Устройство котельной на биотопливе
Если вы выбираете оборудование для котельной на биотопливе, то главным критерием должен стать тот фактор, какое из видов биотоплива является наиболее доступным для вашего предприятия. Если вы, например, владелец лесопилки и имеете большое количество опилок и древесной щепы, то вам необходимо приобрести оборудование для сжигания влажного топлива. Если же вы директор мебельной фабрики, то, скорее всего, отходами производства вашей компании будет сухая щепа, что позволит применять биокотельные для сухого топлива. В этом случае возрастает экономия энергии в процессе сгорания, что приводит к более высокой эффективности процесса. Это позволяет говорить о преимуществах использования просушенных опилок и стружки. Если же у вас имеется или вы намерены приобрести установку для изготовления пеллет, то в этом случае вы сможете применять оборудование для сжигания облагороженного биотоплива − самый высокотехнологичный способ производства энергии из биомассы.
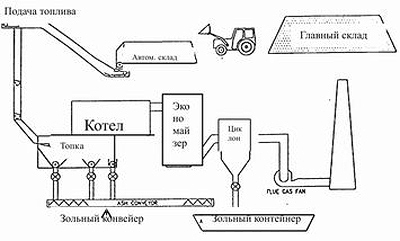
Рис. 1. Схема котельной на биотопливе (щепе)
Как правило, различают три типа оборудования: для сжигания облагороженного биотоплива с влажностью 5–15%; для сухого топлива с влажностью 15–35%; для влажного топлива с влажностью 35–60%.
Нужно отметить, что чем выше влажность топлива, тем дороже обходится производство тепла, тем больше котел, топка, мощность вентиляторов, склад для хранения топлива, риск смерзания и т. д. Кроме влажности определяющими характеристиками топлива при выборе оборудования являются форма и зольность.
Оборудование для сжигания биотоплива состоит из ряда компонентов, которые могут быть сгруппированы следующим образом:
- система складирования и подачи топлива;
- система сжигания;
- система дымовых газов;
- система золоудаления;
- система регулирования и контроля.
Типичная установка для сжигания щепы представлена на рис. 1.
Существует несколько способов складирования и подачи топлива. Ниже описывается один из них, показавший себя наиболее приемлемым при сжигании щепы.
Топливный склад
Конструкция и размеры топливного склада должны соответствовать типу топлива, размеру котельной, условиям поставки топлива и времени работы котельной. Комбинация наружного склада с запасом топлива примерно на неделю работы котельной с небольшим складом с автоматической подачей, рассчитанным примерно на 48 часов работы, − наиболее часто встречающееся решение.
Наружный склад, обслуживаемый тракторами, строится на асфальтовой или бетонной площадке. С целью защиты от попадания пыли за пределы склада он ограждается забором либо возводится полностью крытым. Такой тип склада очень рентабелен, а возможность применения тракторов снижает затраты по его обслуживанию и обеспечивает бесперебойную работу.
Подача топлива на склад может быть решена в разных вариантах. Для этого могут быть использованы самые различные виды машин. Исключение составляют склады с недостаточно высокой крышей, что препятствует использованию транспортных средств с верхней загрузкой. Существует множество различных транспортных средств, так что выбрать оптимальное решение нелегко.
Как правило, автоматический склад соединен с главным складом и обслуживается тракторами или, в отдельных случаях, тельферами с манипулятором. Если позволяет пространство, можно разгружать щепу прямо на автоматический склад. Для того чтобы упростить загрузку, автоматический склад не имеет ворот, и, поскольку ширина скребкового транспортера около 5 м, тракторы могут наезжать на толкатели. Высота загрузки топлива в автоматическом складе ограничена примерно 3 м и зависит от мощности гидравлической системы.
Подача топлива
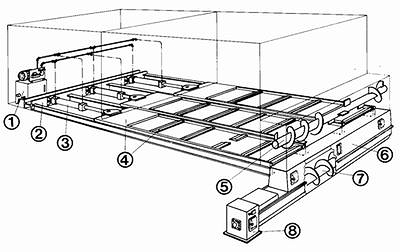
Рис. 2. Автоматический склад со штанговыми толкателями
1. Гидравлическая станция
2. Упорная балка цилиндров
3. Гидравлические цилиндры
4. Толкатели
5. Вал-разрыхлитель
6. Приемный канал
7. Выгружной шнек
8. Привод шнека
Для подачи топлива с автоматического склада используются шнековые и скребковые транспортеры. В последние годы предпочтение отдается скребковым транспортерам, поскольку они более прочны и менее чувствительны к качеству топлива. К тому же они позволяют изменять направление скребкового конвейера, что уменьшает количество необходимых трансмиссий и приводов.
