Куда девать лиственную древесину? Часть 3
Производство древесного угля
В этой статье рассмотрено такое направление переработки лиственной древесины, как производство древесного угля. Его можно эффективно сочетать с производством топлива для каминов и печей - дров и брикетов.
Часть 1. Производство дров и брикетов, их реализация на экспорт
Часть 2. Оборудование для изготовления дров
Часть 4. Производство древесной шерсти
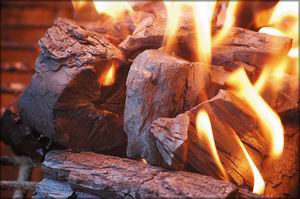
Березовая, ольховая и осиновая древесина может быть сырьем для производства древесного угля. Для традиционного пиролиза в основном используют березовую древесину, так как при ее переработке обеспечивается более высокий выход качественного кускового угля, чем при переработке ольхи и осины; древесина этих пород также используется для изготовления брикетов, из которых в печах получают уголь. При обработке брикетов на пиролизных установках можно добиться более высокой производительности, чем при обработке поленьев, но самое главное: пережженные брикеты на мировом рынке ценятся значительно выше обычного древесного угля.
На рис. 1 приведены данные об объемах производства древесного угля десятью ведущими странами в этой области. В основном это развивающиеся страны, которые используют древесный уголь для удовлетворения собственных потребностей. Например, в Бразилии древесный уголь широко применяется в качестве восстановителя в металлургии, благодаря чему обеспечивается наиболее высокое качество чугуна, а в Китае древесный уголь используется для получения сверхчистого кремния.
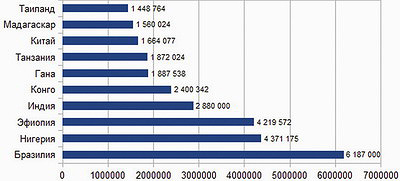
Рис. 1. Десять ведущих стран – производителей древесного угля по
состоянию на 2015 год, т/год
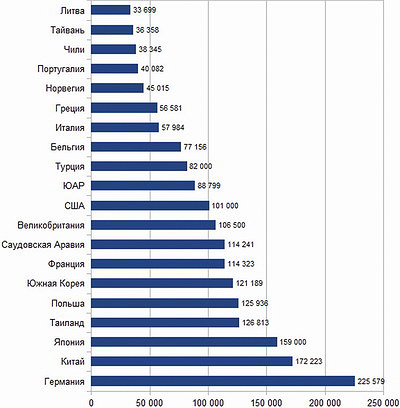
Рис. 2. Двадцать ведущих стран – импортеров древесного угля по состоянию
на 2015 год, т/год
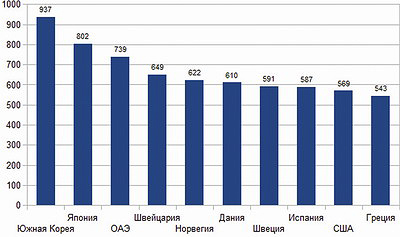
Рис. 3. Десять ведущих стран – импортеров древесного угля по средней
цене по состоянию на 2015 год, $/т
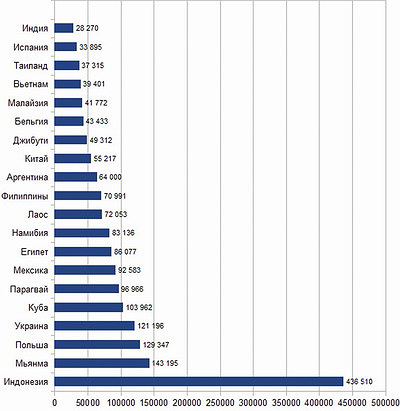
Рис. 4. Двадцать ведущих стран – экспортеров древесного угля по
состоянию на 2015 год, т/год
На десять стран, данные по которым приведены на рис. 1, приходится больше половины мирового производства древесного угля, причем получают его самыми примитивными и экологически «грязными» способами кучного углежжения или в простых печах.
Во многих развитых странах уголь широко используется для приготовления пищи, в том числе в ресторанах, а также в качестве топлива для каминов и печей, и его производство в мире с 2006 по 2015 год выросло с 44,7 до 52,4 млн т. На рис. 2 представлен рейтинг двадцати ведущих стран - импортеров древесного угля.
По стоимости импорта лидером является Япония ($127,6 млн), на втором месте Южная Корея ($113,6 млн), на третьем Германия ($106,6 млн). На рис. 3 приведен рейтинг стран - импортеров древесного угля по средней цене, $/т. Чем выше этот показатель, тем больше в объеме импорта доля наиболее дорогих сортов древесного угля.
Ввиду малых объемов импорта (менее 10 тыс. т в год) в рейтинг не включены Российская Федерация, которая импортировала в 2015 году древесный уголь по средней цене $806/т, и Иран, ввозивший его по средней цене $1943 за тонну.
На рис. 4 приведены данные по объемам экспорта двадцати ведущих стран - экспортеров древесного угля; с большим отрывом лидирует Индонезия. А вот, если составить рейтинг по стоимости экспорта, то отрыв Индонезии (($181,9 млн) от идущего вторым Китая ($77,8 млн) уже не так значителен. Обусловлено это более высокой средней ценой экспортированного из Китая угля.
