Бесшпиндельное лущение. Что нового?
Лущильный станок был изобретен еще в конце XIX века. Без этого оборудования сегодня просто невозможно представить производство фанеры и изготовление спичек. За прошедшие сто с лишним лет было создано немало конструкций и модификаций станков, но принцип остался прежним: срезание с коротких бревен-чураков тонкой ленты древесины.
Но при многих достоинствах у традиционных лущильных станков есть и серьезные недостатки конструкции, связанные с необходимостью использования кулачков, которые вонзаются в торцы чураков и заставляют их вращаться. Нередко чурак проворачивается в кулачках и дальнейшее лущение становится невозможным. Как правило, это происходит из-за сердцевинной гнили, особенно часто встречающейся в осиновых чураках. В результате получаются так называемые провертыши – чураки большого диаметра, непригодные для дальнейшей обработки на лущильном станке.
Еще один недостаток традиционной техники лущения – потери древесины в виде остатков от лущения, так называемых карандашей. Диаметр «карандаша» зависит от диаметра внутренних кулачков станка и длины чурака. При длине чурака 1,6 м диаметр «карандаша» обычно 75 мм, а при длине 2,5 м – до 100 мм. Потери древесины составляют 10–12% объема чурака.
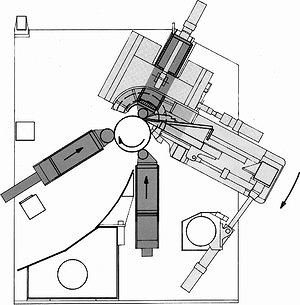
Рис. 1. Схема бесшпиндельного лущильного станка
Желание избавиться от этих недостатков привело конструкторов оборудования к идее бесшпиндельного лущильного станка. Впервые, вероятно, эта идея была реализована фирмой Raute (Финляндия) еще в 1990-е годы (рис. 1) в станках для лущения чураков максимальным диаметром 400 мм и длиной 1,7 и 2,8 м.
Вращение чураков в станке осуществлялось за счет приводных рифленых роликов, расположенных под углом 120° друг к другу. Верхний валец служил одновременно прижимной линейкой, а нижние перемещались прямолинейно по мере уменьшения диаметра чурака. Каждый валец оснащен индивидуальным гидроприводом. В процессе лущения ножевой суппорт немного поворачивался относительно чурака, что обеспечивало оптимальные параметры лущения чурака до диаметра карандаша 50 мм. Положение валов, толщина шпона и угол резания регулировались микро-ЭВМ. Диаметр чурака измерялся до его подачи в станок для определения просвета между валами.
Технология бесшпиндельного лущения шпона в Европе по какой-то причине не получила развития, но широко распространилась в азиатских странах. В Юго-Восточной Азии на многих предприятиях применяют бесшпиндельное лущение тонкомерного сырья и долущивание карандашей. Обычно лущильная линия состоит из окорочно-оцилиндровочного станка, бесшпиндельного лущильного станка с роторными ножницами.
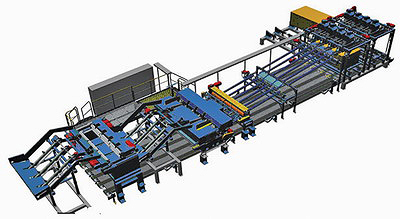
Рис. 2. Линия лущения шпона RD2800 Raute
В окорочно-оцилиндровочном станке чурак зажимается тремя приводными зубчатыми роликами и приводится во вращение. Нож, аналогичный лущильному, удаляет кору и неровности, придает чураку цилиндрическую форму. Начальный диаметр чурака – до 500 мм, после оцилиндровки – не более 360 мм.
Передающий конвейер выравнивает чураки и подает их на бесшпиндельный лущильный станок, оснащенный тремя приводными роликами с мелкой насечкой и лущильным ножом. Максимальный диаметр чурака – 360 мм. Диаметр карандаша – 30–40 мм в зависимости от модели станка. Толщина получаемого шпона – от 1,0 до 3,0 мм. Линейная скорость лущения – 40 м/мин. После лущения шпон поступает на роторные ножницы, где в автоматическом режиме рубится на форматные листы.
Технология лущения тонкомерных чураков будет интересна российским предприятиям, которым приходится работать в наших непростых условиях. Китайские лущильные станки работают и в России, например на фанерном заводе «ИнвестФорэст» в пгт Суслонгер в Республике Марий Эл, на Уфимском фанерно-плитном комбинате, на заводе «Сатис-Мебель» под Нижним Новгородом.
Последнее предложение фирмы Weihai Hanvy из Китая – линия HVPL1326 с окорочно-оцилиндровочным станком и бесшпиндельным лущильным станком с ЧПУ Siemens HXQ2700 и электроникой от фирмы Scheider. Новый станок для бесшпиндельного лущения предназначен для обработки чураков длиной 2,6 м и максимальным диаметром 500 мм. Диаметр карандаша – 40 мм, скорость лущения – 40–100 м/мин. В станке предусмотрено изменение угла наклона ножа в ходе лущения, пневматическое крепление инструмента и автоматическое регулирование толщины шпона.
