку остроты на ощупь; создание слепков лезвий на свинцовых пластинах. Вместе с тем каждая остановка машины приводит к большим потерям рабочего времени, часто к остановке всей поточной линии, затратам труда на осмотр ножей, особенно если на машине их 10-16 шт.
Кроме того, при неполной загрузке рубительной машины директивные остановки машины и осмотры ножей не дают желаемого эффекта. Об этом свидетельствуют результаты исследований проф. С. Б. Васильева. Во время эксперимента круглосуточно отбирались пробы щепы и оценивалась зависимость между временем отбора и фракционным составом. Замена ножей рубительной машины выполнялась директивно два раза в сутки.
В результате обработки результатов эксперимента был сделан вывод об отсутствии влияния состояния ножей рубительной машины на качество щепы, что объясняется тем, что ножи за время работы не вырабатывали свой ресурс ввиду небольшой загрузки.
Известны также устройства для определения степени затупления ножей рубительных машин, в составе которых имеются приборы для измерения параметра, выбранного для оценки состояния ножей, например для измерения зазора между ножами и контрножом. Этот способ также требует периодической директивной остановки рубительной машины, а следовательно всей поточной линии.
Признаками затупления ножей являются: изменение звука при работе машины, увеличение токовой нагрузки на двигатель, ухудшение затягивания древесного сырья (Постановление Госкомтруда СССР от 18.04.91 № 89).
Суждение о степени затупления ножей рубительной машины по изменению потребляемой мощности также малоэффективно, что объясняется очень большой массой рубительных машин и инерцией их агрегатов, работающих как маховики. В связи с этим при прочих равных условиях изменение потребляемой мощности рубительной машиной по мере затупления ножей малозаметно. А с учетом частого изменения физико-механических свойств подаваемых на измельчение балансов - необъективно.
Вывод: используемые в настоящее время технологические процессы производства технологической щепы из низкотоварной древесины неоптимальны, поскольку часто приводят к значительным потерям древесины и перерасходу энергии, и нуждаются в совершенствовании.
Ольга КУНИЦКАЯ,
д-р техн. наук, доцент СПбГЛТУ