Российская Федерация, которая экспортировала в 2015 году 23 тыс. т (средняя цена одной тонны $266) из произведенных в стране 53 тыс. т древесного угля, не входит в двадцатку ведущих экспортеров. А вот Украина в этом рейтинге (рис. 4) на четвертом месте.
Любопытно, что Польша есть в рейтингах как ведущих импортеров, так и ведущих экспортеров с примерно одинаковым объемом импорта и экспорта угля, причем средняя цена экспортированного угля выше средней цены импорта в два раза. В той же базе данных указана стоимость польского экспорта древесного угля в 2015 году: около $73 млн, - а стоимость импорта около $36 млн. Физический объем импорта - 126 тыс. т, экспорта - 129 тыс. т. Впрочем, вероятно, можно говорить не о банальном реэкспорте, а о том, что посредники выполняют сортировку и фасовку угля в тару для потребительского рынка, а также берут на себя функции дистрибуторов по всей Европе. И все же разница между доходами тех, кто умеет производить, и тех, кто умеет продавать, впечатляет.
Но основная причина разброса средних цен все же кроется в том, что под одним и тем же названием в статистике фигурируют три разных продукта: кусковой уголь, брикеты из древесно-угольной пыли и уголь из древесных брикетов («огатан»).
В процессе производства получают кусковой уголь разных фракций. В России, а также Украине и Белоруссии действует ГОСТ 7657-84 «Уголь древесный. Технические условия». В настоящее время в развитых зарубежных странах древесный уголь применяется прежде всего для приготовления пищи, требования к нему определены отдельными стандартами, такими как BS EN 1860, DIN 51749-Н (причем требования ГОСТ 7657-84 жестче, чем нормативы этих документов).
Товарной продукцией считается древесный уголь, размеры фракций которого находятся в диапазоне от 20 до 80 мм. Согласно британскому стандарту BS EN 1860, содержание в продукте углерода должно быть не менее 75%, влаги - менее 8%, золы - менее 8%.
Уголь мелкой фракции (менее 20 мм), получаемый на предприятиях в ходе производства, механически отделяется от кондиционного и продается как отсев. В России оптовые цены на тонну отсева - от 5000 руб. Основными потребителями подобной продукции являются промышленные предприятия (в том числе производители брикетов BBQ). Уголь нормальной фракции фасуют в бумажные пакеты и продают как топливо для грилей и мангалов. В Великобритании подобный уголь называют Lumpwood Charcoal, чем подчеркивается его отличие от брикетов BBQ.
Несмотря на ограничения британского стандарта, отвечающие определенным требованиям куски угля, размеры которых превышают 80 мм, высоко ценятся профессиональными поварами и считаются элитным углем «ресторанного» сорта (restaurant grade charcoal).
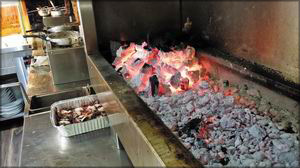
Рис. 5. Качественный уголь востребован прежде всего
кулинарами и предприятиями фастфуда
Цены предложения за тонну «ресторанного» угля на Amazon.co.uk варьируются от 1200 до 2600 фунтов стерлингов (при покупке целой палеты цена, разумеется, значительно ниже). Так, компания T2 Square Ltd, которая является и изготовителем, и продавцом, предлагает уголь по цене 510 фунтов за палету с 55 пакетами по 15 кг, то есть примерно по 618 фунтов за тонну.
Впрочем, в Великобритании трудно найти кусковой уголь, который не позиционируется в качестве продукта класса премиум и ресторанного угля. Кусков размером больше 80 мм в нем может и не быть, но средний размер кусков значительно превышает аналогичный показатель обычного угля.
Говоря о наиболее дорогих сортах угля, нельзя не упомянуть высоко ценящийся в Японии и Южной Корее уголь бинчотан (bincho-tan), или белый уголь. В качестве сырья для его получения используются ветки дуба убамэ, а также некоторых других разновидностей дуба. Белым уголь получается из-за того, что после извлечения из печи раскаленные докрасна ветки быстро гасят, покрывая смесью сухой земли, песка и пепла. Такой уголь твердый, плотный, издает металлический звук при ударе.
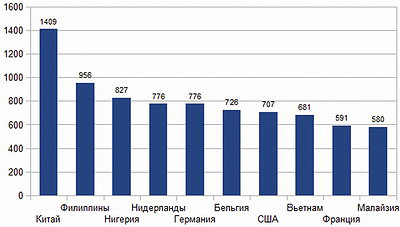
Рис. 6. Десять ведущих стран – экспортеров древесного угля по средней
цене по состоянию на 2015 год, $/т
Считается, что при сгорании этот уголь придает особый аромат блюдам. Загорается он легко, горит долго, что обеспечивает ему популярность у японских шеф-поваров. Многие японские заведения, где подают унаги (жареного угря) и якитори (курицу на шпажках), в рекламе подчеркивают, что готовят на бинчотане. Кроме того, этот уголь используют при производстве косметики, а в силу его абсорбирующих свойств - в качестве освежителя воздуха и очистителя воды (например, продаются бутылки с водой, в которую помещена ветка бинчотана).
