Управление производством на предприятиях ЛПК. Часть 3
Вспомогательное производство. Ремонтное хозяйство
Современные предприятия ЛПК оснащены сложнейшим оборудованием, установками, аппаратами, механизмами, полуавтоматическими и автоматическим линиями, агрегатами, транспортными средствами. Для обеспечения работы основных производственных фондов на предприятиях ЛПК создается ремонтное хозяйство (служба, подразделение). Кроме того, в структуре крупных деревообрабатывающих предприятий, как правило, имеется инструментальное хозяйство, задача которого - обеспечение производства необходимыми инструментами и оснасткой.
Часть 1. Принципы, методы и функции управления. Системный подход к управлению предприятием
Часть 2. Управление основным производством
Часть 4. Вспомогательное производство. Энергетическое хозяйство
Часть 5. Управление экономической деятельностью
Часть 6. Экологический менеджмент
Часть 7. Управление вторичными ресурсами
Часть 8. Управление социальной деятельностью
Основными задачами управления ремонтной службой являются: подготовка правил технической эксплуатации и обслуживания оборудования и других основных фондов; контроль обновления основных фондов, выполнения правил их эксплуатации; сокращение времени и затрат на ремонт; повышение качества ремонтных работ.
Различают четыре метода организации ремонтных работ: аварийный, послеосмотровой, стандартный (принудительный), плановопредупредительный. По аварийному методу ремонт оборудования выполняется после того, как оно вышло из строя вследствие износа, аварии (поломки). Применение этого метода ремонта характеризует отсутствие данных о сроках службы оборудования и свидетельствует о низком уровне проведения ремонтных работ на предприятии. Аварийный метод ремонта нарушает ритм работы, влияет на увеличение продолжительности простоев оборудования, повышение расходов на ремонтные работы. Послеосмотровой метод ремонта характеризуется установлением определенных сроков проведения осмотров оборудования. В процессе осмотров выявляют его техническое состояние и составляют ведомость дефектов. На основе дефектной ведомости разрабатывают оперативные планы проведения ремонтов. Недостатком этого метода является отсутствие необходимых данных для планирования ремонтов на длительный период (квартал, год).
Принудительный метод ремонта характеризуется установлением твердых сроков вывода оборудования в ремонт и содержания ремонтных работ. Ремонт выполняется независимо от фактического состояния объекта. Обычно принудительный метод предусматривается в случаях, когда преждевременный выход оборудования из строя связан с человеческими жертвами или крупными авариями. В этой методике заложена основа для планирования ремонтов на длительное время, но затраты по ним значительные.
Наиболее распространен планово-предупредительный метод ремонта (ППР), который сочетает достоинства послеосмотрового и принудительного. В этом случае заранее устанавливаются сроки проведения ремонта и содержание работ, но выполняются они в зависимости от состояния ремонтируемого объекта. Система ППР представляет собой совокупность организационно-технических мероприятий по уходу, надзору, обслуживанию и ремонту оборудования, проводимых по заранее составленному плану с целью предупреждения выхода оборудования из строя и поддержания его в постоянной эксплуатационной готовности.
Системой планово-предусмотри-тельного ремонта предусматриваются следующие виды работ: повседневный уход (текущее обслуживание) за оборудованием; межремонтное (дежурное) обслуживание; периодические осмотры; плановые ремонты.
Текущее обслуживание выполняется операторами, работающими на оборудовании, и предполагает в основном точное соблюдение правил эксплуатации оборудования и бережное обращением с ним обслуживающего персонала: ежесменную чистку машин и аппаратов, смазку, осмотр и проверку креплений; содержание в чистоте рабочего места. Принимая оборудование от закончившей работу смены, рабочий должен проверить состояние оборудования и качество его обслуживания. Все замеченные приемщиком отклонения в работе оборудования должны быть отмечены в сменном журнале и устранены. Дежурное обслуживание обычно осуществляется дежурным персоналом ремонтной службы, носит профилактический характер и включает в себя регулировку механизмов, устранение мелких неисправностей, проверку работы контрольно-измерительных приборов, периодическую промывку и очистку оборудования, наблюдение за работой агрегата.
Периодические осмотры проводятся по графику, составленному в соответствии со структурой и продолжительностью ремонтного цикла, обычно в середине каждого межремонтного периода с целью проверки состояния оборудования, устранения недостатков межремонтного обслуживания и уточнения объема предстоящего планового ремонта.