Склады, снабженные донными гидравлическими штанговыми толкателями, являются наилучшим решением и используются в большинстве случаев. Толкатели двигаются вперед или назад по полу склада в зависимости от положения гидравлического привода. Когда толкатель доходит до конечного положения, давление возрастает и переключает привод на обратное направление.
Толкатель подает топливо на вал-разрыхлитель (установлен в конце автоматического склада), служащий для выравнивания топлива и особенно необходимый в случаях смерзания топлива. Вал также выполняет функцию управления загрузкой шнекового конвейера, выгружающего топливо со склада. Это происходит с помощью устройства, отключающего или запускающего штанговые толкатели. Система конвейеров подает топливо в промежуточный бункер, расположенный над топкой или перед топкой. Этот бункер выполняет три функции:
- обеспечивает равномерную подачу топлива на решетку толкателем;
- служит «воздушным замком», препятствующим обратному возгоранию;
- предотвращает присосы воздуха и обеспечивает возможность правильного регулирования процесса горения.
Топливный бункер снабжен в верхней части заслонкой, которая при прекращении подачи топлива закрывается.
Сжигание щепы
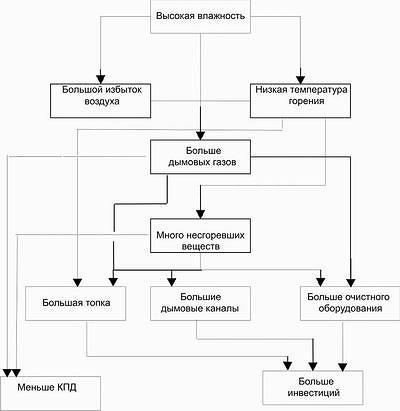
Рис. 3. Влияние влажности топлива на работу оборудования
Выбор подходящего оборудования в принципе зависит от того, сухую или влажную щепу предполагается сжигать. Если щепа влажная, предпочтительно остановиться на конструкции котла с предтопком, имеющего тяжелую обмуровку без или с небольшими поверхностями нагрева, чтобы обеспечить достаточно высокую температуру для полноценного сжигания. Причина заключается в том, что при сжигании влажного топлива образуется много газов и требуется больше тепла, чтобы испарить содержащееся в топливе большое количество влаги. Топочные газы не должны вступать в контакт с поверхностями нагрева до того, как их горючая составляющая не выгорела полностью. Если этого не происходит, то конечным продуктом будет являться не СО2, а промежуточный продукт − СО. Когда газы полностью сгорели, они отдают тепло охлаждаемым водой поверхностям нагрева котла.
Если щепа сухая, то температура горения может быть слишком высокой. Это, помимо нежелательных выбросов NO2, может привести к серьезным повреждениям обмуровки, в большинстве случаев не приспособленной к температурам свыше 1300°С. Поэтому при сжигании сухого топлива в топке должны иметься охлаждаемые поверхности для отбора излишнего тепла.
Граница между сухим и влажным топливом лежит в районе 30% влажности. Обычно указывается и высшая граница влажности − 55%. Если влажность топлива выше, очень трудно достичь хорошего сгорания и обеспечить достаточную мощность «нормального», не приспособленного для сжигания топлива такой степени влажности оборудования.
На рис. 3 схематически показано, как влияет на оборудование влажность топлива.
Загрузка топки и решетки
Загрузка топки может происходить различными способами: либо с помощью шнека, либо толкателя (стокера). Последнее решение является преобладающим. Стокер представляет собой гидравлический скребок, расположенный на дне топливного бункера и подающий топливо на решетку. Стокер может считаться первой подвижной ступенью решетки. В зависимости от размеров топки предусматривают один или несколько стокеров. При мощности котла в 4 МВт стокеров обычно два.
