Нежелательная вибрация дереворежущего инструмента
Рекомендации по снижению влияния вибрации на процессы резания
На многих отечественных деревообрабатывающих, мебельных или лесопильных производствах часто возникают проблемы, вызванные несвоевременным и некачественным обслуживанием и ремонтом технологического оборудования, а также режущего инструмента.
Эти проблемы, как правило, связаны с низкой квалификацией обслуживающего персонала, в т. ч. ремонтных служб, отсутствием специального измерительного оборудования, плохим материально-техническим снабжением из-за мнимой экономии средств на обслуживание и ремонт оборудования, покупкой дешевых низкокачественных расходных запчастей и материалов (подшипников, смазочных материалов и т. п.), особенно импортного производства. На некоторых предприятиях ремонт оборудования выполняется по мере выявления проблем и связанного с ними снижения качества обрабатываемых поверхностей. В случаях, когда в процессе обработки древесного сырья, заготовок или деталей появляются проблемы с качеством продукции: повышенная шероховатость обрабатываемой поверхности при пилении или фрезеровании, увеличенный расход режущего инструмента или быстрое появление сколов, недопустимых размеров на облицованных плитных материалах при их обработке, - многие технологи в качестве причины указывают некачественный инструмент. И только после безуспешных попыток решить эти проблемы заменой режущего инструмента другим (по их мнению, более качественным), понимают, что у проблем есть несколько причин и решений. О правилах выбора режущего инструмента в соответствии с рекомендуемыми режимами резания, конструктивными особенностями применительно к обрабатываемому материалу написано уже довольно много. В настоящей статье автор рассматривает проблему возникновения повышенной вибрации шпиндельных узлов и оборудования в целом, которая сильно влияет на процессы обработки, качество получаемой поверхности обработанных деталей и материалов, а также стойкость режущего инструмента.
Причины возникновения вибрации
Вибрация - это малые механические колебания, возникающие в упругих телах под действием переменных сил. Источником вибрации является, например, технологическое оборудование, в конструкции которого имеются системы, работающие в режиме возвратно-поступательного движения (кривошипно-шатунные механизмы в лесопильных рамах); неуравновешенные вращающиеся инструменты без динамической балансировки - пилы, фрезы; ударное взаимодействие сопрягаемых деталей (режущий инструмент, особенно плохо сбалансированный, технологическое оборудование с зубчатыми передачами, подшипниковые узлы); оборудование и инструмент, которые используются в технологических целях для ударного воздействия на обрабатываемый материал (рубильные машины и дробилки отходов деревопереработки, долбежный инструмент).
Вибрационная зона - это область распространения вибрации. Вибрация характеризуется скоростью (v, м/с) и ускорением (а, м/с2) колеблющейся твердой поверхности. Обычно эти параметры называют виброскоростью и виброускорением соответственно.
Единица измерения уровня вибрации, как и уровня шума, - децибел (дБ). Стандартизированные в международном масштабе величины v0 = 5 · 10 м/с, а0 = 3 · 10 м/с2 приняты за пороговые значения виброскорости и виброускорения, безопасные для человека.
Частота вибрации (f) - число колебаний в единицу времени, измеряется в герцах (1 Гц = 1/с), числе колебаний в секунду. Период колебания Т (с) - время, в течение которого происходит одно колебание, Т = 1/f. Амплитуда виброперемещения А (м) - максимальное расстояние, на которое перемещается любая точка вибрирующего тела. Связь между виброперемещением, виброскоростью и виброускорением выражается формулами:
v = 2πfA, (1)
а = (2f)2A, (2)
где π = 3,14.
Вибрация может характеризоваться одной или несколькими частотами (дискретный спектр) или широким набором частот (непрерывный спектр). Спектр частот разбивается на частотные полосы (октавные диапазоны). В октавном диапазоне верхняя граничная частота f1 вдвое больше нижней граничной частоты f2, т. е. f/f = 2. Октавная полоса характеризуется ее среднегеометрической частотой. Среднегеометрические частоты октавных полос частот вибрации стандартизированы и составляют: 1; 2; 4; 8; 16; 31,5; 63; 125; 250; 500, 1000 Гц. Из определения октавы по среднегеометрическому значению ее частоты можно определить нижнее и верхнее значения октавной полосы частот.
