Есть идея!
Изобретатель или человек, склонный к техническому творчеству и движимый желанием реализовать свою идею, может выбрать несколько путей для достижения цели.
Самый простой и естественный – сделать все своими руками. Это удел людей умелых, тех, кто имеет возможности и навыки работы с металлом. В YouTube можно найти десятки роликов, в которых наши умельцы демонстрируют свои достижения, иногда весьма впечатляющие. Это не только станки для работы с металлом или древесиной, но и автомобили, речные суда, и даже самолеты и вертолеты. Вероятно, какая-то часть новых технических решений находит продолжение в создании профессионального проекта и его воплощения в промышленности. Однако в России все еще сильно недоверие к новому, особенно к своему, отечественному. Вот если импортное, тогда другое дело…
Для большинства, в том числе для инженеров, не обладающих такими возможностями, более естественным кажется вариант оформления своей идеи на бумаге, закрепления своих прав патентом в ожидании больших вознаграждений в будущем. Однако хочется предостеречь оптимистов. В Гражданском кодексе РФ есть глава 72 «Патентное право», в ней прописаны возможности граждан по защите своих прав на изобретения, полезные модели и промышленные образцы. Каждый претендующий на звание изобретателя должен правильно оформить заявку, заплатить за экспертизу (которая обязана доказать, что ничего подобного мир не знает) и, в случае положительного результата, ежегодно платить пошлину за поддержание патента.
Вам это надо? К счастью, в законе есть интересный пункт: при опубликовании в открытом доступе техническая идея через шесть месяцев теряет патентноспособность. То есть становится чистой как ангел, и претендовать на овладение ею не смеет никто, в том числе автор.
У тех, кто не молится золотому тельцу и готов бесплатно осчастливить человечество, есть прекрасная возможность сделать это. Поделитесь своими гениальными техническими мыслями в нашем журнале, и Родина вас не забудет. Никто не обязан патентовать все, что пришло в голову. Пожалейте себя и других!
Мне кажется, что патентование идей бессмысленно. Идеи носятся в воздухе и принадлежат всем. Есть смысл патентовать реализацию идеи в виде полезной модели. «Идея – 5%, а потение – 95%», – говорил Т. А. Эдисон. Сначала докажи, что идея работает, а потом пей шампанское. Но наше патентное право даже не выдвигает такое условие. Достаточно, чтобы техническая идея имела мировую новизну, а остальное бюрократов не интересует.
С учетом вышесказанного автор предлагает схему оцилиндровочного станка (линии) для производства строительных бревен. Идея, заложенная в эту схему, достаточно проста и никогда не проверялись нами на новизну. Единственное, что можно сказать: реально работающие станки такого типа нам не известны. Давайте вместе разбираться, может ли это работать и какие выгоды обещает.

В основе линии ножевая головка с ножами полукруглого профиля (рис. 1).
Изготовить ножи не составляет труда. Из листа инструментальной стали толщиной не менее 10 мм вырезается заготовка квадратной формы со стороной (D + А) мм, где D – заданный диаметр оцилиндрованного бревна, обычно 180–320 мм (с шагом 20 мм), А – величина, дополняющая этот размер до ширины ножевой головки. Затем точно по центру квадрата вырезается круг диаметром D. По окружности заготовки делается фаска под углом, соответствующим углу резания строгальных ножей (45 ± 10°). После этого заготовка разрезается пополам для получения комплекта двух совершенно одинаковых ножей.
Для увеличения срока службы режущего инструмента желательно оснастить ножи пластинками твердого сплава. Пластинки получают методом порошковой металлургии, то есть прессования и спекания порошков на основе карбида титана или аналогичных материалов. Это означает, что режущая пластинка может быть любой формы, в том числе полукруглой.
Естественно, при использовании полукруглой твердосплавной пластины размеры заготовки нужно изменить с учетом размеров пластины. Толщина строгального ножа должна быть максимально возможная, так как выступающая (консольная) часть ножа при диаметре 320 мм может достигать 160 мм. Сегодня наиболее толстые прямолинейные ножи – до 18 мм – используются в лущильных станках. Вероятно, ножи толщиной 18 мм – оптимальный вариант, поскольку обеспечивают высокую жесткость инструмента. Хотя следует заметить, что деформация ножа при резании практически не скажется на правильности формы изделия.
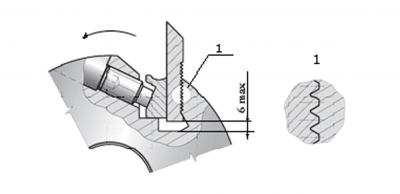
Толстые ножи потребуют некоторых конструктивных изменений ножевой головки, но эта задача вполне решаемая, как видно на схеме узла крепления профильного ножа в головке (рис. 2).
Рифление задней стенки позволяет надежно фиксировать нож, предотвратить его смещение под действием центробежной силы. Это имеет особое значение для толстых и тяжелых ножей.
Для выставки ножей достаточно использовать простые шаблоны круглой формы заданного диаметра. Подходящие режимы работы можно выбрать только в ходе практических испытаний на экспериментальном образце станка. Следует найти оптимальное число ножей в головке (2, 3 или 4), определить максимальный допустимый припуск на строгание и максимальную скорость подачи с учетом этого припуска, оценить качество обработки поверхности при разных режимах работы.