В установках мощностью от 2 до 20 МВт чаще всего используются колосниковые решетки. На решетке происходят следующие процессы:
- прогрев и сушка топлива, происходящая в верхней части;
- выход летучих веществ, горючих газов (СО, Н2, СН4, которые затем сгорают);
- горение коксового остатка (углерода).
Решетки чаще всего бывают наклонными и подвижными, чтобы обеспечить достаточное и контролируемое передвижение топлива в топке. Подвижная решетка, как показывает опыт, препятствует также спеканию золы в большие, мешающие нормальному процессу горения комки. Решетка состоит из нескольких секций. Каждая вторая секция может двигаться вперед и назад, проталкивая топливо. Подвижность достигается с помощью гидравлического привода. При большем количестве топлива частота движений решетки увеличивается. Балки, на которых крепятся элементы решетки, часто имеют водяное охлаждение, в то время как секции решетки охлаждаются первичным воздухом.
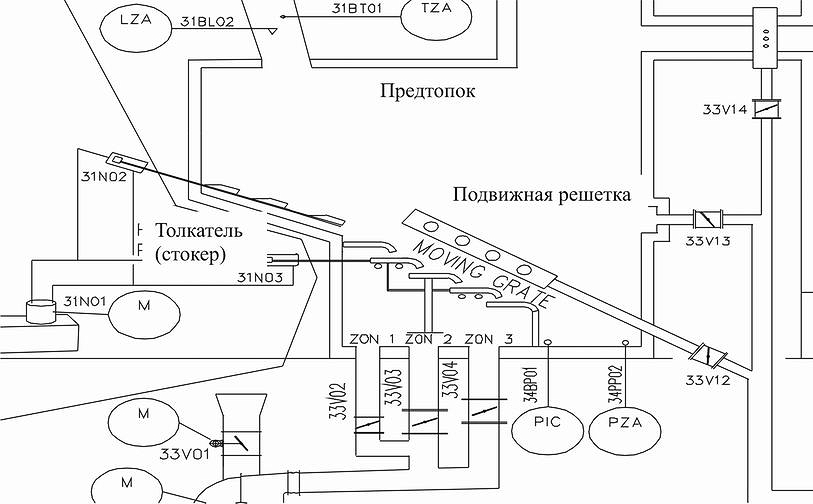
Рис. 4. Подвижная решетка
Воздух
Воздух, необходимый для сжигания топлива, делится на первичный и вторичный. Первичный воздух подается под решетку и предназначен главным образом для сушки и газификации топлива, а также для сжигания той части топлива, которая не газифицируется.
Первичный воздух подается в несколько зон под подвижной решеткой. Зон этих как минимум две, а в установке мощностью 4 МВт их обычно три, а иногда и четыре. Каждая зона имеет свою заслонку и снабжается воздухом от вентилятора первичного воздуха.
Вторичный воздух подается отдельным вентилятором, часто с регулируемым числом оборотов. Воздух должен подаваться с большой скоростью через регулируемые сопла так, чтобы обеспечить хорошее смешивание газов и воздуха.
Третичный воздух − это тоже вторичный воздух, подаваемый на выходе из топки и предназначенный для обеспечения окончательного сгорания. Источником его является чаще всего вентилятор вторичного воздуха.
Примеры топок
Существует много поставщиков такого котельного оборудования, о котором идет речь в этой статье. Шведские изготовители представляют собой самую большую группу. Среди них можно назвать KMW, Saxlund, Hotab, Järnförsen, Osby, Zander и Ingerström, TEEM. Эти производители, чьи конструкции решеток и систем подачи топлива могут заметно отличаться друг от друга, поставляют котлы как для сухого, так и для влажного топлива, причем конструкция приспосабливается к тому виду топлива, которым располагает заказчик.
Котлы
Тепло дымовых газов передается с помощью теплопередающих (конвективных) поверхностей котла посредством водотрубных, жаротрубных дымотрубных установок. Вертикальный жаротрубный котел − наиболее распространенный тип котла. Такие котлы обладают существенным преимуществом: они не занимают много места и удобны в эксплуатации, поскольку очистка проводится в вертикальном направлении снизу. Существует множество конструкций котлов. Они могут быть интегрированы с топкой или расположены рядом с ней или над ней. Котел может также стоять отдельно и соединяться с топкой через газоход.
