Рубительные машины: неутомимые труженицы
Рубительные машины - широко известное оборудование лесозаготовительного и деревообрабатывающего производств. Они используются для переработки деловой балансовой древесины и предварительно окоренных отходов лесопильного производства в технологическую щепу, а также для получения топливной щепы из порубочных остатков, низкотоварной и дровяной древесины.
В зависимости от вида древесного сырья, измельчаемого в щепу, применяются разные виды рубительных машин, которые различают по мобильности, типу рабочего органа, виду и числу используемого режущего инструмента, способу и направлению подачи древесного сырья, форме загрузочных устройств, способу отбора щепы, виду энергии, используемой для привода рабочего органа.
По признаку мобильности рубительные машины (РМ) подразделяются на стационарные и передвижные. Стационарные РМ эксплуатируются на индивидуальных неподвижных основаниях (фундаментах). Рубительные машины, смонтированные на подвижных основаниях, принято называть передвижными установками. Передвижные рубительные установки могут быть автотракторными, плавучими, железнодорожными и т. д. Автотракторные установки, в свою очередь, подразделяются на самоходные, прицепные, полупередвижные.
Наибольшее значение для рубки на щепу имеют следующие физико-механические свойства древесины: плотность, влажность, физико-механическая прочность в разных направлениях ортогональной системы координат, коэффициенты трения древесины по древесине и металлу. Плотность абсолютно сухого вещества древесины не зависит от породы и составляет 1,54 т/м3. Но плотность абсолютно сухой древесины зависит от породы и определяется ее анатомическим строением, наличием пустот внутри волокон и в межклеточном пространстве. Влага сильно влияет на физико-механические свойства древесины, модули упругости, коэффициенты трения, предел прочности. Влажность поступающей в рубку древесины часто сильно колеблется, что зависит от сезона года, метеоусловий, способа хранения и транспортировки сырья. С повышением влажности модуль упругости и прочность древесины снижаются, что приводит к уменьшению удельной работы и мощности, потребной на выполнение резания.
Поскольку важнейшие показатели процесса переработки древесины в технологическую щепу формируются механизмом резания рубительной машины, в качестве основного классификационного признака обычно принимается конструктивная схема механизма резания (режущего органа) машины. По этому признаку РМ можно разделить на три основных класса: дисковые, барабанные и конические.
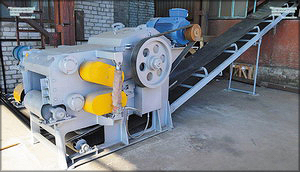
В дисковых рубительных машинах механизм резания (режущий орган) выполнен в виде вращающегося диска с расположенными на его рабочей поверхности режущими элементами. По типу рабочей поверхности диска выделяют РМ с плоским или профилированным (геликоидальным) диском. У рубительных машин сложный механизм резания, при котором плоскость резания не параллельна и не перпендикулярна осям ортогональной системы координат (как при элементарном резании), поэтому резание в рубительных машинах называют торцово-продольно-поперечным (иногда торцово-продольным или торцово-поперечным).
Дисковые рубительные машины подразделяются на малоножевые и многоножевые, а также многорезцовые. Различаются они не только числом режущих ножей, установленных на диске, но и качественными особенностями процесса резания древесины. В малоножевых РМ процесс резания характеризуется цикличностью (прерывистостью). Многоножевые машины работают по принципу непрерывного резания, при котором очередной режущий нож входит в контакт с древесиной раньше, чем предыдущий нож прекращает соприкосновение с древесиной. Многорезцовые РМ применяются в основном для рубки бревен большого диаметра - 0,5 м и более. Отличительной особенностью их режущего аппарата является расположение по спирали множества небольших резцов на диске, за счет чего машины такого типа могут рубить бревна большого диаметра.
В дисковых РМ применяются два способа установки режущих ножей: периферийный и внутренний. При периферийной установке режущий нож располагается на лицевой (рабочей) поверхности диска в специальном посадочном месте и крепится сквозными болтами с потайными головками. В этом случае скошенная фаска является передней гранью резца. При внутреннем способе крепления режущий нож устанавливается в радиальной сквозной щели диска, на рабочей поверхности диска выступает лишь режущая часть ножа. Скошенная фаска ножа при подобной установке играет роль задней грани ножа.
