Инновационные разработки в области модификации древесины
Улучшением свойств древесины ученые и практики занимаются уже несколько столетий. Разработки в этой области ведутся во всех промышленно развитых странах: США, Японии, Китае и странах Евросоюза. Наиболее известные марки выпускаемой за рубежом модифицированной древесины– Accoja, Belmadur, Kehony, Lignamon, Lignomer, Steipack, Steibwood, Thermowood и др. В России в небольших объемах выпускается модифицированная древесина (МД) марок Thermowood, «Дестам» и прессованная древесина для изготовления ткацких челноков и подшипников скольжения. Это очень мало. А между тем, в нашей стране разработаны перспективные способы модифицирования древесины, защищенные патентами и регламентированные государственными стандартами.
Основными техническими приемами модифицирования древесины являются пропитка, сушка и прессование. Дополнительные способы обработки – воздействие ультразвуком, импульсным магнитным полем, намагничиванием пропиточных составов.
Способы модифицирования древесины
Модифицирование древесины преследует следующие цели: повышение формостабильности в среде с переменной влажностью, повышение прочностных свойств, повышение теплопроводности и придание материалу антифрикционых свойств, получение древесины с плотностью бальзы, придание древесине новых свойств.
Необходимость повышения формостабильности древесины – одна из старейших проблем при использовании древесных материалов и изделий из них. В силу разных причин, прежде всего воздействия атмосферной влаги и осадков, объемное разбухание натуральной древесины составляет 15–18%. Но наиболее острая эта проблема для прессованной древесины, объемное разбухание которой составляет 100–120%. Для придания прессованной древесине стабильности форм и размеров ее пропитывают разными стабилизаторами.
В качестве стабилизирующих веществ использовали следующие органические соединения и полимерные материалы: полиэтиленгликоль (ПЭГ), поливиниловый спирт (ПВС), кремнийорганическую жидкость марки ГКЖ-94, формальдегид, метилендиизоцианат (МДИ), а также продукты сополимеризации стирола с кубовыми остатками ректификации толуола (КОРТ) и кубовыми остатками ректификации бутадиена (КОРБ). Поскольку вводимые в древесину стабилизаторы снижают антифрикционные свойства модифицированной древесины, их содержание в ней ограничивали 5%.
В процессе термообработки в течение трех часов при температуре 140 °С прессованная древесина стабилизируется вследствие вступления в реакцию продуктов распада карбамида с ее компонентами.
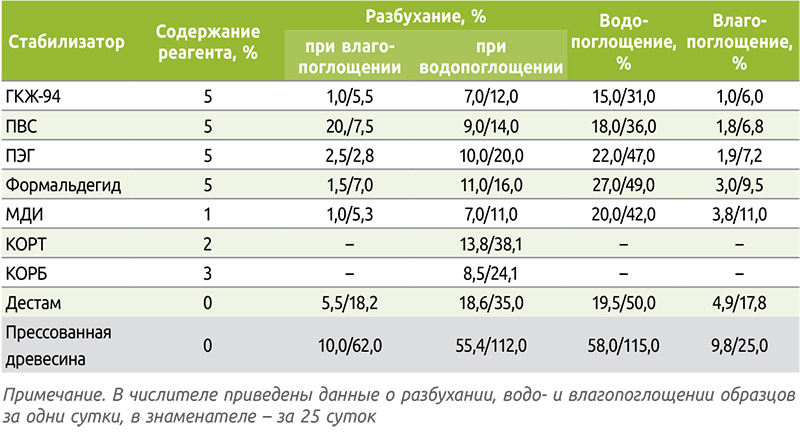
При дополнительном введении добавок наблюдается совместный стабилизирующий эффект, заключающийся в уменьшении влаго- и водопоглощения и разбухания в 5–10 раз в сравнении с фиксируемыми в немодифицированной прессованной древесине (табл. 1).
По результатам исследования, наибольший стабилизирующий эффект отмечен для МДИ и ГКЖ-94, использование которых позволяет сократить разбухание модифицированной древесины марки «Дестам» примерно в три раза.
Но можно ли получить полностью стабильную прессованную древесину, размеры которой останутся неизменными в среде с переменной влажностью? Стабилизация в этом случае должна вестись на трех уровнях: а) на уровне элементарных молекул и функциональных групп ингредиентов древесины; б) на уровне макро- и микрофибрилл, составляющих клеточную стенку; в) на уровне геометрии клеток древесины, меняющих конфигурацию в процессе прессования.
