ООО «Лесопильный и деревообрабатывающий комбинат №2»
Эффективное использование ресурсов
Когда в 2007 году руководство ЗАО «ХК «Вологодские лесопромышленники» принимало решение о строительстве лесопильного завода в г. Вытегре, никто и представить не мог, с какими сложностями придется столкнуться всего через год в связи с экономическим кризисом. Однако продуманное местоположение завода, наличие лесосырьевой базы, кадровый ресурс по всем расчетам должны были обеспечить экономическую эффективность предприятия, что и подтвердилось на деле.

В 2008 году начались проектные и строительные работы, приказом Министерства промышленности и энергетики РФ от 09.04.2008 № 175 предприятие было включено в перечень приоритетных инвестиционных проектов в области освоения лесов. В целях обеспечения нового производства сырьем предприятию был предоставлен в долгосрочную аренду лесной фонд с ежегодным объемом пользования 136,8 тыс. м3. Строительство завода не прекращалось и в период экономического кризиса, несмотря на трудности с привлечением кредитных ресурсов. Для финансовой поддержки проекта правительством Вологодской области предприятию были предоставлены областные государственные гарантии, проект был включен в государственную областную инвестиционную программу с предоставлением государственной поддержки в виде налоговых льгот. Пуск нового производства состоялся в 2010 году. Перенаправив на себя значительную часть объема вывозимого в тот период из Вытегорского района сырья, которое до пуска лесопильного завода перерабатывалось в других регионах, а также вывозилось на экспорт, холдинговая компания обеспечила заводу возможность быстрого наращивания объемов производства. Уже в 2015 году на заводе был распилен миллионный кубометр бревен, а в 2019 году ожидается выпуск миллионного кубометра пиломатериалов.
На проектную мощность – 190 тыс. м3 переработки пиловочного сырья в год ЛДК вышел уже в марте 2011 года. В дальнейшем постоянно осуществлялись локальные модернизации производственных участков, совершенствовались организационные процессы, что в совокупности позволяло ежегодно наращивать объем переработки древесины и довести его к 2018 году до 290 тыс. м3 круглых лесоматериалов в год.
Территория завода занимает 17 га, на ней расположена биржа круглых лесоматериалов, сортировочная линия, зимний склад пиловочника, лесопильный цех, сушильное хозяйство, цех сортировки пиломатериалов, котельная, склад готовой продукции и административное здание.
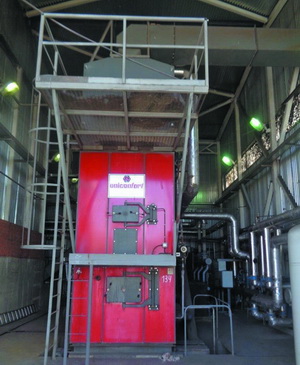
Сырьевое обеспечение
На предприятии перерабатывается древесное сырье двух пород: ели и сосны (74 и 26% соответственно).
Лесообеспечением и реализацией готовой продукции завода занимаются профильные отделы управляющей компании – АО «Группа компаний „Вологодские лесопромышленники“».
Основным поставщиком древесины выступает также входящее в ГК «Вологодские лесопромышленники» предприятие АО «Онегалеспром», которое специализируется на заготовке древесины и обеспечивает основную часть потребностей лесозавода в сырье. Остальные объемы древесины закупаются на свободном рынке в Вытегорском районе и поставляются из соседних регионов. Расчет с поставщиками осуществляется по результатам измерений объемов древесины на линии сортировки бревен. Стоимость древесины определяется не только с учетом расстояния транспортировки, себестоимости лесозаготовки и нормального уровня рентабельности, но в значительной мере с учетом разогретого спроса на рынке. Спрос с каждым годом повышается вследствие роста объемов переработки на существующих мощностях и ввода в эксплуатацию новых предприятий, чему способствует положительная конъюнктура на мировых рынках продукции лесопиления и сопутствующих продуктов (пиломатериалов, технологической щепы, топливных древесных гранул), а также из-за ограниченности доступного лесного фонда. В этой ситуации для успешной работы на рынке требуется не только держать высокие закупочные цены на сырье, но и гарантировать точную, беспристрастную и справедливую приемку сырья у поставщиков.