Внутреннее крепление ножей чаще всего используют в многоножевых рубительных машинах, что позволяет разместить на диске необходимое число ножей. Плюс этого способа в максимальной безопасности крепления. Периферийный способ позволяет поддерживать стабильный угол заострения, так как заточка ножей выполнятся по передней грани с наибольшим износом.
Кроме того, дисковые РМ подразделяются по направлению подачи перерабатываемой древесины на машины с горизонтальной подачей (как правило, под углом к режущему диску для уменьшения усилия резания) и машины с наклонной подачей (в этом случае могут быть один или два угла наклона оси подаваемого сырья относительно плоскости диска рубительной машины). Машины с наклонной подачей менее чувствительны к затуплению лезвий ножей, то есть обеспечивают большую величину их упряга и, кроме того, несколько больший выход кондиционной щепы, чем машины с горизонтальной подачей. С другой стороны, наклонное расположение загрузочного патрона требует особых условий для установки машины в цехе - это должно быть помещение с высоким потолком. К тому же перед патроном необходимо устанавливать направляющее устройство (воронку), форма которого сказывается на работе машины.
При горизонтальной подаче возможны нижнее (относительно оси вращения диска) и верхнее расположение загрузочного патрона. Технологическая привязка подобных машин проста, их можно устанавливать как на первом, так и на втором этаже производственного здания. Сырье к ним подается непосредственно с ленточных транспортеров. Но на этих машинах затруднена переработка короткомерных лесоматериалов из-за сложности согласования скорости подающего конвейера и скорости затягивания древесины в машину, поэтому подобную технику рекомендуется использовать для переработки лесоматериалов длиной от 1,5 метра.
В дисковых РМ возможна подача сырья горизонтально, без отклонения оси подачи от фронтальной плоскости диска, но в этом случае выполняется наклон вращающегося диска (как правило, на 40-45°) и он вращается не вертикально, а под наклоном.
Производительность дисковых рубительных машин зависит от размеров перерабатываемой древесины, числа ножей, частоты вращения диска и заданной длины щепы. Поскольку в машину могут поступать балансы, сильно различающиеся по диаметру, то при расчете производительности используют понятие эквивалентного диаметра балансов, который определяется как средний квадратический диаметр в данной партии поставки.
Мощность двигателя привода дисковой рубительной машины складывается из четырех основных составляющих: мощности на преодоление силы сопротивления резанию древесины; мощности механических потерь; мощности на создание напора воздуха и трения вращающегося диска о воздух; мощности, расходуемой на удаление щепы в циклон при верхнем выбросе щепы. Мощность механических потерь и трения о воздух принято называть мощностью холостого хода, которая составляет 5-7% общей необходимой мощности двигателя привода.
Во время эксплуатации двигатель привода РМ, особенно малоножевой, работает в условиях переменной нагрузки, например, при резком изменении диаметра перерабатываемых балансов или перерывах в их поступлении. Причем мощность сопротивления резания прямо пропорциональна диаметру перерабатываемых бревен. У стационарных рубительных машин для привода используются асинхронные и синхронные электродвигатели. При асинхронном приводе обычно выбирается электродвигатель с механическими характеристиками, допускающими значительное снижение частоты вращения, поэтому предпочтительно использовать асинхронные электродвигатели с фазным ротором.
Большое значение при использовании асинхронного электродвигателя имеют моменты инерции рабочего органа РМ. Во время переработки баланса при снижении частоты вращения вала привода используется инерция диска, за счет чего происходит восстановление частоты вращения и накопление кинетической энергии. И для случая периодической подачи балансов можно использовать двигатель небольшой установленной мощности. В рубительных машинах старого образца для усиления этого эффекта на вал иногда устанавливали маховик, что усложняло конструкцию. В современных машинах почти весь момент инерции сосредоточен в рабочем органе машины - диске. Кроме того, в современных машинах, в основном мобильных, встречается система контроля скорости вращения рабочего органа No stress для оптимизации переработки материалов. Логика работы системы реализована очень просто. Оператор оценивает информацию о параметрах текущего тока главного двигателя: если продолжительное время идет превышение допустимых параметров, то приводные вальцы загрузки материала останавливают и прекращают подачу материала в рубительную машину; после того как токи (нагрузка) на главном валу понизятся до заданных значений, подача сырья возобновляется. Эта опция позволяет избежать остановки двигателя, обеспечить однородность щепы и высокую производительность, возможность использовать менее мощный двигатель. На ряде машин частоту вращения диска, при которой срабатывает система No stress, можно регулировать.