На первом уровне необходимо блокировать гидроксильные группы целлюлозы, гемицеллюлоз и лигнина, ответственные за гидрофильность древесины. Эта задача решается путем исчерпывающего ацетилирования древесины, например, уксусным ангидридом. На втором уровне следует сшить макромолекулы целлюлозы, формирующие микрофибриллы, лишив их возможности перемещения. Для этого важно пропитать древесину мономером или олигомером, проникающим в клеточную стенку и затем полимеризующимся. Эта задача решается с помощью пропитки древесины фенолформальдегидным олигомером (фенолоспиртами) с последующим отверждением. Наиболее сложная задача решается на третьем уровне, когда необходимо стабилизировать клетки древесины, сплющенные в результате прессования, поскольку при их распрямлении происходит основная деформация разбухания древесины (более 80% общей). Сплющенные клетки и сосуды находятся в напряженном состоянии и при попадании в них влаги стремятся к возвращению к естественной форме. Для их стабилизации необходимо создание в люменах пространственной трехмерной сетки с обязательной сшивкой сетки с функциональными группами древесины. Подобную сетку образуют при отверждении фенолоспирты, реагирующие с активными группами ингредиентов древесины.
Экспериментальная проверка этой гипотезы выполнялась следующим образом. Заготовки прямоугольной формы из древесины мягких лиственных пород влажностью 10–15% подвергали исчерпывающему ацетилированию избытком уксусного ангидрида в течение 48 ч. После этого образовавшуюся в древесине уксусную кислоту и избыток уксусного ангидрида удаляли с помощью сушки в сушильной камере при температуре 80—100°С. Прирост массы ацетильных групп составил 25–30% (степень конверсии гидроксильных групп древесины 85–95%). Для обработки вместо уксусного ангидрида можно использовать кетен (длительность обработки 10 ч), в этом случае сушка не нужна. Высушенные заготовки пропитывают под давлением водными растворами фенолоспиртов 46%-ной концентрации до прироста массы раствора 80–100%, после чего их обезвоживают над пятиокисью фосфора до влажности 10–12%. Прирост массы фенолоспирта по сухому остатку в пересчете на сухую древесину составляет 36–42%.
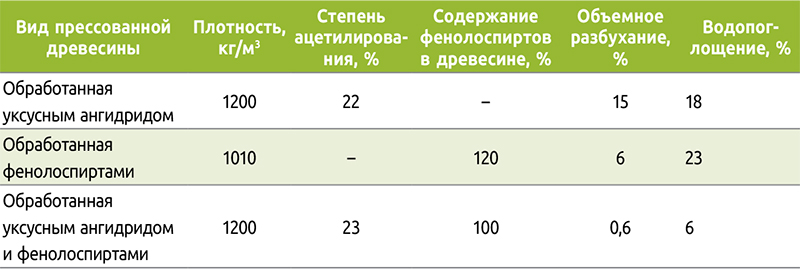
Полученный материал прессуют в пресс-формах до плотности не менее 1200 кг/м3. Если плотность прессованной древесины ниже 1200 кг/м3, то полости клеток сплющены недостаточно и сшивка их продуктами поликонденсации фенолоспиртов происходит не полностью. Спрессованные заготовки подвергают термической обработке при температуре 110—140°С. Период отверждения фенолоспиртов составляет 6–10 мин на 1 мм толщины прессованной заготовки (6 мин при температуре 140°С и 10 мин при температуре 110°С). Предельное объемное разбухание модифицированной подобным образом древесины составило 0,6%, предельное водопоглощение – 6%. В табл. 2 приведены сведения о свойствах древесины, полученной совместным воздействием на нее ацетилирования и обработки фенолоспиртами и способами модифицирования либо ацетилированием, либо обработкой фенолоспиртами.
Суммарный эффект стабилизирующего влияния фенолоспиртов и ацетилирования должен составить по разбуханию 4,3%, а по водопоглощению – 10,3%.