Система дымовых газов
Система дымовых газов предназначена для отвода дымовых газов после их прохождения через котел и удаления их через дымовую трубу. Система состоит, как правило, из дымососа, системы очистки дымовых газов и газоходов. Дымосос − это очень важный, можно сказать, критический компонент оборудования. Он должен работать постоянно, поддерживая разрежение в топке. Работа дымососа регулируется различными способами: либо с помощью шибера, либо, что обычно применяется в современном оборудовании, с помощью регулятора числа оборотов, что выгоднее с точки зрения энергосбережения.
Количество дымовых газов в системе зависит от вида топлива, его влажности, температуры дымовых газов и избытка воздуха. Системы дымовых газов в небольших котельных чаще всего рассчитаны на максимальную температуру дымовых газов 250°С. Рабочая температура дымовых газов в таких установках составляет 200°С. Уменьшение коэффициента избытка воздуха с 2 (О2=10,7%) до 1,6 (О2=7,6%) снижает количество дымовых газов примерно на 20%. Уменьшение влажности с 50 до 40% снижает количество дымовых газов примерно на 7%.
В последнее время система дымовых газов часто дополняется системой так называемой рециркуляции дымовых газов. Это означает, что дымовые газы после очистки возвращаются в топку и используются в качестве воздуха для горения. В результате интенсивность горения снижается, поскольку в дымовых газах мало кислорода. Другой важный природоохранный и экономический эффект рециркуляции − снижение выбросов NO2.
Рециркуляция дымовых газов осуществляется с помощью отдельного вентилятора, установленного после системы очистки, который подает дымовые газы в топку, чаще всего над решеткой. Регулирование вентилятора может осуществляться как шибером, так и числом оборотов на основе показаний датчика температуры в топке. Вентилятор включается тогда, когда температура превышает, например, 1000°С. Рециркуляция дымовых газов особенно актуальна, когда ожидаются проблемы со слишком высокой температурой в топке. Такие проблемы часто возникают, если в котле используется более сухое, чем расчетное, топливо.
Очистка дымовых газов
Существует много конструкций для улавливания летучей золы. С определенной степенью упрощения можно разделить их на следующие основные типы:
- динамические (инерционные) золоуловители, в которых используются гравитационные и инерционные силы, влияющие на уносимые с газом частицы;
- текстильные фильтры, изготавливаемые, как правило, из волокна;
- электрофильтры, в которых используются электростатические силы заряженных частиц;
- водяные (мокрые) золоуловители, которые вымывают частицы водой, распыляемой в уходящих газах.
Степень очистки выражается в отношении уловленной золы к общему количеству золы до работы золоуловителя. Обычно количество золы измеряется как до, так и после золоуловителя.
Степень очистки = (Содержание золы до золоуловителя − Содержание золы после золоуловителя) : Содержание золы до золоуловителя х 100%.
Степень очистки может быть уточнена только тогда, когда известно распределение частиц золы по размерам.
Для того чтобы описать летучую золу, используются диаграммы распределения частиц по размерам, или, как их ещё называют, рассевочные кривые. Кривая выводится путем определения количества частиц разного размера при просеивании золы через проволочные сита с различным диаметром отверстий. Ту часть золы, которая не просеивается через сито, взвешивают и учитывают её процентное отношение к общему количеству просеиваемой золы.
Золоуловитель с достаточно умеренной степенью очистки может показать очень высокий коэффициент очистки, если он используется для очистки газов с высоким содержанием крупных частиц золы, скажем 5%. И все равно может оказаться, что выброс летучей золы будет выше допустимого, поскольку общее содержание золы в газах было велико.
Выбор метода очистки зависит от нескольких факторов:
- свойств золы;
- требований по выбросам;
- характера топлива;
- способа сжигания.
Прежде чем выбирать фильтр, необходимо уточнить все эти данные, иначе результат может быть обескураживающим.