Теперь об особенностях конструкции линии оцилиндровки. Линия должна начинаться с современного сканера или простого измерителя бревен для определения комлевого и вершинного диаметра бревна. Кроме узлов резания, критически важными в линии являются механизм центрирования бревна относительно центра получаемого цилиндра и механизм подачи бревна.

После подачи бревна (обязательно комлем вперед!) на подающий рольганг его следует ориентировать по оси цилиндра с помощью подъема-опускания опорных роликов. Механизм подачи можно заимствовать в окорочных станках (на рис. 3 условно показаны два подающих вальца).
Первая нижняя режущая головка образует полуцилиндрическую базовую поверхность на бревне. Расстояние между узлами резания должно быть достаточно большим (примерно 0,5 м), чтобы обеспечить надежное базирование.
Разница между комлевым и вершинным диаметром бревен может быть довольно большая. Для 6-метровых бревен средним диаметром 24 см она в среднем составляет примерно 6 см, то есть полный припуск на обработку будет около 30 мм и может оказаться не по зубам одной паре ножевых головок. Современные фуговальные станки (при работе с сухим материалом) могут снимать слой древесины до 8 мм. При строгании сырой древесины его, вероятно, удастся увеличить до 10 мм. Следовательно, для надежной работы линии оцилиндровывания в зависимости от длины и толщины бревен потребуется 3–4 пары ножевых головок, для которых заданный диаметр обработки последовательно уменьшается с шагом 2 см.
Такой принцип обработки может подойти и для обработки тонкомеров, то есть лесоматериалов толщиной 10–20 см. В этом случае объем снимаемой древесины меньше и можно обойтись одной или двумя парами шпинделей.
В конструкции следует использовать гидрозажимные ножевые головки, замена которых занимает очень мало времени. На предприятии достаточно иметь 2–3 комплекта ножевых головок с ножами нужных размеров, чтобы обеспечить бесперебойную работу оборудования.
Следует проверить вариант обработки бревен при чередовании встречного и попутного фрезерования. Если первый шпиндель работает при вращении навстречу движению бревна, то второй можно вращать в попутном направлении. Это значительно снизит нагрузку на механизм подачи.
Не исключен и кардинальный вариант: установка на линии полного набора шпинделей, перекрывающего весь диапазон обработки (например, от 18 до 38 см в комлевом диаметре). Это будет 8–12 пар шпинделей, из которых в работу можно запускать только требуемые для того или иного сортимента по данным измерительной системы. (Потребуется разработка специального механизма подъема и опускания шпинделей.) Чем больше ножевых головок в линии, тем меньше снимаемый слой древесины на один нож и тем выше качество обработки и выше оптимальная скорость подачи материала.
Основной станок следует спроектировать в модульном варианте. Модуль должен представлять собой узел с верхним и нижним шпинделями на отдельной раме и легко состыковываться с другими модулями.
Основное преимущество предлагаемого оборудования – высокая производительность. Все известные оцилиндровочные станки работают со скоростью подачи ножевой головки 1–2 м/мин. Строгание полукруглыми ножами выполняется со скоростью до 40 м/мин и больше с достижением высокого качества поверхности и высокой точности заданных размеров.
Важным условием эффективной работы линии оцилиндровки является подключение ее к эксгаустерной системе предприятия. Каждый узел резания должен быть оснащен стружкоприемником. При работе на скорости 40 м/мин с бревнами толщиной 24 см часовая производительность линии (по сырью) составит примерно 120 м3. Около 20% этого объема превратятся в высококачественную мелкую стружку, пригодную для использования в ЦБП, производства топливных брикетов или гранул, используемую в качестве подстилки для домашних животных или (в худшем случае) топливо. Каждый час будет образовываться примерно 60 нас. м3 стружки, которую незамедлительно нужно отправлять пневмотранспортом в бункеры на хранение. Этот полуфабрикат может стать важным дополнительным товарным продуктом, снижающим себестоимость продукции и повышающим прибыль предприятия.
К недостаткам предлагаемой модели следует отнести высокую требовательность к прямолинейности сортимента и правильности поперечного сечения. Возможна, конечно, обработка бревен с нарушением формы, но при этом резко увеличиваются потери в стружку и нагрузка на узлы резания.
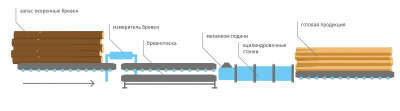
Линия оцилиндровки может работать в составе домостроительного комбината, тогда последним узлом в ней может быть узел формирования укладочного паза и компенсационного пропила. При высокой скорости обработки такая линия может найти применение и в лесопильном производстве. Один поток можно выделить для работы с оцилиндрованными бревнами. Это даст несомненный положительный эффект, так как отпадет проблема образования и использования горбылей как полуфабриката переменного сечения. Вместо горбыля можно получать продукт постоянного сечения, который после сушки и профильного строгания легко превращается в обшивочные доски типа блок-хаус.
Участок оцилиндровки лесоматериалов может быть организован по приведенной схеме (рис. 4). Общая длина линии составит примерно 25–30 м. Заточка строгальных ножей производится по задней грани, поэтому не потребуется специальное заточное оборудование.
А далее есть только один вариант действий: доверяй и проверяй.
Текст Владимир Волынский