В Японии основная часть бинчотана производится в префектуре Вакаяма, где и была изобретена технология его получения. Такой уголь называют Kishu Bincho-tan, чтобы подчеркнуть его отличие от остального бинчотана. Одна из местных компаний предлагает бинчотан по цене от $247 за коробку (15 кг), то есть примерно по $16500 за тонну. Производители угля из Китая, Малайзии и Вьетнама предлагают свои, более дешевые, разновидности бинчотана: тонну угля из Китая за $1500-2500, из Малайзии за $1000-1300, из Вьетнама за $800-900. В качестве сырья зачастую используют древесину эвкалипта или другой подходящей породы. Но главное условие при изготовлении бинчотана соблюдается обязательно: уголь покрыт белой пылью.
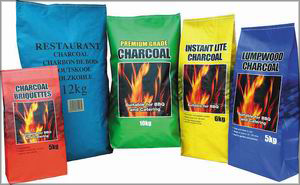
Рис. 7. Упаковки с кусковым углем разных марок
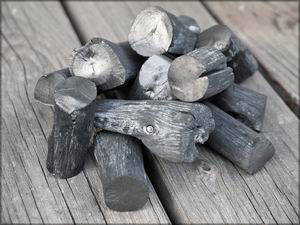
Рис. 8. Уголь бинчотан
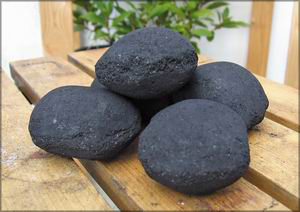
Рис. 9. Британские брикеты BBQ
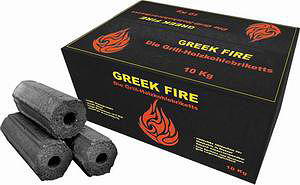
Рис. 10. Уголь из брикетов Pini & Kay обычно
поставляется в коробках по 10 кг
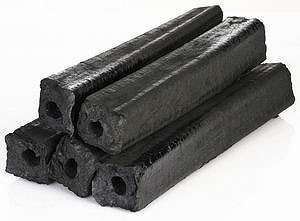
Рис. 11. Уголь польской фирмы Gallus, изготовленный
из брикетов
На мировом рынке продается также древесный уголь в виде брикетов из древесно-угольной пыли, или брикетов барбекю (BBQ). У них интересная история происхождения. Официально эти брикеты были изобретены и запатентованы в 1897 году Элсвортом Цвоейером из Пенсильвании. Однако распространение они получили благодаря... Генри Форду. Еще в 1919 году компания Форда достигла объема продаж автомобилей знаменитой «модели Т» 1 млн шт. Проблема была в том, что на изготовление каждого автомобиля расходовалось примерно 0,25 м3 древесины - из нее изготавливались рама, приборная панель, руль и колеса. Форд обзавелся лесными угодьями и в начале 1920-х годов построил собственный лесозавод и фабрику по изготовлению деталей в г. Кингсфорд (штат Мичиган). Когда возник вопрос с утилизацией образующихся отходов, Форд, как новаторски мыслящий бизнесмен, выбрал производство древесно-угольных брикетов. Технологию производства брикетов разработал химик Орин Стаффорд из Университета Орегона, а фабрику по выпуску этих брикетов для Форда спроектировал не кто иной, как Томас Эдисон, знаменитый американский изобретатель. Брикеты реализовывались исключительно через дилерскую сеть Форда, а созданное предприятие получило название Ford Charcoal. Особенно большим спросом эти брикеты пользовались после Второй мировой войны, при миграции населения в пригороды и появлении современных грилей.
В 1951 году группа инвесторов выкупила завод угольных брикетов у Ford Motor Company и переименовала его в Kingsford Charcoal. В настоящее время доля этой компании на американском рынке угольных брикетов составляет 80%. Ежегодно компания перерабатывает около 1 млн т древесных отходов.
Состав брикета Kingsford (по состоянию на январь 2016 года): древесно-угольная пыль (топливо), каменный уголь (топливо), известь (отвердитель, который также обеспечивает белый цвет золы, что говорит о готовности гриля), кукурузный крахмал (связующее), бура и древесные опилки (для ускорения воспламенения).
За пределами США древесно-угольные брикеты тоже весьма популярны. В нашей стране они известны как брикеты BBQ, или «подушечки», и производят их, как правило, из угольного отсева.
Если сравнивать цены на кусковой уголь и брикеты BBQ в Великобритании, то в рознице стоимость брикетов оказывается на уровне цен на многие марки кускового угля даже ресторанного сорта: 1,2-1,25 фунта за килограмм, или 1200-1250 фунтов за тонну. При покупке палеты (50 пакетов по 10 кг) брикетов марки Long Burn цена получается 597,5 фунтов за тонну, то есть чуть ниже цены высокосортного кускового угля.
За что же ценят брикеты? Во-первых, за эстетические свойства: зрительно для многих потребителей калиброванные «подушечки» гораздо привлекательнее кускового древесного угля. К тому же благодаря высокой прочности угольные брикеты не повреждаются при транспортировке и сохраняют товарный вид, тогда как в пакете с кусковым углем зачастую образуется много мелочи, которую невозможно использовать. Во-вторых, за высокую плотность, которая обеспечивает продолжительное горение - около трех часов, причем за счет однородности продукта тепло распределяется равномерно. Одинаковый размер брикетов позволяет точно дозировать их исходя из целесообразности. В-третьих, угольные брикеты не дымят.