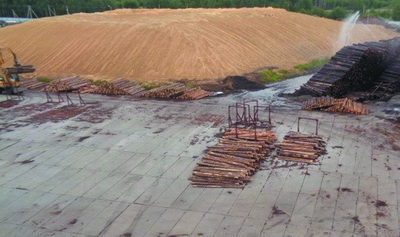
Пиловочник сортируется по группам диаметров на линии Hekotek, оборудованной 3D-сканером Visiometric и металлоискателем. Возможности линии позволяют осуществлять сортировку на скорости подачи до 120 м/мин. Наличие 40 карманов обеспечивает высокую дробность сортировки.
Оптимальные границы сортировочных групп бревен определяются путем анализа поставов в программе Opti-Sawmill. Пересчет границ сортировочных групп осуществляется при каждом переходе на оценку древесины другой породы или длины перерабатываемого сортимента. Подобный подход позволяет обеспечить наиболее рациональное использование пиловочного сырья.
Поступивший на завод пиловочник укладывается на подштабельные места, а для обеспечения его сохранности применяется дождевание, режимы которого подобраны в соответствии с ГОСТ 9014.1-78 «Лесоматериалы круглые. Хранение. Защита дождеванием». Для обеспечения бесперебойной круглогодичной работы лесозавода в период осенней распутицы, а также в течение января-февраля формируется зимний склад сырья.
Работу участка сортировки круглых лесоматериалов обеспечивают фронтальные погрузчики Volvo, а также перевалочная техника производства компании Liebherr.
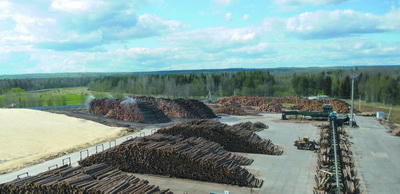
Лесопильный участок
Для распиловки бревен используется фрезерно-брусующая профи- лирующая круглопильная линия производства компании SAB Sägewerksanlagen GmbH. На линии входа установлен сканер и металлоискатель, функциями которых является дополнительный контроль сортиментов, что позволяет исключить попадание непоставных бревен в распиловку. Окорка пиловочных бревен осуществляется непосредственно перед раскроем в двухроторном станке VK 820.
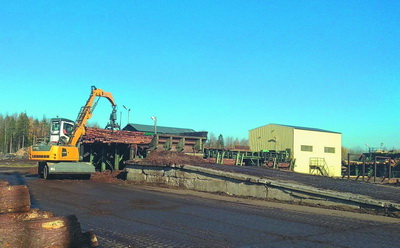
В состав лесопильной линии входят пять основных станков. На первом фрезерно-брусующем агрегате осуществляется фрезерование боковой поверхности бревна и вырабатывается двухкантный брус, который затем поворачивается на 900 и поступает на второй фрезерно-брусующий агрегат. На третьем станке полученный четырехкантный брус профилируется с двух сторон, затем с каждой отпиливается боковая доска. На четвертом станке брус так же профилируется с двух сторон и от него отпиливаются еще две боковые доски. Настройка агрегатов выполняется автоматически в соответствии с предварительно выбранной схемой раскроя. Финишная операция – распиловка полученного бруса на пиломатериалы в двухвальном круглопильном станке, на котором также обеспечивается возможность профилирования еще двух боковых досок. Все вырабатываемые на лесопильной линии пиломатериалы обрезные, поэтому в составе линии нет обрезных станков. Бесступенчато регулируемая скорость подачи зависит от диаметра подаваемого сырья и в диапазоне диаметров 120–500 мм преимущественно варьирует в пределах от 40 до 70 м/мин, при максимально возможной скорости 100 м/мин. Последовательность подачи в распиловку партий бревен определяется с помощью программного комплекса Opti-Sawmill. Крайне важным является обеспечение порядка поступления бревен на участок раскроя таким образом, чтобы минимизировать продолжительность остановок производства для перенастройки станков и одновременно согласовать объемы вырабатываемых пиломатериалов и возможности оборудования сушильного участка.