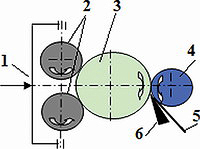
Рис. 3. Бесшпиндельный лущильный станок D1700 G26 и схема его работы
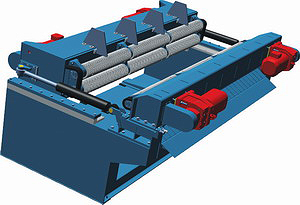
Фирма Raute не оставила идею создания бесшпиндельного лущильного станка и разработала линии RD1400, RD1700 (рис. 3) и RD2800, в составе каждой из которых четыре агрегата с необходимыми транспортным связями: окорочно-оцилиндровочный станок, лущильный станок, роторные ножницы и вакуумный укладчик шпона (рис. 2).
Сырье (чураки заданной длины) подается на поперечный конвейер с дозирующими упорами. В процессе окорки и оцилиндровки чураки приобретают необходимую для лущения цилиндрическую форму и передаются на лущильный станок при помощи еще одного поперечного конвейера.
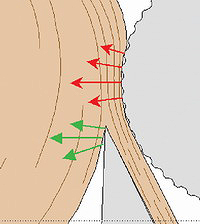
Рис. 4. Схема зоны лущения с прижимным роликом
Кинематическая схема станка претерпела принципиальные изменения в сравнении с предыдущими моделями. Чурак подается в станок сверху, затем поджимается к двум приводным роликам с мелкой насечкой, которые установлены на едином суппорте. В окорочно-оцилиндровочном станке подача роликового суппорта гидравлическая, а в лущильном станке – электромеханическая. Третий ролик находится на неподвижном суппорте с лущильным ножом и играет роль прижимной линейки (рис. 4).
Чурак в станке самоцентрируется по трем точкам. При подаче роликового суппорта вперед чурак поджимается к ножевому суппорту, и выполняется лущение шпона. Толщина шпона задается с пульта управления установкой зазора между ножом и прижимным роликом, в ходе лущения угол резания автоматически меняется для обеспечения оптимальных параметров лущения (рис. 5).
В цепочке за лущильным станком установлены роторные ножницы для рубки шпона. Они подрубают передний край ленты шпона, разделяя форматный шпон и отходы. Передняя кромка листа шпона распознается при помощи фотоэлементов. Далее прохождение шпона по цепочке контролируется с помощью импульсного кодирующего устройства. Рубка выполняется при вращении ножа, расположенного над нижним резиновым роликом. На ножевом вале установлены три ножа. Автономный датчик системы распознавания контролирует пуск и остановку рубки шпона.
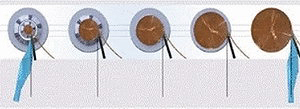
Рис. 5. Изменение угла резания в ходе лущения чурака
За ножницами расположен выходной конвейер с типпельным устройством для отсекания от потока кусков и неформатного шпона. Распознавание осуществляется при помощи фотоэлементов. Далее прохождение шпона по линии контролируется с помощью импульсного кодирующего устройства.
На ножевом валу установлены три ножа. Рубка шпона выполняется при вращении ножа, расположенного над нижним резиновым роликом. Автономный датчик системы распознавания контролирует пуск и остановку процесса рубки шпона.
После ножниц расположен выходной конвейер с типпельным устройством для отсекания кусков и неформатного шпона от потока. Распознавание осуществляется при помощи фотоэлементов, установленных перед типпелем. Форматные листы шпона укладываются стопоукладчиком на подъемник (в базовой модели могут быть один или два подъемника). Управление высотой укладки контролируется фотоэлементом. Полная стопа шпона выкатывается из стопоукладчика при помощи неприводного рольганга. Под линией находится поперечный конвейер необходимой длины для удаления отходов.
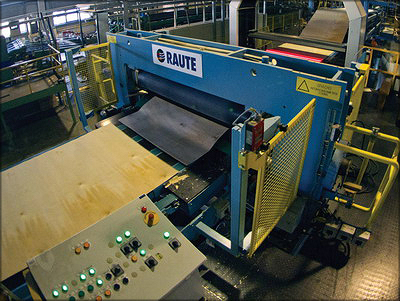
Линия RauteLite предназначена для лущения чураков из мягких и твердых пород древесины длиной 3/4/5/6/8 футов (0,9–2,4 м) и диаметром 120–350 мм. После оцилиндровки диаметр чурака может быть 80–300 мм, диаметр карандаша – 30–35 мм. На линии можно получать качественный шпон толщиной 1,2–2,2 мм c разнотолщинностью ±0,1 миллиметра.
Особо следует отметить, что в состав линии лущения входит система OPG (Optimum Peeling Geometry), с помощью которой посредством сервоконтроля достигается синхронизация скорости подачи роликов, изменение величины зазора между ножом и прижимным роликом, изменение заднего угла ножа в процессе лущения. Эта система осуществляет тотальный контроль всех параметров процесса – с момента начала лущения до удаления карандаша, что позволяет обеспечить высокую стабильность толщины шпона.
Подобные линии вряд ли полностью заменят традиционные лущильные станки, но могут занять свою нишу в линейке оборудования для производства лущеного шпона из маломерного сырья и долущивания карандашей. По расчетам автора, уменьшение диаметра карандаша с 75 до 35 мм позволяет увеличить выход шпона на 7,6% (при среднем диаметре чурака 240 мм), поэтому у подобной техники хорошие перспективы при долущивании карандашей и провертышей.
При выполнении этой задачи в линию уже не нужно включать окорочно-лущильный станок. Именно такую укороченную линию фирма Raute поставила на комбинат «СВЕЗА Кострома», в конце 2017 года линия была пущена.
Владимир ВОЛЫНСКИЙ