Сравнив эти результаты с данными, содержащимися в табл. 2, получимаем, по сути, сверхсуммарный эффект воздействия фенолоспиртов и ацетилирования, превышающий расчетный по разбуханию в семь раз и по водопоглощению в два раза. Наибольший стабилизирующий эффект для прессованной древесины дает обработка фенолоспиртами. Совместное воздействие ацетилирования и фенолоспиртов позволяет уменьшить по сравнению с обработкой древесины только фенолоспиртами водопоглощение – в 4 раза, а набухание – в 10 раз. По сравнению с нестабилизированной прессованной древесиной уменьшение водопоглощения и разбухания составляет 30 и 200 раз соответственно. Придание древесине высоких прочностных свойств и износостойкости не менее важная задача, окончательное решение которой еще не найдено. Наиболее распространенный способ повышения прочности древесины таких пород, как тополь, осина, береза, это прессование. Из древесины этих пород при степени прессования 30–40% получают древесину плотностью 700–800 кг/м3, которую можно использовать как заменитель дуба, а при степени прессования 50–60% – древесину плотностью 1300—1400кг/м3, которая может служить заменителем текстолита. Перед прессованием древесина должна быть пластифицирована либо химическими реагентами (такими как карбамид и аммиак), либо ультразвуком. Для пропитки сырой древесины в виде оцилиндрованных бревен диаметром 20–40 см и длиной до 3 м разработана пропиточная установка, пропитка бревен начинается с торца под давлением жидкости любой вязкости. Если в бревнах есть сердцевинная гниль, то в здоровую зону древесины подаются пластификатор и стабилизатор, а в зону гнили еще и упрочнитель, для того чтобы у модифицированной древесины была одинаковая прочность по сечению. Пропитанные сырые бревна разрезаются на доски и брус, из них формируется на тележке штабель, каждый ряд заготовок перекладывается стальными пластинами с сеткой. Тележка закатывается в установку СПК-1, представляющую собой сушильную камеру, совмещенную с гидропрессом.
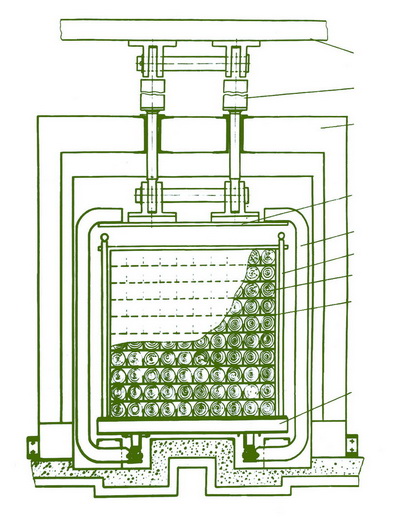
Использование этой установки позволяет в значительной мере сократить число межоперационных транспортных операций и автоматизировать процесс получения модифицированной древесины. Принципиальная схема установки показана на рис. 1. Сверху в стену камеры смонтированы вертикально цилиндры, свободные концы штоков которых находятся внутри камеры и несут прессовые плиты. Гидроцилиндры работают от станции гидропривода, автоматически поддерживающей установленное удельное давление. Принудительную циркуляцию внутри камеры обеспечивает вентилятор, вмонтированный в ее глухую стену.
Сушка в установке выполняется горячим воздухом, нагреваемым электронагревателями или с помощью аэродинамической установки. Влага, испаряемая из древесины, конденсируется в водяном холодильнике и по отводящей трубке выводится из камеры в мерник для определения объема. Охлажденный воздух вентилятором вновь подается на нагреватель и далее на древесные материалы, после чего цикл повторяется.
Для контроля режима сушки используются психрометр, уравновешенный мост КСМ-ЗП и логометр Л-64. Температура сушки поддерживается автоматически.
Использование холодильника в камере СПК-1 позволяет сократить время прессования и сушки до 13–15 ч вместо 24–26 ч. Да и весь процесс получения модифицированной древесины (заготовки сечением 65 × 65 мм и длиной 600 мм) сокращается до 24 ч вместо 32–36 часов.
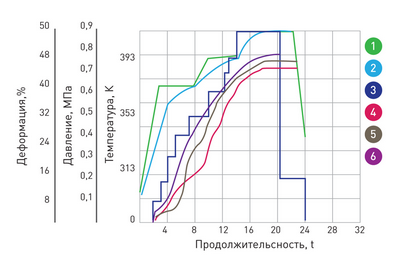
времени
На рис. 2 графически показано изменение технологических параметров работы установки и деформирование древесины под давлением.