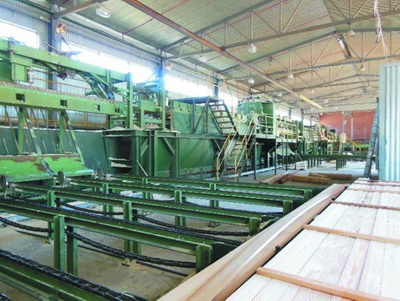
На предприятии ведется учет объемного и качественного выхода пиломатериалов по каждой смене. Средний объемный выход сухих готовых к продаже пиломатериалов – около 50%, но, по мнению руководства предприятия, это не главный показатель оценки эффективности производства. Задачей завода является достижение максимальной товарной стоимости продукции в расчете на кубометр сырья, для чего также используются специальные модули программы Opti-Sawmill, с помощью которых по этому критерию формируются поставы. Технология профилирования SAB позволяет производить боковые доски толщиной до 60 мм, что позволяет обеспечить высокую эффективность раскроя сырья.
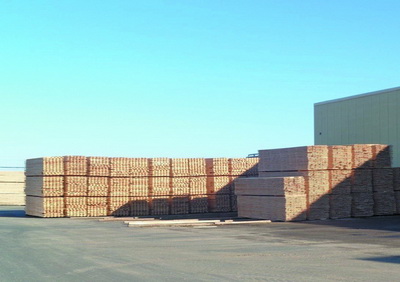
Сушка пиломатериалов
Перед сушкой пиломатериалы, сформированные в сушильные пакеты, хранятся на открытом складе. Для того чтобы обеспечить их сохранность, в зависимости от времени года и породы древесины с помощью программы Opti-Sawmill определяется предельный период их хранения без риска грибных и плесневых поражений, а также растрескивания в летнюю жару.
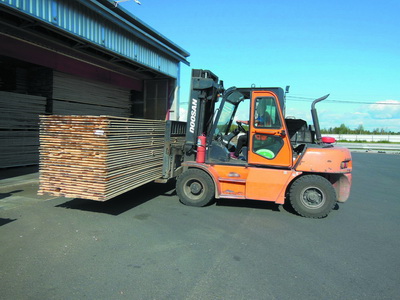
Для сушки пиломатериалов на лесозаводе используют сушильные камеры периодического действия производства компании Baschild (Италия) и Baltbrand (Латвия). Конечная влажность пиломатериалов составляет 16 и 18%, часть спецификации высушивается до влажности 12%.
Для выработки тепловой энергии на предприятии установлены два котлоагрегата Uniconfort (Италия) мощностью 3,5 МВт каждый, в них сжигается смесь топливной щепы, коры и опилок.
Сортировка сухих пиломатериалов
Для сортировки пиломатериалов по сортам используется шведская линия C. Gunnarssons Verkstads AB, в состав которой входят 40 вертикальных карманов. Несмотря на то, что было приобретено бывшее в употреблении оборудование, оно до сих пор работает стабильно и производительно.
Для повышения скорости работы были модернизированы отдельные узлы оборудования, а также скорректированы параметры программного обеспечения, но в целом линия, которая была введена в эксплуатацию при пуске завода, успешно справляется со своими задачами. С учетом того, что сортировка по качеству изначально осуществлялась в круглосуточном режиме, увеличить объемы переработки удалось в основном за счет наработки опыта и навыков работниками предприятия.