Мультициклон − самый распространенный тип динамических золоуловителей. Агрегат состоит из нескольких небольших уловителей типа циклон, соединенных параллельно. Диаметр циклонов варьируется от 125 до 250 мм. Небольшие циклоны помещены в кожух, на дне которого чаще всего имеется пылевой бункер. Количество циклонов в мультициклоне может быть от 4 до 200. Мультициклоны дешевы, надежны и прекрасно выполняют свою роль при сжигании твердого топлива до тех пор, пока требования к очистке не особенно высоки, поскольку они не улавливают наиболее легкие частицы.
Лучше всего мультициклоны работают при большой и постоянной нагрузке. Для того чтобы они функционировали нормально при нагрузке около 50% от номинальной, существуют два метода. Один из них состоит в том, что уже очищенные дымовые газы вновь подают на вход мультициклона, чтобы увеличить поток газов и, соответственно, сохранить необходимую степень очистки (полнопоточное регулирование). Другой метод построен на регулировании соотношения потоков или частичном отключении фильтра. При очень больших колебаниях нагрузки мультициклоны, собственно говоря, непригодны. Впрочем, при низкой нагрузке содержание частиц в дымовых газах и так невелико.
Удаление золы не представляет трудностей. Зола или собирается в золоприемник, или удаляется шнековым либо иным транспортером. Степень очистки в циклонах составляет 85–92% и зависит от содержания тонких фракций в золе. Если допустимый уровень эмиссии летучей золы составляет 300 мг / нм3 сухого газа, то выбор мультициклона в качестве золоуловителя является наиболее целесообразным.
При сжигании щепы содержание частиц золы после мультициклона обычно составляет 160–200 мг / нм3 газов. Мультициклоны имеют стопроцентный доступ для ремонта, поскольку оборудование состоит главным образом из листового металла.
Текстильный рукавный фильтр − общее название для целого ряда золоуловителей, в которых газ проходит через волокнистый материал и частицы золы осаждаются частично на его поверхности, частично между волокнами. В качестве фильтрующего материала используется полиамид, полиэфир, тефлон и другие. Могут использоваться как тканые, так и нетканые материалы, а также их комбинация.
Обычно поверхность фильтра имеет форму рукава, но встречаются также складчатые и плоские кассеты. Рукава натянуты на стальные каркасы и чаще всего расположены вертикально, но существуют и конструкции с горизонтальным расположением рукавов. Газы поступают в рукав, и летучая зола оседает на их внутренней поверхности в виде зольных отложений.
Регулярная очистка фильтров важна для их правильного функционирования. Существует несколько основных методов очистки: встряхивание, обратная продувка и импульсная очистка. Наиболее распространенным методом является импульсная очистка. Она происходит с помощью сжатого воздуха, подаваемого в верхний конец каждого рукава через установленный на трубе мундштук. В этих мундштуках устанавливается сопло Вентури, чтобы быстро преобразовать энергию скорости воздуха в энергию давления. Ударная волна, получаемая таким образом, используется для резкого раздувания рукава, так что зольные отложения при этом отлипают от стенки фильтра.
Такую очистку с успехом проводят на работающем котле. Под фильтрующими рукавами зола собирается в воронки. Текстильные фильтры обеспечивают очень высокую степень золоулавливания и надежны в эксплуатации, пока фильтрующие материалы не повреждены и проводится их очистка. Теплостойкость материала, из которого изготовлены фильтры, ограничивает их использование температурой 240–280°С. Высокое содержание влаги и низкая температура дымовых газов могут быть причиной конденсации в фильтрующем материале и забивания фильтра. Эта опасность особенно велика в момент запуска котла, поэтому в фильтр вмонтированы специальные петлевые трубы для подогрева, чтобы избежать конденсации. Полагается делать также байпас, так что фильтр можно отключать, если его эксплуатационные характеристики не соответствуют требуемым.
Степень очистки в фильтрах очень высока и может в зависимости от нагрузки достигать 99,9%. Сопротивление в фильтре текстильном в сравнении с электростатическими фильтрами велико и составляет при нормальных эксплуатационных условиях 1000–1500 Па.
Фильтры довольно дороги в эксплуатации, поскольку рукава необходимо менять каждые три года. Затраты зависят также и от того, какой материал используется в фильтре. Ремонтодоступность − около 98%.