В первые четыре часа процесса температура в установке повышается до 100°С (температура мокрого термометра 91°С), температура древесины растет до 93°С. С использованием давления до 0,2 МПа начинается деформирование древесины, не превышающее 6 % первоначального объема. Далее следует сушка при температуре 100°С. Одновременно повышается давление с 0,1 до 0,5 МПа. Технологическая деформация возрастает до 15–20%. Влажность древесины снижается с 50–70 до 30%, что позволяет повысить температуру сушки до 120°С при температуре мокрого термометра 100 °С. Эта температура устанавливается после 9 ч процесса и поддерживается постоянной в течение 10 ч (основная температура сушки). За это время древесина высыхает до влажности 3–5% и завершается уплотнение древесины до степени деформирования 45–48%. Удельное давление доходит до 0,8 МПа и остается постоянным. Следует отметить, что приращение технологической деформации прекращается после 17 ч процесса, когда влажность древесины падает до 10%.
Завершающей стадией процесса является термическая обработка модифицированной древесины с целью стабилизации размеров. Для этого температура в камере повышается до 140°С и с 20-го по 23-й час процесса проводится термообработка древесины. Температура внутри древесины возрастает до 135°С, карбамид расплавляется и полимеризуется, соединяясь с компонентами древесины. Давление в этот период снижается до 0,2 МПа для предотвращения распрессовки. По завершении термообработки нагрев прекращается, установка открывается и при работающем вентиляторе воздух в ней охлаждается до 60°С.
Для получения древесины высокой плотности заготовки с одного торца уплотняют поперек волокон в радиальном направлении на 9–29% (в зависимости от начальной плотности древесины,) а в тангенциальном – на 29% до достижения максимальной плотности, близкой к плотности древесинного вещества.
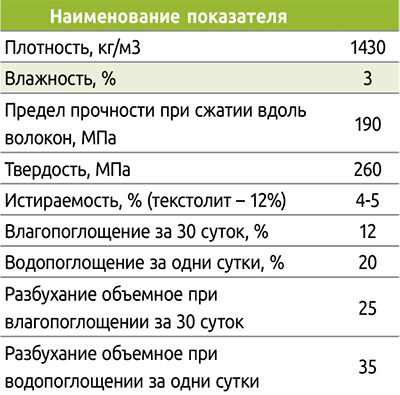
Оптимальные технологические факторы и показатели свойств модифицированной древесины приведены в табл. 3.
При использовании изделий из модифицированной древесины в качестве деталей трения самым сильным сдерживающим фактором является низкая теплопроводность древесины, составляющая 0,5 Вт/м/град. Для повышения теплопроводности древесины разработан способ ее металлизации парами тетрокарбонила никеля с последующим разложением его в древесине до металлического никеля в виде пленки толщиной 0,4 мкм, выстилающей всю внутреннюю поверхность древесного материала. В результате теплопроводность древесины повышается до 15 Вт/м/град.
Технология получения модифицированной древесины для подшипников скольжения следующая. Брус из березы (комлевой части) сечением 80 × 80 мм и длиной 350 мм высушивается в сушильных СВЧ-камерах до постоянной массы, то есть до влажности менее 2%. Бруски помещаются в установку металлизации и при глубоком вакууме из древесины удаляется вся оставшееся влага. После этого бруски с торца под давлением обрабатываются парами тетракарбонила никеля, которые проникают внутрь бруса и равномерно распределяются по всем полостям и капиллярам. Далее один торец бруска нагревается до 180°С и зона нагрева плавно продвигается к другому торцу в течение 8 ч. В результате происходит реакция
Ni(CO)4 → tNi + 4CO↑.
Содержание никеля в древесине 5–10% по массе и 0,8–1,1% по объему. Металлизированные бруски с торца пропитываются в установке под давлением аэрозолем (воздух плюс микрокапли смазки Biol), содержащим наночастицы графита и дисульфида молибдена, пока содержание смазки в древесине не достигнет 7–8%, за счет чего коэффициент трения модифицированной древесины снижается с 0,7 до 0,07. Далее бруски пластифицируются ультразвуком и прессуются в пресс-формах методом трехстороннего уплотнения при давлении 500 МПа до плотности 1250–1350 кг/м3. Бруски, после прессования длиной 300 мм и сечением 50 × 45 мм, замораживаются жидким азотом, извлекаются из пресс-формы и обрабатываются импульсным магнитным полем для стабилизации форм и размеров. Из этих брусков изготавливают подшипники скольжения с рабочей торцевой поверхностью для прокатных станков, установок-качалок, используемых для добычи нефти, транспортеров, погружных насосов, комбайнов, втулок разных узлов и т. д.