Несмотря на все эти качества, профессионалы кулинарии, как правило, не любят использовать брикеты BBQ. Так, например, британский шеф-повар Корнелиус Викинс, специалист по готовке на открытом воздухе, говорит, что брикеты - скорее источник тепла, чем топливо для приготовления пищи. В брикетах содержатся химические добавки, которые придают приготовленной на них пище непредсказуемый привкус. Кроме того, г-н Викинс указывает, что на некоторых упаковках брикетов написано: «Не использовать золу для компоста», что внушает еще больше сомнений в пригодности их для гастрономических целей. По мнению британского кулинара, кусковой уголь, который сохраняет вид и форму исходного куска древесины, является наиболее естественной формой древесного угля, он горит жарче, чем брикеты, позволяет лучше контролировать процесс, после сгорания оставляет меньше золы и придает пище характерный «копченый» вкус.
К тому же брикеты трудно разжечь. Специально для их розжига изобретены приспособления, называемые стартерами, используются жидкости и свечки. Из-за присутствия минеральных компонентов выход золы достигает 20%, что крайне неудобно для ресторанов, которые используют уголь в больших объемах.
Представленный на рынке кусковой уголь для гастрономических целей сильно различается по качеству. Даже на британском рынке немало продукции невысокого качества, с низким содержанием углерода и повышенным содержанием летучих. Подобный уголь дымит, горит как древесина и сгорает быстро, что обусловлено, как правило, кустарными технологиями производства. По оценке компании Green Power, лишь 5% древесного угля в мире изготавливается промышленным способом, с соблюдением требований к режимам сушки и пиролиза древесины. Низкосортный кусковой уголь, изготовленный «кустарями», проигрывает брикетам. Качественный же уголь как минимум не уступает брикетам по длительности горения и теплоотдаче. Можно сказать, что как у кускового угля, так и у брикетов BBQ хорошие перспективы на рынке. У каждого продукта свой потребитель.
Однако есть и третий вид древесно-угольной продукции: уголь, изготовленный из древесных брикетов. В отличие от производства брикетов BBQ, древесные частицы сначала без всякого связующего прессуют в брикеты, а потом подвергают пиролизу. Полученный угольный брикет характеризуется довольно высокой прочностью и даже издает металлический звук при ударе.
Спрос на подобный уголь впервые возник в Японии, где его называют «огатан». Основные его потребители - японские рестораны. Однако спрос растет и в других странах Юго-Восточной Азии, а также за ее пределами. В настоящее время существует множество мелких и крупных производств угля из брикетов в Китае, Индонезии и Вьетнаме, которые предлагают брикеты по $600-800 за тонну с завода (на основе анализа предложений на Alibaba.com). Есть сведения, что в Китае на долю этого сорта угля приходится 70% всего объема производства. Достоинства угля из брикетов уже оценили рестораторы в Греции, Турции и на Ближнем Востоке. А вот на европейском рынке этот уголь только завоевывает популярность. Тем не менее произведенные в Польше брикеты Gallus продаются в Великобритании в розницу по 17,90 фунта за коробку (10 кг), то есть по 1790 фунтов за тонну. Брикеты Big K на Ebay предлагаются в коробках по 10 кг за 30,69 фунта, то есть по цене больше 3000 фунтов за тонну, что вдвое дороже элитных марок кускового угля этой же фирмы.
Если говорить об оптовых ценах, то компания Log Barn продает брикеты по 545,48 фунта за палету (40 коробок по 10 кг), то есть по 1364 фунта за тонну. Таким образом, уголь из брикетов вдвое дороже качественного кускового угля и брикетов BBQ. Чем это обусловлено?
Изготовитель углевыжигательных установок украинская компания Green Power, пропагандирующая производство угля из брикетов, отмечает, что этому углю присущи такие свойства «идеального» древесного угля, как высокая плотность и высокое содержание углерода (не менее 85%), устойчивость к механическим воздействиям, однородный фракционный состав, низкая зольность.
Традиционная технология позволяет получать уголь с близкими характеристиками только из древесины очень высокой плотности. При брикетировании в результате искусственного изменения плотности материала можно производить «идеальный» уголь даже из древесины ольхи, осины и тополя.
Уголь из брикетов горит дольше, чем обычный уголь, и дает больше тепла. Если горение брикетов BBQ продожается 3-3,5 ч, качественного березового угля - до 4 ч, угля из древесины «железного дерева» - до 6 ч, то уголь, изготовленный из брикетов, горит 5-6 ч, в некоторых случаях до 10 ч. За это качество, за одинаковый размер кусков, отсутствие дыма и ароматов, а также за малый объем золы уголь из брикетов высоко ценят заведения быстрого питания.
Впрочем, есть у подобного угля один, хотя и не очень существенный, недостаток: в силу высокой плотности он медленно разгорается, так что для розжига иногда приходится комбинировать его с кусковым углем.
Необходимо заметить, что традиционно уголь получают из брикетов Pini & Kay шестигранной формы, поскольку на предприятиях в Азии преобладает соответствующий тип шнековых прессов. Покупатели, как правило, целенаправленно ищут уголь шестигранной формы. Тем не менее качественный уголь можно изготавливать и из брикетов, полученных на ударно-механических прессах (C.F. Nielsen, Di-Piu и т. п.). К примеру, угольные брикеты фирмы Gallus изготавливаются на прессах именно такого класса (см. рис. 11).