К основным недостаткам асинхронных электродвигателей относятся: низкое использование коэффициента мощности (особенно при недогрузке), высокий показатель пускового тока. Поэтому в конструкции современных стационарных рубительных машин все чаще встречаются синхронные электродвигатели привода, основным достоинством которых является высокое использование коэффициента мощности, когда активная мощность используется только для выполнения полезной работы. Кроме того, синхронные электродвигатели могут работать со значительной кратковременной перегрузкой, причем момент инерции рабочего органа машины не имеет большого значения, поскольку частота вращения вала, приводимого в движение синхронным электродвигателем, не снижается при повышении нагрузки.
машин
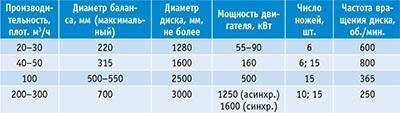
По размерам (диаметру) перерабатываемого сырья и требуемой производительности можно выбрать дисковую РМ по рекомендациям ЦНИИМЭ (табл. 1).
В барабанных рубительных машинах режущим органом (механизмом резания) служит вращающийся барабан, на образующей которого устанавливаются режущие элементы. Как и в дисковых машинах, в барабанных применяют два способа крепления ножей: периферийный (тангенциальный) и внутренний, при использовании которых роль заточной фаски ножа разная.
В практике предприятий используются два типа конструкций ножевых барабанов, различающихся способом удаления из зоны резания полученной (срезанной) щепы: барабаны щелевого и пазушного типа.
Щелевые барабаны полые, и образующаяся в процессе резания стружка (щепа) через подножевые щели поступает в полость барабана и затем удаляется вдоль оси его вращения через один из торцевых проемов. Работа подобных барабанов основана на принципе поперечного резания. Они обеспечивают постоянство фракционного состава и малую повреждаемость щепы, что, в свою очередь, обеспечивает высокое качество получаемой из нее целлюлозы. Достоинством подобных РМ является их невысокая энергоемкость, а недостатком - сложность конструкции.
В барабанах пазушного типа ножевой сплошной (массивный) барабан одновременно служит и маховиком; срезанная щепа собирается во впадинах (пазухах) в теле барабана перед каждым режущим ножом. Работа подобных рубительных машин основана на принципе торцово-продольного резания, эта техника применяется в основном для переработки отходов деревообработки и порубочных остатков. Существенным недостатком таких машин является зависимость угла резания от диаметра перерабатываемого сырья, в результате чего щепа получается неоднородной по фракционному составу и с разным углом среза.
У конических рубительных машин конструкция промежуточная между конструкциями дисковых и барабанных машин. Отличительная особенность конических РМ - выполненный в виде вращающегося усеченного конуса (одного или двух) механизм резания (режущий орган). При малом угле конусности режущего органа конструктивная схема конической машины приближается к конструкции барабанной рубительной машины, при большом угле конусности - к конструкции дисковой. Режущие элементы располагаются на образующей поверхности конуса.
Помимо этого, рубительные машины каждого из трех классов могут быть ножевыми или резцовыми. В ножевых РМ в качестве режущего инструмента выступают плоские ножи с односторонней заточкой. Длина режущей кромки ножей соответствует ширине рабочей поверхности ножевого диска (барабана, конуса), что предопределяет воздействие режущего ножа одновременно на всю ширину сечения перерабатываемого материала. Резцовые РМ отличаются от ножевых тем, что на рабочей поверхности диска (барабана, конуса) установлены резцы, режущие кромки которых в несколько раз меньше ширины рабочей поверхности. Эта особенность существенно меняет процесс резания в рубительных машинах подобного типа. В данном случае по ширине сечения перерабатываемого материала последовательно срезаются полосы шириной, соответствующей длине режущей кромки резцов.
