Что такое скримбер, или правильно ли мы измельчаем древесину
Переработка вторичного сырья лесозаготовки и деревообработки, как правило, начинается с измельчения в рубительной машине, которая выполняет самую тяжелую работу – разрушает древесину в направлении наибольшей прочности, то есть вдоль волокон.
Так производят технологическую или топливную щепу. Из круглых лесоматериалов можно сразу получить стружку (минуя этап щепы), а путем истирания прогретых сортиментов – волокна. Эти полуфабрикаты затем используются для производства стружечных или волокнистых плит, топливных гранул или брикетов, древесно-полимерных композитов.
Очевидно, что любой материал лучше разрушать в направлении минимальной прочности. В случае древесины – поперек волокон. Прочность древесины при растяжении поперек волокон в 20–50 раз ниже прочности при растяжении вдоль волокон. Тем не менее на стадии первичного измельчения господствуют рубительные машины, разрушающие древесину вдоль волокон.
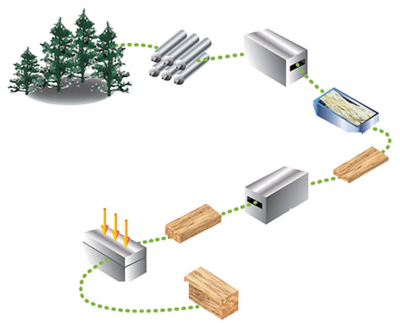
Измельчать древесину поперек волокон, то есть расщеплять на волокна, можно путем раскалывания или раздавливания при прокатке через вальцы. Еще 30 лет назад в Австралии было создано предприятие по производству материала скримбер (Scrimber). В качестве сырья использовались стволы молодых деревьев после рубок ухода. Отсортированный кругляк подавали в раздавливающие вальцы для продольного расщепления без разрушения структуры древесины, а затем в аппарат с профильными вальцами, где полученная масса разравнивалась с сохранением направления волокон и из их равномерно распределенных прядей формировался ковер. Непрерывное полотно из волокнистой массы высушивали до влажности 5%, разделывали на заготовки, которые укладывались одна на другую, подпрессовывались, и полученные «слоеные пироги» раскраивали на продольные блоки длиной 12 м. В индукционном прессе из блоков формировали продукцию конечной плотности и требуемых размеров. Полученные таким способом балки применялись в строительстве, промышленности и для декоративных целей.
Эстафету подхватила канадская фирма TimTek, выпускаемый ею аналогичный материал называется скримтек (Scrimtek). Упрощенная схема производства скримбера следующая (рис. 1).
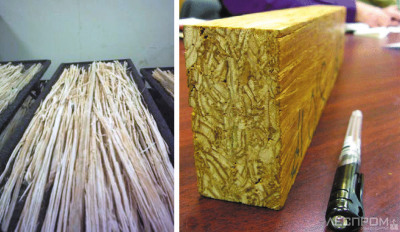
В качестве сырья для производства скримбера можно использовать маломерную и низкосортную древесину почти всех пород, полученную при рубках ухода, а также деревья, пораженные насекомыми или пострадавшие от пожара. Стволы диаметром 8–18 см после окорки и прирезки на нужную длину раздавливаются на линии вальцовых станков – подвергаются скриммингу. Получаемый в итоге материал сохраняет волокнистую структуру древесины и называется Scrim (рис. 2).
Скрим (с диаметром пучков волокон около 7 мм), высушенный камерным способом до влажности 20%, смешивается со связующим (примерно 12% фенолоформальдегидной смолы по сухому остатку) и снова подсушивается до влажности 6–7%. Далее собирается в пакет и после холодной подпрессовки окончательно прессуется в горячем прессе при высоком давлении.
Скримбер отличается высокой плотностью (до 900 кг/м3 и более) и прочностными показателями, превосходящими даже прочностные показатели шпоновых досок LVL. К тому же скримбер-брусья и доски характеризуются очень низким водопоглощением, высокой стабильностью формы и размеров, поэтому используются в каркасном домостроении, производстве окон, дверей и покрытий пола, а также в мебельной индустрии.
В конце 1990-х годов производство подобного материала из бамбука было налажено в Китае. Бамбуковые стволы после раскроя на нужную длину (в зависимости от размеров пресса) и радиального раскалывания превращаются в полосы, которые пропускаются через специальный вальцовый станок, в котором распускаются на волокна. Волокнистая масса пропитывается раствором фенольной смолы и высушивается до влажности не выше 10%, а затем либо закладывается в формы и прессуется при очень высоком давлении (60 МПа) с получением брусьев плотностью до 1300 кг/м3, либо формируется как ковер, из которого горячим прессованием изготавливают плиты толщиной от 15 до 40 мм.
Скримбером сегодня также стали называть композитный материал из полос лущеного шпона толщиной примерно 2 мм. Шпон пропитывается синтетической смолой, высушивается и прессуется под давлением с получением брусьев плотностью 780–940 кг/м3. В России подобный материал называют древесно-слоистым пластиком. Его изготавливают из тонкого березового шпона в виде плит толщиной до 60 мм и плотностью до 1200 кг/м3 и используют как заменитель цветных металлов в машиностроении.
Вообще технология раздавливания древесины весьма перспективна в России, где сегодня избыток лиственных балансов, причем довольно дешевых. Новый материал может составить серьезную конкуренцию плитам OSB, сырьевая база которых ограничена. Для производства волокнистых плит MDF требуется сравнительно дорогая стволовая древесина, к тому же размол на волокна – энергоемкий процесс. Преимущества новой технологии не только в доступной сырьевой базе, но и в простоте измельчающего оборудования (на сайте компании TimTek можно видеть линию измельчения в виде мощных раздавливающих вальцов, числом не менее 4 пар, с различным профилем рабочих элементов) и относительно низких энергозатратах на измельчение древесины.
Если измельчать сырье до частиц толщиной примерно 1 мм, то вследствие их эластичности древесная масса станет сыпучей. Значит, ее можно применять для производства плит MDF по отработанной технологии с получением качественно новой продукции высокой прочности. А при формировании ковра можно использовать перекрестную ориентацию частиц (как в технологии изготовления OSB-плит), с тем чтобы выпускать материалы, одинаково прочные в продольном и поперечном направлении.
В Канаде и странах Азии сейчас широко распространена технология прессования скрима при высоком давлении с получением материала, характеризующегося не только очень высокой прочностью, но и большим весом. В строительстве не требуются сверхпрочные и сверхтяжелые несущие, а тем более ограждающие конструкции. Рациональнее может быть технология прессования при давлении 2–2,5 МПа, применяемая сегодня в производстве фанеры и большинства древесных плит.
Текст Владимир Волынский