Производство древесного угля
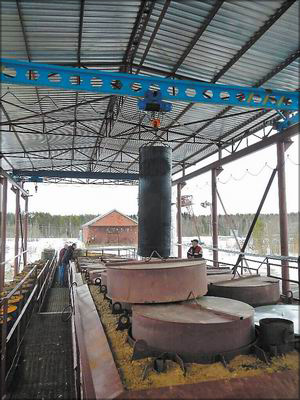
Рис. 12. В процессе работы установок «Эколон» все переместительные операции выполняются краном
Как было отмечено выше, основной объем древесного угля в мире производится кустарными методами - при пережигании древесины в кучах и в простейших печах. Кустарей немало даже в развитых странах. Таким образом, у индустрии древесного угля колоссальный потенциал развития, ведь промышленными методами можно производить высококачественный уголь, причем меньшей себестоимости и без вреда для окружающей среды и здоровья рабочих.
В России древесный уголь в основном получают в мобильных печах, которые устанавливают прямо в лесу для утилизации лесосечных отходов. У этих печей крайне низкая производительность, и основная цель их использования - очистка делянок. Поэтому подобное оборудование в этом обзоре не рассматривается.
На каком же оборудовании можно производить уголь безопасными методами и в промышленных объемах? Вот пять основных типов установок, которые в настоящее время выпускаются серийно:
- установки с вертикальными выемными ретортами производства ЗАО «Лонас технология», а также УПР-90, МПРУ, Россия;
- установки с вертикальными выемными ретортами CG-2000 (Carbo Group), Нидерланды;
- установки с горизонтальными выемными ретортами Ван Мариона: VMR Systems, Нидерланды, и УМТ-2М/УМТ-3, Украина;
- установки с выемными ретортами УП-4 «Евро», Украина;
- установки Lambiotte, Бельгия.
Распространению технологии с вертикальными выемными ретортами в нашей стране способствовал Юрий Давидович Юдкевич, один из авторов установок «Поликор» и «Эколон». Он много сделал для развития в России промышленного производства древесного угля. Его статьи неоднократно публиковались в «ЛПИ». К сожалению, в прошлом году Юрия Давидовича не стало...
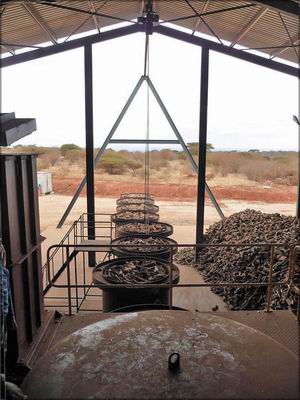
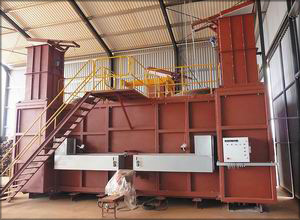
Вот как изобретатель описывал установки «Эколон» и подобные им: «В основе их технологического решения лежит использование помещаемых в обогреваемую камеру вертикально реторт. Реторты закрыты сверху, а внизу у них есть отверстия для выхода паров и газов, которые отводятся прямо в топку. Продукты горения омывают реторты в пиролизной камере. Затем горячие газы проходят через камеру сушки. Такое решение позволяет использовать топливо эффективно»2.
Сжигание побочных продуктов пиролиза в топке позволяет в летнее время обеспечить работу установок «Эколон» без использования дополнительного топлива, а в зимнее - в качестве топлива использовать отходы деревообрабатывающих производств. На этом оборудовании можно работать с сырыми дровами, которые сушат в тех же ретортах, в сушильном отделении. В конструкции установки «Эколон 5.2» по 10 ячеек для сушки и пиролиза. Реторта с загруженными в нее дровами сначала помещается краном в ячейку для сушки, спустя определенное время (зависит от влажности и породы древесины) ее переставляют в ячейку для пиролиза. Пиролиз продолжается 8-10 ч. Затем реторту вынимают и ставят рядом с установкой для охлаждения, а на освободившееся место тут же ставят следующую реторту, и процесс не прекращается. Из охлажденной реторты уголь разгружают в специальную воронку (рабочее положение реторт «Поликора» и «Эколона» - загрузочным люком вниз, и для их разгрузки нужно лишь открыть люк над воронкой, из которой уголь поступает на фасовку в биг-бэги или на сортировку и фасовку в пачки. Производительность установки «Эколон 5.2» в среднем 5,2 т готового угля в сутки. Таким образом, с одной установкой теоретически достижим объём производства 1800 т угля в год.