Ножи рубительных машин надо регулярно обслуживать для получения качественной щепы. Продолжительность упряга ножей зависит прежде всего от характеристик измельчаемой древесины - породы, ее влажности, температуры, засоренности минеральными примесями и посторонними включениями, - а также от качества изготовления ножей. По мере работы происходит затупление режущей кромки ножей (резцов), увеличение радиуса ее закругления, что приводит к быстрому росту процента выхода мелкой и крупной фракции щепы и существенному снижению процента выхода требуемой (кондиционной) фракции щепы, а также смятию капилляров на срезе щепы. Признаками затупления ножей являются: изменение звука при работе машины, повышение токовой нагрузки на двигатель, ухудшение затягивания древесного сырья.
Степень затупления ножей рубительных машин при производстве технологической щепы определяют путем измерения радиуса затупления режущей кромки во время периодической остановки РМ. Частота остановки назначается директивно, например, зимой - два раза в смену, летом - один раз в смену.
Подобный подход к остановке рубительной машины и обслуживанию ножей не учитывает многие часто меняющиеся показатели предмета труда: породу древесины, ее качество и объем. При остановке рубительной машины используют следующие методы определения степени затупления ножей: визуальный осмотр; проверку остроты на ощупь; создание слепков лезвий на свинцовых пластинах. Вместе с тем каждая остановка машины приводит к большим потерям времени, часто к остановке всей поточной линии, требутся немалые затраты труда на осмотр ножей, особенно если их 10-16 шт. на машине. Кроме того, при неполной загрузке РМ директивные остановки машины и осмотры ножей не дают желаемого эффекта.
Есть устройства для определения степени затупления ножей, содержащие средство измерения выбранного для оценки состояния ножей определенного параметра, например, зазора между ножами барабана и контрножом. Этот способ также требует периодической остановки рубительной машины, а следовательно всей поточной линии.
Судить о степени затупления ножей рубительной машины по изменению потребляемой мощности тоже малоэффективно, что объясняется очень большой массой и, соответственно, инерцией рабочих органов машин, работающих как маховики. В связи с этим при прочих равных условиях изменение потребляемой мощности РМ по мере затупления ножей малозаметно.
На выход кондиционной, мелкой и крупной фракций щепы, помимо степени затупления лезвий ножей, влияет и их настройка (правильность установки в машине). Например, при неправильно выставленном расстоянии между ножами и контрножом размеры большей части получаемой щепы не будут соответствовать требуемым.
Для повышения эффективности работы РМ в поточных линиях древесно-подготовительных цехов деревоперерабатывающих предприятий представителями научной школы «Инновационные разработки в области лесозаготовительной промышленности и лесного хозяйства», которая включена в реестр ведущих научных и научно-педагогических школ Санкт-Петербурга, было разработано технические решение. Устройство включает систему оперативного определения степени затупления ножей по фракционному составу щепы, вычислительный модуль, а также весоизмерительные устройства для поступающего на переработку древесного сырья и разных фракций полученной технологической щепы. Вычислительный модуль связан со всеми весоизмерительными устройствами и с приводом рубительной машины.
Щепа из рубительной машины поступает в сортировочное устройство, а оттуда в зависимости от фракции на разные транспортеры. Количество кондиционной и мелкой фракции щепы на транспортерах фиксируется весоизмерительными устройствами и передается в вычислительный модуль. Щепа крупной фракции специальным транспортером возвращается в рубительную машину на повторное измельчение. Готовая кондиционная щепа отправляется на отгрузку.
Расчет момента остановки РМ из-за чрезмерного затупления ножей ведется в вычислительном модуле по следующим формулам:
где В - выход кондиционной щепы, %; φ - количество мелкой фракции щепы, %; - допускаемое количество щепы мелкой фракции, %; М - масса балансовой древесины направленная на переработку; М1 - масса полученной кондиционной щепы; М2 - масса полученной мелкой фракции щепы, кг.
В расчетах не учитывается крупная фракция щепы, так как она направляется на повторное измельчение.
Ц-3 и допускаемое количество мелкой фракции (φ) при переработке
балансов разных пород
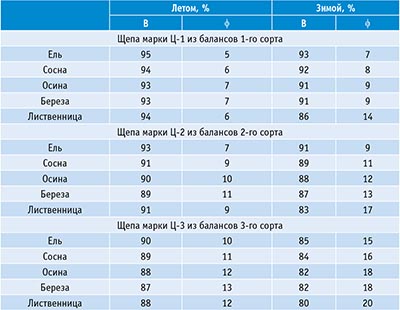
Поскольку по мере затупления ножей повышается и процент выхода мелкой фракции щепы, при достижении предельно допустимого выхода мелкой фракции (см. табл. 2), который определяется по данным весоизмерительных устройств, вычислительный модуль может дать сигнал оператору либо выключить двигатель привода рубительной машины.