По способу передачи выделяют общую и локальную вибрацию. Общая вибрация (вибрация рабочих мест) передается через опорные поверхности на все тело сидящего или стоящего человека, контактирующего с вибрирующим инструментом или вибрирующими поверхностями технологического оборудования. Локальная вибрация (местная) передается на руки или отдельные участки тела человека.
Предельно допустимые нормы вибрации зафиксированы в ГОСТ 12.1.012 Вибрация. Гигиенические нормы. ГОСТ 12.1.003 Шум. Гигиенические нормы. По информации европейских станкостроительных фирм, предельно допустимая величина амплитуды виброускорения на деревообрабатывающем оборудовании, в конструкции которого нет механизмов, совершающих возвратно-поступательное движение, и которые оснащены шпинделями с частотой вращения не более 6000 об/мин, не должна превышать 4 м/с2, особенно для станков с ЧПУ.
Кроме негативного влияния на персонал, повышенная вибрация оборудования и режущего инструмента приводит также к некоторым проблемам в процессе резания, например к повышенному износу и выходу из строя как режущего инструмента, так и оборудования, низкому качеству обрабатываемой поверхности (повышенной шероховатости) из-за повышенной вибрации, которая приводит к неоднородному износу режущих элементов. Вибрация пильных шпинделей ведет к потере устойчивости в процессе пиления даже высококачественных пил и, как следствие, к появлению сколов, рисок, мшистости, ворсистости и т. п. Значительная вибрация пильного оборудования приводит также к увеличению ширины пропила при пилении.
Повышенная вибрация оборудовании является следствием развивающихся дефектов в разных узлах станков, а фирмы, специализирующиеся на сервисных услугах, могут при оценке спектра вибрации распознать нарушение кинематических связей отдельных деталей. Любое оборудование, даже сконструированное и изготовленное без ошибок, установленное без дефектов монтажа и эксплуатируемое со всеми требованиями технической документации, рано или поздно подвергается износу. Поэтому нельзя забывать о его своевременной диагностике и ремонте.
Сервисные фирмы, как правило, предлагают два варианта организации вибромониторинга и виброналадки разного технологического оборудования: закупка диагностических приборов и организация службы надежности и диагностики на вашем предприятии с проведением выездного обучения и повышением квалификации инженерно-технических работников, а также привлечение по схеме аутсорсинга специалистов сервисной компании, которые периодически с помощью необходимых приборов и инструментария будут выполнять задачи по вибромониторингу и виброналадке вашего оборудования. Второй вариант в большинстве случаев с экономической точки зрения более выгоден, например, для небольших предприятий с малой численностью персонала и нечастой потребностью в проведении работ подобного рода.
Вибродиагностика оборудования осуществляется методами оценки общего уровня абсолютной вибрации подшипниковых узлов и частотным анализом. Для точного определения диагностических признаков дефектов на ранней стадии их возникновения применяются:
- метод PeakView («Пик-Фактор», ПФ). Наличие даже зарождающихся дефектов, например, в подшипнике, приводит к появлению высокочастотных ударных импульсов и, следовательно, к росту уровня пиков амплитуд высокочастотного сигнала вибрации, причем его среднеквадратичные уровни в общем случае могут даже оставаться неизменными. Рост значения ПФ, превышающий некоторый пороговый уровень, свидетельствует о возникновении единичных ударных импульсов (например: микроудары тел качения об раковину на внутреннем кольце подшипника), а последующее снижение уровня ПФ говорит о появлении большого числа ударных импульсов, что свидетельствует о высоком риске дальнейшей эксплуатации подшипника;
- спектральный анализ огибающей вибрационного сигнала, ударные импульсы, фазовый анализ, усреднение во временной области и др. Также возможно определение собственных частот оборудования, изменений в работе оборудования в процессе его эксплуатации, свидетельствующих, например, об износе оборудования из-за его некачественного обслуживания, плохой смазки и прочего, либо, например, изменении формы сварной станины станка из-за некачественного изготовления или монтажа оборудования, построение псевдоорбит вибросигналов, полученных по нескольким каналам. Теория и практика анализа вибросигналов в настоящее время позволяет получить достоверную информацию почти по любому дефекту оборудования, допущенному в ходе монтажа, изготовления или в результате износа технологического оборудования.