К плановым ремонтам по системе ППР относятся:
- малый ремонт (разновидность текущего ремонта), в ходе которого выполняется замена или восстановление изношенных деталей, срок службы которых соответствует длительности межремонтного периода, а также разборка и регулировка узлов, подверженных наибольшему износу и несущих большие нагрузки;
- в ходе среднего ремонта выполняют работы, аналогичные работам текущего ремонта, плюс частичную разборку оборудования, замену и восстановление значительного количества изношенных деталей и отдельных узлов, сборку, регулировку и испытание оборудования на холостом ходу и под нагрузкой;
- капитальный ремонт, в ходе которого выполняются полная разборка оборудования с заменой всех изношенных частей, сборка, регулировка и испытание под нагрузкой. После капитального ремонта оборудование должно соответствовать требованиям по мощности, производительности и другим важным параметрам. Капитальные (и частично средние) ремонты рекомендуется совмещать с модернизацией. При этом ремонты, сопровождающиеся модернизацией с целью повышения технического уровня.
Затраты (а они весьма существенные) на капитальный и средний (с периодичностью более года) ремонты оборудования осуществляются за счет амортизационных отчислений. Поэтому выполнению капитального и среднего ремонтов должно предшествовать экономическое обоснование целесообразности, что определяется путем расчета коэффициента эффективности ремонта kp. Граница, за пределами которой экономически нецелесообразно проводить очередной капитальный (средний) ремонт, определяется по формуле
где - ΣЗ суммарные затраты на капитальные и средние ремонты с периодичностью более года, проведенные с начала эксплуатации оборудования; Зi - стоимость очередного ремонта; Ar - общая сумма амортизационных отчислений за весь срок службы оборудования; Л - ликвидационная стоимость оборудования. Величину Ar можно определить по формуле
где Ф - первоначальная стоимость оборудования; Н - годовая норма амортизации; T - число лет эксплуатации оборудования.
Ликвидационная стоимость оборудования Л определяется расчетным путем или укрупненно может быть принята в размере 3% его первоначальной стоимости, то есть
Л = 0,03Ф.
Тогда формула для расчета коэффициента эффективности ремонта kp в развернутом виде:
Итак, чтобы ремонт был экономически эффективен, должно соблюдаться условие
Кp < 1.
Отказ от очередного ремонта оборудования и замена его новым оказывается экономически целесообразным при условии, что
Кp > 1.
Когда Кp = 1, проведение очередного ремонта не является убыточным, но представляет границу его эффективности.
В качестве примера проанализируем экономическую эффективность ремонта оборудования метанольной установки. Первоначальная стоимость аппарата - 3,6 млн руб.; нормативный срок службы - 17 лет; общая норма амортизации - 12,9%, в том числе 6,9% - на капитальный (средний) ремонт и модернизацию. В период эксплуатации на ремонты затрачено 1,55 млн руб. Смета очередного капремонта - 240 тыс. руб. Целесообразность проведения ремонта или замены аппарата новым определяется расчетом
Следовательно, экономическая целесообразность проведения очередного ремонта очевидна.
Ремонтный цикл представляет собой порядок чередования работы и простоя оборудования в период ремонта. Он характеризуется продолжительностью - периодом работы и простоев оборудования между двумя капитальными ремонтами или периодом от ввода оборудования в эксплуатацию до первого капитального ремонта, а также структурой. Структура ремонтного цикла представляет собой перечень и последовательность выполнения ремонтных работ в пределах одного ремонтного цикла. Положение о ППР содержит следующие условные обозначения: К - капитальный ремонт, С - средний ремонт, М - малый ремонт. Ремонтный цикл включает один капитальный, несколько средних и несколько малых ремонтов.
Для деревообрабатывающего оборудования прерывных производств ремонтный цикл состоит из 10 осмотров (О - 10), четырех малых ремонтов (М - 4) и одного капитального (К - 1). У структуры ремонтного цикла следующий вид: К - О1 - О2 - МР1 - О3 - О4 - М2 - О5 - О6 - М3 - О7 - О8 - М4 - О9 - О10 - К.
Число малых и средних ремонтов и их чередование в ремонтном цикле для разных видов лесохимического оборудования неодинаково. Число малых ремонтов - от 6 до 92, а средних - 1-5. Например, структура ремонтного цикла реторты вертикальной непрерывного действия типа Р-6А производительностью 75 тыс. м древесины такова: К - М1 - М2 - М4 - М5 - М6 - М7 - М8 - М9 - М10 - М11 - С1 - М12 - М13 - М14 - М15 - М16 - М17 - М18 - М19 - М20 - М21 - М22 - С2 - М23 - М24 - М25 - М26 - М27 - М28 - М29 - М33 - С3 - М34 - М35 - М36 - М37 - М38 - М39 - М40 - М41 - М42 - М43 - М44 - К. То есть за один ремонтный цикл проводится один капитальный, три средних и 44 малых ремонта.