Самоходные рубительные установки компонуются путем размещения РМ и необходимого вспомогательного оборудования на самоходных шасси (автомобиль, трактор и
т. п.). Широко распространенным исполнением подобной установки является вариант с использованием для привода механизмов двигателя транспортного шасси.
В случае с прицепными рубительными установками РМ монтируются на одноосной колесной паре, у них небольшие габариты и небольшая (1,5-3,0 т) масса. В качестве базовых машин используют колесные и гусеничные тракторы общего назначения, для сельскохозяйственных и лесных работ. Привод РМ осуществляется от раздаточной коробки трактора через карданный вал. Подобные машины удобны для использования в культивируемых лесах при рубках ухода. Загрузка древесины может выполняться вручную двумя-тремя рабочими или с помощью манипулятора.
Полупередвижными называются установки, технологическое оборудование которых монтируется на несамоходных многоосных платформах. Технологическое оборудование содержит механизмы, по функциональному назначению аналогичные самоходным рубительным установкам.
Полупередвижные рубительные установки почти во всех случаях оснащаются автономной энергетической установкой, чаще всего дизель-генераторной. Для транспортных или технологических перемещений подобных установок требуются автотягач или трактор. Грузоподъемность специальных платформ под полупередвижные установки позволяет монтировать на них рубительные машины с рабочим органом большего диаметра, что при использовании энергетической установки высокой мощности обеспечивает переработку в щепу хлыстов или деревьев. Подобные рубительные установки нашли широкое применение во второй половине XX века в США и Канаде, в основном при сплошных рубках малоценных или плантационных насаждений для использования древесины в производстве целлюлозы и волокнистых материалов или в энергетических целях. В тот период на рынке появились модели передвижных РМ, позволяющих использовать для выработки щепы всю наземную биомассу дерева, включая сучья и ветви. Рубительные машины предназначались для работы в лесу на площадках у лесовозных дорог, устанавливались на трейлерах и были оснащены гидроманипуляторами. Деревья трелевались к рубительным машинам колесными трелевочными тракторами. Вырабатываемая щепа подавалась в большегрузные автомобили-щеповозы. В европейских странах используются преимущественно самоходные и прицепные установки на колесном ходу с механизированной подачей сырья на переработку. В России производство мобильных рубительных машин было развито слабо, в литературе конца ХХ века в числе причин неэффективности использования порубочных остатков отмечались следующие: недостаток передвижных рубительных машин для переработки ветвей и сучьев, отсутствие налаженного производства автощеповозов и выпуска отечественной промышленностью надежных и быстродействующих гидроманипуляторов для подачи сырья.
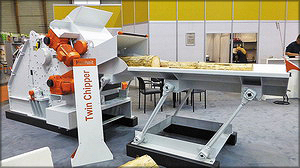
Дробильная машина Twin Chipper
Для обеспечения загрузки РМ древесным сырьем на шасси устанавливаются механические или гидравлические манипуляторы, а также устройства для подачи древесины к механизму резания, в состав которых входят цепные и гусеничные конвейеры, вальцевые или иные механизмы обжима и принудительной подачи перерабатываемого материала. В ряде случаев на самоходном шасси монтируются автономные энергетические установки для привода механизма резания и навесного технологического оборудования.
По принципиальной конструктивной схеме загрузки порубочных остатков рубительные машины можно разделить на два класса: с позиционной загрузкой и непрерывной загрузкой.
Конструктивная схема РМ с позиционной загрузкой порубочных остатков предполагает возможность ручной и механизированной загрузки древесного сырья в зону измельчения. Для непрерывной загрузки сырья в РМ необходима механизированная загрузка древесных отходов.
Для ручной загрузки порубочных остатков в рубительную машину требуется специальная конструкция загрузочного патрона. Порубочные остатки подаются под углом в горизонтальной и вертикальной плоскостях к ножам, что обеспечивает автоподачу материала в зону рубки. Существенным недостатком этого способа является низкая производительность и высокая трудоемкость работ.