Малоценную древесину низкой плотности (тополя, ветлы, ивы) нельзя использовать там, где нужно обеспечить тепло-, звуко- и виброизоляцию, поскольку она слишком плотная (300–350 кг/м3), чтобы конкурировать с древесиной бальсы (плотность которой 150–200 кг/м3) из Южной Америки.
До сих пор снизить плотность древесины можно было лишь путем нарушения ее структуры. Древесину обрабатывали сильными химическими реагентами (кислотами, щелочами, окислителями и др.) либо воздействовали на нее дереворазрушающими грибками. В то же время известные способы повышения плотности древесины (обработка аммиаком, сушка, силовое воздействие) позволяют получить и древесину пониженной плотности за счет увеличения ее объема.
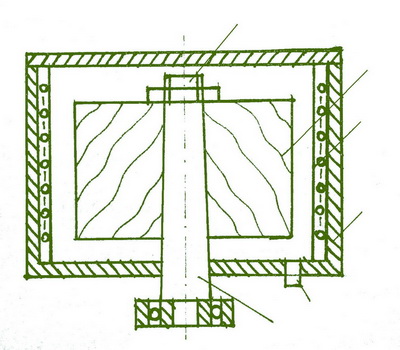
Объем древесины увеличивается при переходе в сверхнабухшее состояние и последующем силовом воздействии путем растяжения поперек волокон во взаимно перпендикулярных направлениях. Растяжение древесины осуществляют на специальных установках под действием центробежных сил, причем заготовку располагают так, чтобы ее вертикальная ось, параллельная волокнам, совпадала с осью вращения. Установка для увеличения объема древесины представлена на рис. 3.
Цилиндрические или прямоугольные заготовки из древесины мягких лиственных пород пропитываются жидким аммиаком до предела набухания. В жидком аммиаке предел набухания вдвое больше, чем в воде, он составляет 32%. После этого заготовку помещают в сушильную камеру таким образом, чтобы вертикальная ось заготовки, параллельная оси волокон, совпадала с осью вращения центрифуги. Температура в камере повышается до 95–105 °С, а частота вращения центрифуги доводится до 2000 мин-1, и заготовки сушатся при растягивающих напряжениях. Частота вращения центрифуги плавно увеличивается до 8000 мин-1 по мере повышения жесткости древесины вследствие десорбции аммиака. Подобное ограничение частоты вращения центрифуги обусловлено тем, что растягивающие напряжения не должны превышать предел прочности древесины при растяжении для каждого ее состояния, зависящего от температуры, влажности и количества пластификатора.
В начале процесса центрифугирования предел прочности древесины на растяжение при температуре 95°С и избытке аммиака составляет 2,5 МПа, а напряжение центрифуги при частоте вращения 2000 мин-1 – 2,2 МПа. В конце процесса предел прочности древесины возрастает до 9 МПа, а растягивающие напряжения центрифуги – до 8,8 МПа. Температура процесса должна быть 95—105°С. При температуре ниже 95°С десорбция аммиака происходит медленно и продолжительность сушки значительно увеличивается. При температуре выше 105°С начинается термодеструкция древесины, что предопределяет снижение ее прочности. Окончание процесса определяется по прекращению поступления аммиака через канал в камеру. Длительность процесса, включая пропитку и сушку, зависит от размеров заготовки и составляет от одного до трех часов. Растягивающие напряжения в древесине можно развивать за счет действия не только центробежных сил, но и растяжения образца древесины прямоугольного сечения в двух взаимно перпендикулярных направлениях.
В результате сушки под воздействием растягивающих напряжений объем заготовки увеличивается дополнительно на 7–8%, в том числе в радиальном направлении на 2,5–3%, в тангенциальном на 4,5–5%. Таким образом, общее увеличение объема заготовки после разбухания и сушки составляет 39–40% первоначального объема.
Древесина – материал непрочный, изрядно уступающйй по прочности, например, керамике, углестеклопластикам, легированным сталям. В тоже время по приведенной прочности (прочности, отнесенной к единице плотности) древесина даже превосходит перечисленные материалы, что объясняется ее ажурной структурой, которую миллионы лет создавала природа и которую человек не может воспроизвести с той же точностью. Повысить прочность древесины можно за счет модифицирования: либо увеличить содержание самой древесины в единице объема путем прессования или сжатия, либо заполнить пустоты в ее структуре жидкими модификаторами (мономерами, олигомерами, синтетическими смолами) с последующим отверждением. Таким образом можно повысить плотность древесины вплоть до плотности древесного вещества, а ее прочность – до прочности стали Ст3 или текстолита, то есть до предела прочности при сжатии волокон 200–220 МПа.