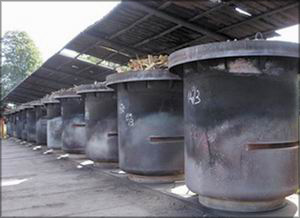
Рис. 14. Реторты на сушильном борове на предприятии в России
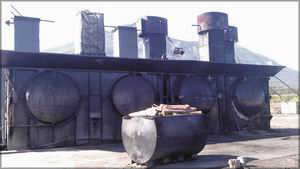
Рис. 15. Две установки VMR на предприятии в Сербии. На переднем плане реторта с дровами
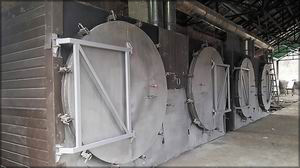
Рис. 16. Две установки УМТ на предприятии на Украине
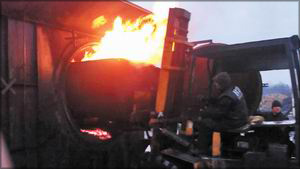
Рис. 17. Выгрузка реторты Ван Мариона из камеры на предприятии в г. Болевац, Сербия
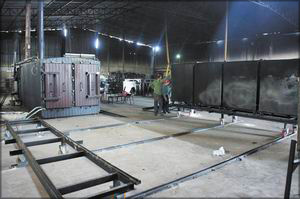
Рис. 18. Установка УП. Справа вагонетки на рельсовой платформе
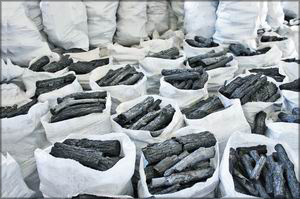
Рис. 19. Расфасованный вручную элитный кусковой уголь
В России выпускались аналогичные «Эколону» установки УПР-90, которые были рассчитаны на производство 3 т продукции в сутки, или 90 т в месяц. Самый крупный в стране производитель древесного угля - компания «СевЗапУголь» располагает шестью подобными установками, построенными в 2004-2008 годах. То есть мощность производства превышает 6000 т угля в год. Аналогом «Эколона» являются и установки семейства МПРУ, которые изготавливают в уральском г. Кушве.
Двухретортные установки CG-2000 выпускаются компанией Charbon Engineering, правопреемницей голландской компании Carbo Group. Использование двух вертикальных реторт с общей топкой позволяет не прерывать горение при смене реторт. Все выделяемые из реторт газы и пары отводятся в топку, где сжигаются с получением тепловой энергии. Внешняя подача топлива (мазута) требуется только при пуске установки, далее процесс протекает автономно, без добавления топлива.
Избыточное тепло используется для сушки и подогрева дров перед подачей в установку. С этой целью недалеко от установки сооружают сушильный боров, на который устанавливают реторты, и топочные газы, проходящие по борову, обогревают реторты.
В самой установке осуществляется только пиролиз. Технология предполагает, что влажность загружаемых дров не превышает 20%, что вынуждает переработчиков сначала сушить сырье в штабелях, а затем подсушивать на борове перед подачей на пиролиз.
Объем реторты 4,5 м3. Приплюснутая, бочкобразная форма и прорези по бокам для захвата вилами позволяют выполнять основную часть манипуляций с ретортами с использованием вилочного погрузчика. Кран используется только для загрузки реторт в установку и извлечения из нее. Использование высушенного сырья обеспечивает довольно короткий цикл пиролиза: 8-10 ч, несмотря на то что диаметр у реторт больше, чем в российских установках. На одной установке можно за год произвести 900-1000 т угля. На некоторых предприятиях работают две подобные установки и больше, что позволяет эффективно использовать кран, погрузчик и другое вспомогательное оборудование.
Завод Industrie Bois Rousseau в г. Дюссак является самым крупным предприятием во Франции, работающим по описанной технологии. В год здесь производят 10 тыс. т угля. Вот как представлен производственный процесс на сайте этой компании. Сначала бревна сушат на складе в течение двух лет. Затем на дровокольной линии получают из них поленья длиной не более 30 см, которые пропускают через сепаратор для отделения щепок и отвалившейся коры и загружают в реторты. В течение четырех часов реторты находятся на сушильном борове, нагреваются до 100°С, после чего их загружают в одну из установок для пиролиза. В обороте на предприятии постоянно находятся 120 реторт. После завершения пиролиза выгруженную реторту забирает вилочный погрузчик и помещает на песчаную площадку для охлаждения в течение 40-50 ч. Затем погрузчик перевозит ее на крытый склад и выгружает уголь, переворачивая реторту, для чего вилы снабжены механизмом поворота. На складе уголь выдерживают еще 24 ч, чтобы гарантированно избежать его самовоспламенения, после чего подают на линию сортировки (от кусков отделяются пыль и отсев) и фасовки в бумажные мешки по 4 кг, 20 л и 50 л. Каждый день завод выпускает 8 тыс. мешков угля. Пиролиз идет круглосуточно и безостановочно в течение всего года.
Установки с горизонтальными ретортами Ван Мариона - также разработка голландских специалистов. Как и описанная выше, эта система является двухретортной, что обеспечивает непрерывное горение топки. Правами на эту технологию в настоящее время обладает компания VMR Systems, однако украинская ООО «Импекс Трейдинг Продакшен» изготавливает аналогичные установки под марками УМТ-2М и УМТ-3, они отличаются большим размером реторт. По данным украинской компании, производительность установки УМТ-2М 35-45 т угля в месяц, установки УМТ-3 - до 50 т в месяц. Эти установки могут работать на сырых дровах влажностью от 50%, но при этом за счет сушки сырья в камере производительность снижается на 15-20%.