Наибольшее распространение получил механизированный вариант загрузки порубочных остатков в РМ. Она может осуществляться двумя способами: сырье для измельчения помещают в машину; машину устанавливают над измельчаемым сырьем. Варианты технического исполнения для реализации первого способа: погрузка сырья транспортером, клещевым захватом, вальцами или при помощи гидравлической подачи.
Для загрузки порубочных остатков при помощи транспортера используется цепной или гусеничный транспортер на подающем столе. Основным тяговым органом цепного транспортера является многорядная длиннозвенная цепь, а гусеничного - гусеничная транспортная лента. У обоих видов транспортеров две рабочие ветви. Верхняя ветвь рабочая, на этом участке устанавливаются дополнительные направляющие для стабилизации движения в поперечном направлении. Нижняя ветвь предназначена для обратного движения секций транспортеров. Секции цепного или гусеничного транспортера соединяются шарнирно, с одной стороны они оснащаются выступами для надежного удержания транспортируемого сырья, а с другой - пазами для линейных направляющих и звездочек. Поступательное движение транспортеров осуществляется за счет вращения звездочек приводом подачи. Подающий стол рубительной машины может располагаться справа по ходу ее перемещения или сзади.
Применение подобных технических решений в высокопроизводительных рубительных машинах ограничено из-за малой скорости подачи, а также из-за риска заклинивания порубочных остатков шарнирами конвейера, что сказывается на его работоспособности.
Погрузка порубочных остатков в загрузочный патрон рубительной машины может выполняться при помощи клещевого захвата (грейфера), который состоит из двух рычагов (лап), связанных общей осью или корпусом, и тяг, соединяющих рычаги с навесным устройством, за которое захваты навешивают на стрелу грузоподъемного механизма. При подъеме порубочных остатков клещевыми захватами усилие сжатия рычагов зависит от массы древесины, соотношения плеч рычагов, конфигурации порубочных остатков и угла стягивания.
Эффективная погрузка сырья в загрузочный патрон рубительных машин при помощи грейферов возможна при работе с отдельными бревнами. В случае использования подобных захватов при погрузке сырья в виде порубочных остатков возникает проблема с габаритной компоновкой груза у входного окна загрузочного патрона.
При погрузке порубочных остатков вальцами основным устройством для загрузки служат вращающиеся навстречу друг другу вальцы с рифленой поверхностью с ножами, которые выполняют дополнительную функцию дробления загружаемой древесной массы. Вальцы вращаются с разной скоростью и разламывают захватываемое древесное сырье путем срезания частиц древесины. Существенным недостатком вальцового механизма захвата является отсутствие возможности регулировки величины зазора между захватными вальцами вследствие постоянно меняющегося объема порубочных остатков, поступающих для загрузки в приемный бункер.
Кроме того, трудно обеспечить прямолинейное движение порубочных остатков, забираемых из куч в приемный бункер.
Применение устройств с установленными одним или двумя роликами гидравлической подачи позволяет использовать при измельчении отходов древесины как первый, так и второй способ механизированной загрузки порубочных остатков в рубительную машину.
Конструкция машины с гидравлической подачей позволяет забирать древесину из кучи без ее предварительного разбора (первый способ), причем машина может находиться в движении, а при переработке ветвей небольшого диаметра (до 8 см) ее скорость может быть довольно высокой (второй способ). Наибольшее применение получил первый способ (загрузка сырья для измельчения в машину) с использованием позиционной загрузки порубочных остатков в загрузочный патрон.
В последнее время на рынке техники появилась многоступенчатая дробильная машина, конструкция которой позволяет измельчать круглые лесоматериалы, обаполы или рейки до размера зерна, подходящего для сушки и гранулирования, за счет последовательного прохождения материала через роторный измельчитель и молотковую дробилку.
Дробильная машина Twin Chipper производства компании Rudnick & Enners (Германия) обеспечивает высокую эффективность переработки древесины, например, для гранулирования или брикетирования. Ввиду того что при дроблении на этой машине достигается требуемая структура стружки, нет необходимости в дополнительном мокром или сухом измельчении.
Валентин ГЛУХОВСКИЙ,
канд. техн. наук, доцент,
Ольга КУНИЦКАЯ,
д-р техн. наук, доцент,
Игорь ГРИГОРЬЕВ,
д-р техн наук, профессор, СПбГЛТУ