В древесину невозможно ввести высокопрочные материалы, например жидкую сталь, из-за ее низкой теплостойкости. Поэтому можно констатировать, что возможности известных способов модифицирования исчерпаны.
Полученные в последнее время наноматериалы (фуллерены, нанотрубки и т. д.) пока не являются конструкционными из-за размеров, но обладают наивысшей удельной прочностью. У натуральной древесины высокая удельная прочность обеспечивается за счет высокой прочности древесного волокна и близкой к оптимальной конструкции механических элементов – трахеид и волокон либриформа, соединенных в единое целое.
Авторы этой публикации предлагают следующую схему получения конструкционного материала. Древесина граба отличается среди известных пород наибольшей приведенной прочностью (213, 8 кПА/кг/м3) и плотностью (800 кг/м3). Плотность древесного вещества 1550 кг/м3. Следовательно, примерно половину объема заготовки из граба составляет воздух, другую половину – древесное вещество.
Для проведения работ берутся заготовки из древесины граба влажностью 3–6% в виде куба с ребром 300 мм. Проводится исчерпывающая пропитка образца веществом А с заполнением всех пустот древесины заготовок. Подобную пропитку можно осуществить автоклавным способом по методу «вакуум – давление – вакуум» за 4–6 циклов.
Требования к веществу А: вязкость пропиточного раствора должна быть такой, чтобы раствор заполнил пустоты, но не проникал в клеточные стенки. Вводимое в древесину вещество должно быть термостойким при температуре 300°С и выше. Веществом А может служить нанодисперсный кремнезем или каолин в виде суспензии в жидком связующем. В качестве связующего можно использовать фенолформальдегидную смолу Ф-10 или кремнийорганический компаунд «Викинг ПК-68». После того как эта смесь застывает в древесине, заготовки обжигаются при температуре 300–400 °С. При обжиге древесная составляющая выгорает и остается силикатная структура со строением, соответствующим структуре пустот древесины, и с пустотами, которые занимали элементы древесины. Эти пустоты в виде трубок и каналов заполняются жидким веществом В. Таким веществом могут быть расплавы высоколегированных сталей, титановых сплавов, жидкие стеклопластики или наноматериалы в начальной стадии формирования, то есть в гелеобразном состоянии. После отверждения вещества В вещество А удаляется из полученного материала: для силикатов может быть использована обработка сильными щелочами с последующим центрифугированием.
Таким образом получается материал с ажурной конструкцией, предел прочности которого при сжатии вдоль волокон близок к пределу прочности, например, титанового сплава, но его масса в четыре раза меньше, то есть удельная прочность полученного материала выше минимум в три раза.
Заключение
Рассмотренные в статье способы модифицирования древесины намного опередили подобные зарубежные разработки, однако широкого распространения не получили. Объясняется это тем, что в нашей стране бизнес-сообщество ориентировано преимущественно на получение сиюминутной выгоды, тогда как прорывные технологии требуют немалых вложений и несут определенные риски. Государственная поддержка лесопромышленного комплекса не дает эффекта. Еще одним барьером является стереотип мышления: мы, мол, самая богатая лесом страна, и пока заниматься улучшением свойств древесины не стоит («когда вырубим, тогда будем думать»). В результате в будущем мы будем закупать модифицированную древесину в Китае так же, как сейчас ежегодно закупаем 150 тыс. м3 древесины в Африке, Юго-Восточной Азии и Латинской Америке. А ведь при применении представленных методов модифицирования могли бы производить из древесины местных малоценных пород модифицированную древесину, не уступающую по свойствам древесине палисандра, махагони и т. д. Основоположник модифицирования древесины в нашей стране Н. Г. Матвеев в 40-х годах прошлого века писал: «Прессование древесины пока является реальной сказкой. Наша задача сделать ее сказочной реальностью».
Владимир Шамаев, д-р техн. наук, проф. кафедры древесиноведения ВГЛТУ
Ольга Куницкая, д-р техн. наук, проф. кафедры технологии и оборудования лесного комплекса ЯГСХА
Александр Анучин, науч. сотр. ЦНИИ лесной генетики и селекции ВГЛТУ