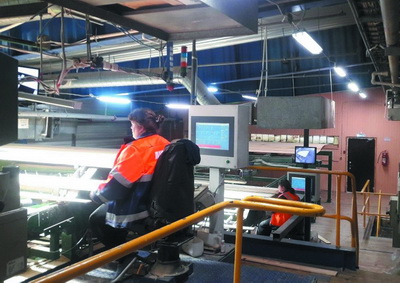
Рынки сбыта
В течение года на заводе выпускают пиломатериалы разного сечения: несколько десятков вариантов. Вся продукция производится по предварительным заказам и долгосрочным контрактам и почти сразу после изготовления отгружается потребителям. Согласованная работа производственных участков определяется тем, что у предприятия есть длительный горизонт планирования работы. Производственное задание определяется на месяц вперед и разбивается по дням. Служба продаж заносит в программу необходимые данные о сечении и объемах пиломатериалов из действующих контрактов, а на предприятии на основании этой информации в программе Opti-Sawmill рассчитываются оптимальные границы сортировочных групп бревен, составляются поставы и определяется очередность распиловки сырья, обеспечивающая производство пиломатериалов только заданного сечения.
Почти весь объем выпускаемой продукции реализуется на экспортных рынках более 20 стран. Основными покупателями являются страны Западной и Центральной Европы, Балтии, а также Китай.
В России почти нет деревообрабатывающих предприятий, готовых закупать пиломатериалы в больших объемах по долгосрочным контрактам. Ну а частных покупателей в основном интересуют заказы в объеме 2–3 м3 пиломатериалов для ремонта или строительства, да и покупку они не могут совершить в день обращения – по действующим правилам системы ЛесЕГАИС. Это обстоятельство существенно снижает привлекательность пилопродукции завода для индивидуальных потребителей и усложняет работу на внутреннем рынке для прозрачно и честно работающих предприятий. Частные покупатели вынуждены приобретать продукцию на малых и мелких производствах, реализующих пиломатериалы в обход системы учета лесоматериалов и зачастую выпускающих пиломатериалы низкого качества.
Технологическая щепа, которая образуется в результате обработки древесины на фрезерно-брусующих станках, поставляется на ЦБК автомобильным транспортом или водным путем в период навигации. Бóльшая часть опилок реализуется производителям топливных гранул, а также поставляется на местную электростанцию.
Сложности логистики
Реализация пиломатериалов осуществляется как на условиях FCA, так и путем поставки продукции до склада покупателя. Ввиду отсутствия в Вытегре железной дороги, 90% пиломатериалов перевозятся автомобильным транспортом, остальные 10% – водным транспортом по Волго-Балтийскому водному пути в период навигации.
Готовая продукция загружается в морские контейнеры на предприятии. Так как с 1 июля 2016 года любой контейнер должен сопровождаться декларацией о подтверждении его массы, завод прошел сертификацию по системе VGM (Verified Gross Mass).
Сложности для логистики предприятия вызваны и плохим состоянием участка дороги от Вытегры до федеральной трассы «Кола», которая больше похожа на направление, нежели на дорогу общего пользования. Из-за низкого качества дороги, по которой почти невозможно проехать весной, часть грузов приходится отправлять в порт Санкт-Петербурга по трассе через г. Череповец, из-за чего почти в два раза увеличивается расстояние перевозки.
Кадровое обеспечение
На первом этапе завод испытывал кадровый дефицит, что представляло серьезную проблему при общей необходимой штатной численности работников 188 человек. Ведущих специалистов приходилось привлекать из других регионов, обучение операторов осуществлялось своими силами.
Управляющий директор ЛДК № 2 Евгений Игнахин поделился своим видением вопроса: «Готовые специалисты с профильным образованием и опытом работы практически отсутствуют на рынке труда. Даже те, которых удается привлечь, очень часто не имеют знаний и умений в области работы с современным оборудованием, поскольку отечественные отраслевые учебные заведения давно не успевают за техническим прогрессом и используют устаревшие методики.