В электрофильтрах частицы, уносимые с газами, ионизируются при прохождении мимо проволочных электродов (эмиссионных или коронирующих), навитых на вертикальные пластины. Осадительные электроды, выполненные в виде пластин, заземлены, и благодаря разности потенциалов между коронирующими электродами и пластинами частицы золы оседают на осадительных электродах. Как эмиссионные, так и осадительные электроды очищаются встряхивающими устройствами, приводимыми в действие электромоторами, что обеспечивает их постоянное встряхивание.
Электростатические фильтры обеспечивают очень высокую степень очистки, очень надежны, эксплуатационные затраты и затраты на их обслуживание невелики. Степень золоулавливания обычно высока, но она зависит от проводящих свойств золы и размеров частиц золы. Эффективность электростатических фильтров и их размеры в гораздо большей степени, чем у других видов фильтров, зависят от физических и химических свойств золы, и такие фильтры обычно велики и дороги. Падение давления в электростатических фильтрах мало − 100–200 Па, поскольку скорость дымовых газов в них низка. Стоимость обслуживания невелика и составляет около 1% инвестиционных затрат. Ремонтодоступность − 99%.
Конденсация дымовых газов − метод не столько их очистки, сколько утилизации тепла. Тем не менее очищающий эффект метода в отношении золы и других эмиссий весьма значителен. Система конденсации дымовых газов состоит из установки, где дымовые газы насыщаются водой в конденсаторе, в результате чего они охлаждаются. Тепло обычно используется для горячего водоснабжения или в тепловых сетях − локальных или коммунальных. Перед тем как уйти в дымовую трубу, газы обычно снова нагреваются примерно до 100°С. Иногда дымовые газы охлаждаются до очень низкой температуры в увлажнителе, где полученное тепло и влага используются для подогрева воздуха, подаваемого для сжигания топлива. При этом потоки воздуха и дымовых газов увеличиваются, но и повышается количество тепла, которое может быть утилизировано в конденсаторе.
Очистка дымовых газов частично прямая, за счет отделения частиц золы в конденсаторе, частично непрямая, зависящая от уменьшения потребления топлива при повышении КПД котла. Большое значение имеет конструкция для насыщения газов влагой. Это может быть просто канал, куда впрыскивается вода, или специально сконструированный скруббер с равномерным распределением воды в газах и продолжительным контактом газов с водой.
Конденсатор всегда сочетается с каким-либо другим оборудованием для очистки газов. Оно варьируется от случая к случаю; есть примеры, где используются мультициклоны, циклоны грубой очистки и рукавные фильтры.
Степень очистки при конденсации находится в интервале 40–90%, в зависимости от топлива и содержания золы в газах. Можно достичь снижения эмиссии до 30 мг / МДж топлива или 100–125 мг / нм3 газов. Степень очистки конденсата при конденсации дымовых газов зависит, с одной стороны, от того, какие золоуловители установлены до контактного теплообменника, с другой − от того, какое топливо используется. Обычно хороший эффект дает разделение потоков воды от скруббера и контактного теплообменника, поскольку вода в последнем намного чище.
При сжигании древесного топлива и торфа водяная очистка относительно проста. Часто проводится обычное осаждение, иногда используются флокулянты. Показатель рН регулируется так, чтобы он не превышал 6,5.
Водная фаза после очистки может использоваться вновь в качестве воды для скруббера, осадок идет в канализацию. Осадок часто используется для увлажнения золы.
В табл. 1 показаны достоинства (+) и недостатки (-) различных систем золоулавливания.
Приблизительно правило, касающееся закупочной цены мультициклонов, текстильных и электрических фильтров, таково: они соотносятся друг с другом как 1:3:4.
Как правило, для очистки дымовых газов при сжигании биотоплива достаточно мультициклона. Но в определенных случаях, в частности если котельная находится в плотно заселенном районе, требования к выбросам золы повышаются и обойтись только мультициклоном не удается. Наиболее приемлемой альтернативой в таких случаях является установка конденсатора дымовых газов после мультициклона, что в большинстве случаев и делается. Таким образом достигается более высокая степень очистки и повышается коэффициент полезного действия котельной. Как уже было сказано, в отдельных случаях КПД может превышать 100%.