Структура ремонтного цикла распылительных сушилок в гидролизно-дрожжевом производстве следующая: К - М1 - М2 - М3 - С1 - М4 - М5 - М6 - С2 - М7 - М8 - М9 - С3 - М10 - М11 - М12 - С4 - М13 - М14 - М15 - С5 - М16 - М17 - М18 - К, или 1К - 5С - 18М.
На основе продолжительности и структуры ремонтного цикла устанавливается продолжительность межремонтного периода П, то есть время между двумя плановыми ремонтами. Расчет ведется по формуле
где Тц - продолжительность ремонтного цикла, ч; n - количество средних ремонтов в цикле; m - количество малых ремонтов в цикле; 1 - капитальный ремонт.
Применительно к реторте типа Р-6А продолжительность межремонтного периода составляет 720 ч
Простои оборудования по причине ремонта вычисляются с момента остановки агрегата на ремонт до момента приемки его из ремонта. Туда также включается время на подготовку оборудования к ремонту (охлаждение, нейтрализацию, промывку, чистку и
т. п.) и время, необходимое для испытания агрегата после ремонта. Продолжительность простоя оборудования в ремонте зависит от вида ремонта, сложности агрегата, состава ремонтной бригады, технологии ремонта и организационно-технических условий выполнения ремонтных работ. Нормативы простоя оборудования в ремонте устанавливаются в часах на каждый вид ремонта. Время простоя в ремонте включается в норматив времени работы оборудования между ремонтами. В качестве примера в табл. 1 приведены нормативные данные о длительности простоя в ремонте для некоторых видов лесохимического оборудования.
Длительность простоя оборудования в ремонте за ремонтный цикл Пц можно определить по формуле
Пц = 1Рк + nРc + mРm,
где Рк, Рc, Рm - нормативы простоя в капитальном, среднем и малом ремонтах соответственно, ч. Другие показатели пояснены ранее.
Простой оборудования по причине ремонта за год устанавливается на основании плана-графика ППР (табл. 1).
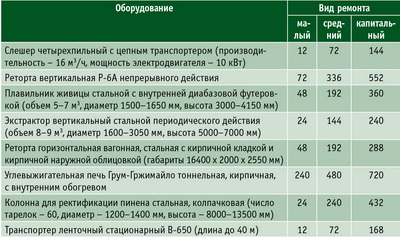
Система нормативов ППР должна включать в себя также затраты времени на ремонтные работы и межремонтное обслуживание. Нормативы трудоемкости ремонтных работ разрабатываются применительно к каждому виду оборудования, категории ремонта и профессии ремонтных рабочих (станочники, слесари и др.). Они устанавливаются с учетом рациональной организации проведения ремонтных работ. Нормативы межремонтного обслуживания рассчитываются на одного явочного рабочего. Другим необходимым условием организации работы оборудования по системе ППР является организация парка запасных частей (деталей). Она включает в себя разработку номенклатуры запчастей и установление нормативов их запаса. Номенклатура запасных деталей устанавливается на основании дефектных ведомостей и состоит из следующих классификационных групп:
- детали, срок службы которых короче, чем продолжительность межремонтного периода;
- детали, срок службы которых превышает межремонтный период, но которые расходуются в большом количестве;
- детали, которые часто выходят из строя.
При определении нормативов запаса запчастей для ремонта исходят из того, чтобы запас был минимальным, но достаточным для проведения ремонта по системе ППР. Норматив рассчитывается по формуле
сокращения запаса деталей k

где Hi - норматив запасных деталей i-го наименования; а - норма запаса деталей в месяцах (от 3 до 6); n - число одинаковых деталей; N - количество однотипного оборудования; t - срок службы детали в месяцах; k - коэффициент сокращения запаса деталей (для его определения можно использовать нормативные данные, приведенные в табл. 2).
Выполнение работ по системе ППР требует разработки необходимой технической документации: паспортов всех объектов оборудования и их систематического обновления; альбомов чертежей запасных деталей, узлов и механизмов; составления учетно-контрольных карт на каждую единицу оборудования и дефектных ведомостей; инструкций и сменных журналов по эксплуатации и уходу за оборудованием.