Хуже всего то, что часть преподавателей не имеет мотивации к повышению собственной квалификации и на протяжении многих лет не актуализирует преподаваемые дисциплины. Используемое в вузах и профильных технических училищах софтверное обеспечение и технологическое оборудование тоже в подавляющем большинстве не соответствует современному, используемому на промышленных предприятиях. Вынуждены справляться своими силами. За каждым новым человеком, приходящим работать на завод, закрепляется наставник, функцией которого является обучение не только непосредственной работе на оборудовании цеха, но и в целом технологии, логистике, взаимосвязям и взаимодействию со смежными участками и подразделениями завода.
На современном лесопильном производстве при наличии квалифицированных операторов оборудования, технолог, как таковой, фактически не требуется. В условиях нашего производства задачи технолога возложены на начальников цехов, которые, помимо этого, несут административную и методическую нагрузку: управление персоналом, обучение, учет сырья и продукции, производственная отчетность и анализ текущих результатов работы производственного участка. Подобное положение в полной мере соответствует общим тенденциям развития современных лесопильных предприятий и иных отраслей в части сокращения количества персонала, не связанного напрямую с выполнением технологических операций».
Направления развития
Развитие производства в текущих условиях тесно связано не только с использованием автоматизированного оборудования, но и с внедрением современных комплексных софтверных систем выбора решения, связывающих все производственные участки предприятия. В 2016 году на заводе был внедрен программный комплекс Opti-Sawmill производства российской IT-компании Opti-Soft, созданной при Петрозаводском государственном университете. Внедрение механизмов автоматизированного планирования производства Opti-Sawmill, включающего модули объемного, календарного, экономического и коммерческого планирования, позволило не только повысить экономическую эффективность раскроя сырья, но и за счет уменьшения числа простоев оборудования увеличить общий объем производства. «Величина экономического эффекта при использовании подобных программ, зависит от исходного уровня организации планирования на предприятии, – говорит Евгений Игнахин. – Естественно, что чем ниже был изначальный уровень, тем большую эффективность могут принести современные информационные технологии. Ожидаемый эффект от программного комплекса Opti-Sawmill был достигнут уже по результатам внедрения только модуля объемного планирования. На наш взгляд, это связано с тем, что человек может оперировать весьма ограниченным числом сценариев работы предприятия, как правило, это пять – семь вариантов, в то время как программа оценивает и делает выбор более чем из тысячи подобных сценариев за очень короткое время. Программный учет остатков на складах как сырья, так и полуфабрикатов позволил не только упростить планирование работы предприятия, но и значительно уменьшить потери качества древесины за счет сокращения продолжительности ее хранения до начала механической обработки и сушки».
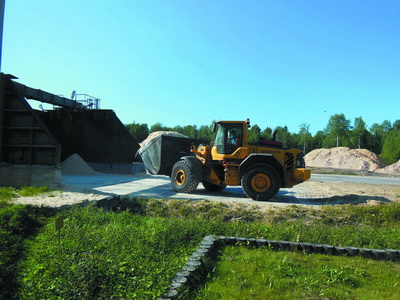
По объемам переработки круглых лесоматериалов предприятие в настоящее время приблизилось к своим максимальным производственным мощностям. Повышение производительности возможно только путем модернизации машинного парка завода, которая в первую очередь должна предусматривать замену линии сухой сортировки пиломатериалов и переход от визуальной сортировки к использованию фотометрических средств контроля. Этот шаг требует привлечения значительных инвестиций, проект пока находится в стадии предварительного изучения и оценки экономической эффективности.

Основным направлением развития предприятия в среднесрочной перспективе будет являться повышение эффективности использования древесины, как с привлечением внутренних резервов, так и с рассмотрением различных вариантов модернизации производственных участков.
Текст и фото Александр Тамби, д-р техн. наук, проф. ЯГСХА