Шлакоудаление
Зола, образующаяся при горении, делится на топочную и летучую. Топочная зола и шлак удаляются непосредственно из топки, в то время как летучая зола уносится дымовыми газами и улавливается оборудованием для очистки дымовых газов. В топках с подвижной решеткой большая часть золы удаляется с помощью мощного, поперечно расположенного в конце решетки шнекового транспортера или другого специального устройства. Шнек рассчитывается так, чтобы он мог справиться со спекшейся, твердой золой. Эти узлы подвергаются большим нагрузкам и должны быть защищены от слишком высокой температуры. Это означает, что надо следить, чтобы транспортер был всегда покрыт защитным слоем золы. В небольших котельных зола часто удаляется вручную. Летучая зола, составляющая лишь небольшую часть от общего количества золы, улавливается.
Мокрое шлакоудаление
При этом способе зола, как топочная, так и летучая, падает в заполненный водой желоб, откуда она транспортируется далее. В желобе, расположенном под топкой, под уровнем воды имеются «воронки» для подачи первичного воздуха в различные зоны топки. Для изготовления зольных транспортеров используется обычная сталь, поскольку зола имеет щелочную реакцию и рН воды может достигать 12. При значении рН свыше 10 ржавления не происходит. Если рН воды слишком низок, его можно корректировать с помощью гидроксида натрия.
Влажное золоудаление удобно и надежно. Исчезают проблемы с запылением или тлеющей горячей золой. При этом способе золоудаления помимо всего прочего легче герметизировать топку. Впрочем, у этого метода есть и недостатки. Износ подвижных частей в воде может быть весьма заметным и требовать больших ремонтных работ. Щелочная вода представляет собой определенный риск для здоровья персонала. К тому же такая конструкция дороже и требует большей высоты помещения котельной.
Сухое шлакоудаление
Этот способ шлакоудаления может осуществляться как вручную, так и механически или пневматически. Пневматический транспорт золы обычно применяется в котельных мощностью свыше 10 МВт, в то время как в небольших котельных преобладает механическое золоудаление. Как уже было сказано, механическое шлакоудаление происходит с помощью шнековых транспортеров, расположенных под уровнем дна топки с одной из её сторон. Этот транспортер забирает золу не только в конце решетки, но и проваливающуюся через решетку. Эта зола подается на шнек толкателями в каждой из первичных зон. На этот же шнековый транспортер подается зола после золоулавливания, например из циклонов.
Зола в конечном итоге поступает в герметичный контейнер, чтобы избежать пыли. Помимо герметичности контейнер должен быть хорошо изолирован и находиться вне помещения. Удаление золы может происходить и с помощью ленточного транспортера, но шнек предпочтительнее, поскольку он может работать при больших углах наклона.
Сухое шлакоудаление очень распространено, прежде всего, по причине его дешевизны. Недостатками сухого шлакоудаления являются пыль, а также то, что при этом бывает трудно избежать присосов воздуха в топку через шнековый транспортер.
Системы регулирования
Современные котлы, работающие на биотопливе, оснащены более или менее сложными системами регулирования, автоматизирующими эксплуатацию котла. Система регулирования должна обеспечивать работу котла в так называемом модульном режиме, что означает, что мощность котла все время регулируется так, чтобы соответствовать потребностям тепловой сети. В этом случае все котельное оборудование, по крайней мере дымососы, работает постоянно. Модульный режим тем не менее возможен только в тех случаях, когда котел работает с нагрузкой выше минимальной, которая обычно составляет около 25% максимальной мощности.
При нагрузке ниже минимальной котел работает в режиме «включен / выключен»: котел работает только часть суток, а в остальное время его останавливают. Крайне желательно, чтобы котельные на биотопливе работали в модульном режиме максимальное количество времени. Не существует единой системы регулирования для работающих на биотопливе котлов. Такие системы, изготовленные различными производителями, могут значительно отличаться. Для небольших, работающих на щепе котлов существует потребность в автоматическом управлении уровнем топлива в топливном бункере, тягой для поддержания постоянного разрежения в котле и топке, а также температурой воды на выходе из котла для поддержания соответствия мощности котла потребностям сетей.
Регулировка наличия топлива в топливном бункере важна по трем причинам: чтобы обеспечить равномерную подачу толкателем топлива на решетку; чтобы обеспечить «воздушный замок» и воспрепятствовать обратному возгоранию; чтобы воспрепятствовать неконтролируемой подаче воздуха и таким образом обеспечить хорошее управление процессом горения.