В г. Болевац, на сербском предприятии, оснащенном установками VMR, используют сухие буковые дрова влажностью не более 20%. Продолжительность цикла пиролиза - 8 ч. При непрерывной работе установки дополнительное топливо не требуется. Манипуляции с ретортами осуществляют вилочным погрузчиком. В этом как достоинство, так и недостаток технологии. Дело в том, что выгружаемый из печи раскаленный уголь при контакте с воздухом вспыхивает, из-за чего в метре от кабины погрузчика появляются длинные языки пламени. Реторту накрывают стальной крышкой, для чего рабочим приходится приближаться к ней. Все эти манипуляции отнюдь не безопасны для персонала.
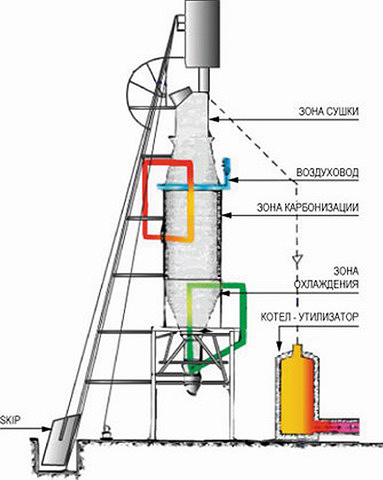
Рис. 20. Схема установки Lambiotte
После охлаждения реторту разгружают, повернув вилы погрузчика. При разгрузке реторты Ван Мариона уголь подвергается меньшим ударным нагрузкам, по сравнению с углем, получаемым в вертикальных ретортах, что положительно сказывается на выходе годной фракции.
Установки УП-4 «Евро» украинской компании Green Power являются четвертым поколением печей этого изготовителя. Предыдущие версии нередко подвергались критике пользователей, поэтому компания подчеркивает в рекламе, что в УП-4 устранены все конструкционные недостатки предыдущих версий.
Установки УП можно классифицировать как двухкамерные с выемными ретортами-вагонетками. В одну камеру загружают 3-4 вагонетки. Каждая камера может работать в режиме сушки и нагрева древесины и в режиме пиролиза, причем в камерах разные режимы, что позволяет осуществлять процесс непрерывно. Возможность сушки и нагрева допускает использование сырых дров, хотя изготовитель отмечает, что при влажности сырья выше 50% производительность оборудования снижается. Продолжительность полного цикла сушки и пиролиза в УП-4 «Евро» - 18-30 ч. Производительность в зависимости от влажности древесины, породы, размера кусков составляет 25-45 т угля в месяц для УП-4 «Евро» и до 55 т в месяц для УП-4 «Евро-М»; при производстве угля из брикетов производительность до 60 и 70 т продукции в месяц соответственно.
Процесс в значительной степени автоматизирован, для чего каждая установка УП-4 оснащена восемью термопарами. Автоматика позволяет оптимизировать режим использования тепла и контролировать факторы, которые могут повлиять на качество продукции, выбросы вредных веществ в атмосферу и работоспособность печи. Пульт дистанционного управления дает возможность оператору, находящемуся в отдельном помещении, контролировать работу одной или нескольких установок и при необходимости переключать режимы; в случае возникновения угрозы аварийной ситуации можно мгновенно остановить работу печи.
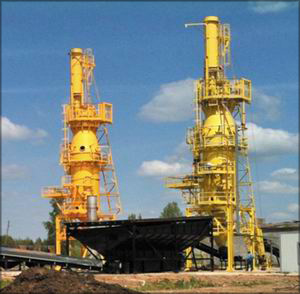
Рис. 21. Установки Lambiotte на заводе Livanu Karbons, Латвия
Для перемещения вагонеток с участка подготовки сырья к установкам и готовой продукции после пиролиза от установок на участок охлаждения используются рельсовые платформы с электролебедками, с помощью которых горячие вагонетки вытаскивают из камеры. Разгрузка и загрузка камеры, таким образом, могут быть осуществлены довольно быстро.
Компанию Green Power много критиковали за то, что загрузка сырья в вагонетки и выгрузка угля из них осуществляются вручную. Однако при производстве элитного кускового угля, сохраняющего форму полена или ветки, а особенно при производстве угля из брикетов, эта особенность технологии Green Power позволяет избежать повреждения продукции при выгрузке. Повышенные затраты на труд в этом случае с лихвой компенсируются высокой ценой продукции.
Наиболее сложным, технически совершенным и производительным оборудованием для производства кускового угля считаются установки Lambiotte или аналогичные им. Различают две технологии Lambiotte: SIFIC - с производством побочных продуктов за счет конденсации летучих соединений, CISR - без производства побочных продуктов. Оба метода были 70 лет назад реализованы на предприятиях компании Lambiotte во Франции (крупном производстве, выпускавшем 27 тыс. т угля в год) и в Бельгии. В настоящее время разработчиком и его лицензиатом предлагаются в основном установки CISR, как наиболее экономически эффективные.