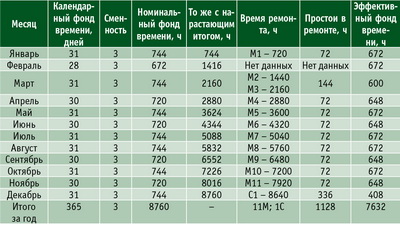
Планирование ремонтных работ по системе начинается с разработки графиков ремонта, в которых содержится базовая информация для проведения всех последующих расчетов, связанных с планированием ремонтного хозяйства предприятия. Для составления графиков планово-предупредительного ремонта необходимо знать режим работы оборудования, ремонтные циклы, нормативы простоя в период ремонта. Обратимся к примеру, приведенному в табл. 3. Составим на планируемый год график ППР вертикальной реторты типа Р-6А производительностью 75 тыс. м в год. Реторта работает непрерывно, межремонтный период равен 720 ч. Время простоя в малом ремонте - 72 ч, в среднем - 336 ч. Начало ремонтного цикла совпадает с началом года, структура цикла: 44М, 3С, 1К. Сначала расчитывается номинальный фонд времени работы реторты в часах для каждого месяца и в целом за год. При непрерывном режиме работы реторты номинальный фонд времени совпадает с календарным и определяется как произведение количества календарных дней в месяце, сменности работы и продолжительности смены в часах. Например, в январе номинальный фонд времени работы реторты составит 744 ч (31), в феврале этот показатель будет равен 672 ч (28 х 3 х 8). Номинальное время за год при таком режиме работы реторты составит 8760 ч. Первым видом ремонтных работ реторты в планируемом году должен быть первый
30 января первым малым ремонтом, заканчивается 26 декабря первым средним ремонтом и проводится по следующей схеме: М1 - М2 - М3 -М4 - М5 - М6 - М7 - М8 - М10 - М11 - С1.
Продолжительность простоя реторты в ремонте в планируемом году составит 1128 ч, а эффективный фонд времени - 7632 (8760 - 1128) ч. Планы-графики ППР составляют по каждому виду оборудования. Они согласуются с начальниками цехов, утверждаются главным инженером и являются обязательными для всех структурных подразделений предприятия. На основании разработанных планов-графиков ППР определяется трудоемкость ремонтных работ. Если принять нормативом трудоемкости для малого ремонта 149 чел./ч, а для среднего - 863 чел./ч, то в рассматриваемом примере трудоемкость ремонта реторты составит 2502 (149 х 11 х 863) чел./ч.
Зная значения трудоемкости ремонтных работ (Tрем), эффективный фонд времени (Tэф) и средний коэффициент выполнения норм (k), можно вычислить число рабочих, необходимое для выполнения ремонтных работ в планируемом году (R), по формуле
Число рабочих для межремонтного обслуживания рассчитывается по формуле
где nсм - сменность работы; tобс - норматив межремонтного обслуживания на одного явочного рабочего человека, а - процент невыходов рабочих на работу.
Планирование заработной платы в ремонтном хозяйстве осуществляется в порядке, аналогичном порядку в основном производстве. Затраты на ремонтные работы включают следующие статьи расходов: заработную плату ремонтных рабочих, стоимость материалов для ремонта и производства запчастей, цеховые расходы, общепроизводственные расходы. На основе проведенных плановых расчетов составляются показатели работы ремонтного хозяйства: объем ремонтных работ, чел./ч; численность работающих, чел. (в том числе рабочих); выработка на одного рабочего, чел./ч; годовой фонд заработной платы, тыс. руб.; средняя заработная плата, руб.; себестоимость ремонтных работ, тыс. руб.; себестоимость капитальных ремонтов; себестоимость ремонтных работ по отношению к балансовой стоимости оборудования, %; снижение расходов на ремонтные работы, приходящиеся на 1 руб. товарной продукции. С целью улучшения технико-экономических показателей разрабатывается план повышения эффективности работы ремонтного хозяйства.
Как уже отмечалось, на деревообрабатывающих предприятиях самостоятельным структурным подразделением является инструментальное хозяйство. На крупных деревообрабатывающих предприятиях инструментальное хозяйство включает общепроизводственные и цеховые службы. К общепроизводственным службам относят инструментальный отдел, центральный инструментальный цех и склад, к цеховым - инструментальные участки и инструментально-раздаточные кладовые в основных и вспомогательных цехах. Общепроизводственные службы обеспечивают оснасткой все инструментальные цеховые службы, которые, в свою очередь, через мастеров и бригадиров обеспечивают рабочие места. Руководит инструментальным хозяйством инструментальный отдел, подчиненный главному технологу (начальнику технического отдела) или главному инженеру. В центральном инструментальном цехе изготавливают и ремонтируют оснастку, затачивают особо сложные инструменты, утилизируют инструменты. Центральный инструментальный склад осуществляет учет, хранение, получение и выдачу инструмента цехам. Часть функций по подготовке инструмента, особенно ручного и несложного, выполняется рабочими, использующими эти инструменты. Смена инструмента на станках входит в обязанности рабочих, занятых на этом оборудовании, если их квалификация высока. На некоторых предприятиях инструментальное хозяйство рассредоточено по цехам, функциональное руководство осуществляет технологический отдел, техническое обеспечение - отдел главного механика и ремонтно-механический цех, снабжение - отдел материально-технического снабжения.
Владимир МОСЯГИН, д-р эконом. наук, проф. СПбГЛТУ