Уровень топлива в топливном бункере должен быть всегда выше минимума, чтобы не дать возможности пламени распространиться с решетки назад в бункер. Чтобы этого не произошло, в верхней части топливного бункера имеется специальная крышка (демпфер), который автоматически закрывается, если в бункере нет топлива, и препятствует распространению огня. Помимо этого имеется автоматический разбрызгиватель воды (спринклер), включающийся автоматически в тех случаях, когда температура в бункере слишком высока. В бункере установлен также температурный датчик, дающий сигнал тревоги, так что оператор котельной может включить спринклер вручную.
Минимальный уровень топлива в бункере часто регулируется с помощью инфракрасного датчика. Передатчик и приемник расположены по обе стороны, так что, когда уровень опускается до минимального, включается автоматическая подача топлива с топливного склада. Загрузка топлива останавливается либо через определенное время, либо с помощью ещё одного датчика.
Количество топлива между минимальным и максимальным уровнем зависит от размеров котла. По практическим соображениям подача топлива в бункер не должна происходить чаще, чем 10 раз в час. Поддержание разрежения в топке и в котле очень важно с точки зрения безопасности. Разрежение, задаваемое в пределах 5–10 мм водного столба, регулируется механическим шибером на дымососе или, в отдельных случаях, регулированием числа его оборотов. Кратковременное повышение давления допустимо, но только на очень короткое время − 10–15 секунд.
Регулятор мощности является наиболее важным элементом системы. Его главной задачей является обеспечение того, чтобы температура воды на выходе из котла поддерживалась на постоянном, заранее выбранном уровне, например 110°С. Для поддержания этой температуры требуется управление подачей воздуха, движением решетки и подачей топлива.
Как это в принципе происходит? Если истинное значение температуры воды ниже, чем желаемое, а сетевая нагрузка возрастает, то регулятор мощности обеспечивает следующие меры:
- дается команда на увеличение оборотов вентиляторов первичного и вторичного воздуха;
- дается команда на увеличение частоты движения решетки;
- дается команда на более частую подачу топлива толкателем.
В результате этих мер увеличивается также подача топлива в бункер со склада, поскольку бункер опорожняется быстрее, в то же самое время дымосос увеличивает обороты вследствие увеличения количества газов. В дополнение к указанной схеме в современных котлах предусмотрено также автоматическое регулирование содержания О2 в дымовых газах. Это осуществляется с помощью отдельного регулятора на вентиляторе вторичного воздуха, который, таким образом, управляется в зависимости от нескольких параметров.
Очень важно также поддерживать на заданном уровне температуру обратной воды, которая на входе в котел никогда не должна быть ниже 70°С. Для того чтобы достичь этого, должен иметься обводной контур (байпас) с насосом, обеспечивающим подмешивание воды до нужной температуры.
Регулирование байпасом может происходить с помощью регулятора температуры или насоса с регулируемым числом оборотов. Иногда байпасом управляют вручную. Необходимые параметры устанавливаются поставщиками при запуске котельной, они же производят наладку систем регулирования. Тем не менее необходимо постоянно следить за настройкой и, возможно, корректировать её, поскольку отдельные параметры эксплуатации могут изменяться, например вид и качество топлива.
Каждая котельная должна иметь систему безопасности, обеспечивающую оповещение и остановку котла, если возникает какая-то угроза безопасности эксплуатации.
Сжигание соломы
В лесной местности целесообразно использовать древесные отходы для получения тепла, в сельскохозяйственных районах имеет смысл применять солому, лузгу и другие продукты сельского хозяйства.
Рассмотрим процесс сжигания соломы. Один из самых простых способов, который активно применяется в Европе (особенно в Дании), − сжигание целых тюков соломы. Вначале тюк соломы с помощью фронтального подъемника загружается через открытую топочную дверцу в топку, затем дверца закрывается и топливо зажигается. Воздух для горения подается сверху. Установка работает циклически.
Автоматизация сжигания соломы достигается за счет первоначального её измельчения. Возможна также непрерывная подача целых тюков соломы без предварительного измельчения.
Татьяна ШТЕРН, к. т.н., доцент