Оба варианта установок предполагают использование высокой стационарной реторты, в которую сверху скиповым подъемником загружается сырье. Постепенно опускаясь, сырье проходит через зону сушки и нагрева, где нагревается поднимающимися из зоны пиролиза пиролизными газами и парами, затем оказывается в зоне пиролиза (карбонизации). Полученный уголь поступает в расположенную внизу зону охлаждения, а после выгружается из установки на находящийся под ней конвейер. При изготовлении угля по технологии CISR образующиеся пиролизный газ и летучие продукты сжигаются в отдельной топке, и продукты горения поступают в реторту, за счет чего установка после пуска работает автономно, без питания топливом. Во время процесса в установку поступает ровно столько воздуха, сколько необходимо для сжигания пиролизных газов и паров, что позволяет минимизировать потери нелетучего углерода. Процесс автоматизирован и механизирован. Оператор осуществляет контроль и управление, сидя перед дисплеем в кабине недалеко от установки.
Единичная мощность установки CISR - от 2 до 6 тыс. т в год. Срок службы - 15 лет.
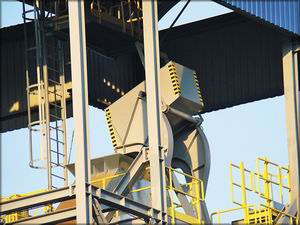

Лицензию на тиражирование технологии на территории стран Балтии и СНГ имеет латвийская компания Balt Carbon, которая уже реализовала в Латвии один проект: на заводе Livanu Karbons работают две реторты суммарной производительностью 5 тыс. т угля в год.
Влажность используемого древесного сырья не должна превышать 25%, длина сырья должна быть не больше 30 см, а толщина - не больше 10 см. Для обеспечения нормальной работы установки требуется участок подготовки сырья. На базе реторт CISR 2000 компания Balt Carbon разработала техническое решение для одновременного производства продукции и энергии. Две реторты вырабатывают 0,5 МВт электрической и 1,75 МВт тепловой энергии.
В Польше компания Ozen Plus в 2011 году построила крупный завод, используемый на нем технологический процесс отличается от процесса CISR Lambiotte, но основан на том же принципе непрерывного производства в стационарной реторте. Завод по праву считается самым современным в Европе и одним из крупнейших в мире. В год здесь производят 15 тыс. т угля, 5 тыс. т брикетов BBQ и 52 тыс. МВт-ч электроэнергии. Для производства электроэнергии используются как парогазовые продукты пиролиза, так и биомасса (древесная щепа и солома), сжигаемые в отдельном котле.
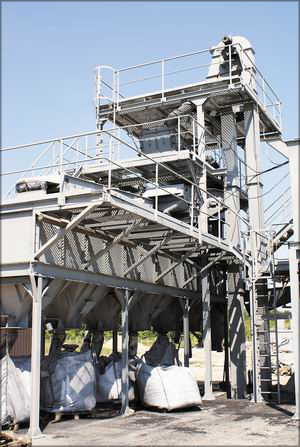
Рис. 23. Установка сортировки угля на сербском
предприятии BTR exp.
Процесс осуществляется в двух ретортах. На базе каждой реторты выстроен технологический поток, включающий двухстадийную сушку сырья, пиролиз и охлаждение угля. Сначала бревна длиной до 2,5 м (граб, бук, ясень, береза и ольха) выдерживаются на складе в течение трех месяцев, что позволяет снизить и выровнять влажность. Затем бревна подаются на накопитель одного из двух технологических потоков, откуда дозируются на подающий конвейер гильотинной установки Holtec, на которой пачка бревен нарезается на поленья. Поленья транспортируются конвейером в камеру первичной сушки и нагрева, откуда после обработки поступают в скип, который транспортирует их к люку спаренной сушильной установки. В вертикальной сушилке древесина подвергается сушке горячим воздухом. Затем с помощью другого скипа загружается сверху в реторту. В реторте осуществляются пиролиз и первичное охлаждение угля. Выгружаемый из реторты уголь поступает в один из пяти бункеров для охлаждения. Готовый уголь от двух технологических потоков проходит сортировку (просеивание). Качественный кусковой уголь поступает на станцию фасовки в бумажные мешки. Прошитые мешки укладывают на палету, которую обматывают пленкой и отправляют на склад.
Отсев угля и пыль используются для производства брикетов «барбекю». Отсев измельчается в пыль, которая затем смешивается с композицией на основе крахмала. Из полученной смеси формуются «подушечки» брикетов, подвергающиеся сушке, готовый продукт фасуется в бумажные пакеты.
Аналогично может быть организована переработка отсева на любом пиролизном предприятии, даже небольшом.
Итак, производство древесного угля - это весьма перспективный бизнес с большим экспортным потенциалом. Наиболее привлекательным направлением является производство угля из брикетов на экспорт. Автору пока неизвестно ни одно предприятие полного цикла в России, где было бы и производство, и пиролиз брикетов. Интерес к получению угля из брикетов пока проявляют в основном небольшие пиролизные предприятия, которые закупают брикеты на стороне, у небольших переработчиков опилок. В результате накладные и транспортные расходы съедают значительную часть прибыли.
Намного больший экономический эффект могло бы дать создание в местах, где концентрируются большие объемы невостребованной лиственной древесины, производственных комплексов, включающих участки брикетирования и пиролиза. Уголь из лиственной древесины всегда будет пользоваться спросом у покупателей, использующих его для приготовления пищи. В первую очередь в переработку целесообразно пускать древесину осины и лесосечные отходы. Березовая древесина может быть использована для производства кускового угля.
Резюмируя, следует отметить, что существующие технологические решения позволяют организовать производство в промышленных масштабах.
Артем ЛУКИЧЕВ