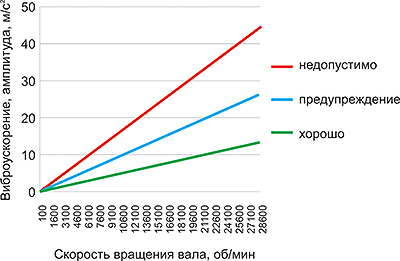
График зависимости допустимой вибрации шпинделя от частоты его вращения при фрезеровании на станках мощностью от 15 до 300 кВт
Помимо приборов виброанализа, сервисные фирмы по собственному усмотрению и в случае необходимости могут использовать приборы и средства для других методов неразрушающего контроля, таких как термография, анализ смазочного материала и т. д. Для измерения уровней вибраций и шума используются разные точные приборы, наиболее распространенный ВШВ-003. Как правило, цель этих измерений - получение фактических значений частот (Гц) и уровня вибрации (дБ), которые сравнивают с предельно допустимыми нормами, на основании чего делают заключение о необходимости проведения ремонтных работ, а также о сроках и порядке проведения планово-предупредительных работ (ППР) на предприятии.
Понятно, что названные приборы и услуги сервисных фирм недешевы, но в век бурного развития средств мобильной связи и электронных устройств можно порекомендовать для определения повышенной вибрации оборудования или его отдельных элементов, например подшипниковых узлов, использовать мобильные устройства (смартфоны, планшеты).
Суть измерений с использованием подручных средств, например iPhone, состоит в следующем. Необходимо в AppStore в окне «Поиск» набрать слово «виброметр», из нескольких предложенных программ для измерения степени вибрации выбрать наиболее удобную и загрузить ее. Включив эту программу и установив телефон на любую горизонтальную поверхность оборудования, можно получить результаты замеров амплитуд колебаний данного узла.
На мой взгляд, для подобных целей больше всего подходит программа «Измеритель вибрации, сейсмограф» от разработчика ExaMobile S.A., которая в реальном времени записывает амплитуду виброускорений (м/с2). Нужно помнить, что следует интересоваться суммарными максимальными измеренными значениями амплитуды в определенном диапазоне (+/-). Понятно, что этот метод не может обеспечить идеальную точность измерений, но проблемы с оборудованием в части недопустимой вибрации выявить поможет. Эти измерения можно использовать, например, при ремонте оборудования (замене подшипниковых узлов) и проверить качество ремонта путем сравнения показаний, полученных с помощью указанной выше программы до и после ремонта. К сожалению, автору не удалось найти данные исследования вибрации в деревообрабатывающем оборудовании, но он надеется, что в качестве примера помогут данные, приведенные на графике зависимости амплитуды виброускорений фрезерного металлообрабатывающего оборудования от частоты вращения шпиндельного вала (см. рис.).
Достоинства этого метода: не требует финансовых затрат и использования специальных приборов, позволяет проверить наличие вибраций, по сути, на любом технологическом оборудовании.
Средства и методы защиты от вибрации и повышенного шума:
- на технологическом оборудовании (особенно таком, где установлены шпиндели для работы на высоких оборотах - более 6000 об/мин) следует эксплуатировать только динамически сбалансированный режущий инструмент с минимально допустимым дисбалансом; например, нельзя эксплуатировать на подобном оборудовании инструмент, изготовленный по ГОСТ Р 52401-2005;
- использовать способы изменения конструкции оборудования, такие как замена вида зубчатого зацепления (прямозубого шевронным); повышение норм точности используемых зубчатых колес (пятна контакта); выбор подшипников более высокой точности; повышение жесткости вала шпинделя; применение литых деталей, например станин станков;
- следует выбирать оптимальные режимы резания, соответствующие характеристикам обрабатываемого материала, качественный режущий инструмент и т. д.;
- необходимо постоянно заботиться о повышении эксплуатационных характеристик оборудования, своевременно выполнять обслуживание, текущий и плановый ремонт, устранять люфты, зазоры и изношенные детали в механизмах передачах, обеспечивать смазочными материалами все узлы и механизмы согласно картам завода-изготовителя;
- технологическое оборудование необходимо устанавливать на качественные фундаменты или на фундаменты с использованием виброопор;
- при эксплуатации оборудования необходимо использовать спецодежду и спецобувь, а также индивидуальные средства защиты от вибрации и шума: наушники, шлемы, вкладыши, которые защищают слуховой аппарат человека.